James Lamont Abrams
Lead Material Science and Process Engineering Specialist at Hamble Aerostructures Ltd- Claim this Profile
Click to upgrade to our gold package
for the full feature experience.
Topline Score
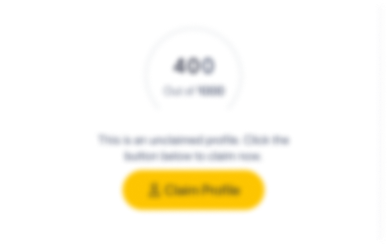
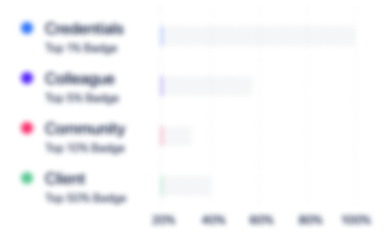
Bio


Experience
-
Hamble Aerostructures Ltd
-
United Kingdom
-
Airlines and Aviation
-
100 - 200 Employee
-
Lead Material Science and Process Engineering Specialist
-
Nov 2021 - Present
-
-
Lead Manufacturing Specialist - Assembly
-
Jan 2020 - Nov 2021
-
-
-
GE Aerospace
-
United States
-
Aviation and Aerospace Component Manufacturing
-
700 & Above Employee
-
Industrialisation Engineer
-
Jul 2018 - Jan 2020
-
-
Manufacturing Engineer (Assembly)
-
Aug 2015 - Jul 2018
-
-
-
Brunel University London
-
United Kingdom
-
Higher Education
-
700 & Above Employee
-
Student Ambassador
-
2012 - Jul 2015
Customer facing role in which I represented the College of Engineering, Design and Physical Sciences at industry trade shows as well at university-run events and open days. Tasks in these roles include presentations to new and prospective students, answering questions about the university, course and department and helping to run events such as the Brunel Engineers show.
-
-
Aerospace Engineering with Professional Development (MEng) Student
-
Sep 2010 - Jul 2015
Overall degree classification: 1st class honours. Degree accredited by the Royal Aeronautical Society and the Institute of Mechanical Engineers.Fifth Year (1st class overall, average coursework mark 73%)Modules - Strategic Management, Innovation and Enterprise (1); Advanced Aerodynamics, Propulsion Systems and Space Mechanics (1); Advanced Thermofluids (2.1); Current Topics in Aerospace (2.1)Group Dissertation - Balloon Launched Autonomous High Altitude Atmospheric Research Aircraft (1). This project was awarded the TWI prize for Excellence and Innovation in Engineering for Economic and Environmental Sustainability.Fourth Year (1st class overall, average coursework mark 74%)Modules - Professional Engineering Practice (1); Propulsion Systems, Aircraft Structures and Materials, Airworthiness and Stability and Control (1); FEA, CFD and Numerical Modelling (2.1)Dissertation - Design and Construction of a Velocity Probe Calibration Facility (1)Internship (Assembly Engineering Intern at GE Aviation) carried out between second and fourth years. Second Year (2.1 class overall, average coursework mark 78%)Modules - Work Placement Assignments (1); Professional Engineering Applications and Practice (1); Principles of Aircraft Design (2.1); Thermofluids (2.2); Solid Body Mechanics (2.2); Computing, Analytical Methods, Control and Instrumentation (2.2)First Year (2.1 class overall, average coursework mark 72%)Modules - Aerospace Laboratories, Technical Drawing and Workshop Experience (1); Fundamentals of Solid Body Mechanics (2.1); Fundamentals of Thermofluids (2.1); Engineering Materials, Manufacturing and Electrical Machines (2.1); Introduction to Engineering Design (2.1); Analytical Methods and Skills (2.2)
-
-
-
Carbon60
-
United Kingdom
-
Staffing and Recruiting
-
100 - 200 Employee
-
Assembly Engineer (Contracted to GE Aviation)
-
Jul 2014 - Sep 2014
-
-
-
GE Aerospace
-
United States
-
Aviation and Aerospace Component Manufacturing
-
700 & Above Employee
-
Assembly Engineering Intern
-
Jul 2012 - Sep 2013
Year in industry placement undertaken between the second and third years of my degree. Tasks and responsibilities in this role included: •Shop floor assembly process optimisation, including tool and fixture designs, as well as assembly process changes. My major project focused on A380 wing rib assembly process improvements, resulting in significant time and cost savings, quality and health and safety improvements. •Creation of shop floor assembly processes, in compliance with customer and company specifications and procedures. •Providing shop floor support where required to solve day-to-day production issues, and where necessary liaise with internal or external design departments to determine if an acceptable work around solution is achievable. •Working with procurement and other departments to ensure that appropriate stock levels are maintained without creating excessive inventory, and where necessary define and purchase new part requirements to aid manufacture. •Working with the quality department to ensure that a safe, reliable and compliant product is produced. •I was also involved in improving the site Environmental, Health and Safety audit score, working with the training department. This included the creation of procedures, forms and policy documents to enable the site to meet its requirements for EHS training.
-
-
-
Mid-Anglia School of Flying
-
Cambridge, United Kingdom
-
Flight Operations Assistant
-
Jul 2007 - Sep 2012
Assisted in the general running of the school, including administrative office tasks, handling payments and bookings, dealing with customers and helping to look after the school’s fleet of aircraft. Developed personal and communication skills, as well as experience of an industrial airport environment. I continue to volunteer at the school in my spare time. Assisted in the general running of the school, including administrative office tasks, handling payments and bookings, dealing with customers and helping to look after the school’s fleet of aircraft. Developed personal and communication skills, as well as experience of an industrial airport environment. I continue to volunteer at the school in my spare time.
-
-
-
-
Website Administrator
-
2006 - 2010
Tasks in this role included editing and updating the product databases, assisting with stock checks, editing photographs for publishing on the website and producing email marketing campaigns. Given the large numbers of similar products, this required a methodical and systematic approach to avoid errors, which given the small size of the company, could have proved expensive both in terms of time to correct and customers purchasing products with incorrect information for example. Tasks in this role included editing and updating the product databases, assisting with stock checks, editing photographs for publishing on the website and producing email marketing campaigns. Given the large numbers of similar products, this required a methodical and systematic approach to avoid errors, which given the small size of the company, could have proved expensive both in terms of time to correct and customers purchasing products with incorrect information for example.
-
-
Education
-
Brunel University London
Master of Engineering (MEng), Aerospace Engineering with Professional Development -
Impington Village College
International Baccalaureate, Maths, Physics, Economics, Chemistry, English Literature, French, Further Maths -
St Bede's Inter-Church School, Cambridge
Community
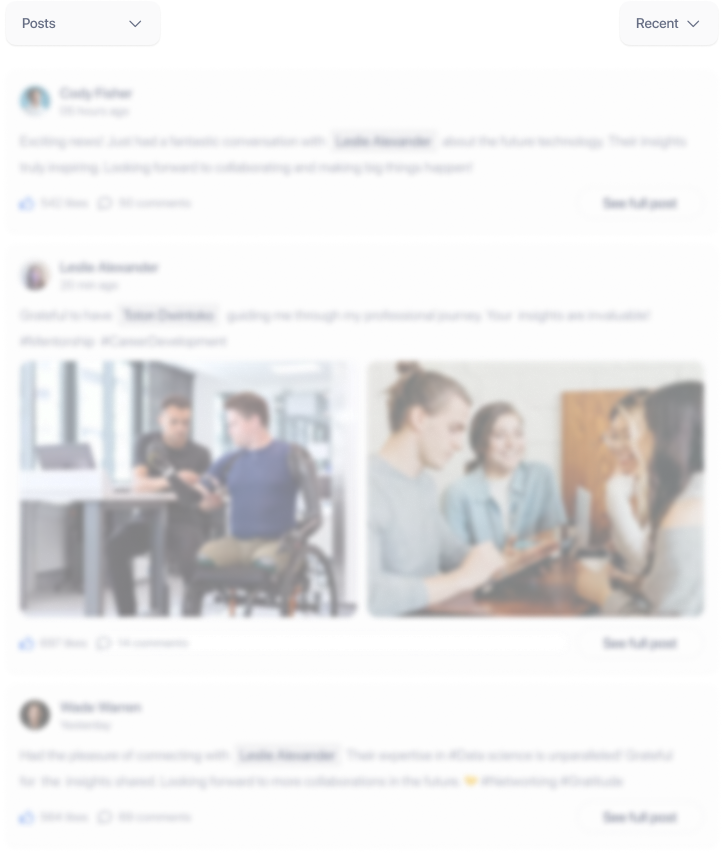