Miguel Angel Vega
Operation Manager at eos Products- Claim this Profile
Click to upgrade to our gold package
for the full feature experience.
Topline Score
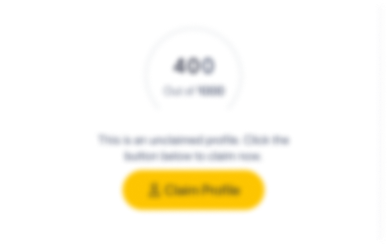
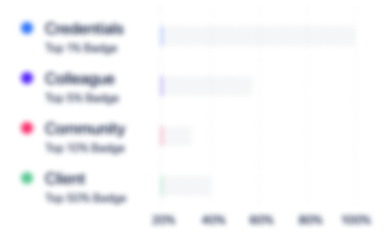
Bio

Miguel is a self oriented person, focus on process and great Knowledge of Demand, anticipating to it. He also developed great Team Building habilities, creating a strong team, and teaching each one how to read demand on such a challenging environment as Bic.

Por medio de la presente me permito recomendar ampliamente al Ing. Miguel Vega; quien es un profesional en relacion a todos los aspectos de la cadena de suministro (Demanda, Compras, distribucion y abastecimiento); aunado a sus competencias interpersonales tales como: Comunicacion, Liderazgo, Inteligencia emocional entre otras. Lo cual lo hace un profesional altamente capacitada para llevar a buen termino cualquier asignacion dada. Atentamente: M.A Marcos Estrada (CPIM,RSCC,CPF.PmP)

Miguel is a self oriented person, focus on process and great Knowledge of Demand, anticipating to it. He also developed great Team Building habilities, creating a strong team, and teaching each one how to read demand on such a challenging environment as Bic.

Por medio de la presente me permito recomendar ampliamente al Ing. Miguel Vega; quien es un profesional en relacion a todos los aspectos de la cadena de suministro (Demanda, Compras, distribucion y abastecimiento); aunado a sus competencias interpersonales tales como: Comunicacion, Liderazgo, Inteligencia emocional entre otras. Lo cual lo hace un profesional altamente capacitada para llevar a buen termino cualquier asignacion dada. Atentamente: M.A Marcos Estrada (CPIM,RSCC,CPF.PmP)

Miguel is a self oriented person, focus on process and great Knowledge of Demand, anticipating to it. He also developed great Team Building habilities, creating a strong team, and teaching each one how to read demand on such a challenging environment as Bic.

Por medio de la presente me permito recomendar ampliamente al Ing. Miguel Vega; quien es un profesional en relacion a todos los aspectos de la cadena de suministro (Demanda, Compras, distribucion y abastecimiento); aunado a sus competencias interpersonales tales como: Comunicacion, Liderazgo, Inteligencia emocional entre otras. Lo cual lo hace un profesional altamente capacitada para llevar a buen termino cualquier asignacion dada. Atentamente: M.A Marcos Estrada (CPIM,RSCC,CPF.PmP)

Miguel is a self oriented person, focus on process and great Knowledge of Demand, anticipating to it. He also developed great Team Building habilities, creating a strong team, and teaching each one how to read demand on such a challenging environment as Bic.

Por medio de la presente me permito recomendar ampliamente al Ing. Miguel Vega; quien es un profesional en relacion a todos los aspectos de la cadena de suministro (Demanda, Compras, distribucion y abastecimiento); aunado a sus competencias interpersonales tales como: Comunicacion, Liderazgo, Inteligencia emocional entre otras. Lo cual lo hace un profesional altamente capacitada para llevar a buen termino cualquier asignacion dada. Atentamente: M.A Marcos Estrada (CPIM,RSCC,CPF.PmP)

Credentials
-
Certified in Logistic, Transport & Distribution
-Jan, 2018- Nov, 2024 -
Certified Professional Forecaster
-Jan, 2011- Nov, 2024 -
Certified in Production and Inventory Management.
-Jan, 2008- Nov, 2024
Experience
-
eos Products
-
United States
-
Manufacturing
-
1 - 100 Employee
-
Operation Manager
-
Feb 2020 - Present
Under my manage are: Supply and demand to ensure a fill rate >90% with adequate inventory levels.
-
-
-
-
Integration Project Manager
-
Apr 2018 - Dec 2019
Responsibilities: Gathering information through SAP, analysis and deliver strategies for: Product slotting, infraestructure and equipment needed (part of) in order to meet the project requirements for picking process automation at Vallejo CEDIS. Profiling and data mining were the analysis tools used to identify patterns and orders behaviours regarding volume, lines per order, pieces per order and value per order, also ABC analysis per Vendors, Customers and products. Deliver monthly expenses reports and comparatives real expenses vs budget per CEDIS and consolidated.
-
-
-
BIC
-
France
-
Manufacturing
-
700 & Above Employee
-
Demand Planner.
-
Oct 2016 - Aug 2017
Responsibilities: Demand management for the Lighters and Shaving categories, through the development of an FCST that would allow a level of service greater than 95% to reach the company's customers. Analyze historical sales and debug them to have correct base information for the statistical FCST. Develop a comprehensive FCST, which will contemplate the history, trends and volumes of promotions and / or new releases.Update the FCST in the system, both national and exports of the categories monthly, to ensure a correct visibility of the supply of demand. Monitoring and execution of the S & OP cycle. Product review. Review of the demand. Review of the offer. Reconciliation S & OP. Prepare information to address with the sales accumulated in units and value to the current month, as well as the scenarios in units and value of the future months for decision making of the new target volumes.Key Contributions: The demand team improved the Fill Rate by 4%, reaching 98.4% in 2017 (January-July) versus the same period of 2016, likewise, we reduced the amount of penalties for Fill Rate from $ 8.15 million pesos to $ 1.5 million pesos. In 2017 we developed and defined the guidelines for handling, loading and updating the FCST for the countries to which we export in order to integrate their demand and ensure an adequate level of service.In 2016 I trained the demand team in loading and handling of information to the ERP (JD Edwards) and the Demand module (Manugistic). We worked on the debugging of the catalog of the clients so that their orders
-
-
Planning and Demand Manager for Central America and the Caribbean
-
2015 - 2017
Responsibilities: Responsible for Logistics of the Central America and Caribbean region to coordinate the supply of imported PT for each of the countries, as well as the administration of the production of machined products for subsequent export. In charge of a work team consisting of 4 Logistics Supervisors and a Coordinator of imports and exports.Review and coordinate the loading of FCST from different countries. Creation and updating of the master plan for the production of the machined products in Guatemala. Negotiation of volumes and times required by the region of both PT and Bulks with the different Group plants in Mexico, France and Greece. Creation and updating of the Budget for the distributing countries of Central America and the Caribbean. Generation and sending of reports of the area for Finance LAM.Key Contributions: In 2016 and 2017 we achieved two successful seasons of BTS (Back to School) with a Fill Rate of 98% and zero penalties. Also in 2016 we implemented the copacking of lighters and shavers in blister presentation in Guatemala, which allowed us to improve the supply to the region by 30%. We improved the supply processes, which resulted in planned purchases and online with the FCTS, which allowed to clean up inventory levels. Same year I successfully coordinated a recall of lighters in the region for quality issues, negotiated with the plant in France shipments to replace the lighters and minimize the shortage and impact on the level of service in the countries of the region.
-
-
Inventory Planner and Copacking Control
-
2008 - 2015
Responsibilities: Administration and planning of inventories of the 42 lines of stationery, to ensure adequate availability of inventories that allow us to meet orders with a level of service greater than 90%. Creation of the production master plan (MPS) to satisfy the national and export demand. Execution of the MRP and analysis of procurement and manufacturing suggestions generated from the system. Negotiation with the different plants of the group (Mexico, Greece, France and Brazil) volumes, product availability and shipping dates. Development of new copackers to increase capacity in processes with a bottleneck. Review and update BOMs related to SKUs under my manage.Key Contributions: In 2015 we conducted, search, evaluation and selection of copacker in Honduras (San Pedro Sula) successfully implementing a shaver copacking, optimizing times (we reduced 1 month of time) and logistics costs by 12%. Same year I negotiated with a maquila provider the cost of freight delivery, obtaining an annual savings of $ 432,000 pesos. In 2012 we developed a new copacker which allowed us to have the material in time and form to meet the BTS orders of that year.
-
-
-
Condumex
-
Mexico
-
Appliances, Electrical, and Electronics Manufacturing
-
700 & Above Employee
-
Project Leader.
-
2005 - 2008
Responsibilities: Implement the corporate ERP system of the Group (SyteLine) in the different Group companies, both manufacturing and services. Mapping of business processes (As Is) under the BPMN standard. Development of improvements to business processes (To Be). Design of new functionalities to the ERP system. Training in manufacturing modules, inventories and purchases to end users of the system. Support for business processes managed in the ERP. Inventories, Production, Purchases and Sales.Key Contributions: In 2006 we implemented ERP (SyteLine) in a manufacturing company (Alternate Energies) leading the manufacturing and planning part, with the benefit of better inventory control, MRP for shopping suggestions and manufacturing within the system
-
-
Education
-
Universidad Autónoma Metropolitana
Industrial Engineer.
Community
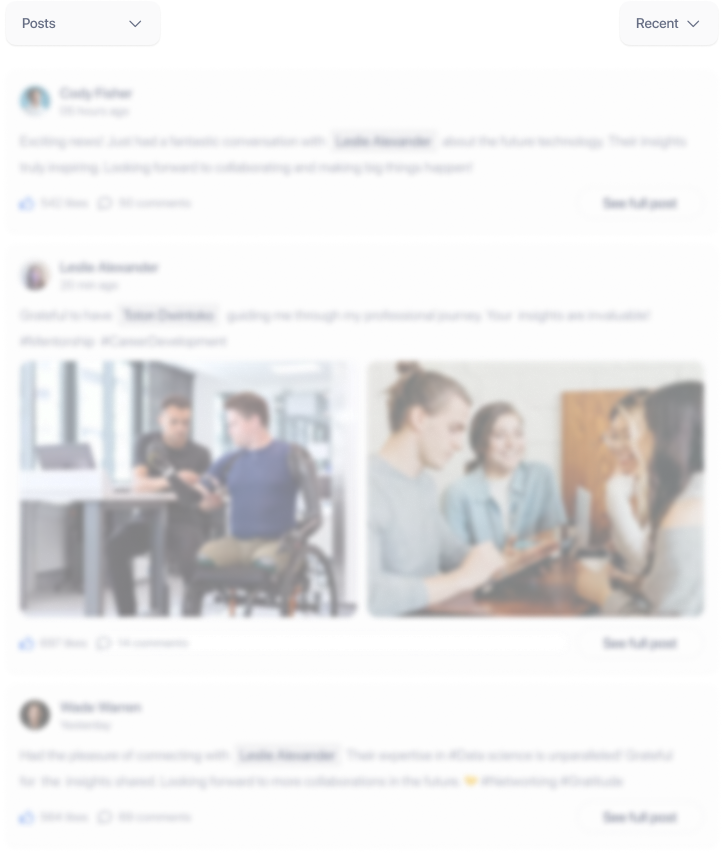