Jeff Bray
Project Supervisor/Coordinator at Electronic Controls and Systems, Inc- Claim this Profile
Click to upgrade to our gold package
for the full feature experience.
Topline Score
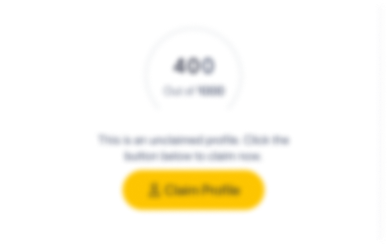
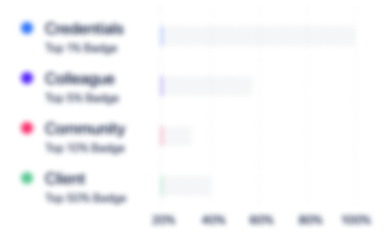
Bio


Experience
-
EC&S, Inc.
-
United States
-
Industrial Machinery Manufacturing
-
1 - 100 Employee
-
Project Supervisor/Coordinator
-
Nov 2010 - Present
Responsible for installation of all hydraulic equipment, piping, inventory and safety. Responsible for installation of all hydraulic equipment, piping, inventory and safety.
-
-
-
-
Production Supervisor
-
Aug 2008 - Feb 2009
Responsible for all aspects of production to include scheduling, safety, housekeeping, quality, costs, efficiencies, shipments, training, preventative maintenance. Responsible for all aspects of production to include scheduling, safety, housekeeping, quality, costs, efficiencies, shipments, training, preventative maintenance.
-
-
-
-
Project Manager
-
Nov 2005 - Aug 2007
Assisted Corporate Engineering in the startup of a 9.2 million dollar roll forming plant in Pasadena Texas. Renovated 135,000 square foot building. Laid out production flow for all equipment. Installed 8 brand new roll forming lines, 54 inch slitter, press break and shear. Interviewed and hired management staff along with plant employees. Completed startup by required time lines and budget. Assisted Corporate Engineering in the startup of a 9.2 million dollar roll forming plant in Pasadena Texas. Renovated 135,000 square foot building. Laid out production flow for all equipment. Installed 8 brand new roll forming lines, 54 inch slitter, press break and shear. Interviewed and hired management staff along with plant employees. Completed startup by required time lines and budget.
-
-
-
-
Production Superintendent
-
Aug 2004 - Oct 2005
Directed the efficient and profitable production of company products by promoting programs designed to increase productivity, improve quality and manage costs. Reduced plant staff by 15% while maintaining production output. Revised inventory layout for more efficient production flow throughout plant. Implemented shadow boards and pictorials to improve housekeeping techniques. Put preventative maintenance plan in place to reduce equipment break downs. Directed the efficient and profitable production of company products by promoting programs designed to increase productivity, improve quality and manage costs. Reduced plant staff by 15% while maintaining production output. Revised inventory layout for more efficient production flow throughout plant. Implemented shadow boards and pictorials to improve housekeeping techniques. Put preventative maintenance plan in place to reduce equipment break downs.
-
-
-
-
Production Superintendent
-
Feb 1999 - Nov 2003
Responsible for all aspects of plant operations. Met all fixed and variable cost goals. Turned Net Income from a 1998 loss of $137,032 to a profit of $641,852 in August of 2002. Reduced man hours per ton from 6.2 to 3.9. Reduced cost per ton from $122 to $98. Implemented Continuous Improvement programs in including 5S concepts. Responsible for all aspects of plant operations. Met all fixed and variable cost goals. Turned Net Income from a 1998 loss of $137,032 to a profit of $641,852 in August of 2002. Reduced man hours per ton from 6.2 to 3.9. Reduced cost per ton from $122 to $98. Implemented Continuous Improvement programs in including 5S concepts.
-
-
-
-
Production Manager
-
Jan 1995 - Jan 1999
Reduced overtime by 25% while increasing throughput 3.8%. Increased on time shipments from 85% to 97%. Revised set-up methods for press operations. Saved an average of 15 minutes per set-up, reducing annual set-up time by 2175 hours. Completed implementation of ISO 9002 Quality System. Reduced overtime by 25% while increasing throughput 3.8%. Increased on time shipments from 85% to 97%. Revised set-up methods for press operations. Saved an average of 15 minutes per set-up, reducing annual set-up time by 2175 hours. Completed implementation of ISO 9002 Quality System.
-
-
-
-
Special Assembly Supervisor
-
Jan 1984 - Jan 1995
Custom and Standard Assembly Supervisor Promoted development of work cell environments that increased production output 23% per capita in a 4 month Custom and Standard Assembly Supervisor Promoted development of work cell environments that increased production output 23% per capita in a 4 month
-
-
Education
-
Joliet Junior College
Some College, Business, Management -
Intership
4 year, Tool Room Machinest -
Dale Carnegie Management training
Community
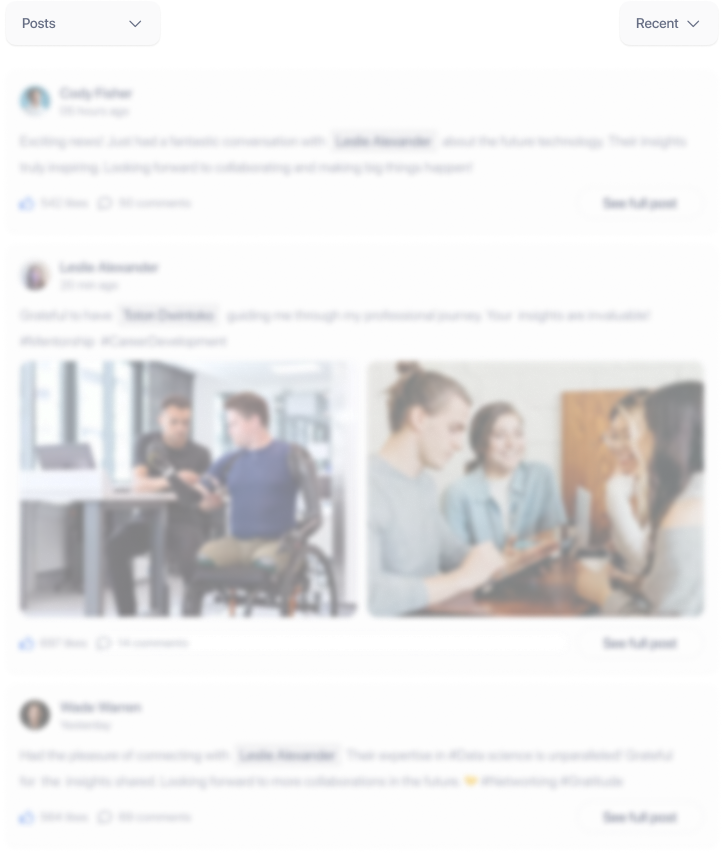