Evan Schairbaum
Data Manager at Saltchuk Marine- Claim this Profile
Click to upgrade to our gold package
for the full feature experience.
Topline Score
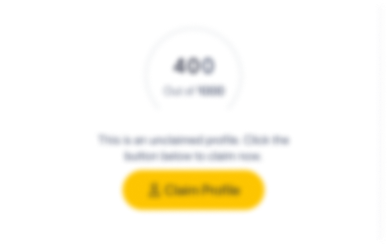
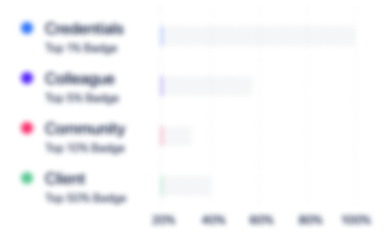
Bio

Bryan Meier
I had the pleasure of working with Evan for a few years and I am grateful for it. Evan brings a lot of energy, enthusiasm and experience around BI and how data can be used, analyzed and visualized. I would consider him an expert in many aspects of the BI world.

Bryan Meier
I had the pleasure of working with Evan for a few years and I am grateful for it. Evan brings a lot of energy, enthusiasm and experience around BI and how data can be used, analyzed and visualized. I would consider him an expert in many aspects of the BI world.

Bryan Meier
I had the pleasure of working with Evan for a few years and I am grateful for it. Evan brings a lot of energy, enthusiasm and experience around BI and how data can be used, analyzed and visualized. I would consider him an expert in many aspects of the BI world.

Bryan Meier
I had the pleasure of working with Evan for a few years and I am grateful for it. Evan brings a lot of energy, enthusiasm and experience around BI and how data can be used, analyzed and visualized. I would consider him an expert in many aspects of the BI world.

Experience
-
Saltchuk Marine
-
United States
-
Maritime Transportation
-
1 - 100 Employee
-
Data Manager
-
Apr 2020 - Present
-
-
-
Oldcastle Infrastructure
-
United States
-
Construction
-
700 & Above Employee
-
Senior Business Intelligence Analyst
-
Jun 2019 - Mar 2020
- Design, implement and support transition from on-prem SQL Server to Snowflake data warehouse solution - Manage ELT process through automation of procedures and tasks - Create and administer BI analytic solution for data analysts to answer business requirements - Advanced experience with data visualization tools to provide expertise to business units in regards to analytic decisions - Subject matter expert on NetSuite & Axapta ERP systems; Manufacturing, CRM, Transportation, Accounting/Finance, Customer Service
-
-
-
-
Business Intelligence Analyst
-
Jun 2017 - Jun 2019
- Responsible for creating complex data and analytic models to evaluate Manufacturing, Sales, and Transportation departments within Tableau, PowerBI, Excel, and integrated ERP reporting systems.- Partner with company stakeholders to isolate problems and structure analysis to address business needs. - Work with DB administrators to validate data integrity and accuracy in Azure Data Warehouse.- Design and implement standard operational dashboards to be used by internal and external clients pertaining to CRM and MES systems.- Educate and train users on displaying data in new forms for the purpose of analysis and problem solving.- Conduct onsite training at all manufacturing and DC locations on utilization of reporting tools and dashboards across all levels of management.
-
-
Operational Excellence Manager/ERP Specialist
-
Nov 2015 - Jun 2017
- Team lead for implementation of new ERP System across 12 manufacturing and distribution sites. Focused on Manufacturing Execution System (MES) and Customer Relationship Management (CRM) system.- Served as ERP Subject Matter Expert on all things reporting, data collection, dashboards, and manufacturing.- Collaborated with Sales and Marketing personnel to identify and address customer support needs.- Develop and implement effective scheduling and shop floor control system for discrete process manufacturing- Analyzed operational workflow to improve efficiencies throughout production facilities- Lead Product Management of implementation of Maintenance Management System (MMS) at over 25 manufacturing locations. Increasing machine uptime by 25%.
-
-
Production Manager
-
Jan 2014 - Nov 2015
- Responsible for providing leadership, vision and direction for the daily operations of precast concrete.- Drive a Culture of Safety with employees in compliance with local and national regulations.- Coordinate daily & weekly production plans to meet customers delivery schedules and budgeted efficiency expectations.- Assist sales team with product development & design of complex industrial, power, and communication structures- Drive continuous improvement through 5S projects collaborated among employees and process leads.- Emphasized focus exceeding expectations for Safety, Quality and Efficiencies.- Manage coordination and execution of preventative maintenance and work order systems ensuring 98% uptime across all equipment.- Increased operations in six months from 30 yd3/day to 80+ yd3/day while maintaining a Total Case Incident Rate (TCIR) < 2.0. Hired and trained additional 15 employees to meet this demand.- Oversee purchasing and receiving program for order fulfillment and plant operation.- Manage corrective action and disciplinary processes for all production personnel.
-
-
-
-
Production Manager In Training
-
Jun 2013 - Jan 2014
-A member of Operational Excellence team focused on improving operations around country; inclusive of safety, efficiencies, quality, maintenance initiatives -Assist in Monthly Safety Presentations, White Board/Efficiency training, Morning Huddles, and daily Mid-Day meetings -Developed and implemented Excel Based Computerized Maintenance Management System(CMMS) in Houston TX -A member of Operational Excellence team focused on improving operations around country; inclusive of safety, efficiencies, quality, maintenance initiatives -Assist in Monthly Safety Presentations, White Board/Efficiency training, Morning Huddles, and daily Mid-Day meetings -Developed and implemented Excel Based Computerized Maintenance Management System(CMMS) in Houston TX
-
-
-
PACCAR
-
United States
-
Motor Vehicle Manufacturing
-
700 & Above Employee
-
Process Improvement Engineer
-
Feb 2012 - Jun 2013
- Provide analytically support for quality and process issues to production floor and manufacturing lines. - Work closely with Kenworth and Peterbilt truck plants to facilitate improvement initiatives resolving quality issues. - Initiate and 8D corrective actions: Assist in Root Cause Analysis (RCA) through Gemba Walks, Cause & Effect Diagrams, Plan Do Check Act (PDCA) - Internal Product/Process Auditor for manufacturing lines ensuring compliance to ISO standards. -Participate in PACCAR Production System workshops improving process flow and eliminating waste. - Warranty Analyst – process and track all Dynacraft warranty claims. Identify repeat occurrences to eliminate failure in field applications - Generate and track metrics based on product Scrap, Warranty claims, Non-Conforming Parts - Presented to Senior Management - Create & Verify Process Control Plans (PCP), Standard Work Instructions (SWI), and Process Failure Mode Effects Analysis (PFMEA) documents
-
-
-
Elevate Outdoor Collective
-
United States
-
Retail
-
200 - 300 Employee
-
Research Assistant on Surface Coatings for Skis
-
Sep 2010 - Jun 2011
-Investigation and development of “snowphobic” polymeric surfaces for skis in collaboration with K2 Sports R&D division. -Characterized current and future materials using optical microscopy, scanning electron microscopy (SEM), atomic force microscopy (AFM), goniometry, and energy dispersive x-ray spectroscopy (EDAX). -Designed and constructed apparatus capable of measuring coefficient of friction between ski surface and snow. -Investigation and development of “snowphobic” polymeric surfaces for skis in collaboration with K2 Sports R&D division. -Characterized current and future materials using optical microscopy, scanning electron microscopy (SEM), atomic force microscopy (AFM), goniometry, and energy dispersive x-ray spectroscopy (EDAX). -Designed and constructed apparatus capable of measuring coefficient of friction between ski surface and snow.
-
-
-
Old Castle Precast
-
Madera, CA
-
Process Engineer
-
Jun 2010 - Sep 2010
-Researched and developed new mix designs for polymer concrete based on various aggregates, sands, resins, catalysts, and fiberglass. Led to a $3,000,000 budget proposal to become more competitive and efficient. -In charge of quality control and inspection of the polymer concrete production lines resulting in reduced product waste and hazardous contaminants. -Oversaw three production lines while reviewing processing techniques to improve efficiency and reduce manufacturing costs. -Conducted Bill of Materials on all products ensuring product accuracy and quality.
-
-
Education
-
University of Washington
BS, Material Science and Engineering
Community
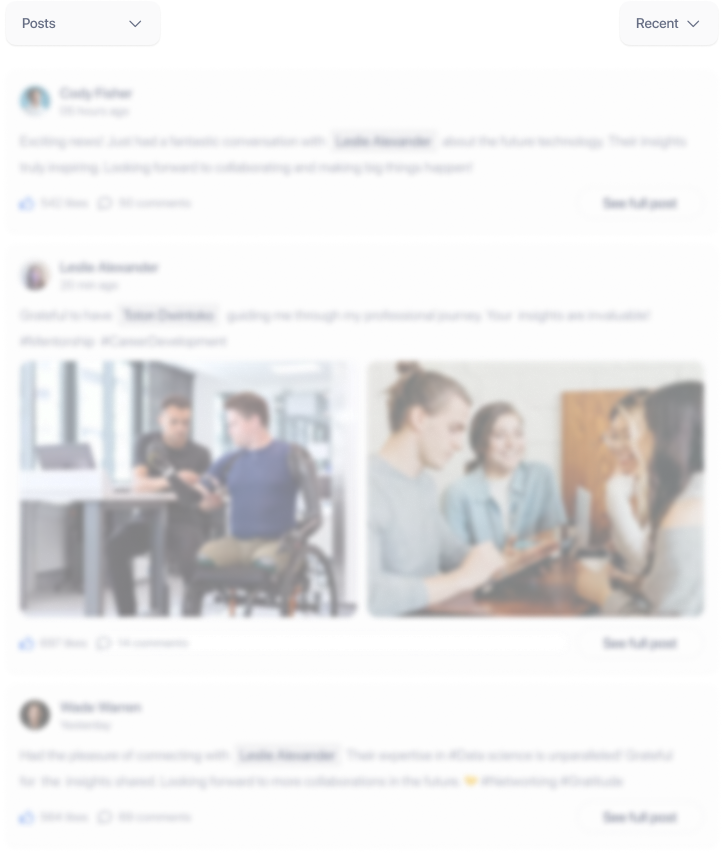