Paul Ross
Supply Chain SME at ekaterra- Claim this Profile
Click to upgrade to our gold package
for the full feature experience.
-
French Limited working proficiency
-
Spanish Elementary proficiency
Topline Score
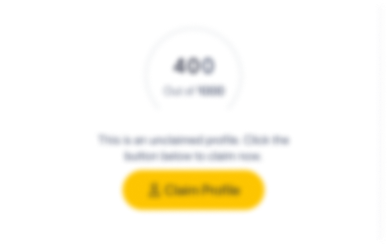
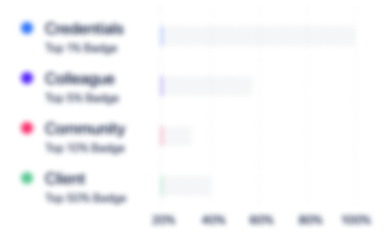
Bio

Andy Carter
Paul was an asset to have in the team at Petainer; an extensive knowledge of supply chain coupled with great organisational skills and adept at people management. Paul has the ability to cut through problems at pace with a practical, common sense view. A focussed individual, with whom it is possible to achieve challenging objectives.

Colin Drummond
Paul provided focussed logistics expertise and trouble shooting. He interacted well with work colleagues and logistics partners and helped provide valuable support during a period of rapid change management

Anne-Laure Green
Paul was a strong team player who was very easy to work with. He always aimed to achieve the best results possible and whilst having excellent technical expertise, he was also open to new ideas and ways of doing things. He was always keen to expand his knowledge and wanted to understand other areas of the business to ensure alignment and benefits across all teams.

Andy Carter
Paul was an asset to have in the team at Petainer; an extensive knowledge of supply chain coupled with great organisational skills and adept at people management. Paul has the ability to cut through problems at pace with a practical, common sense view. A focussed individual, with whom it is possible to achieve challenging objectives.

Colin Drummond
Paul provided focussed logistics expertise and trouble shooting. He interacted well with work colleagues and logistics partners and helped provide valuable support during a period of rapid change management

Anne-Laure Green
Paul was a strong team player who was very easy to work with. He always aimed to achieve the best results possible and whilst having excellent technical expertise, he was also open to new ideas and ways of doing things. He was always keen to expand his knowledge and wanted to understand other areas of the business to ensure alignment and benefits across all teams.

Andy Carter
Paul was an asset to have in the team at Petainer; an extensive knowledge of supply chain coupled with great organisational skills and adept at people management. Paul has the ability to cut through problems at pace with a practical, common sense view. A focussed individual, with whom it is possible to achieve challenging objectives.

Colin Drummond
Paul provided focussed logistics expertise and trouble shooting. He interacted well with work colleagues and logistics partners and helped provide valuable support during a period of rapid change management

Anne-Laure Green
Paul was a strong team player who was very easy to work with. He always aimed to achieve the best results possible and whilst having excellent technical expertise, he was also open to new ideas and ways of doing things. He was always keen to expand his knowledge and wanted to understand other areas of the business to ensure alignment and benefits across all teams.

Andy Carter
Paul was an asset to have in the team at Petainer; an extensive knowledge of supply chain coupled with great organisational skills and adept at people management. Paul has the ability to cut through problems at pace with a practical, common sense view. A focussed individual, with whom it is possible to achieve challenging objectives.

Colin Drummond
Paul provided focussed logistics expertise and trouble shooting. He interacted well with work colleagues and logistics partners and helped provide valuable support during a period of rapid change management

Anne-Laure Green
Paul was a strong team player who was very easy to work with. He always aimed to achieve the best results possible and whilst having excellent technical expertise, he was also open to new ideas and ways of doing things. He was always keen to expand his knowledge and wanted to understand other areas of the business to ensure alignment and benefits across all teams.

Experience
-
ekaterra
-
Netherlands
-
Food and Beverage Services
-
200 - 300 Employee
-
Supply Chain SME
-
Oct 2022 - Present
Brand portfolio carve out transition. Brand portfolio carve out transition.
-
-
-
E2E Supply Chain Excellence Ltd
-
United Kingdom
-
Transportation, Logistics, Supply Chain and Storage
-
Director
-
Jan 2014 - Present
E2E SCE is an interim management company that supports Manufacturing, Supply Chain & Renewable Energy companies. It has saved/benefited clients for almost 10 years and has delivered benefits in excess of £1billion since is started operating. It specialises in assisting organisations with skills that they do not have, including, change management, business transformation, technology development, strategy, turnaround, implementation of continuous improvement techniques, assurance and compliance. This is achieved by working as part of your team supporting and collaborating across and your organisatio at at all levels. Helping Clients Develop World Class Sustainable Supply Chain Solutions, including: - Business Transformation & Change - End to End Supply Chain Improvement - Acquisition & Mergers Sales & Operations Planning (S&OP) & (IBP) - Innovation and New Product Development - Business Turnaround and Start Ups - Supply Chain Risk Mitigation and Business continuity planning Contact us for more information.
-
-
-
RoslinCT
-
United Kingdom
-
Biotechnology Research
-
100 - 200 Employee
-
Supply Chain Consultant
-
Jul 2022 - Present
Assessed RoslinCT end to end supply chain and associated business practices. Delivered 3 point plan from execution to automation to meet the organisations growth plans. Assessed RoslinCT end to end supply chain and associated business practices. Delivered 3 point plan from execution to automation to meet the organisations growth plans.
-
-
-
Costa Coffee
-
United Kingdom
-
Retail
-
700 & Above Employee
-
Supply Chain Subject Matter Expert (S&OP)
-
Dec 2021 - Mar 2022
Designing and developing end to end planning processes for Costa products supplied to +2500 retail stores. Designing and developing end to end planning processes for Costa products supplied to +2500 retail stores.
-
-
-
Scholl
-
United Kingdom
-
Wellness and Fitness Services
-
1 - 100 Employee
-
Director Supply Chain Planning & Supply Chain SME
-
Apr 2021 - Jul 2021
Scholl, is a brand carve out acquisition from Reckitt Benckiser to Yellow Wood private equity. Scholl is the leading global consumer goods brand for foot-care and foot related medical products. The new business turnover is approx. £170million per annum. Developed operating model between sales and buying parties for all aspects of supply chain to align with Transition Service Agreements (TSA) and Manufacturing & Supply Agreements (MSA) to ensure that risks are managed and mitigated, customer service levels are maintained and profitability maximised. • Implemented practices to maintain customer service and maximise revenue by reducing out of stock products during complete duration of transition period. • Produced tools/reports/methodology to reduce overall inventory period during transition period (12 months) • Support transition plan and market/supplier migration between two entities. Developed end to end Sales & Operations Planning (S&OP) process for new business model, including alignment with migration plan and onboarding of new business operating teams, Sales, marketing, finance and supply chain. • Designed detailed (level 3) processes for end-to-end S&OP processes, including detailed process maps for demand and supply planning and dashboards and KPIs for Pre-S&OP and S&OP Exec • Created an implementation plan for the end-to-end process including, sales, marketing, finance, supply chain, suppliers, and Exec board • Supported ERP key requirements capture for Infor M3 including Supply Chain / business planning, supply chain execution, logistics, procurement and customer services • Created new lean organisational structure, based on standard automated best practices with associated role descriptions and recruitment plan
-
-
-
Mundipharma
-
Pharmaceutical Manufacturing
-
700 & Above Employee
-
Director 3rd Party Manufacture
-
Oct 2020 - Mar 2021
Developed new global role for 3rd Party Manufacture management, including: • New Business Development & Integration; supported due diligence process, undertake supply chain impact and risk assessment, ensured alignment with operational model and developed standard supply chain terms for current and future business agreements. Implemented 3 new products to market. • Strategic Supplier Development and Relationship development; created a medium-term plan to develop partnerships with key suppliers based on value, volume and strategic importance, developed supplier best practices and engagement portal and engagement tools whilst reducing costs and improving customer service • Supplier Rationalisation: evaluated current supplier footprint and developed strategy to reduce number of suppliers whilst reducing supply risks and total product supply costs by £15 million / annum • Operational Support, acted as point of escalation for all supplier performance failures
-
-
-
Mundipharma
-
Pharmaceutical Manufacturing
-
700 & Above Employee
-
Supply Chain Transformation
-
Jul 2019 - Feb 2020
Lead a global supply chain transformation focused on improving profitability, reducing costs and improving customer service • Global Sales & Operations Planning (S&OP) implementation for both ethical and consumer businesses• Design & implementation of automated planning information data sources and the configuration and installation of a new planning technology tool (Infor IBP)• Order to cash process efficiency and automation throughout the company internal entity organisation and to supplier/ internal customer• Product Lifecyle Management, both Beginning of Life (BoL) New product development and implementation and End of Life (EoL) portfolio management• Strategic supplier management, commercial alignment and rationalisation• Systems improvement including data specification, global automated collation & management• Deployment of Repeated Process Automation (RPA)• Global ERP platform standardisation for management of master data and order management automationIdentified savings including:• Global Supply Chain Headcount reduction of ~20%, via process improvement and automation• Inventory reduction of 30% via improved planning and implementation of product segmentation (ABC/XYZ)• Elimination of lost sales due to out of stock products and agreed service levels• Cost reduction of product and freight; +$5 million, by longer term planning enabling better shipping and freight decisions• Improved customer service levels, via improved forecast accuracy and supplier management, via OTIF management• Supplier relationship management and commercial alignment, reduction of number of contracts by 80%, suppliers by 60% and implementation of standard terms
-
-
Supply Chain Excellence
-
Jan 2019 - Jul 2019
Implementing Supply Chain best practices across global organisation.Developing and embedding S&OP process best practices, ways of working and monthly cycle drumbeat.Reviewing existing practices and designing new best practices for all stages of the S&OP cycle from including portfolio review, including end to end PLM methodologies, Demand and supply planning, platform reviews and Exec summary within agreed monthly routine.Designing and installing simple and pragmatic standardized practices including inventory tracking and management, supplier engagement, master data management etc
-
-
New Product Introduction
-
Sep 2018 - Dec 2018
Transitioned, with zero failures, new product development team into new commercial asset team organisation as part of a business restructure.Reviewed existing NPI process assessing any gaps and identifying future continuous improvement opportunities implementing a Right first time on budget and delivered on time in full concept to support existing 25 day implementation timescale.Introduction of new products within global pharmaceutical company. Successfully Launched +5 new products.
-
-
-
Glennmont Partners from Nuveen
-
United Kingdom
-
Services for Renewable Energy
-
1 - 100 Employee
-
Business Transition / Change
-
Oct 2016 - Nov 2017
I was appointed to oversee the development of effective business transformation, and initiate business transformation strategies to respond to internal and external drivers, with challenging existing practices and identifying improved ways to achieve strategic outcomes.As a Supply Chain subject matter expert, l ensured service transformation, and business change alignment with a talented team of professionals.Leading the development and delivery of a comprehensive internal and external Transformation programme, comprised of service, operations and supply chain reconfiguration, and deliver major service re-design procedure provision remains essential.Sample achievements were; establishing an agile strategic solution, to manage end-to-end supply and operation for material supply contracts, with a stock monitoring tool to safeguard plant and supplier operations, and instituted plant design operational practices for plant and supply chainI endorsed all necessary business work-stream accountabilities, with focus given to responsibility, procedures and documents; identified data requirements and timings to enable automated data transfer on a concurrent basis between service providers, with the introduction of a comprehensive data migration list from incumbent service provider, which delivered business information, data and communications, generated from business development to finance and regulatory data.Supported a successful business re-finance, with providing new lenders with supply chain oversight and operational solutions to manage materials supply risk to the plant.
-
-
Supply Chain Development & Assurance
-
Jan 2016 - Nov 2017
In this role, I was selected to manage a 3rd party service provider operating a 40MW renewable energy plant, compliant with Master Service Agreement; the entire remit was to improve the inbound supply chain to maintain plant supply and minimise costs and manage risk. Delivery of supplier assurance services compliant with policies, standards and target operating model, with identifying potential areas of weakness, driving proactive remediation and affirmative action, with supporting the business in developing remediation plans was a key component of my work.Ensured the tracking and updating of supplier assurance plans to accurately reflect the work undertaken with full engagement with key stakeholders to ensure assurance plans were aligned with the business’ risk framework. In addition I oversaw an innovative industry partnership engagement strategy for existing and future suppliers to the plant, which was to ensure the business was not only best positioned against competitors, but was a preferred customer in the market.Led the implementation of a successful ERP solution, with lifespan costs to deliver LIVE status information for all business functionalities; including finance, contract to invoice, inventory, forecasting, scheduling and automated logistics tracking, alongside the successful of an interim inventory management and material delivery scheduling tool, designed to track inventory by contract and location, enabling visibility and precision of stock movement and volumes.I created a zero waste plan, intended to recycle waste materials producing substantial cost saving +25% versus budget; with producing supply contract covering material supply solutions, rationalising from 11 to 1, which enabled commercial, HSE, regulatory data and reporting improvements, along with cost calculations to facilitate superior delivery coverage for customer and supplier, in addition to instituting proactive safety and housekeeping supervision that resulted in +450 LTI free days
-
-
-
Petainer
-
United Kingdom
-
Packaging and Containers Manufacturing
-
1 - 100 Employee
-
New Product Development and Implementation
-
Nov 2014 - Jul 2015
-
-
-
Nelsons
-
United Kingdom
-
Retail
-
200 - 300 Employee
-
Business Improvement
-
Jun 2014 - Sep 2014
This assignment was to manage and integrate high quality business improvement initiatives to deliver comprehensive and innovative business solutions that delivered cost efficient business benefit, with focus given to upgrading Sales Order to Delivery. I coordinated engagements with client to outline strategy, ensured the ERP strategy enabled robust procedures to align with forecasted growth, along with monitoring the production to distribution product flow, to discern, manage and remove anomalies across the operation. Provided subject matter expertise, insight and the necessary resources to drive through business improvement initiatives, while also developing and maintaining stringent project governance across the Sales Order to Delivery process with key emphasis on the priority areas. Maintaining scalable supply chain business processes ensured the sales and order to delivery processes and systems were managed proficiently, in addition to enabling processes to drive mechanisms to deliver continued improvements for business benefit.
-
-
-
Drax Group
-
United Kingdom
-
Utilities
-
700 & Above Employee
-
Business Transformation
-
Jun 2012 - Dec 2013
Responsible for leading cross functional team to implement a far-reaching end-to-end business transformation; including the creation of a new supply chain, major plant changes, operating model and changes to business financial accounting and regulatory reporting systems with an overall programme value of circa £750 million. Ensuring new business model maximises profitability and understands changes of its financial drivers. The conversion of the UK’s biggest coal fired electricity plant to predominantly biomass. Successful conversion of 1st 100% biomass fuelled generation unit capable of generating 600MW/Hr. Procured and executed 1st unit fuel procurement volume and associated supply chain solutions and capacity, ~2.5 million tonnes per annum including development and deployment of new business policies. Developed a long term supply chain infrastructure programme including fuel supply, port capacity delivery and receipt, freight management, rail and road management including: Procurement of biomass material to chemistry specification and safety control ~7.5million tonnes per annum. Port capacity at 4 UK ports provided ~12million tonnes per annum. Rail path and wagon capacity of approx. 250 rail wagons ~14million tonnes per annum capacity, cost ~£120 million. Modified existing generation plant to incorporate new materials burn characteristics with no detrimental effect on plant efficiencies. Constructing new plant and existing plant capacity increase, including new material storage, rail and associated material handling systems with a total value of £325 million. Instigated simple and pragmatic but robust programme management processes and procedures and controls. Implemented general business change control methodology ensuring prioritisation, approval and best practice development of all new projects delivery to business, developed 5 years visibility.
-
-
-
Rolls-Royce
-
Industrial Machinery Manufacturing
-
700 & Above Employee
-
Supply Chain Transformation
-
Jan 2011 - Jul 2012
Supply Chain (Business Improvement) Responsible for identification and intervention of poor supply chain performance at key suppliers. Supporting suppliers', preparing and implementing medium to long term improvement strategies for all aspects of quality, delivery, supply security and cost. Programme management of all Rolls Royce team interventions ensuring effective resource availability and adherence to objective and time. Development of improvement strategy for top 5 worst performing suppliers. Implementing simple and pragmatic best practice improvement processes fit for purpose and for organisation. Initiating proactive supply chain management practices focusing long term actions on prevention of delivery failure. Designed and instigated simple route cause continuous improvement process addressing underlying failure modes.
-
-
-
Shell
-
United Kingdom
-
Oil and Gas
-
700 & Above Employee
-
Global Supply Chain Programme Manager
-
Oct 2008 - May 2010
Responsible for Global Supply Chain initiatives control, prioritisation and implementation; ensuring integration into end-to-end business strategy and targets. Developed pragmatic but robust change management processes and systems for all global change initiatives, ensuring challenging but realistic targets are defined and achieved. Ensuring implementation of global plan is defined, visible, planned and realistic; ensuring key change processes are in place to assure timelines and budgets are strictly adhered to. • Global Programme Manager for global portfolio rationalisation for sales growth programme (globalisation of product catalogue), value between $150-200 million, and associated supply chain simplification programme (removing complexity), value $100-150 million. • Acted as an end-to-end supply chain consultant for all global & regional operations teams. • Developed selection and prioritisation process for all globally driven initiatives, including a $ benefits value matrix. • Instigated project management systems for both CAPEX and non-CAPEX initiatives. • Implemented effective globally standardised implementation methodologies ensuring full visibility, resource utilisation and clear progress tracking. • Developed key change management competences throughout global organisation, defining awareness and training opportunities, setting targets and expectations in addition to measurement mechanisms. • Pioneered a real-time experience based change management tool to enable competence development based on real initiatives.
-
-
-
Ross Consulting - Vietnam
-
Ho Chi Minh City - Vietnam
-
Director
-
Jun 2007 - May 2008
Established a consultancy business in Vietnam to assist local companies reduce operational costs, improve productivity, product quality and customer service. Assisted local companies to understand global supply chain standards and practices as well as developed plans for implementation with excellence. Applied and successfully achieved Vietnam business license for consultancy in all matters of supply chain, including, procurement, operations management, quality management, logistics & product supply and safety management. Developed company brand and business identity as well as promotional and advertising materials. Set-up local networking group for local company benchmarking. Presented modern supply chain management practices to existing established business groups within Vietnam, including Total Supply Chain Overview, stock management, operational organisation, quality management and assurance, distribution and logistics standards and practices. Assisted international companies with new business set-up including project management timescales, local expectations and procedures, and human resource availability. Assisted customers to review organisational effectiveness with particular attention paid to elimination of multiple repetition of task with view to prevent quality control failure and long term cost avoidance. Particularly focused on elimination of non-value adding tasks.
-
-
-
Kronenbourg Vietnam Limited
-
Vietnam (Ho Chi Minh City)
-
Operations & Supply Chain Manager
-
Oct 2007 - Apr 2008
Kronenbourg Vietnam Limited (KVL) was originally a 50/50% joint venture company set up between Scottish & Newcastle and Vinataba in 2008. The company was set-up to brew, package, distribute and sell beer products in Vietnam and SE Asia. Reporting to General Director (KVL) and Group Operations Director (S&N). Responsible for setting up operations processes and procedures for new green field joint venture brewing business in Vietnam between Vinataba and Scottish & Newcastle. Responsibilities included product launch, 3rd party logistics provider set-up, brewery construction project preparation, procurement of raw materials, brewery equipment and contracting services. Responsible for set-up for operations systems and total supply chain implementation for green field business: Working with 3rd party design consultant developed project plan for brewery construction, ensuring local practices and procedures are captured in cost budget and timeline: Designed and developed implementation plan for operations structure for initial 5 years of business operation: Instigated employee development and training plan for every individual position, both 'on-the-job' and personal development: Implemented best importation solution of product from S&N global to KVL to meet launch dates and minimising import costs: Identified local materials suppliers ensuring satisfactory quality standards are met whilst delivering best costs and supply timings, including brewery construction companies.
-
-
-
Kimberly-Clark
-
United States
-
Manufacturing
-
700 & Above Employee
-
European Supply Chain Development Manager
-
2003 - 2006
Responsible for delivering all company developments, both regional and global, ensuring that supply chain implementation aspect of all projects was delivered with excellence. Developed 5 year European packaging and supply chain strategy, including capital budget planning, manufacturing, materials supply, distribution efficiency, customer management and marketing support. Responsible for all supply chain and packaging design solutions for total European sales region over 25 countries and 3 manufacturing sites: Managed and developed central packaging development team and manufacturing sites representatives setting both personal and corporate objectives and expectations for quarterly and annual review and publication: Identified short medium and long term strategy for regional sector specific supply chain & packaging developments, including manufacturing, marketing and customer management support: Interfaced with all business functions, acting as central liaison between Marketing and European Purchasing, Manufacturing and European Logistics: Benchmarked and developed best practices for design and implementation procedures for new SKU introduction within European and Global sectors as well primary competitor analysis: Implemented +35 product upgrade projects. Managed multiple projects (+50) at any time, including supplier development, manufacturing improvement, product upgrade and regional promotional projects.
-
-
Business Consultant
-
Jun 2003 - Dec 2003
Manufacturing & Supply Chain - As part of a core business team re-defined product positioning in marketplace focusing on 4 key areas of product development and customer relations; including trade terms, product consumer alignment, promotional design and implementation, and specifically responsible for leading a multi-functional management team to support manufacturing and supply chain element of business project. Asset Leader - Responsible for 2 diaper manufacturing assets with total turnover above $60million per annum. Managed and developed day support asset team to focus on safety, quality and productivity. Assisted and mentored shift management team to develop shift operating teams performance and individual's skills.
-
-
Asset Leader
-
May 2002 - Jun 2003
Responsible for 2 diaper production assets with annual turnover ~$60 million. Line manager for team of 63 personnel, 4 x 17 shift teams plus 7 day shift support personnel.Safety, 0 Lost time incidents. Quality reduced waste by ~40%, customer complaints by 35%. Increased productivity by ~42%.
-
-
Packaging Engineer
-
Feb 2001 - May 2002
Responsible for leading group of 11 mechanical / electrical maintenance technicians. Responsible for leading cross functional improvement team to address plant number 1 safety, quality and productivity issue (packaging systems). Eliminated from number 1 key issues in 12 months.
-
-
-
Scottish and Newcastle
-
Food and Beverage Services
-
1 - 100 Employee
-
Project manager
-
Apr 1998 - Feb 2002
Developed and implemented major capital projects across the group, including project financial authorisation, budget control design, project management, implementation and completion. Projects were identified at all stages of the business from dry goods handling, through process and final packaging, marketing and brand intiatives incoporating both on/off trade projects. Developed and implemented major capital projects across the group, including project financial authorisation, budget control design, project management, implementation and completion. Projects were identified at all stages of the business from dry goods handling, through process and final packaging, marketing and brand intiatives incoporating both on/off trade projects.
-
-
-
-
Senior Project Engineer
-
Jan 1998 - Jan 2001
Responsible for implementation of group major capital project within manufacturing & supply chain organisation of brewing business, including presentation to main board for capital expenditure authorisation, design and implementation of project objective, supplier selection and contract strategy, and budget control to ensure no overspend of authorised budget.
-
-
Process Development Engineer
-
1997 - 1998
-
-
-
IMI: Yorkshire Fittings Ltd
-
Dundee, United Kingdom
-
Manufacturing Engineer
-
1995 - 1997
Successful launch of world's first push-fit copper pipe plumbing fitting and valve range. Implemented hi-technology, hi-flexibility, customer response manufacturing cell. Managed all site sub-contract suppliers for quality delivery and cost, reduced sub-contract cost by ~60% in 12 months. Successful launch of world's first push-fit copper pipe plumbing fitting and valve range. Implemented hi-technology, hi-flexibility, customer response manufacturing cell. Managed all site sub-contract suppliers for quality delivery and cost, reduced sub-contract cost by ~60% in 12 months.
-
-
-
IMI: Yorkshire Fittings
-
Dundee, United Kingdom
-
Quality Engineer
-
1994 - 1995
Named delegate for ISO 9000 site accreditation. Achieved full 9002 accreditation for Dundee site. Lead plant continuous improvement processes with cell operations teams. As part of leadership team implemented self directed work teams culture within a new cell manufacture organisation. Role of instigating quality control and prevention within work teams. Named delegate for ISO 9000 site accreditation. Achieved full 9002 accreditation for Dundee site. Lead plant continuous improvement processes with cell operations teams. As part of leadership team implemented self directed work teams culture within a new cell manufacture organisation. Role of instigating quality control and prevention within work teams.
-
-
-
-
Apprentice Mechanical Engineer
-
Jan 1990 - Dec 1993
Apprenticeship covering toolmaking, CNC manufacturing, maintenance, tooling draughtsman, and quality engineering. Apprenticeship covering toolmaking, CNC manufacturing, maintenance, tooling draughtsman, and quality engineering.
-
-
Education
-
Abertay University
BSc, Engineering (Mechnical, Electrical and Electronic), Manufacture, Design, IT -
University of Abertay Dundee
HND Integrated Engineering & Manufacture, Mechanical, Manufacturing, Electrical & Electronic Engineering
Community
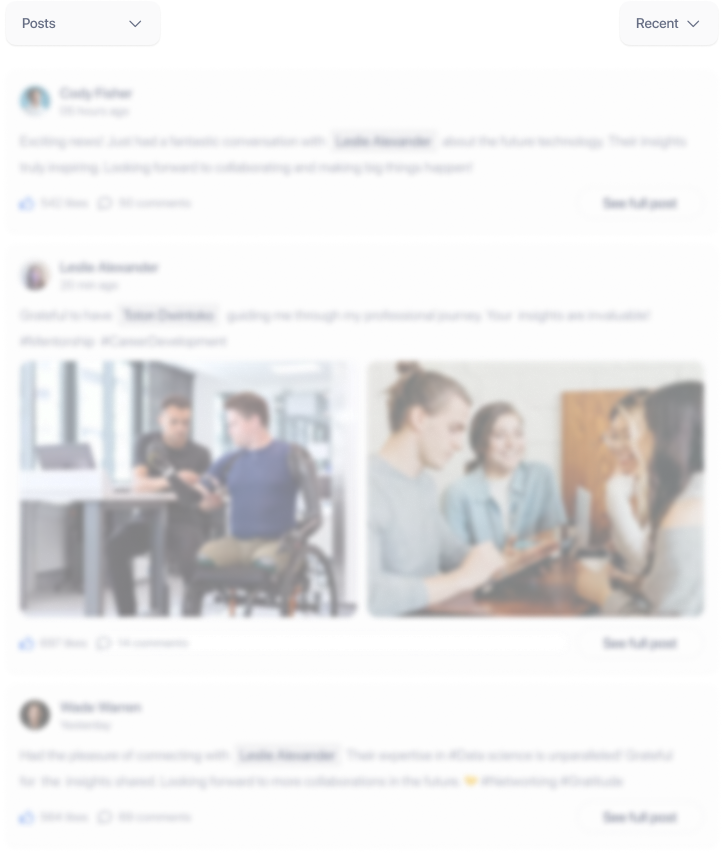