Andrew Garton
Project Manager (Renewables and Hydrocarbons) at Advisian- Claim this Profile
Click to upgrade to our gold package
for the full feature experience.
Topline Score
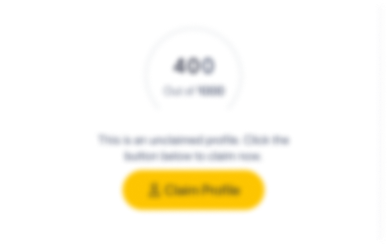
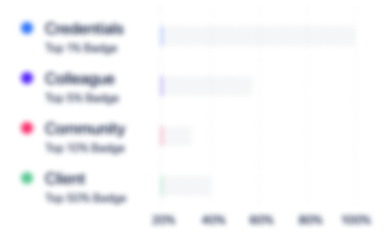
Bio


Credentials
-
PRINCE2® 2017 Practitioner
ex. Axelos -
RPEQ
ex. BPEQ
Experience
-
Advisian
-
Australia
-
Business Consulting and Services
-
700 & Above Employee
-
Project Manager (Renewables and Hydrocarbons)
-
Aug 2019 - Present
• Project Manager 30MW green hydrogen to green ammonia pre-FEED study (20,000 tpa anhydrous liquid ammonia) • Project Manager 10MW green hydrogen pre-FEED study (1,600 tpa, 350 bar, MEGC road transport) • Project Manager 200,000 tpa green hydrogen Concept Study (liquid hydrogen via sea transport) • Project Manager 500,000 tpa green ammonia Concept Study (anhydrous liquid via sea transport) 54 direct and indirectly reporting staff. Duties; Hydrocarbon project management and process engineering team leadership in both greenfield and brownfield Concept/Select/Detailed Design & Execute projects (renewable hydrogen, unconventional gas, UCG. Gas gathering and gas field dewatering. Gas processing, compression, transmission); Safety in Design, Process Safety studies; regulatory compliance; Client & vendor negotiations. Execution support. I am responsible for the full spectrum of project and technical deliverables; project control, monitoring & reporting. Schedule establishment and control. CAPEX, OPEX estimating, critical documentation generation including Basis of Design, Control Philosophy, PID/PFD, Heat & Mass Balance, MTO’s, process simulation and flow assurance. Technical calculations HAZID & HAZOP facilitation, SMS, Hazardous Area assessments, ALARP / SIL / LOPA studies, AS / API / ASME compliance, EHS constraint & compliance monitoring. Field Development Planning based on type curve characterization. Adherence to and promotion of a “Zero Harm” safety culture. Show less
-
-
-
Worley
-
Australia
-
Professional Services
-
700 & Above Employee
-
Principal Process Engineer (Hydrocarbons)
-
Aug 2012 - Dec 2018
I participated in / lead the following studies; • CSG Asset Safety Review. • Seconded to APA as Project Manager (internal project to realign management systems & technical departments so as to improve critical delivery). • Seconded as Project Manager responsible for the development of a plasma based hazardous waste disposal pilot plant (syngas production & power generation). • Discipline Lead for the detailed design of 340 gas well network supplying a 240 MMscfd compression facility. Capex +1.5 Billion. • Discipline Lead for Concept / Selection & FEED development of an adsorbent bed plant for heavy hydrocarbon (+C5) removal from a 50 MMscfd contaminated CSG stream upstream of an LNG plant. • Concept / Selection & pre-FEED of a compression facility (160 MMscfd, screw compressors) including TEG dehydration (Low Temperature Separation vs TEG sub-study), pig launcher & gas trunkline design. • Concept / Selection, FEED & Detailed Design of CSG wellhead 3 phase separation skids, gathering networks & gas flaring. • Pre-FEED of a 240 MMscfd gathering network and compression trunkline project. • Concept study for the stabilization of 500 bbl/day crude oil facility. • Life of field simulation and flow assurance study (including LPD and HPV placement) for a 110 well CSG network. Principal duties: project management delivery and reporting. Team leadership, ensuring Safety in Design, regulatory compliance. Client & vendor negotiations. Responsible for the full spectrum of technical deliverables: CAPEX, OPEX, Basis of Design, Control Philosophy, datasheets, process simulation & flow assurance. Technical calculations & drawings. HAZID, HAZOP, Hazardous Area assessments, SIL / LOPA studies, Technical Standards compliance, EHS compliance monitoring, fabrication QA/QC reviews, FATs. Gas Field Development based on type curve characterization. Based on my broad industrial experience I am able to provide multi discipline input (mechanical, electrical, instrumentation, structural). Show less
-
-
-
-
Engineering Manager (Coal)
-
Jan 2011 - Jul 2012
I was responsible for managing the infrastructure component for two of BMA’s major coal mining projects. Studies and Projects I lead the surface and underground infrastructure element of; • the Red Hill project’s feasibility study (approx AU$ 5.5 billion) and • the Saraji East Underground project (approx AU$ 6.5 billion). My responsibilities included; • Maximisation of the project’s NPV. • Risk assessments and mitigations. • Maintenance of engineering standards focusing on safety in construction and operation. • Multidisciplinary staff and consultant management. • Contract & contractor management. • Liaising with principal stake holders (both internal and external). • Project wide equipment and infrastructure Scope of Work determination (including open cut, underground, coal processing and allied infrastructure). • Development and adjudication of tenders. • Assisting with the development of Environmental Impact Statements • Compliance with environmental, statutory and local regulations / agreements. • Production of Capex, Opex and schedule estimates. • Benchmarking. Show less
-
-
-
-
Engineering Manager (UCG)
-
Nov 2009 - Nov 2010
Studies and Projects a) I lead the Pre Feasibility Study (PFS) for the study of power generation from Underground Coal Gasification (UCG). This study resulted in the design of a 200MW CCGT power plant with a pre-contingency Capex of AU$ 580 million. The study encompassed: power generation by gas turbines, gas engines and direct fired steam boilers, gas clean up and waste water treatment processes. I was responsible for leading the process conceptualisation and pre-FEED of this project from gas gathering and clean up through to waste water treatment and recycling. I was central in the development of the capex and opex estimates as well as the determination of the proposed plant’s economic evaluation. Operation b) I was involved with the commissioning and operation of a 10MW UCG test plant. My managerial responsibilities included; • The interviewing and appointing of engineers, • Guiding plant engineers and senior management with respect to plant design and modification, • Project cost control, • Routine office administration and staff management. My technical responsibilities included; • Contractor / consultant selection (local and international). • Technical vendor selection (local and international). • Foreign travel to selected conferences & symposia presentations. • Process safety and quality management. • HAZOP / HAZID studies, • PFD/ P&ID mass and energy balance development, • Process design of all unit operations, • Commercial and financial analysis of the proposed plant. My other duties included; • the presentation of a technical paper concerning the nature of UCG and Cougar Energy’s proposed application of that technology at the “Coal Gas 2010” conference (New Delhi, February). • Attending the “Power-Gen 2010” conference (Amsterdam, June) with a view to selecting the appropriate low BTU syngas turbines and associated plant for a 200 MW power station. I reported to the General Manager (Projects) and Managing Director. Show less
-
-
-
-
Technology Development Manager (Coal)
-
Jan 2008 - Nov 2009
Studies and Projects a) I developed both the business case and plant design of a vacuum based evaporative process for the bulk recovery of plant water from a waste mineral stream. I designed and costed a AU$ 25 million, 300tph plant for this purpose, b) I led the process engineering aspect of a definitive feasibility study for a Continuous Hydro Thermal Dewatering of Victorian lignite plant of 12 Mtpa with and estimated plant Capex = AU$1.9 billion. The process operating conditions were 300 oC and 100 bars. c) I developed both the business case and plant design of a commercial waste coal consuming pyrolysis/CTL plant. Feedstock flexibility will additionally allow the use of waste car tyre rubber. Direct and indirect liquefaction processes are currently under investigation. d) I investigated the business case and process design of a Methanol / DME from Carbon Dioxide plant. The purpose of this plant is to add value to carbon dioxide instead of simply treating it as cost intensive waste material that requires secure storage. e) I developed both the business case and plant design for the use of waste coal in on-site embedded power generation. The indicated capex for the 12.5MW boiler-turbine-generator plant is AU$35 million with a payback period of 5yrs. Show less
-
-
-
-
Lead Process Engineer (Coal & Hydrocarbons)
-
Sep 2006 - Jan 2008
Studies and Projects a) Assisted with a 6 Mtpa coal gasification feasibility study for a lignite miner. Product range included: diesel, methanol, DME, urea and electricity. I was involved in process design, equipment specification and selection. I am familiar with the current technologies and processes related to materials handling, coal gasification, chemical synthesis, power generation and effluent handling systems. b) Produced many of the P&ID’s and assisted with the control philosophy for the bulk water transfer pipeline of the Western Corridor Recycled Water Project, c) Assisted with the design and hydraulic study of a Geo-sequestration CO2 injection pipe line (FEED) d) Undertook the study and redesign of a refinery LPG terminal fire safety system, e) Was the Project Manager on an underground oil transmission pipeline project (EPCM). This was a 273km long DN200 buried crude oil pipeline operating at 13.5Mpa, with multiple riser stations (AU$ 86 million). Show less
-
-
-
-
Group Project Manager (Industrial Chemicals)
-
Apr 1999 - Aug 2006
I was involved in the shift operation of the fertilizer production plant. I lead the FEED, detailed design and execution of several brownfield EPC projects. Operations a) Fertilizer plant (ammonium phosphate, calcium nitrate, ammonium sulphate, ammonium nitrate) Projects b) Phosphoric Acid reactor c) Phospho-gypsum recovery plant d) Underground storage facility for flammable solvents, e) ANFO waste explosives disposal incinerator, f) Oil flash drying unit – FEED I was involved in the FEED of spray tower production of mono ammonium phosphate, de-fluorination of phosphoric acid, sodium silicate recovery from scrubber effluent and aluminium sulphate manufacture from spent refinery FCC catalyst. I assisted in the R&D and EPC of a new Nitro-Phosphate production plant. This work included market assessment, economic and logistic feasibility studies, plant design, equipment specification, supplier negotiations, project management, EPA negotiations and compliance as well as strategic planning with respect to local and international plant locations and capacities. Show less
-
-
-
-
Senior Process Engineer (Industrial Chemicals)
-
Apr 1994 - Mar 1999
I lead several brownfield D&C projects. Responsibilities included client liason, process design, production of PFDs, Mass & Energy balances, P&IDs. Site project management and plant commissioning. Operating manual production. Brownfield Projects - Design and Construct a) Gas fired furnace optimisation (ISCOR steel works), b) Power station boiler feedwater pH control (Arnot Power Station), c) Coal gasifier effluent water desalination RO / EDR (Sasol), d) Flue gas SCR plant (Columbus Stainless Steel JV). Show less
-
-
-
Karbochem (Dow Chemicals)
-
Sasolburg (South Africa)
-
Senior Chemical Engineer (Industrial Chemicals)
-
Feb 1987 - Mar 1994
I was involved in the shift operation of various operating plants. Responsibilities included process control, troubleshooting and process correction / modification. Trend analysis, data interpretation and reporting. I reported to the Plant Superintendant. I was involved in the in-house design and operation of several pilot plant scale projects. Operations a) Coke oven off gas processing and hydrocarbon recovery (BTEX plant), b) Fixed bed desulphurisation of Benzene (BTEX plant), c) Catalytic chlorination of phenol (DCP / TCP production), d) Synthetic rubber production plant (Styrene Butadiene Rubber & Ethylene Propylene Diene Monomer) Projects e) Design and operation of a solvent extraction pilot plant for chlorinated phenol, f) Design and operation of a solvent extraction pilot plant for ferric oxide pigments. Show less
-
-
Education
-
University of Natal (Durban, South Africa)
BSc Eng (chem), Chemical Engineering (hydrocarbons)
Community
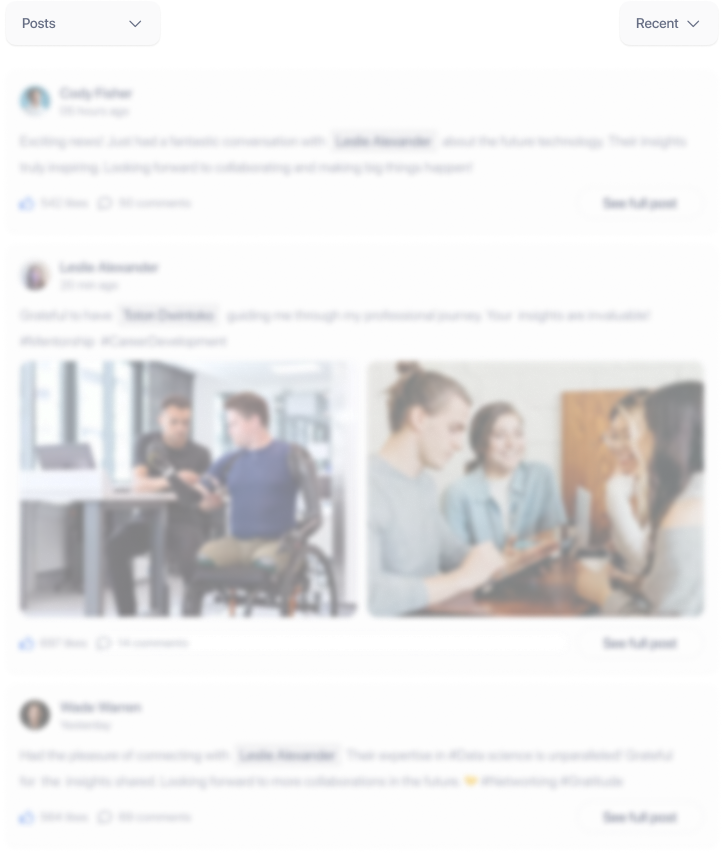