Rubik Hartounian
Director, Quality System at Promedica International- Claim this Profile
Click to upgrade to our gold package
for the full feature experience.
Topline Score
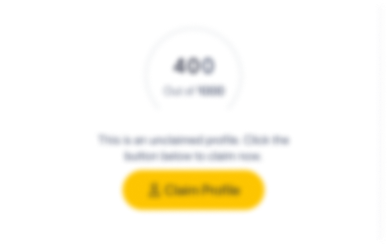
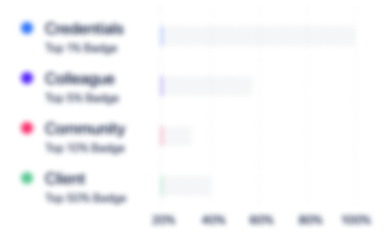
Bio

Paul Landesman
Rubik’s background and experiences provide thoughtful insight to his audits, focusing on critical parameters while insuring compliance to routine expectations. His interpersonal skills allow him to work with internal and external parties to provide clarity and solutions to complex issues. Rubik is solid performer in the Pharmaceutical and Medical Devices regulatory environment.

LinkedIn User
Rubik exemplifies leadership through effective management. In the time I worked with Rubik, he was able to set a good tone and work ethic for all departments. He pays great attention to detail while maintaining sight of overall goals. His good sense of foresight and proactive nature makes him a great team player. Rubik is an asset to any organization and it would a pleasure to work with him again.

Paul Landesman
Rubik’s background and experiences provide thoughtful insight to his audits, focusing on critical parameters while insuring compliance to routine expectations. His interpersonal skills allow him to work with internal and external parties to provide clarity and solutions to complex issues. Rubik is solid performer in the Pharmaceutical and Medical Devices regulatory environment.

LinkedIn User
Rubik exemplifies leadership through effective management. In the time I worked with Rubik, he was able to set a good tone and work ethic for all departments. He pays great attention to detail while maintaining sight of overall goals. His good sense of foresight and proactive nature makes him a great team player. Rubik is an asset to any organization and it would a pleasure to work with him again.

Paul Landesman
Rubik’s background and experiences provide thoughtful insight to his audits, focusing on critical parameters while insuring compliance to routine expectations. His interpersonal skills allow him to work with internal and external parties to provide clarity and solutions to complex issues. Rubik is solid performer in the Pharmaceutical and Medical Devices regulatory environment.

LinkedIn User
Rubik exemplifies leadership through effective management. In the time I worked with Rubik, he was able to set a good tone and work ethic for all departments. He pays great attention to detail while maintaining sight of overall goals. His good sense of foresight and proactive nature makes him a great team player. Rubik is an asset to any organization and it would a pleasure to work with him again.

Paul Landesman
Rubik’s background and experiences provide thoughtful insight to his audits, focusing on critical parameters while insuring compliance to routine expectations. His interpersonal skills allow him to work with internal and external parties to provide clarity and solutions to complex issues. Rubik is solid performer in the Pharmaceutical and Medical Devices regulatory environment.

LinkedIn User
Rubik exemplifies leadership through effective management. In the time I worked with Rubik, he was able to set a good tone and work ethic for all departments. He pays great attention to detail while maintaining sight of overall goals. His good sense of foresight and proactive nature makes him a great team player. Rubik is an asset to any organization and it would a pleasure to work with him again.

Experience
-
Promedica International, A California Corporation
-
Pharmaceutical Manufacturing
-
1 - 100 Employee
-
Director, Quality System
-
Oct 2022 - Present
Head of the Quality Management SystemOversee and provide direction to the Quality Department for Clinical Trial Quality support, Audits, Regulatory Compliance, Process Improvements, Validation, and strategic planning.
-
-
Quality System Manager
-
Jun 2020 - Oct 2022
Manage and provide direction for the Quality SystemClinical Study Quality Assurance SupportTrial Master File Review and AuditsProtocol Development and ReviewInternal/External/Supplier AuditsCAPA ProgramComplaints and Feedback ProgramTraining Program
-
-
-
Abbott
-
United States
-
Hospitals and Health Care
-
700 & Above Employee
-
Sr. Manager, Clinical Quality (Global Role)
-
Mar 2019 - Jun 2020
Owner of the global Clinical Quality CAPA ProgramResponsible or the Securing Compliance process for clinical trials.Regulatory Agency and Notified Body inspections/audits (i.e. FDA BIMO, etc.) Regulatory Surveillance and related gap analysesEU MDR Readiness activity and related internal updatesProject participation data review and monitoring plansInvestigation site inspection readiness activitiesConduct Internal AuditsBudget preparation and reviewSupport the management review process
-
-
-
Doheny Eye Institute
-
United States
-
Non-profit Organizations
-
100 - 200 Employee
-
Head Of Compliance
-
Oct 2018 - Feb 2019
Accountable for all GCP compliance decisions and providing overall direction for the organization for GCP compliance related topics. Provide the overall strategy for the validation program and the validation of electronic systems. Process owner for external inspections/audits, internal audits, supplier quality management. Review/approval authority on non-conformances, CAPAs, change management, and other key Quality System elements. Providing subject matter expertise to enhance the Quality Management System, System Development Life Cycle (SDLC), Computer System Validation (CSV), and other areas to improve compliance with 21 CFR Parts 11, 50, 312, 812, Privacy and HIPAA (45 CFR Parts 160, 164), ICH E6(R2) Good Clinical Practices (GCP), ISO 9001, and GAMP 5.
-
-
Compliance SME Consultant (Head of Compliance)
-
Jul 2016 - Sep 2018
Accountable for all GCP compliance decisions and providing overall direction for the organization for GCP compliance related topics. Provide the overall strategy for the validation program and the validation of electronic systems. Process owner for external inspections/audits, internal audits, supplier quality management. Review/approval authority on non-conformances, CAPAs, change management, and other key Quality System elements. Providing subject matter expertise to enhance the Quality Management System, System Development Life Cycle (SDLC), Computer System Validation (CSV), and other areas to improve compliance with 21 CFR Parts 11, 50, 312, 812, Privacy and HIPAA (45 CFR Parts 160, 164), ICH E6(R2) Good Clinical Practices (GCP), ISO 9001, and GAMP 5.
-
-
-
Medtronic
-
United States
-
Medical Equipment Manufacturing
-
700 & Above Employee
-
Sr. Compliance Manager, Internal Audit and Training
-
Sep 2014 - Jun 2016
Manager and Program Owner for the Internal Audit and the Quality System Training Programs* Lead the training and audit teams in their daily activities and problem solving to ensure a compliant, effective and efficient training program and internal audit program* Responsible for issuance of and adherence to annual internal audit schedule, through direct performance of audits as well as management of auditing staff* Responsible for facilitating and hosting external audits, assessments and inspections of the quality system* Responsible for ongoing execution and improvement of the quality system training program through direct activities as well as through oversight and prioritization of training staff activities* Provides expertise and guidance in interpreting US and foreign governmental regulations, agency guidelines, and internal/corporate policies to ensure compliance is maintained. These include 21 CFR 4, 11, 58, 210, 211, 600, 820, ISO: 13485, 14971, 17025, Medical Device Directive, Eudralex Volume 4, CMDR, JPAL, ANVISA, and other global regulations and standards* Drive continual improvement projects and CAPAs for the department’s processes and participate as independent reviewer of CAPAs from all areas.* Participate in Quality Management Review providing status and metrics on the Internal Audit and Quality System Training Programs* Participate in and lead process improvement project teams and global Medtronic Training Sub-Council, Audit Sub-Council, and Combination Products Project Team.
-
-
-
Allergan
-
Pharmaceutical Manufacturing
-
700 & Above Employee
-
Senior Manager, Worldwide Quality Assurance
-
Sep 2009 - Aug 2014
• Head of the global internal and supplier audit program for pharmaceutical, medical device, biologics, and combination product manufacturing sites and regional offices.• Tracking internal and external compliance trends and news to support global compliance strategy including updates to global quality standards.• Conduct comprehensive due diligence quality audits for partnerships and participate in new product launch core team.• Host and co-host external regulatory inspections (FDA, ISO, etc.) and related response preparation and CAPAs.
-
-
Manager, Worldwide Quality Assurance
-
May 2007 - Sep 2009
Manage internal and supplier audits. Perform risk assessment to determine risk priority for audits of suppliers. Perform trend analysis and prepare presentations for the Quality System Management Review. Manage notified body and FDA inspections. Review/approve audit reports and audit responses. Track responses to audit observations. Ensure meeting targeted budgets. Train team members.
-
-
-
K.C. Pharmaceuticals, Inc.
-
United States
-
Pharmaceutical Manufacturing
-
1 - 100 Employee
-
Director, Quality Assurance
-
Mar 2003 - Apr 2007
• Directed and was the final approval on the following:o Final Product Releaseo Validation of facility, equipment, processes, and methods.o Pharmacovigilance and device-vigilance activities including Medical Device Reporting (MDR) and recalls.o Exception Management (deviations, CAPAs, OOS, OOT)o Supplier Quality Management (vendor approvals)o Change Management Process (all change controls)o Labeling (e.g. Master Labeling/Packaging Records)o Design Control (prepared retrospectively for grandfathered products)• Personal accountability and responsibility for:o Complaint handing system including complaint investigations, complaint data analysis, and complaint trending.o Annual product reviews for 9 product lineso Preparation of import dossiers for products exported to Canadao Regulatory registrations such as Drug Master Files (DMF), and facility registration updates.o Prepared a 510K for a Class II sterile medical device including bench, animal, and clinical studies• Complete quality system overhaul• Under my leadership, the Validation program was significantly enhanced to meet today's standards.• Improved the Exception Management program to include Cause and Effect Analysis, Plan/Do/Check/Act, DMAIC, and Kaizen when necessary.• Enhanced the Management Review process by including Key Process Indicators, Process Capability (Cpk), Control Charts, Trends, and Dashboard. Chaired the Management Review meetings.• Prepared and managed the Quality Assurance budget in excess of $1.5M.• 5 Direct reports with as high as 15 indirect reports
-
-
-
-
Specialist, Quality Assurance
-
Sep 2002 - Feb 2003
• Final review of all batch records and the release of all Biologic raw materials (human plasma) before shipment to a cryogenic storage facility. These materials would then be utilized for manufacturing of plasma derived biologics.• Inspection and release of all incoming raw materials (reagents) and soft-goods (plasma collection single-use medical devices)• Compliance review and audit of all records in the plasma collection facility including test results and certificates of analysis• Preparation and submission of Biologic Product Deviation Reports (BPDRs)• Reviewed GCP documents within the batch records associated with an on-going clinical study.
-
-
Education
-
California State University, Los Angeles
BS, Microbiology
Community
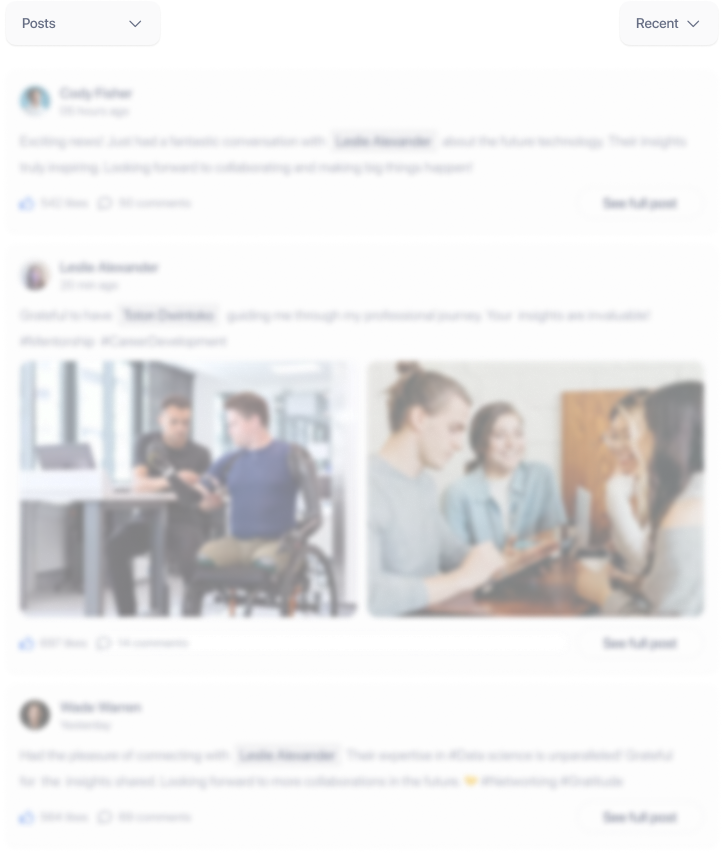