Shawn Silvey
Director Of Quality at Brad Foote Gear Works- Claim this Profile
Click to upgrade to our gold package
for the full feature experience.
Topline Score
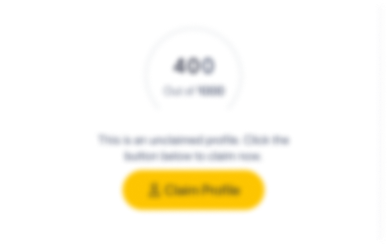
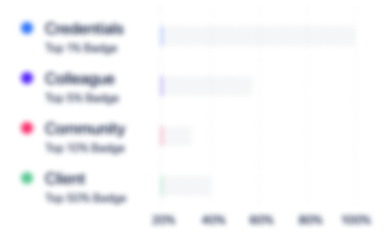
Bio


Experience
-
Brad Foote Gearing
-
Machinery Manufacturing
-
1 - 100 Employee
-
Director Of Quality
-
Jun 2021 - Present
-
-
-
Meritor
-
United States
-
Motor Vehicle Manufacturing
-
700 & Above Employee
-
Quality Manager
-
2019 - May 2021
Meritor purchase of US Gear Meritor purchase of US Gear
-
-
-
US Gear Meritor Chicago
-
US Gear Division, Chicago Illinois
-
Quality Manager
-
2015 - May 2021
Manufacturer and Heat Treater of Automotive Gears, Shafts, and Axle Assemblies – Quality Manager 2015 - Present KEY ACHIEVEMENTS ★ Manages the Quality Department, including twelve technicians and two quality engineers, gear lab/heat treat lab profiling and analysis, process and product improvement, and efficiency through corrective and preventive actions utilizing Six Sigma practices, 8D, and 3 Legged 5Y tools. ★ Maintain and certify ISO 9001 QMS, including revising, managing, and improving all plant-wide processes and work instructions. ★ Enables APQP new product development/launches by testing prototypes via in-process inspections to ensure design compliance, including process flows, PFMEA’s, Control Plans, in-process inspection procedures, AIAG PPAP’s, and ongoing product validation. ★ Manages full gage calibration and the gage design lab for more than 2,500 gages while overseeing DMNs and containment issues for customers such as Dana, Eaton & Poclain, in addition to developing lean manufacturing practices. ★ Executed the ISO 9001:2008 recertification audit with two minor findings, three surveillance audits with three minor results, and a transition recertification audit of ISO 9001:2015 Standards with two minor findings. Show less
-
-
-
Funk Linko
-
United States
-
Railroad Equipment Manufacturing
-
1 - 100 Employee
-
Director Quality & Operations
-
2014 - 2015
Custom Fabrication and Welding of Metal Products Oversaw the development, implementation, and maintenance of Production Operational Systems and Quality Management Systems to meet AWS (American Welding Society), AAR (Association of American Railroads), and ISO 9001 standards. Developed a complete operational metrics dashboard, including strategic goals and objectives for all operations, managed sales, office, and production operating costs and expenses while increasing profitability and efficiency. Delivered input to develop the product strategy and improve research and development of new/emerging products and defined responsibilities of the assigned organization and staff positions to accomplish business objectives. Established production and quality standards, developed budget and cost controls and obtained data regarding the types, quantities, specifications, and delivery dates of products ordered. Maintained zero non-compliances regarding the Association of American Railroads Section J Specification for Quality Assurance M-1003 while developing the sales team. Show less
-
-
-
-
Quality Manager
-
2011 - 2014
• Redeveloped and implemented a strategic plan for a comprehensive quality management system using ISO 9001:2008, AS9100 and TS-16949 from door-to-door. • Defined all operational processes, including raw material purchasing, material identification, control, quality processes, manufacturing process, warehouse and inventory, shipping, invoicing, and billing. • Led process improvement initiatives and corrective actions to increase organizational efficiency, while increasing profitability through combined initiatives. • Spearheaded full process audits and improvement initiatives that led to passing three ISO Surveillance audits and one full Recertification audit - the audits were conducted by a third-party International Registrar with no corrective actions. Key Accomplishments: • Recruiting, interviewing and developing salaried leadership team • 26.7% reduction in quality defects • 21% increase in operational efficiency • 3.5 % increase in profitability through combined initiatives Show less
-
-
-
-
Vice President
-
2006 - 2011
• Designed and generated creative funding and financing structures for multi-billion-dollar initiatives by collaborating with clients. • Developed business plans, proformas and full financials for clients, including hedge funds, Wall Street Banks, international capital markets divisions, pension funds, and other funding sources such as The World Bank Group in the manufacturing sector. • Delivered knowledge and experience in international financial markets, hedge fund management, pension fund management/ investments, retail/commercial mortgage, lending industry, and SEC and Federal Reserve compliance requirements. • Founded and established relationships and “pipelines” in the financial markets for MTN transactions, Currency Swap transactions, asset leveraging, financial instrument leveraging, commodities transactions, and other diverse financial initiatives. Show less
-
-
-
Cherry Creek Mortgage, LLC
-
United States
-
Financial Services
-
400 - 500 Employee
-
Commercial & Residential Loan Originator and Lender
-
2006 - 2009
Provide appropriate funding for commercial loans. Any project considered from smaller development to economic infrastructure support. Provide trusted financial counseling to clients and provide funding or find appropriate funding for the loan needs. Determine if project needs a local lender or Wall Street support and provide for those needs. Mezzanine, hard money, perm, joint venture, equity partners all part of the portfolio available. Capable of lending and conduits from $500K to multi-billion dollar proposals and everything in between. Show less
-
-
-
PartyLite
-
United States
-
Manufacturing
-
700 & Above Employee
-
Quality & Warehouse Manager
-
May 2003 - Sep 2006
Assumed dual roles, managed the QA and QC technical staff. Reported to the Operations Manager, District Operations Manager and National Corporate Quality Director. Performed Six Sigma and Kaizen style product, process, system analysis and improvement. Served as an internal consultant for quality process improvement across multiple facilities and developed and facilitated team leadership and facilitation courses. Designed and analyzed cause and effect data to implement district level corrective actions. Show less
-
-
-
George S. May International
-
United States
-
Business Consulting and Services
-
1 - 100 Employee
-
Chief of Quality Systems Consulting US & Canada
-
Jul 2002 - Mar 2003
Re-designed, implemented, managed and trained all quality management systems consulting in 2 of 3 international divisions. Redeveloped the George S. May International Quality Management System Standard based on ISO-9001:2000. Performed Quality Needs Assessment audits at client facilities and trained field staff in management systems consulting Re-designed, implemented, managed and trained all quality management systems consulting in 2 of 3 international divisions. Redeveloped the George S. May International Quality Management System Standard based on ISO-9001:2000. Performed Quality Needs Assessment audits at client facilities and trained field staff in management systems consulting
-
-
-
Grotefeld Hoffmann Schleiter Gordon & Ochoa LLP
-
Law Practice
-
1 - 100 Employee
-
Consultant to Firm
-
Nov 2001 - Jul 2002
Performed full financial systems auditing after dismissal of CFO. Financial audits resulted in recovery of funds in excess of $500K. Modified and created significant improvement of financial reporting accuracy due to incorrect accounting practices. Audits resulted in restructuring financial tracking process to ensure accuracy which ‘recovered’ funds in P&L accounts which had been incorrectly posted and ledgered. Development and application of appropriate processes required to ensure ongoing accuracy in posting and tracking of trust funds and litigation awards. Show less
-
-
-
Qualex
-
Consumer Goods
-
100 - 200 Employee
-
QA & QC Manager
-
Jan 2000 - Sep 2001
Assumed dual roles, managed the QA and QC technical staff. Reported to the Operations Manager, District Operations Manager and National Corporate Quality Director. Performed Six Sigma and Kaizen style product, process, system analysis and improvement. Served as an internal consultant for quality process improvement across multiple facilities and developed and facilitated team leadership and facilitation courses. Designed and analyzed cause and effect data to implement district level corrective actions. • Created and integrated strategic quality planning into the lab’s strategic business plan. • Reduced complaints and operations costs and introduced quality indicators through multi-facility Six Sigma team development, facilitation and leadership. Accountable for reducing costs, waste and customer complaints. Key accomplishments: • Reduced total PPM defects by 39%, reduced photo redo complaints by 67% avg./mo in 9 months. • Introduced Six Sigma Master Black Belt style team development, process mapping, cause and effect analysis and DMAIC (define, measure, analyze, improve, control), process improvement techniques, which reduced ops defects by 44% and complaints by 23%. • Applied Six Sigma Project, Kaizen, and lean manufacturing, reducing paper waste by 24%. • Achieved annualized savings of gross operating expenses by 2% to 3% through combined Master Black Belt style quality initiatives. • Increased departmental productivity, efficiency and PM of equipment through Kaizen and Six Sigma. • Brought facility and district quality to a 4.3 sigma level, a 1 sigma improvement in 18 months Show less
-
-
-
Elkay Manufacturing
-
United States
-
Manufacturing
-
400 - 500 Employee
-
Process Engineer, Quality Coordinator
-
Jan 1997 - Dec 1999
Led the quality and manufacturing shop floor activities and managed the Quality staff. Conducted Six Sigma Black Belt style project management including lean manufacturing production optimization, waste reduction and reporting, defect reduction and identification, and Six Sigma type data collection systems. Led and facilitated cross-functional process, project, and customer problem solving teams using employee empowerment methods and principles. • Revised and developed manufacturing and quality processes, documentation, procedures and systems. • Upgraded the departmental staff to technician level by restructuring positions and training. Managed department during manager replacement search. • Led the process team that reduced customer rework by 30% in 1 quarter. • Created a budget that reduced prior year costs by 10% resulting in a 20% favorable balance. • Developed and implemented a scrap tracking & reporting system that integrated multiple vendors into a previously single supplier facility. • Implemented an electronic bar coded data collection system. Show less
-
-
-
WMS Gaming
-
United States
-
Gambling Facilities and Casinos
-
300 - 400 Employee
-
Production Support Engineer, QA Engineer
-
Jan 1995 - Jan 1997
Identified and resolved manufacturing, design, process and product issues. Developed and facilitated training programs and served as liaison for design engineering departments, manufacturing, purchasing, quality, industrial engineering and planning. Conducted root cause identification and analysis of quality issues. Identified and resolved supplier defect issues. • Developed, improved, mapped and documented processes for manufacturing and quality. • Redesigned testing procedures for the manufacturing lines and trained staff. • Supported production and engineering in the start up of a lean manufacturing, turnkey plant. Show less
-
-
-
-
Quality Administrator
-
Oct 1987 - Dec 1995
Designed and implemented a team based, continual improvement quality system that exceeded Eaton EQ-1 and Ford Q-1 standards. Implemented a statistical process control program (SPC), documented procedures, developed quality assurance manuals and created quality policies and guidelines. Developed and implemented supplier raw material standards and an employee-run quality system, facilitated a problem solving and corrective action program that reduced production related claims, rejects and defects by 24% in 2 years and developed a material identification and control procedure that eliminated material mix ups in the plant and eliminated scrap and rework. Show less
-
-
Education
-
Elmhurst College
Bachelor of Science (BS), Business Administration, Management and Operations
Community
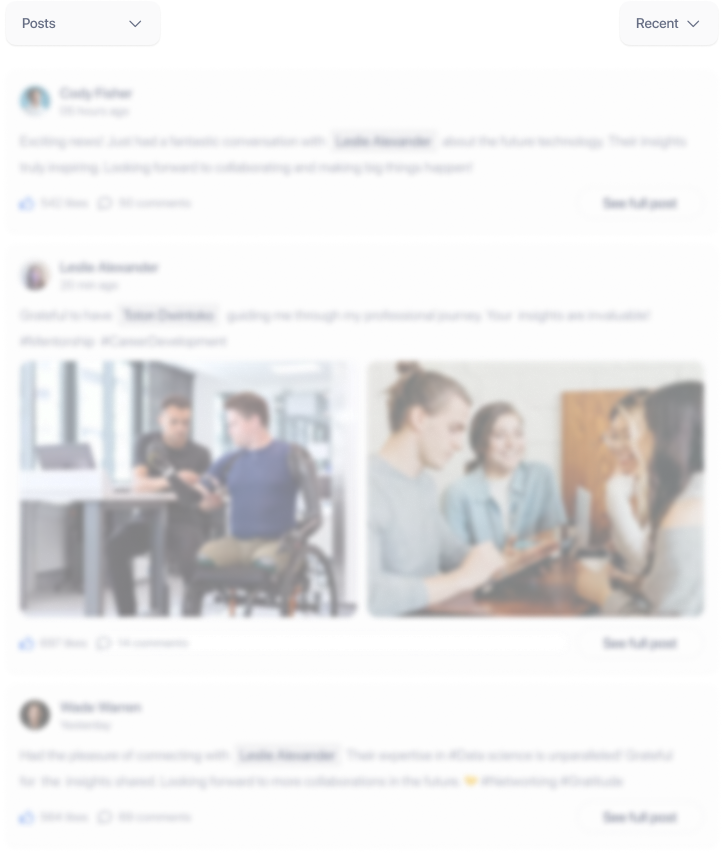