Lei Zhao
Industrial Engineer - ME Powertrain at Mercedes Benz- Claim this Profile
Click to upgrade to our gold package
for the full feature experience.
-
English Full professional proficiency
-
Chinese Native or bilingual proficiency
Topline Score
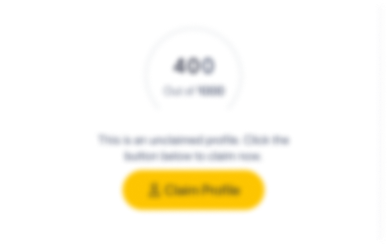
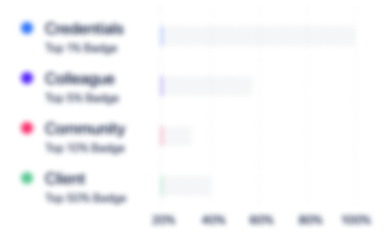
Bio


Credentials
-
MTM-C VALUES CERTIFICATION
German MTM AssociationFeb, 2016- Oct, 2024 -
MTM-1-QUALIFICATION CERTIFICATE
International MTM DirectorateDec, 2015- Oct, 2024 -
MTM-SD-QUALIFICATION CERTIFICATE
German MTM AssociationDec, 2015- Oct, 2024
Experience
-
Beijing Benz Automotive Co., Ltd.
-
China
-
Motor Vehicle Manufacturing
-
100 - 200 Employee
-
Industrial Engineer - ME Powertrain
-
Jul 2015 - Present
• Conducted detailed MTM (Methods-Time Measurement) analysis for all current manual stations among 4-cylinder assembly lines (M274 & M270), final assembly line (flywheel assembly), cylinder head pre-assembly lines as well as cold test area. • Reduced totally 72 headcount (12 operators/line x 3 lines x 2 shifts/line); decreased line cycle time from 117 sec. to 112 sec. and improved operators' ave. workload from 72% to 89% through implementing line balancing project among all three 4-cylinder assembly lines. • Supported in new product planning (M264 project); initiated planning MTM analysis for new/changed parts based on 3D model and formed draft process document. • Established and promoted standard time management process within entire engine plant including set up new product/process standard time and manage current standard time changes due to process improvement/product change. • Promoted and applied ergonomics (human factors) within engine plant; set ergonomic standard and evaluation process; lead secondary assessment of ergonomic risks and supported in solving ergonomic problems. Show less
-
-
-
TOPRE CORPORATION
-
Japan
-
Law Practice
-
1 - 100 Employee
-
Industrial Engineer ( Press Gorika Team)
-
Apr 2013 - Jun 2015
Leading and implementing complex kaizen projects to improve plant materials’ handling and storage, press operations, production/inventory control, space utilization and reduce waste and cost. • Improved forklift operations, floor space utilization and inventory management (100% FIFO) by implementing a universal flow rack system to accommodate WIP parts with various demand volume and varieties of packaging, which also reduced press and assembly downtime, safety concerns, shipment of defective parts and missed shipment; Estimated annual cost saving is $450,000 and total space saving is 23,000 sq.ft. • Created a highly-organized WIP layout through reorganizing pallet racks, centralizing empty container storage area and modifying pedestrian and forklift aisles; increased space expansion opportunities for new programs (including WIP parts, blanks, coils and dies) as well as current model design change. • Planned and reorganized blank racks to fit both current and new programs and achieve better floor space efficiency and material flow; developed effective method to make blank rack labels more striking and long-lasting. • Standardized blank rotator and blank rack beam locations by figuring out the common fork positions among the destackers of transfer lines (2500T) and tandem line (4500T), which will dramatically reduce unnecessary fork repositions. • Conducted press machine capability analysis, balanced machines through rearranging jobs to reduce operators’ overtime. Show less
-
-
-
Asia Pulp & Paper
-
Indonesia
-
Paper and Forest Product Manufacturing
-
700 & Above Employee
-
Industrial Engineer Intern/Team Leader
-
Jul 2012 - Sep 2012
Played lead role in standardizing 2860-210 folding machine assembly line, promoting 5S methods and visual management facility-wide, and designing 5S audit sheets to promote continued practice. Built consensus for key overhauls by demonstrating effectiveness to other team members, plant employees, and corporate leadership. • Reducing training time from 7 to 3 days by directing team in developing Standard Operating Procedures (SOP’s) for 2860-210 folding machine assembly line. • Improved efficiency and reduced waste by performing time and motion studies to enhance working sequences and achieve more accurate standard time to guide production progress. • Reduced assembly line cycle time 50% by implementing 5S methodology overhauling folding machine assembly workplaces and increasing cleanliness and safety of storage areas. • Chosen to design layout of new plant using AUTOCAD, assuring optimal cost efficiency and material flow and improving plant capacity to satisfy customer expectations regarding paper processing technologies. Show less
-
-
-
Shougang Group
-
Industrial Machinery Manufacturing
-
1 - 100 Employee
-
Production Engineering Intern (Production Safety Management)
-
Aug 2010 - Sep 2010
• Investigated the workers' working conditions in steel-making and rolling plant; determined the corresponding dangerous level and proposed necessary countermeasures to reinforce the safety. • Analyzed potential unsafe factors in major job shops and composed appropriate Safety Check Lists (SCL), which could effectively avoid the occurrences of accidents. • Improved the inappropriate equipment layout in the sintering plant by rearranging the conveyor which dramatically reduced the underlying safety risks. Show less
-
-
-
Mine Rescue Environment Simulation Laboratory
-
University of Science & Technology Beijing
-
Research Assistant (Team Leader)
-
Apr 2009 - Apr 2010
Team leader: • Created an optimized air conditioner which integrated three functions: oxygen supply, carbon dioxide removal and carbon monoxide absorption. • Researched the optimal method to make oxygen preparation highly efficient using sodium chlorate decomposition, which achieved a higher reliability with low cost and simpler reaction. • Proposed an economic way to absorb the low concentration of carbon dioxide by sodium lime. • Summarized the most convenient and effective method of eliminating carbon monoxide: copper catalyst absorption, which reached high catalytic activity, absorption efficiency and feasibility. • Managed team members in scheduling and task allocation, reported progress regularly to the supervisor. • Published the corresponding paper in the National Key Journal "City Construction". Show less
-
-
Education
-
University of Michigan
Master of Science (M.S.), Industrial & Operations Engineering -
University of Science and Technology Beijing
Bachelor of Engineering, Safety Engineering
Community
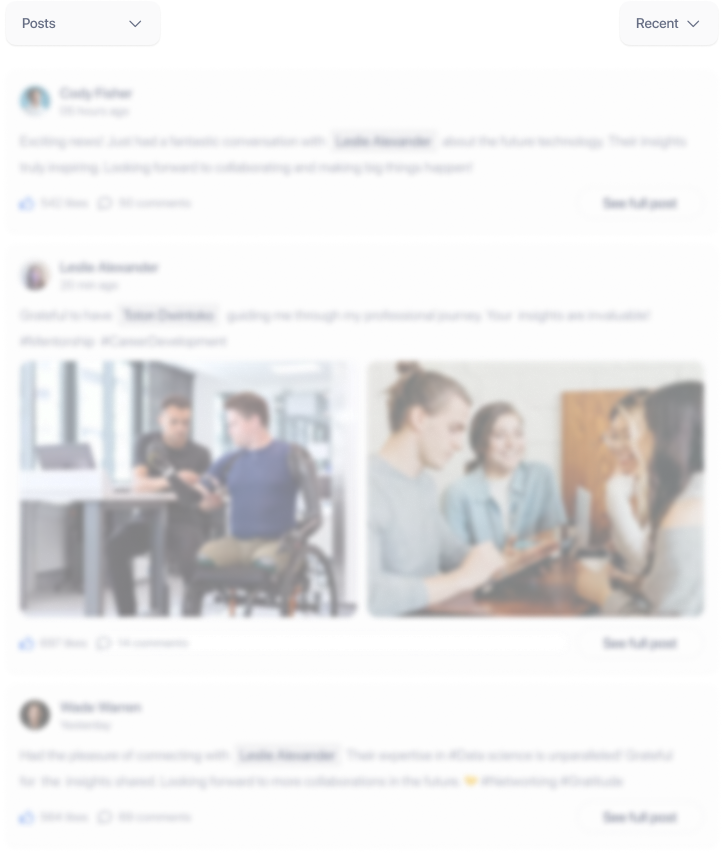