David Brow
Tool Install Support Engineer at Nissin Ion Equipment USA- Claim this Profile
Click to upgrade to our gold package
for the full feature experience.
Topline Score
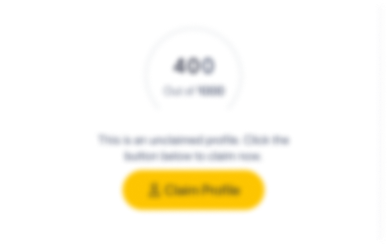
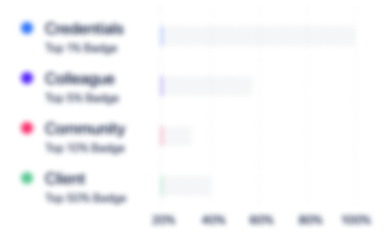
Bio

Mark Allen
It is my great privilege to recommend Mr. Brow . It has been a rare pleasure to work with someone with a wide ranging skill set who is always successful in whatever is attempted. As a Manufacturing Engineer, I had often sought David’s knowledge for product improvement feedback and technical information. Recently I had the honor of working alongside him at a customer site in Dresden, Germany during the first install of a newly developed tool. He genuinely understood how to meet, then exceed the customer’s needs using his knowledge of the product, communication skills, teamwork, and tireless work all blended with a delightful sense of humor. I feel any organization would be well served by his participation.

Marie Graichen, MBA
David is an outstandingTest/Install representative with strong customer service skills. He works well as a member of a team and is very professional in dealing with customers. David was a former "Employee of the Month" while at Tokyo Electron Massachusetts, due to his work achievements. He would be an asset to any organization .

Mark Allen
It is my great privilege to recommend Mr. Brow . It has been a rare pleasure to work with someone with a wide ranging skill set who is always successful in whatever is attempted. As a Manufacturing Engineer, I had often sought David’s knowledge for product improvement feedback and technical information. Recently I had the honor of working alongside him at a customer site in Dresden, Germany during the first install of a newly developed tool. He genuinely understood how to meet, then exceed the customer’s needs using his knowledge of the product, communication skills, teamwork, and tireless work all blended with a delightful sense of humor. I feel any organization would be well served by his participation.

Marie Graichen, MBA
David is an outstandingTest/Install representative with strong customer service skills. He works well as a member of a team and is very professional in dealing with customers. David was a former "Employee of the Month" while at Tokyo Electron Massachusetts, due to his work achievements. He would be an asset to any organization .

Mark Allen
It is my great privilege to recommend Mr. Brow . It has been a rare pleasure to work with someone with a wide ranging skill set who is always successful in whatever is attempted. As a Manufacturing Engineer, I had often sought David’s knowledge for product improvement feedback and technical information. Recently I had the honor of working alongside him at a customer site in Dresden, Germany during the first install of a newly developed tool. He genuinely understood how to meet, then exceed the customer’s needs using his knowledge of the product, communication skills, teamwork, and tireless work all blended with a delightful sense of humor. I feel any organization would be well served by his participation.

Marie Graichen, MBA
David is an outstandingTest/Install representative with strong customer service skills. He works well as a member of a team and is very professional in dealing with customers. David was a former "Employee of the Month" while at Tokyo Electron Massachusetts, due to his work achievements. He would be an asset to any organization .

Mark Allen
It is my great privilege to recommend Mr. Brow . It has been a rare pleasure to work with someone with a wide ranging skill set who is always successful in whatever is attempted. As a Manufacturing Engineer, I had often sought David’s knowledge for product improvement feedback and technical information. Recently I had the honor of working alongside him at a customer site in Dresden, Germany during the first install of a newly developed tool. He genuinely understood how to meet, then exceed the customer’s needs using his knowledge of the product, communication skills, teamwork, and tireless work all blended with a delightful sense of humor. I feel any organization would be well served by his participation.

Marie Graichen, MBA
David is an outstandingTest/Install representative with strong customer service skills. He works well as a member of a team and is very professional in dealing with customers. David was a former "Employee of the Month" while at Tokyo Electron Massachusetts, due to his work achievements. He would be an asset to any organization .

Credentials
-
OSHA 30-Hour General Industry Safety and Health
OSHA Training Institute Education Center at Great Lakes OSHA Education CenterMay, 2019- Nov, 2024 -
Hydroelectric Machinery Mechanic
U.S. Department of LaborJan, 2003- Nov, 2024 -
EPA CFC/CHFC Refrigerant Processing Certification - Universal
United States Department of DefenseJan, 1998- Nov, 2024
Experience
-
Nissin Ion Equipment USA
-
United States
-
Semiconductor Manufacturing
-
1 - 100 Employee
-
Tool Install Support Engineer
-
Aug 2020 - Present
-
-
Field Service Engineer
-
Jul 2014 - Present
Managed and performed installation of Medium Current Ion Implantation Manufacturing Equipment (including specialized Ion Implanter designs to cater to the various needs of the customer). Provided on site service/support for daily operations and on-hands training regarding this equipment when the company schedule required. Responsible for system set-up and debugging to ensure the health of the system for return for process verification and return to production. Was able to travel as needed to fulfill either installation and set-up needs or on site support. Developed several work flow procedures to ensure the smooth transition of information from the supply side to the customer side. Show less
-
-
-
Tokyo Electron US
-
Japan
-
Semiconductor Manufacturing
-
700 & Above Employee
-
Etch Systems Installation and Modification Engineer
-
Jan 2014 - May 2014
Managed and performed modifications and installation of Reactive Ion Etch and Surface Preparation Semiconductor Manufacturing Equipment. Coordinated all maintenance actions for the projects including IBM resources to ensure a safe and smooth evolution keeping projects under budget and on time. Tasks included in depth pre-task planning (project management) to identify potential stop gaps and eliminate them to ensure the tasks were complete safely and in a timely manner. Responsible for system set-up and debugging to ensure the health of the system for return for process verification and return to production. Show less
-
-
Etch Systems Technical Lead
-
Mar 2013 - Jan 2014
Responsible for escalation management and development of escalation solution to address advance system failures. Trained personnel in troubleshooting methods (KT) and equipment operation and maintenance. Developed several Best Known Methods. Instructed personnel on the use and analysis of Statistical Process Controls and how to apply the data collected to create viable action plans that would lead to quick resolution of out of control processes and mechanical performance.
-
-
Etch Systems Enginneer in Charge and Field Service Engineer III
-
Apr 2010 - Mar 2013
Managed and coordinated 10-13 personnel across two shifts (Day 1 and Night 1) regarding matters of troubleshooting and repair of Reactive Ion Etch Equipment as prioritize by the customer. Attended and lead daily production and manpower meetings with the customer reviewing maintenance needs to properly allocate resources to correct the issues in a timely manner. Developed and maintained shift personnel scheduling. Managed escalation reports and developed advanced troubleshooting solutions during escalation calls. Show less
-
-
-
Tokyo Electron US
-
Japan
-
Semiconductor Manufacturing
-
700 & Above Employee
-
FINAL TEST AND INSTALLATION TECHNICIAN III
-
Jan 2007 - Apr 2009
Production Test Technician III Performs the set-up, calibration, testing and troubleshooting of circuits, components, instruments and mechanical assemblies. Determines and may develop test specifications, methods and procedures from blueprints, drawings and diagrams. Tests and troubleshoots assemblies and/or final systems. May complete rework on assemblies and/or systems as a result of testing. Prepares technical reports summarizing findings and recommending solutions to technical problems. May assist in the selection and set-up of specialized test equipment. Show less
-
-
-
-
RESEARCH AND DEVELOPMENT REFRIGERATION TECHNICIAN
-
Jan 2006 - Dec 2006
Conducted system assembly, testing, and analysis on innovative personal cooling refrigeration systems utilizing Fluke data acquisition systems to acquire statistical data of operations; including, but not limited to, temperatures, pressures, rotations per minute, and flow rates. Performed numerous calculations to determine the following: power consumption, power output, flow rates, airflow, and other various thermal properties. Tasks included system assembly, brazing of aluminum to aluminum, aluminum to copper and copper to copper tubing and components. System flushes and cleaning was mandatory post assembly to ensure the systems were free of any contaminations and placed onto vacuum systems for integrity tests ensuring the systems were free of air and non-condensables that degrade refrigeration system performance. Tests were also conducted to ensure proper system operational balance and adjustments were made to improve Saturation Temperatures and cooling capacities. Show less
-
-
-
US Navy
-
United States
-
Armed Forces
-
700 & Above Employee
-
ENGINEERING TRAINING DEPARTMENT SUPERVISOR (NEC 9502) and MACHINIST’S MATE
-
Oct 2002 - Nov 2005
As the Leading Petty Officer, supervised 14 instructors specializing in mechanical applications on board United States Submarines, oversaw 13 courses of curriculum to be delivered to new and veteran submariners. Handpicked to receive and deliver specialized training using my excellent communication skills to instruct other personnel in the operation, preventive maintenance, troubleshooting and repair of gas/fluid systems, valves, and machinery. Made significant contributions, which allowed the command to earn excellent ratings in administration and mechanical safety during a Nuclear Propulsion Examination Board. Learned the value of being an effective leader and team supporter to provide maximum productivity while ensuring the highest quality work. Certified as a Master Training Specialist ensuring the highest quality of technical knowledge was presented in a clear and concise manner. Show less
-
-
SENIOR TECHNICIAN and MACHINIST’S MATE
-
Dec 1996 - Oct 2002
Qualified ahead of my peers for critical leadership positions and was placed in charge of preventive and corrective maintenance, and troubleshooting on all systems involving hydraulics, gas/fluids, refrigeration, diesel engines and fire fighting. Selected to rebuild an entire high pressure air system (4500 psi), including three high pressure air compressors and over 100 valves in three weeks, a mission critical repair. Earned qualification as the Chief of the Watch, and Duty Chief, the only Second Class Petty Officer to accomplish this on board U.S.S. Louisiana SSBN 743. My demonstrated technical abilities, job knowledge, and leaderships matched more senior personnel. Flawlessly performed sub-safe critical repairs in hydraulics and high/low pressure air systems, ensuring all documentation, maintenance and retests were completed correctly to ensure the ship’s safe operation at sea. Show less
-
-
Education
-
University of Phoenix
BS, Business Management -
Military Training
Various, Mechanics and Administration
Community
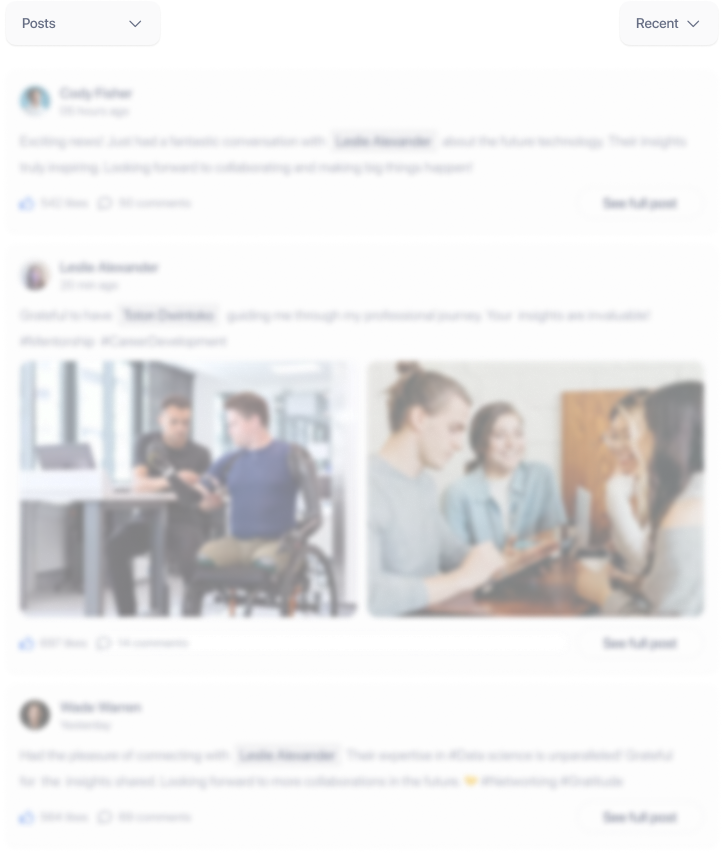