Mumtaj Ali
Planning Engineer at H. K. Al-Sadiq Sons Contracting Co. Ltd.- Claim this Profile
Click to upgrade to our gold package
for the full feature experience.
Topline Score
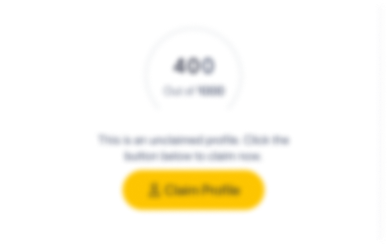
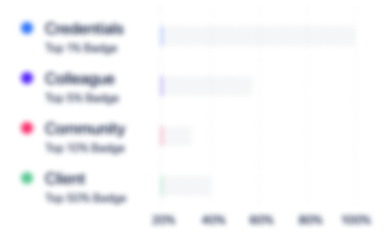
Bio


Experience
-
H. K. Al-Sadiq Sons Contracting Co. Ltd.
-
Saudi Arabia
-
Construction
-
100 - 200 Employee
-
Planning Engineer
-
Jan 2019 - Present
Manage the shutdown planning input to the corporate, long term and associated budget plans.Develop detailed shutdown schedules in Primavera, identifying critical path activities, overall shutdown durations and resource requirements. Develop detailed shutdown manpower histograms within POB constraints, and provide advice on the most efficient use of resources in implementing the shutdown activities. Monitor and control planning activities through all phases of the shutdown lifecycle; long term planning; strategy; preparation; pre-work; work; post work and feedback. Produce and issue progress S curves to allow visual representation of plan and progress Prepare / present planning data for ad-hoc and regular meetings with Contractor's Management. Preparation of detail work preparation of all the disciplines, preparation of plan cards for the purpose of scheduling. Communication protocol (review) between departments for the checking of work packages. Preparation of Order and track materials, tools and consumables, estimating hours and budgeting and monitoring bids. Adding documents as attachment and compiling as digital file, preparing management status report of the complete project (KPIs). Issue work packages to contractors (per discipline) and track the status of it. Coordinate with Quality control and commissioning to prepare their reports. Monitoring progress during execution by means of digital wallpapers, Handover package per system, process area/unit etc. Ensure the SAP maintenance management system is maintained for all planned shutdown activities to reflect the schedule and resource requirements within the overall integrated shutdown plan. Ensure schedule and resource actuals and lessons learnt for PM activities are captured in SAP maintenance plans. Show less
-
-
Maintenance Planner / Scheduler
-
Jan 2016 - Dec 2018
Prepare Clause 14/8.3 Contract Master Programme based on Contract Requirements. Prepareconstruction/Coordination Programmes based on project requirements. Identify, monitor & manage, in an organized manner, scope changes, variations and Extension of Time (EOT) Claims using “Impacted as Planned” and “TIA” techniques. Prepare the following deliverables with the prepared programmes: 1. Planning Method Statement/Narrative Report 2. Shop Drawing Submittal & Approval Schedule 3. Material Submittal & Approval Schedule 4. Material Procurement Schedule 5. Resource & Equipment Histogram 6. Cash Flow & Detailed Manpower/Workforce Schedules Coordinate & integrate sub-contractors with the project programmes and ensure compliance with the programme requirements. Issue the following reports on weekly basis to the project team: 1. Two/ 4 weeks look ahead schedules. 2. Project Productivity reports and updated KPI‟s 3. Delay Notification with proper substantiations 4. Daily welding progress report, Material Tracking sheet, Updated ID list 5. Technical Query updated log & Transmittal tracking log 6. Critical Path activities. Prepare delays/disruption/Time claims using delay analysis techniques as applicable- Impacted As-Planned, Time Impact Analysis, As-Planned VS As-Built & Collapsed As-Built. Identify the best series of events in the correct order for the project to finish on time and on budgeted in coordination with the project manager. Conduct site visits to verify physical progress, identify any potential /critical issues. Works with the cost and estimation, assist and liaise with project team to rectify potential cost overruns/schedule delays. Perform statistical analysis to identify schedule and cost variances of project status against baseline using EVMs and calculate schedule performance index (SPI) Show less
-
-
-
IRC ENGINEERING SERVICES (I) PVT. LTD.
-
India
-
Oil and Gas
-
1 - 100 Employee
-
Site Planner
-
Aug 2012 - Dec 2015
Level III CPM Schedule reflecting Critical Path– Reflecting the activities with other subcontractor and to be link to activities related to Packages or project and other tie-in activities to existing plant or battery limit. Primavera Critical Path Level I Schedule – Reflecting all activities on Critical Path. Primavera Schedule Activities assigned to Manager responsible for work task completion- Schedule Ownership/ Assignment/ Accountability. Primavera Milestone Summary Schedule- Reflecting Key Milestone, Equipment arrival date on site, Engineering Deliverables for Start & Finish Dates. Physical Progress Curves – Group by Area Discipline Indirect Staff Matrix- Reflecting craft type, Staff head count, and indirect service provided –over the contract period on a monthly basis. Direct Manpower Distribution - By Work Category Construction Equipment Plan- Detailing type of equipment, quantity of equipment, Equipment mobilization and de- mobilization dates Detailed Subcontracting Plan – A narrative and Level III CPM Primavera Schedule of Subcontracting Phase to Mobilization- By Subcontract. Detailed Organizational Chart – Reflecting Individual key Personnel Group by Area or by Section Daily Report, Weekly Progress Measurement System & Report and Monthly Report. Schedule Basis and Assumptions- a narrative detailing schedule basis and assumptions- related activities, completion activities, pre-commissioning and Turnover. To ensure that the Detailed schedules developed by Subcontractors, as per their contractual obligations, and consistent when we rolled up from level IV to I. Integrate the above Primavera plan and develop Progress Monitoring System to generate the graphics and figures to control and monitor the project. Show less
-
-
Education
-
The institute of engineers (AMIE)
B- tech, Mechanical Engineering -
CT Group of Institution, Jalandhar
Diploma, Mechanical Engineering
Community
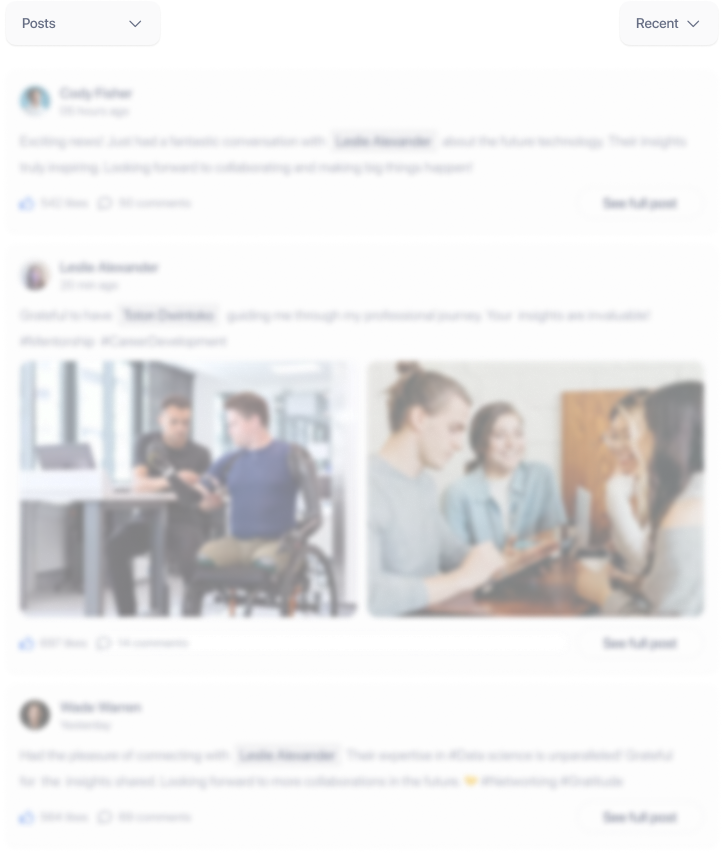