Stephen Hill
Mechanical Design Engineer at Guild Associates, Inc- Claim this Profile
Click to upgrade to our gold package
for the full feature experience.
Topline Score
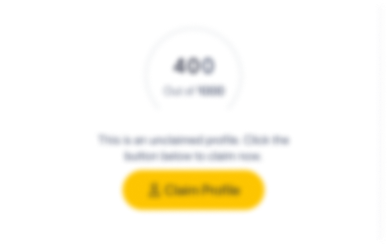
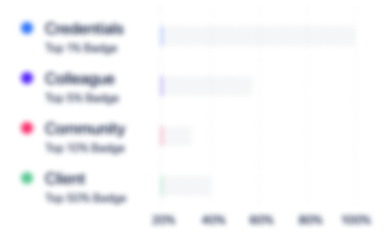
Bio

Brian DeBoer
Steve is a team player in the many tasks he accomplished. Examples of the assigned tasks were designing components in SolidWorks, researching current component part numbers to update a 25 year old hydraulic circuits, or working directly with assembly technicians on fitment of components or design improvements.

Brian DeBoer
Steve is a team player in the many tasks he accomplished. Examples of the assigned tasks were designing components in SolidWorks, researching current component part numbers to update a 25 year old hydraulic circuits, or working directly with assembly technicians on fitment of components or design improvements.

Brian DeBoer
Steve is a team player in the many tasks he accomplished. Examples of the assigned tasks were designing components in SolidWorks, researching current component part numbers to update a 25 year old hydraulic circuits, or working directly with assembly technicians on fitment of components or design improvements.

Brian DeBoer
Steve is a team player in the many tasks he accomplished. Examples of the assigned tasks were designing components in SolidWorks, researching current component part numbers to update a 25 year old hydraulic circuits, or working directly with assembly technicians on fitment of components or design improvements.

Experience
-
Guild Associates, Inc
-
United States
-
Defense & Space
-
1 - 100 Employee
-
Mechanical Design Engineer
-
Mar 2021 - Present
-
-
-
Eden Cryogenics
-
Plain City, Ohio, United States
-
Project Engineer
-
Feb 2018 - Mar 2021
• Developed proposal and bill of materials for project proposal • Monitored part purchasing and delivery to maintain production schedule. • Created project timelines using Microsoft Project during quoting stage and updated during production • Produced manufacturing drawings using AutoCAD and Inventor from Eden design or customer’s drawings • Directed communication with customer during manufacturing • Developed proposal and bill of materials for project proposal • Monitored part purchasing and delivery to maintain production schedule. • Created project timelines using Microsoft Project during quoting stage and updated during production • Produced manufacturing drawings using AutoCAD and Inventor from Eden design or customer’s drawings • Directed communication with customer during manufacturing
-
-
-
YIZUMI HPM NORTH AMERICA
-
United States
-
Mechanical Engineer
-
Apr 2013 - Sep 2017
1. Use Solidworks and AutoCAD to develop and update for Die Cast and Injection Molding Machines 2. Help implement part inventory system to clarify part purchasing and quoting 3. Redesigned shot and intensifier piston with new seals that shorten down time and improved longevity. 4. Purchased parts ahead and during Die Cast Machine assembly to delivery machine on a shorten time frame build. 5. Project Manager for 4500 ton Die Cast Machine, including developing shot end and calculating hydraulic pressure and flow to match correct accumulator bottles and hydraulic valves. 6. Inspected drawings from our parent company in China to insure machine was built to customer specs state side 7. Design rotator shot encoder to indicate shot position used to monitor shot injection speed to ensure optimum Die Cast part. 8. Worked with machine shops on pricing and lead time on parts that needed to be outsourced. 9. Worked on assembly of die cast machine and completing check list for the machine before shipping out to customer 10. Worked with inhouse machine shop in parts design to insure efficient design and functionality 11. Organized shipment of 100,000 lbs machines Show less
-
-
-
Sakamura USA, Inc.
-
United States
-
Machinery Manufacturing
-
1 - 100 Employee
-
Sales Engineer
-
Mar 2010 - Mar 2013
1. Troubleshooted machine on the phone with customers to narrow down a solution and set up service trips for the customer when needed 2. Worked on machines in field from routine maintenance to full machine rebuilds 3. Prepared daily reports on machine progress in the field to document status on repair for Ohio office and headquarters in Japan. 4. Prepared and maintained company project schedule 5. Had rapport with customers to help fix issue with machines before issues became too large and required costly shut down Show less
-
-
-
Toyoda Gosei Americas
-
United States
-
Motor Vehicle Manufacturing
-
700 & Above Employee
-
Mold Engineer
-
Jan 2008 - Jun 2009
1. Kicked off Injection molds and followed mold progress during time line of build with mold shop 2. Completed specific mold changes from plant with mold shops 3. Attended mold tryouts from first shot to final shot for production 4. Help manage the new Toyota Sienna program while running other programs 5. Used Catia V5 to check for part feasibility. 1. Kicked off Injection molds and followed mold progress during time line of build with mold shop 2. Completed specific mold changes from plant with mold shops 3. Attended mold tryouts from first shot to final shot for production 4. Help manage the new Toyota Sienna program while running other programs 5. Used Catia V5 to check for part feasibility.
-
-
Education
-
The University of Toledo
Bachelor of Engineering - BE, Mechanical Engineering Related Technologies/Technicians
Community
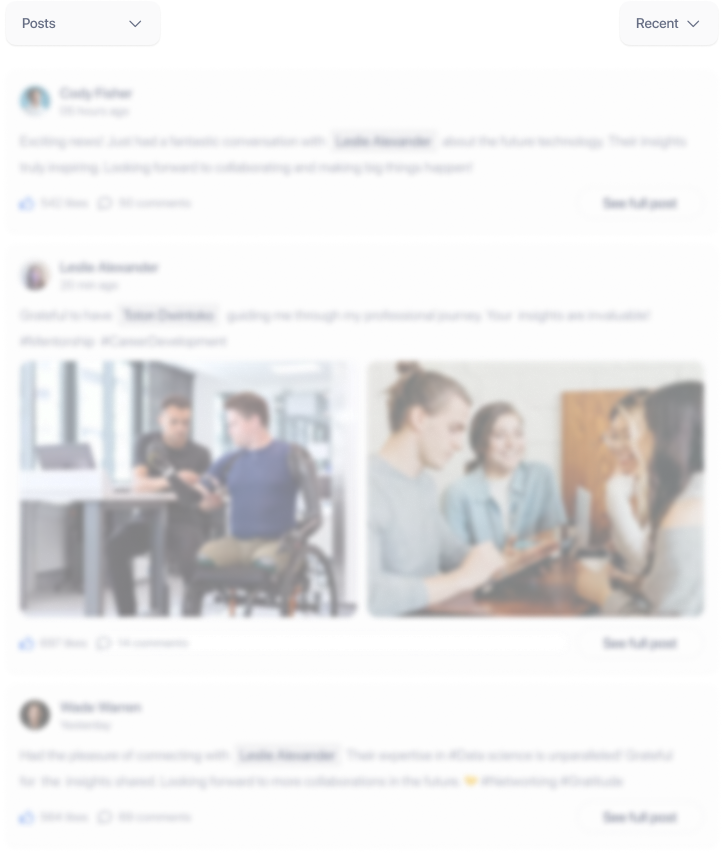