Christopher Horning
Quality Manager at The AZEK Company- Claim this Profile
Click to upgrade to our gold package
for the full feature experience.
-
English Full professional proficiency
-
Spanish Limited working proficiency
Topline Score
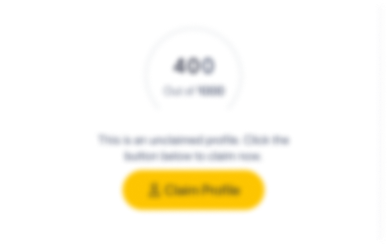
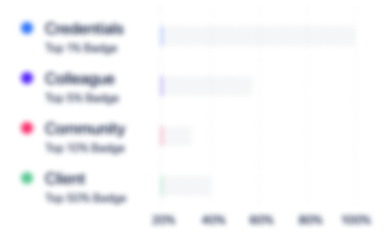
Bio

Massimo Sabattini
I found Chris to be very trustworthy, focused in his job and a very reliable contact. I highly recommend him for his work in quality assurance.

Mark Hamilton
Chris is very detailed oriented and Quality is his passion. He believes in doing things right the first time and is always available to assist and provide train when needed. He would be an asset to any team.

Massimo Sabattini
I found Chris to be very trustworthy, focused in his job and a very reliable contact. I highly recommend him for his work in quality assurance.

Mark Hamilton
Chris is very detailed oriented and Quality is his passion. He believes in doing things right the first time and is always available to assist and provide train when needed. He would be an asset to any team.

Massimo Sabattini
I found Chris to be very trustworthy, focused in his job and a very reliable contact. I highly recommend him for his work in quality assurance.

Mark Hamilton
Chris is very detailed oriented and Quality is his passion. He believes in doing things right the first time and is always available to assist and provide train when needed. He would be an asset to any team.

Massimo Sabattini
I found Chris to be very trustworthy, focused in his job and a very reliable contact. I highly recommend him for his work in quality assurance.

Mark Hamilton
Chris is very detailed oriented and Quality is his passion. He believes in doing things right the first time and is always available to assist and provide train when needed. He would be an asset to any team.

Credentials
-
ISO 9001 Lead Auditor
Cavendish Scott, Inc.Jun, 2016- Nov, 2024 -
Certified Quality Auditor
ASQDec, 2012- Nov, 2024 -
Six Sigma Green Belt
ASQJun, 2011- Nov, 2024 -
Diploma in Brewing
Institute of Brewing and Distilling (U.K.)Jun, 2009- Nov, 2024 -
Certified Quality Engineer
ASQDec, 2008- Nov, 2024 -
Certified Manager of Quality/Organizational Excellence (CMQ/OE)
ASQ - World HeadquartersMay, 2019- Nov, 2024 -
Advanced HACCP
Ecolab
Experience
-
The AZEK Company
-
United States
-
Wholesale Building Materials
-
300 - 400 Employee
-
Quality Manager
-
Jan 2022 - Present
Building a sustainable Quality Culture from the ground up at a new startup facility utilizing process-based continuous improvement. Taking the best of decades of experience within the AZEK TimberTech family of brands and creating a world-class manufacturing environment with a collaborative team of industry experts. Building a sustainable Quality Culture from the ground up at a new startup facility utilizing process-based continuous improvement. Taking the best of decades of experience within the AZEK TimberTech family of brands and creating a world-class manufacturing environment with a collaborative team of industry experts.
-
-
-
Caroba Plastics, Inc.
-
United States
-
Medical Equipment Manufacturing
-
1 - 100 Employee
-
Quality Manager
-
Dec 2020 - Oct 2021
Leading a team of Quality professionals to monitor and improve an ISO 9001:2015 injection molding facility. QMS includes new part onboarding, 8D CAPA program, and internal metrology department serving Quality and Tool Maintenance processes. Medical, consumer goods, and ATF standards built in to daily processes. Leading a team of Quality professionals to monitor and improve an ISO 9001:2015 injection molding facility. QMS includes new part onboarding, 8D CAPA program, and internal metrology department serving Quality and Tool Maintenance processes. Medical, consumer goods, and ATF standards built in to daily processes.
-
-
-
Tenere Inc.
-
United States
-
Manufacturing
-
100 - 200 Employee
-
Quality and Safety Manager
-
Sep 2017 - Dec 2020
Ensuring the consistent quality of production by developing and enforcing quality systems and programs, validating processes, and providing information, data and analysis. Providing environmental, health and safety facilitation to assure regulatory compliance, achieve continuous performance improvement and integrate EHS performance objectives into standard work processes. Developing strategies to achieve these goals in alignment with site business goals and values. Design, develop and support the efficiency and continuous improvement of new and existing production processes, and assesses the effectiveness of the quality processes of the organization. Show less
-
-
-
Reata Engineering & Machine Works, Inc.
-
United States
-
Industrial Machinery Manufacturing
-
1 - 100 Employee
-
Quality Manager
-
Jan 2017 - Aug 2017
Leading the Quality Department of an ISO 9001 and AS9100 certified manufacturing facility specializing in custom machining of metal and plastic parts through management of the overall Quality System, which governs plant procedures on both a day to day and strategic long-term basis. Planning, coordination, and direction of a Quality Control program designed to ensure continuous production of products consistent with established standards by performing the following duties personally and/or through subordinate supervisors and technicians: • Management of Quality System, documentation and direction • Maintenance of regulatory compliance certifications • Administration of the Corrective Action system • First Article Inspection • Reporting of Quality System results • Non-Conformance deviation issuance • Conversion to AS9100(d) • Continuous Improvement projects and culture • Customer complaint resolution • Lean Manufacturing implementation projects Show less
-
-
-
Intertech Plastics, LLC
-
United States
-
Plastics Manufacturing
-
1 - 100 Employee
-
Quality Manager
-
Oct 2015 - Jan 2017
Leading the Quality Department of an ISO 9001 certified manufacturing facility specializing in plastic injection molded consumer goods through management of the overall Quality System, which governs plant procedures on both a day to day and strategic long-term basis. Planning, coordination, and direction of a Quality Control program designed to ensure continuous production of products consistent with established standards by performing the following duties personally and/or through subordinate supervisors and technicians: • Management of Quality System documentation • Maintenance of regulatory compliance • Administration of the Corrective Action system • Customer complaint resolution • First Article Inspection • Reporting of Quality System results • Non-Conformance deviation issuance • Customer Credit approvals • Continuous Improvement projects • Lean Manufacturing implementation projects Show less
-
-
-
-
Quality Manager
-
Feb 2015 - Oct 2015
Process Improvement, 8D/DMAIC Problem Solving, Data Analysis• Project Management for process improvement opportunities in Operations and Quality• RCCA analysis and customer response• Daily direction of the Quality Department staff (30+ IPQC auditors, Laboratory, IQC)• Quality System facilitator and Document Control System custodian• Lean Manufacturing and 5S implementation support
-
-
Quality Engineer
-
Mar 2014 - Feb 2015
Process Improvement, Quality Assurance, Lean Manufacturing, Quality System Development, Root Cause Analysis, Customer Service
-
-
-
MillerCoors
-
United States
-
Food and Beverage Services
-
700 & Above Employee
-
Trade Quality Specialist
-
May 2012 - Nov 2013
TRADE QUALITY SPECIALIST, Golden Brewery Customer Service & SupplyAddressed and resolved distributor complaints involving Golden Brewery product. Managed action plans for problem solving of distribution quality opportunities. Provided service and support for nationwide supply chain. • Tracked and identified root cause for packaging, distribution, and logistics errors.• Supported Short Interval control implementation in the Golden Brewery Warehouse.• Performed Distributor Quality audits in the Central and Pacific regions.• Partnered with distributors to improve and shape their own internal quality procedures to better meet MillerCoors Standards.• Raised average Distributor Quality Audit score in the Central Region by 5.5% 2012 vs. 2013.• Developed and performed GMP and Quality audits in the Golden Brewery Warehouse and Golden Distribution Center. • Authored several Job Aids and One Point Lessons in support of Golden Brewery Warehouse operations.• Reduced Distributor Complaints by 41% Q1 vs. Q4 2013 Show less
-
-
Quality Assurance in Packaging
-
Oct 2006 - May 2012
INSTRUMENTATION SPECIALIST, Golden Brewery PackagingIdentified and Troubleshot Packaging Quality finished product holds. Managed Quality instrumentation inventory and calibration. Provided operations support for product quality checks.• Developed and maintained quality instrumentation database.• Serviced and repaired multiple product quality testing instrumentation systems.• Created operations instrumentation training tracking system and trained over 80 employees on quality instrumentation across three shifts.• Authored dozens of Work Instructions, Job Aids, and One Point Lessons in support of new and established instrumentation and operations.• Monitored and qualified new products and packages across all three shifts.• Tested, dispositioned, and identified root cause of finished product holds in the Golden Brewery.SUPPLIER QUALITY SPECIALIST, Golden Brewery PackagingIdentified and Troubleshot Packaging Quality finished product holds. Tracked and managed materials quality for Packaging suppliers. Implemented supplier management system in the Golden Brewery.• Cultivated partnership approach to increase performance with key suppliers.• Tracked and verified supplier quality issues across all three shifts.• Managed root-cause corrective action requests made to suppliers.• Authored Supplier Quality Management Procedure and several other SOPs for the Golden Brewery.• Led the team in developing qualification system for new products and packages.• Tested, dispositioned, and identified root cause of finished product holds in the Golden Brewery.• Reduced supplier-related downtime by 21% 2008 vs. 2009.QUALITY TECHNOLOGIST, Golden Brewery PackagingIdentified and Troubleshot Packaging Quality finished product holds. • Performed quality checks for packaged product attributes.• Provided operations troubleshooting support across all three shifts.• Tested, dispositioned, and identified root cause of finished product holds in the Golden Brewery. Show less
-
-
Education
-
Metropolitan State College of Denver
Bachelor of Science, Biology/Chemistry -
Regis Jesuit High School
Diploma
Community
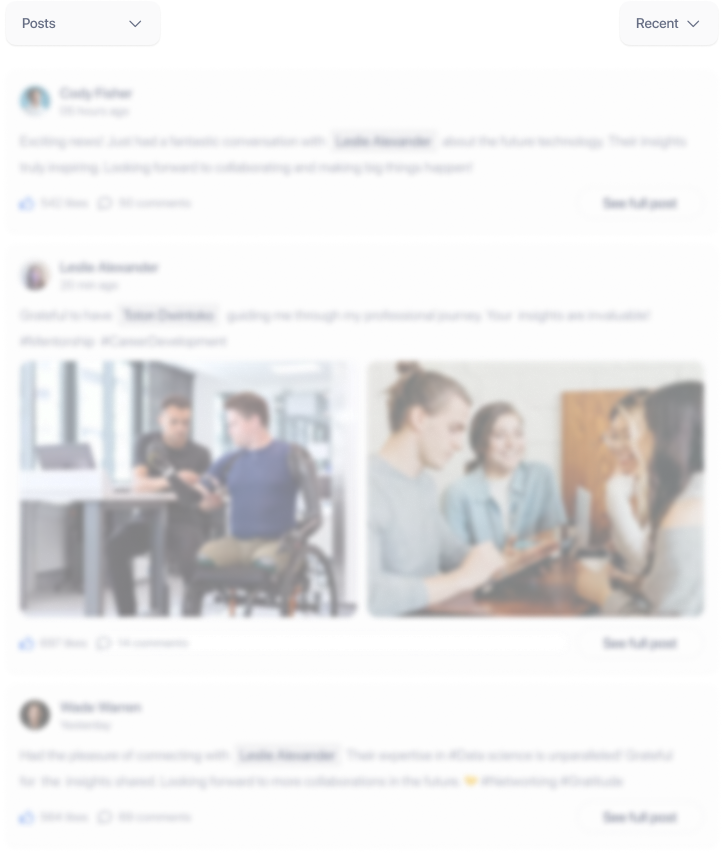