Roselle Bundalian
Quality Specialist II at Nanōmix- Claim this Profile
Click to upgrade to our gold package
for the full feature experience.
-
English -
Topline Score
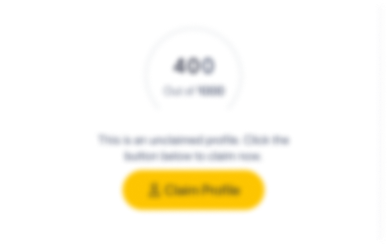
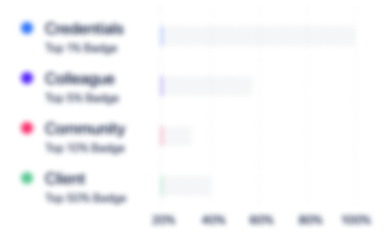
Bio


Experience
-
Nanōmix
-
United States
-
Medical Equipment Manufacturing
-
1 - 100 Employee
-
Quality Specialist II
-
Aug 2022 - Present
Batch record review to ensure GDP compliance and train as necessary. Responsible for monitoring, inspecting, and proposing measures to correct or improve a company's final products and processes to meet established Quality Standards. Prepare and implement quality assurance policies and procedures and perform routine inspections and Quality tests. Inspect and approves incoming materials by confirming specifications, conducting visual and measurement tests, rejecting and returning unacceptable materials. . Approves finished products by confirming specifications, conducting visual and measurement tests. Documents inspection results by completing reports and logs, summarizes re-work, waste, and inputs data into quality database. Keeps measurement equipment operating by following operating instructions, calibration requirements, and calling for repairs. Maintain equipment calibration records and log. Collaborated in writing and investigating NCMR’s. Manage daily purchasing activities, preparing requisitions, purchase orders and maintaining records. Coordinated with inventory control to determine and manage inventory needs. Show less
-
-
-
ExThera Medical
-
United States
-
Medical Device
-
1 - 100 Employee
-
Operations Specialist
-
Oct 2019 - Aug 2022
•Batch record review to ensure GDP compliance and train as necessary. •Coordinate shipping and receiving to and from all CMs, distributors and customers. •Maintain a safe, healthy work environment with full compliance to the company’s policies and procedures. •Establish a culture that is proactive, responsible and accountable for compliance and working knowledge of OSHA. •Help with manufacturing if necessary. •Work with Quality and Operations to ensure compliance and adherence to ISO13485. •Interact with vendors to ensure that raw materials, subassemblies and product are delivered on time,within cost, and meet the company’s quality standards. •Establish procedures for monitoring raw materials. •Ensure that raw materials are promptly ordered to maintain an adequate inventory. •Help analyze cost for raw materials. •Component Control – Receiving and incoming inspection to include verification of items/quality to PO and packing slip, verification of approved vendor, logging received materials. •Promote good housekeeping standards. •Perform other duties assigned to meet business needs. •Responsible for performing work activities in accordance with the procedures and requirements of ExThera Medical’s Quality Management System and Quality Policy. Show less
-
-
-
MiraDry/Sientra
-
Santa Clara, California
-
Service Technician
-
Oct 2017 - Oct 2019
•Responsible for repair and service of miraDry products. •Failure analysis of returned miraDry products. •Troubleshoot and debug failed components. •Repair assemblies and subassemblies. •Perform non destructive testing. •Provide feedback to production and engineering for product improvement. •Clean and inspect incoming RMA’s. •Complete and maintain service records, document repair findings and quality overview. •Follow written procedures and submit change orders for quality improvement and efficiency. •Perform HW and SW upgrades. •Assist production when needed. Show less
-
-
-
Thoratec, now a part of St. Jude Medical
-
Medical Equipment Manufacturing
-
100 - 200 Employee
-
Lead Electromechanical Technician
-
Sep 2015 - Nov 2016
● Helped position Thoratec for a successful exit with St. Jude Medical. ● Launched and commercialized the world’s first Percutaneous Heart Pump (PHP catheter), a PMA device. ● Read and gave valuable feedback for DFM (Design for Manufacturing) objectives to improve efficiency, cycle times, order / method of assembly and process flow. ● Helped Engineering and management understand yields and defect fallout. Assisted on all yield improvements objectives and improved yields from 45th percentile to the upper 85th percentile in 4 months. ● Repaired and reworked assemblies to meet operational specifications, tolerance and performance. ● Interviewed and trained all new hires with a rigorous training plan and tested aptitude prior to sign-off. ● Supported R&D with component and assembly tests and incorporated upgrades to existing product line. ● Helped Manufacturing Engineers understand where fixtures and jigs were needed for reliability and repeatability with consideration in reduction of overall cycle time. ● Helped improve all documentation including Batch Records, Quality Inspection Protocols, Manufacturing Process Instructions among other SOPs and documents. ● Checked all written documents to ensure there was adherence to GDP in a timely manner prior to sterilization. Show less
-
-
-
CR Bard
-
United States
-
Medical Equipment Manufacturing
-
700 & Above Employee
-
Manufacturing Team Lead
-
Aug 2013 - Aug 2015
● Helped with staffing objectives, interviewing for 2nd and 3rd shift operations and scaled production post acquisition to approximately 2.5X. ● Received recognition for punctuality and consistently striving to improve yields and efficiencies. ● R&D team-lead for development of new processes for all pipeline products. Gave valuable feedback on multiple DFM objectives. Often assisted with inventory control objectives when needed. ● Interpreted and followed engineering drawings, work instructions and technical specifications as necessary for manufacturing technology transfer to Glen Falls, NY. ● Improved product quality and process yields by helping understand defect cause and effect. Helped implement various processes to improve yields. ● Helped launch a new Class 8 cleanroom and assisted in creating a cleaning schedule including Hepa filtration and janitorial service schedules. ● Often worked on multiple projects in parallel and utilized and maintained all types of process tools and equipment safely and efficiently. ● Assisted Engineering in equipment calibration scheduling and tracking. Kept training records up to date for process equipment, Work Instructions and SOPs regarding company regulations. ● Complete hands-on second shift position with no Engineering or management supervision available. Assembled new product prototypes for engineering evaluation on a regular basis. Show less
-
-
-
Loma Vista Medical, Inc.
-
United States
-
Manufacturing Team Lead
-
Aug 2011 - Jul 2013
● Helped position Loma Vista Medical for a successful exit with Bard Peripheral Vascular in Q3, 2013. ● Hired as the primary assembler and “wore multiple hats” until Series B funding. Implemented and helped design the process flow, DFM initiatives and helped with cycle time reduction and yield improvements. ● Launched LVM’s True Valvuloplasty catheter and helped drive the idea from conception to commercialization. ● Implemented Lean Manufacturing methodologies in the clean room for proper placement of tools, equipment and manufacturing aids. ● Trained all new hires on manufacturing processes, Quality standards and proper use of equipment. ● Called and placed POs for all adhesives, disposables and responsible for inventory control of all manufacturing components. ● Performed incoming receiving inspection for all raw materials and utilized Excel for company’s internal ERP system. Implement 5S in the entire facility including the Engineering Lab, CER, offices and conference rooms. ● Utilized my written and verbal skills to address concerns and communicate with engineering and management on safety, efficacy and other objectives. ● Ran various unsupervised experiments and tests to help engineering with product specification activities. Follow and enforced all cGMP and GDP as well as other ISO 13485 regulations. ● Lead and coached team members and ensured that they were following standard processes. Consistently pushed team to perform at a higher level while sustaining net yields in the mid-90th percentile. Sustained 90th percentile net yields for 1.5 years in a row and until acquisition. ● Worked with the Production Supervisor, Quality Control Personnel and Maintenance Engineering teams to assemble at the lowest cost while providing highest quality product possible. Show less
-
-
-
Abbott
-
United States
-
Hospitals and Health Care
-
700 & Above Employee
-
Senior Manufacturing Operator
-
Apr 2001 - Jul 2011
● Employed for eleven years with Abbott Vascular with an outstanding attendance and punctuality record. ● Worked on a cost reduction projects to save on component cost and simultaneously increase margins. ● Assumed responsibility as a Back-Up Lead for multiple production lines wherein duties included certification of personnel Line Clearance and verification of Lot History Records. ● Lead the development and creation of an eLHR or “Viewpoint” a paperless integration program for all manufacturing documents including Manufacturing Process Instructions, Travelers, and Quality Inspection Procedures amongst others. ● Worked with Quality Assurance to ensure product complied with local, divisional and corporate procedures as well as conformed to Quality systems regulations and documented work accurately. ● Worked in a sterile environment for Class II disposable devices. Responsible for the safe disposal of all hazardous waste. ● Assembled, inspected, and tested products according to various protocols and verbal instructions. ● Certified personnel for the Instron tensile testing machine and Class I laser testing of products for tension and integrity according to protocol. Show less
-
-
Education
-
Kaplan University
Real Estate -
Westmoore High School
General Studies
Community
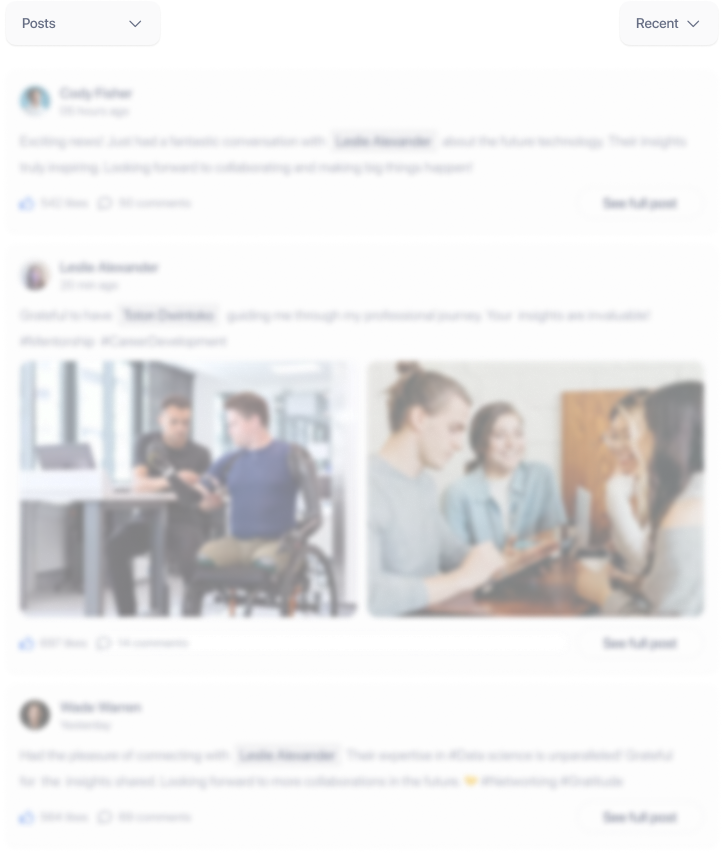