Chris Egan
Principal Engineer at Spectra-Physics- Claim this Profile
Click to upgrade to our gold package
for the full feature experience.
Topline Score
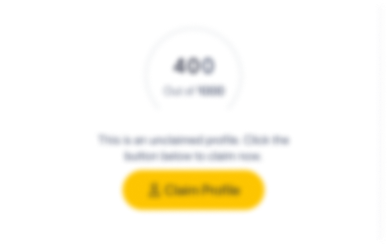
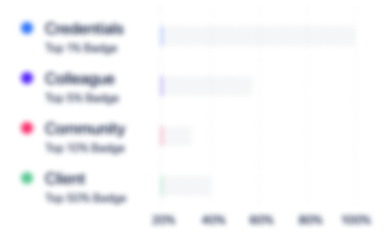
Bio

Frederick Cole
Chris is a skilled professional and recognized by his peers as a leader. He takes direction well and completes his projects on time. He was value asset to the company. I would recommend Chris for any quality opportunity that allows him to utilize all of his skills and knowledge.

Frederick Cole
Chris is a skilled professional and recognized by his peers as a leader. He takes direction well and completes his projects on time. He was value asset to the company. I would recommend Chris for any quality opportunity that allows him to utilize all of his skills and knowledge.

Frederick Cole
Chris is a skilled professional and recognized by his peers as a leader. He takes direction well and completes his projects on time. He was value asset to the company. I would recommend Chris for any quality opportunity that allows him to utilize all of his skills and knowledge.

Frederick Cole
Chris is a skilled professional and recognized by his peers as a leader. He takes direction well and completes his projects on time. He was value asset to the company. I would recommend Chris for any quality opportunity that allows him to utilize all of his skills and knowledge.

Credentials
-
Certified IPC-A-610 Trainer
IPC-Association Connecting Electronics IndustriesJun, 2014- Nov, 2024 -
ISO13485, FDA/21CFR-Part 820, Quality System Regulation / Medical Devices RABQSA Lead Auditor
BSI, British Standard InstitutionApr, 2012- Nov, 2024 -
Lean Six Sigma Green Belt
ASQJan, 2005- Nov, 2024
Experience
-
Spectra-Physics
-
United States
-
Appliances, Electrical, and Electronics Manufacturing
-
100 - 200 Employee
-
Principal Engineer
-
Dec 2015 - Present
-
-
-
Spectranetics
-
United States
-
Medical Device
-
100 - 200 Employee
-
Principal Quality Engineer
-
Oct 2015 - Dec 2015
-
-
-
Ultra Clean Technology
-
United States
-
Semiconductor Manufacturing
-
700 & Above Employee
-
Senior Quality Engineer (Medical)
-
Mar 2012 - Jun 2015
• Manage medical customers as the CQE (Customer Quality Engineer) Ensuring high level of compliance to Customer specification; FDA QSR/cGMPs and ISO 13485 in all assigned areas are met. Resolve all customer complaints, driving timely disposition and closure. • Project Manager / Team Leader for the implementation of ISO-13485:2003 QMS for corporate headquarters, registration certificate granted. NQA, Jan 14, 2014. • Trained internal audit team to ISO-13485 and 21CFR-Part 820 regulations. Established internal audit plan/schedule and conducted audits internally, medical suppliers, and subcontractors. • Lead activities related to customer product integration and other areas such as Risk Management, Process Validation, Test Validation, Part Qualification, IQ/OQ/PQ protocols and reports. • Review build to print items and recommend critical inspection requirements versus customer documentation. Determine critical characteristics and establish IQC inspection points based on drawing specification and assembly OMS. • Create inspection plans identifying, inspection tools, inspection methodology and AQL sample plan, trained IQC personal on GD&T principles and measuring techniques. Guide IQC on resolving daily incoming, WIP, and final inspection issues. • Developed and manage all medical IQC functions, including Gage R&R, Cp/Cpk analysis, inspection record maintenance, supplier FAIR and third party inspection lab activities. • Established DHR requirements and developed process. Managed DHR team and performed final DHR package review prior to product shipment. • Drive internal departments (Operations, NPI. Supplier Management to resolve customer complaints, in-house and supplier quality problems using established problem-solving methodologies (8D, Root Cause Analysis, Mistake-proofing, etc.).
-
-
-
Coherent Laser
-
United States
-
Appliances, Electrical, and Electronics Manufacturing
-
700 & Above Employee
-
Sr Staff Quality Engineer
-
Sep 2008 - Nov 2011
• Responsible for QE/SQE support of four BU, Semiconductor, DPSS, HOPS, DDF of laser components such as; machined components, ceramic sub mounts, coatings, PCB/PCBA and domestic/overseas contract manufacturing. • Development of quality plans internal and external. Implement and drive established methods for new and existing products for mechanical inspection, final product acceptance, HALT, HASS and PCBA inspection and test requirements • Managed CAPA database, investigated and resolved problems with manufacturing of raw material, components and product assembly’s • Analyzed field failure reports of customer return products, identified failure modes, root cause and presented results along with corrective actions to management in detailed failure analysis reports. • Created technologically informative presentations, documents, manuals and procedures, and present these to relevant groups within Coherent. • Represented the quality department in a variety of quality improvement areas such as; (CCB) Change Control Board and (MRB) Material Review Board • Investigated NCR’s, analyzed data and reported on a monthly basis all site quality related statistics and metrics. • Provide coordination and technical support to management and other personnel; o Performed internal and external quality audits of QMS to ISO 9001-2008, ISO 13485 as required. o Implemented Lean 6 Sigma techniques and projects within each business unit for continual improve
-
-
-
Santur Corporation
-
United States
-
Telecommunications
-
1 - 100 Employee
-
Senior Supplier Quality Engineer
-
Apr 2007 - Aug 2008
• Responsibilities as the SQE included; supplier site audits, overseas product transfer, qualification, development, performance quality of optoelectronic / laser components such as; machined components, packages, sub mounts, coatings, PCB/PCBA and contract manufacturing. • Provide technical direction and assistance to design engineering, procurement, and manufacturing, receiving inspection and supplier activities. • Consult with engineering personnel to establish material purchasing specification, inspection plans, standard operation procedures (SOP) and performance criteria for manufacturing and testing. • Monitor and trend overseas production activities, identify areas of concern and utilize a scientific approach to implement corrective actions to achieve company yield and shipment requirements, as well as cost reduction goals. • Review production processes with Engineering to resolve manufacturing efficiency and DFM issues with Engineering • Conduct /participate in Material Review Board (MRB), Change Control Board (CCB) and Corrective Action Requests (CAR) as required.
-
-
-
Photon Dynamics
-
San Jose, CA
-
Senior Supplier Quality Engineer
-
Feb 2006 - Apr 2007
Responsible for supplier development, performance and quality of custom optics, advanced camera vios, PCB/PCBA, mechanical electrical sub-assemblies, solid-state lasers and contract manufacturing. • Lead and coordinate supplier risk analysis and technical assessment audits and/or participate with Purchasing and Engineering during the supplier identification, development, and qualification process. • Development and execution of process characterization and validation on supplier processes using quality tools such as statistical analysis, process qualification plan (PQP) and reliability testing. • Established first article testing requirements for new materials and components, supplier design reviews for NPI products including coordination of critical measurements, gauging systems, evaluation of process stability and process capability. • Non-conforming material review and disposition, supplier auditing and troubleshooting / root cause analysis, continual improvements to process control, test methods, inspection criteria and related documentation used to evaluate product functionality and quality. • Assisted in the development and review of product specifications and test requirements including the development of critical characteristics and tolerances for manufacturing, process control inspection and quality acceptance. • independently coordinated and performed product failure analysis activities to determine root cause of failures and determine corrective action recovery plan with production and suppliers.
-
-
-
VIAVI Solutions
-
United States
-
Telecommunications
-
700 & Above Employee
-
Senior Procurement Engineer
-
Sep 2002 - Oct 2005
Responsible for custom display products, glass, custom optics, machined components, nickel / gold plating, hermetically sealed packages, chemical etching and optical coating with a net annual revenue of $50,000,000 • Introduced lean sigma techniques for capacity planning, reduce machine / process cycle and takt time. Improve lead-times and on time delivery consistent with business objectives of 98% • Identified opportunities and implement cost improvement plans at existing suppliers to continuously reduce cost to meet business objectives of 6 % per fiscal quarter. • Developed new supply chains in South East Asia, China. Japan and Europe in effort to reduce overall product cost by 15-20 % to meet the company and customers pricing expectations. • Developed supplier qualification and control plans requiring DMAIC principles, process control, SPC, statistical sampling, traceability and critical to quality (CTQ) requirements for new and existing products. • Performed measurement system analysis studies (Gage R&R) on equipment used throughout various processes to insure product specification can be measured consistently and accurately. • Performed DOE, FMEA and advanced statistical analysis to improve overall process yields, reduce material cost and incoming inspection, result net savings 15%. • Performed onsite supplier quality surveys and process audits in compliance with ISO 9001-2000. Assess potential supplier technology expertise and perform risk analysis to insure TQCRD business objectives are met
-
-
-
Flex
-
United States
-
Appliances, Electrical, and Electronics Manufacturing
-
700 & Above Employee
-
Senior Staff Engineer, Supplier Quality
-
Sep 2000 - Sep 2002
• Responsibilities included QE/SQE disciplines throughout the organization for network and medical device components and finished product. • Assists in the development, approval, and maintenance of incoming material specifications, quality assurance procedures, as well as supplier documents such as inspection and control plans. • Defined process and supplier data collection/reporting requirements within the company enterprise data collection software to insure the accuracy and integrity of data • Collected and analyzed quality information from various quality systems, developed reports and drove root cause analysis as needed for customers and senior management. • Prepared supplier audit schedules and ensured audits are conducted on a scheduled basis to ISO 9001-2000. Prepared audit reports based on audit findings. Worked with suppliers on corrective actions to ensure effective resolution and closure. • Develop and implement quality procedures as needed to document current practices. • Investigated supplier quality problems and resolve product issues through supplier corrective action process. Track ongoing supplier quality performance and work with suppliers on quality issues. • Developed systems/process/product FMEA, failure mode analysis and initiation of preventive action for internal and supplied product.
-
-
-
Promex Industries Inc.
-
United States
-
Medical Equipment Manufacturing
-
1 - 100 Employee
-
Senior Quality Engineer
-
1999 - 2000
Team member in development and implementation of the organization’s Quality System in preparation for ISO certification (Certified in Dec. 1999). • Perform Supplier assessments and Internal Quality system audits in accordance with ISO 9000. • Develop and implement real-time SPC in the following areas, SMT, Die Attachment and Wire Bond; analyze data for trends and state of control. Utilize statistical tools, such as process-capability studies of processes and equipment; analyze results for continuous improvements. • Investigate nonconforming material, components and product for quality problems and root cause, established and managed closed loop corrective action program. • Formulate quality policies and set quality standards to fulfill customer’s needs: develop customer-specific Quality Plans and interfaced with customers to resolve customer complaints and quality-related issues. • Develop and provide continuous education and training in TQM, SPC, ISO, and ESD. • Lead Engineer in the design and implementation of DFT (Demand Flow Technology) concepts to reduce cycle time and reduce inventory.
-
-
-
Polycom
-
United States
-
Telecommunications
-
700 & Above Employee
-
Staff Engineer, Supplier Quality
-
1997 - 1999
Perform supplier surveys in compliance with ISO 9000 for new business partnerships U.S. and Asia suppliers. • Established and managed closed loop corrective action program for U.S. and Asia supplier base. • Developed and implemented extensive quality plan for front end SMT (Surface Mount Technology) and box build requirements for U.S. and Asia sub-contract manufacturing. • Qualified new tooling for plastic, sheet metal and machined parts and established critical for functioned dimensions for in-process control of single and double shot injection mold plastic components. • Manufacturing team member in the development and implementation of manufacturing process instructions utilizing DFT (Demand Flow Technology) concepts for new and existing products • Manufacturing team member in the conception of new product design to product launch with Asia based suppliers. • Monitored day-to-day manufacturing operations of high-speed surface mount assemblies to maintain quality standards and production goals.
-
-
-
West Coast Quartz Corporation
-
1 - 100 Employee
-
Quality Engineer
-
1995 - 1997
Established a total quality system in compliance with ISO 9000. • Interfaced with customer and each departmental manager to continuously improve the quality system. • Prepared manufacturing instructions, flow charts and work orders for process control. • Designed and develop Process Qualification Plan (PQP) for customer certification. • Performed machine/process capability studies analyzing Cp and Cpk results for continuous improvements. Developed and implement real-time (SPC) and (WIP) program and training. • Performed Supplier and internal Quality System audits in accordance with ISO 9000. • Developed customer satisfaction survey to establish departmental and company goals and objectives
-
-
-
Syntex Laboratories
-
Palo Alto,CA
-
Compliance Specialist
-
1990 - 1994
• Ensured operations in production were in accordance with Current Good Manufacturing Procedures (CGMPs) • Monitored and sampled inspected work-in process drug products and finished goods to appropriate (POSs) and sampling plans, audited batch records to guarantee that materials produced were within specifications and (CGMP) guidelines • Generated receiving inspection plans of critical dimensions and set AQL sampling plans set forth by MIL-STD 105 and audit vendor performance using established procedures and programs • Performed internal and vendor audits in accordance with ISO and CGMP standards, • Performed the review/revision process for compliance documentation, specifications, and methods: critical examination for errors redundancies and improvements.
-
-
Education
-
San Jose State University
Industrial Technology
Community
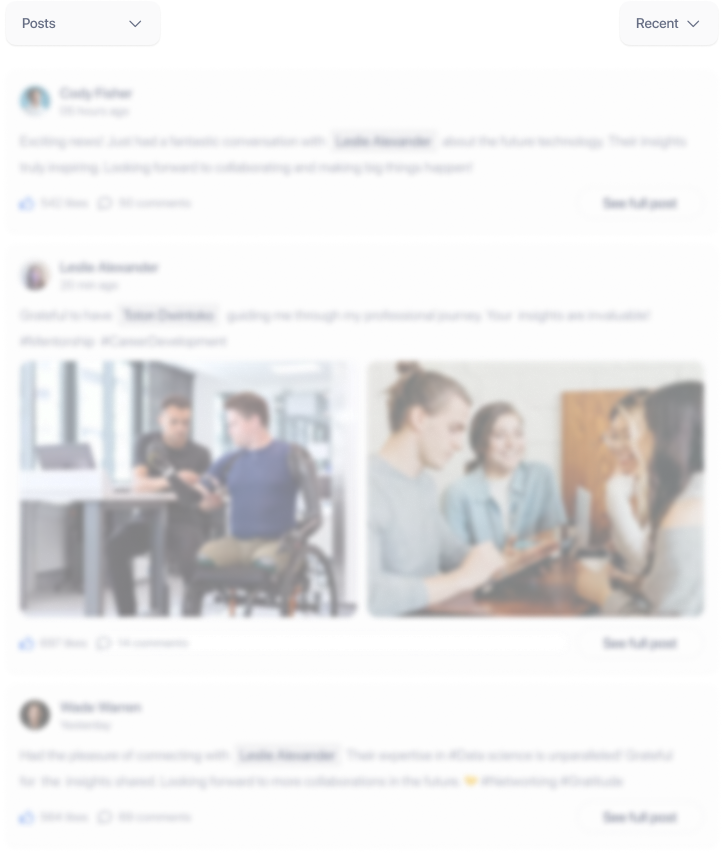