Yosua Kristanto
Process Engineer at Tempo Automation- Claim this Profile
Click to upgrade to our gold package
for the full feature experience.
-
English -
-
Indonesian -
Topline Score
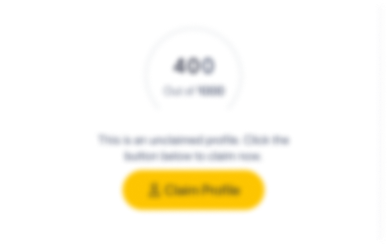
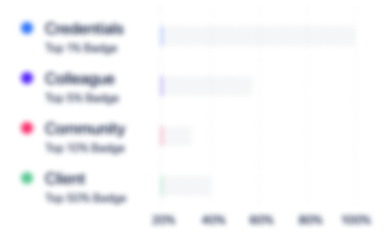
Bio


Experience
-
Tempo Automation
-
United States
-
Appliances, Electrical, and Electronics Manufacturing
-
1 - 100 Employee
-
Process Engineer
-
Mar 2021 - Present
-
-
-
Unigen Corporation
-
United States
-
Semiconductor Manufacturing
-
100 - 200 Employee
-
Process/ Manufacturing Engineer
-
Oct 2019 - Mar 2021
• Responsible in setting up $160K conformal coating (CC) production line that includes potting/staking, masking stations, automated CC machine (PVA), UV oven, QC and rework stations. • Continuously monitored and improved the quality and quantity of CC outputs by consulting with the manufacturer, the expert in the industry, and researching to meet and exceed the customer's expectation. • Reviewed and sourced the necessary equipments, materials, and tools to support production. • Trained the technicians and operators for potting, masking, operating semi-auto dispensing machine, operating and programming the automated CC machine, unmasking, and touching-up. • Supported the production team with various program creations and machine trouble shootings that includes laser marking, SPI, reflow oven, selective wave, press-fit, and routing machine.
-
-
-
Sonic Manufacturing Technologies
-
Appliances, Electrical, and Electronics Manufacturing
-
1 - 100 Employee
-
Process Engineer/ Manufacturing Quality Engineer
-
Aug 2011 - Oct 2019
• Prepared toolings for the NPI projects e.g. stencil and SMT, wave solder, and routing fixtures. • Worked with Sr. Engineers in replacing the routing machine that significantly increases productivity. • Worked with Sr. Design Engineer on universal fixture design that leads to cost reduction and process improvement. • Created various programs e.g. for SPI, CNC routing, and thermal-cycle oven. • Trained SMT programmers and engineering assistant to create SPI and CNC/ thermal-cycle oven programs respectively. • Developed SPI Operation procedure and routing machine Preventive Maintenance procedure. • Designed panel drawing of various assemblies using AutoCAD. • Ordered equipments/ parts e.g. vacuum sealer, spare parts, and labels. • Worked closely with customers to select and create various labels including high-temp, thermal transfer, and paper labels with various barcodes including code 128, data matrix, and QR code. • Worked with customers to develop the NPI documentation of a pilot run for high-volume production that includes special processes such as dispensing potting material, conformal coating application, curing, and hi-pot test. • Conducted a time study of a pilot run. The result is then used to project high-volume production capability. • Collaborated with Sr. Process Engineer to create DFm report that includes proposals to use different land patterns to prevent solder issues and to panelize PCB for more efficient assembly process. • Improved Document Control system by standardizing the MPI template and changing the history filing system from paper-based to electronic-based. • Developed effective work instruction that includes MPI, BOM, and Assembly Drawing for production personnels. Also, performed efficient BOM comparisons. • Controlled revision changes that include BOM changes and customer directives. • Led and trained a team of three engineering assistants to accomplish various assignments such as recycling project of more than 1200 stencils.
-
-
-
Solar Turbines
-
United States
-
Oil and Gas
-
700 & Above Employee
-
Senior Design Team from Texas A&M University
-
Feb 2010 - May 2010
• Analyzed the system's bottleneck and performed assembly-line balancing analysis that resulting in 43% reduction of queuing times. • Documented new production routings. • Analyzed the system's bottleneck and performed assembly-line balancing analysis that resulting in 43% reduction of queuing times. • Documented new production routings.
-
-
-
-
Manufacturing Development Intern
-
May 2009 - Jul 2009
• Developed current process map of new product development • Developed tools to enhance the process of developing new product. Tools include: Process Failure Mode and Effect Analysis (PFMEA), Control Plan, and Production Process Flow Chart (PPFC) • Presented a weekly progress report to plant manager • Developed current process map of new product development • Developed tools to enhance the process of developing new product. Tools include: Process Failure Mode and Effect Analysis (PFMEA), Control Plan, and Production Process Flow Chart (PPFC) • Presented a weekly progress report to plant manager
-
-
-
GE Power
-
United States
-
Electric Power Generation
-
700 & Above Employee
-
Industrial Engineering Co-op
-
Aug 2008 - Jan 2009
• Oversaw repairing processes performed in house as well as by external vendors. • Prioritized work orders to meet promised shipment dates. • Occasionally generated inspection reports for the customers. • Oversaw repairing processes performed in house as well as by external vendors. • Prioritized work orders to meet promised shipment dates. • Occasionally generated inspection reports for the customers.
-
-
Education
-
Texas A&M University
Bachelor's degree, Industrial Engineering
Community
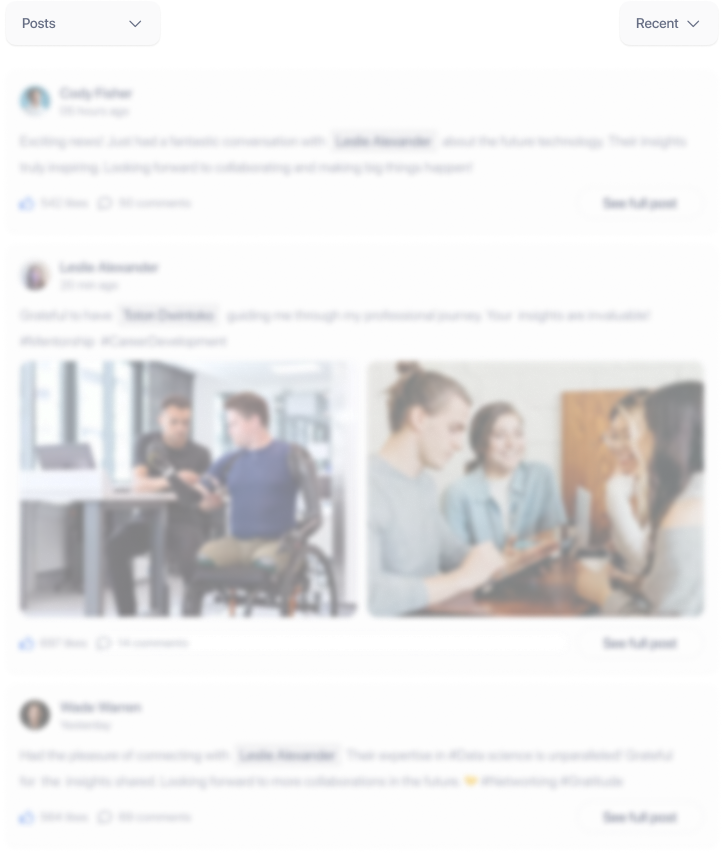