Pamala Knox
Supplier Quality Engineer at Inalfa Roof Systems, Inc. - North America- Claim this Profile
Click to upgrade to our gold package
for the full feature experience.
Topline Score
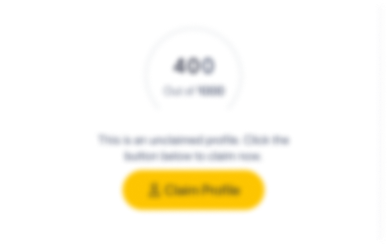
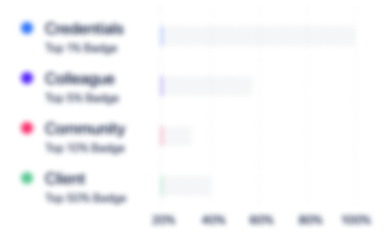
Bio

Clark Morrison
Worked with Pamala over several years. She is very capable, hard working and loyal. She would be a great attribute to any company she might work with.

Kristie J.
I had the pleasure of working with Pamala in the Quality Department at Inalfa Roof Systems. Pamala always does her job with integrity and dedication. She is motivated and takes the initiative to help solve problems without being asked. She’s able to communicate issues and expectations clearly, and follows though to ensure timely closure. As a Supplier Quality Engineer, Pamala is articulate, extremely knowledgeable, and a valuable resource not only to the Company, but also to the Suppliers she mentors and works with. No matter how difficult the issue is, Pamala goes above and beyond to help solve it, all the while keeping her professionalism and sense of humor. Pam is an absolute joy to work with.

Clark Morrison
Worked with Pamala over several years. She is very capable, hard working and loyal. She would be a great attribute to any company she might work with.

Kristie J.
I had the pleasure of working with Pamala in the Quality Department at Inalfa Roof Systems. Pamala always does her job with integrity and dedication. She is motivated and takes the initiative to help solve problems without being asked. She’s able to communicate issues and expectations clearly, and follows though to ensure timely closure. As a Supplier Quality Engineer, Pamala is articulate, extremely knowledgeable, and a valuable resource not only to the Company, but also to the Suppliers she mentors and works with. No matter how difficult the issue is, Pamala goes above and beyond to help solve it, all the while keeping her professionalism and sense of humor. Pam is an absolute joy to work with.

Clark Morrison
Worked with Pamala over several years. She is very capable, hard working and loyal. She would be a great attribute to any company she might work with.

Kristie J.
I had the pleasure of working with Pamala in the Quality Department at Inalfa Roof Systems. Pamala always does her job with integrity and dedication. She is motivated and takes the initiative to help solve problems without being asked. She’s able to communicate issues and expectations clearly, and follows though to ensure timely closure. As a Supplier Quality Engineer, Pamala is articulate, extremely knowledgeable, and a valuable resource not only to the Company, but also to the Suppliers she mentors and works with. No matter how difficult the issue is, Pamala goes above and beyond to help solve it, all the while keeping her professionalism and sense of humor. Pam is an absolute joy to work with.

Clark Morrison
Worked with Pamala over several years. She is very capable, hard working and loyal. She would be a great attribute to any company she might work with.

Kristie J.
I had the pleasure of working with Pamala in the Quality Department at Inalfa Roof Systems. Pamala always does her job with integrity and dedication. She is motivated and takes the initiative to help solve problems without being asked. She’s able to communicate issues and expectations clearly, and follows though to ensure timely closure. As a Supplier Quality Engineer, Pamala is articulate, extremely knowledgeable, and a valuable resource not only to the Company, but also to the Suppliers she mentors and works with. No matter how difficult the issue is, Pamala goes above and beyond to help solve it, all the while keeping her professionalism and sense of humor. Pam is an absolute joy to work with.

Credentials
-
Lean Six Sigma Blackbelt
Lawrence Technological UniversityJun, 2018- Nov, 2024 -
Lean Six Sigma Greenbelt
Lawrence Technological UniversityJun, 2018- Nov, 2024 -
Advanced Project Management
Lawrence Technological UniversityMay, 2018- Nov, 2024
Experience
-
Inalfa Roof Systems North America
-
United States
-
Motor Vehicle Parts Manufacturing
-
100 - 200 Employee
-
Supplier Quality Engineer
-
Jan 2018 - Present
-
-
-
-
Supplier Quality Engineer/Customer Liaison
-
Oct 2017 - Jan 2020
Primary Duties & ResponsibilitiesOn site quality representation for Automotive Supplier Clients.Attendance at all Customer quality and warranty meetings.Attendance at all Customer engineering and vehicle launch meetings.Direct involvement with Customer quality and engineering teams in understanding quality concerns, data collection, measurement analysis and root cause identification.Direct involvement with Customer quality and engineering teams in establishing Interim Containment Actions.Direct involvement with Client quality and engineering teams to understand and establish Permanent Corrective Actions.Communication with Client and Customer teams to present Client actions and countermeasures to address identified quality concerns.Interaction with Customer production teams and managers in the production environment.Understand, adhere to and practice safety guidelines in the production environment.Work and communicate within the Quality Strategies teams to developed team concepts, goals and directions to increase efficiency.
-
-
-
-
Quality Manager
-
Jul 2011 - Sep 2017
Communicated with client regarding quality issues including 8D or client specific corrective action tools Communicated continuous improvement projects with the customers Communicated with client specific requirements and retrieving the associated test methods Supported the lab test package presentation with the customers Reviewed, communicated, and transmitted PPAP documents to client Analyzed and interpreted technical data and information Coordinated and obtained quotes for testing Directed international liaisons both remotely and onsite Knowledgeable in TS16949
-
-
-
NYX Inc.
-
United States
-
Motor Vehicle Manufacturing
-
400 - 500 Employee
-
Supplier Quality Representative
-
Jun 2008 - Nov 2009
Supplier Quality Plant Representative / GM Supported any requirements from NYX including but not limited to dimensional studies on parts, validation builds, and launch of new programs. Improving customer satisfaction, reducing customer rejections, improve part quality and performance of Supplier and continuous improvement. Worked with the GM team to analyze & identify root cause and corrective action by following the 7 Diamond process. Initiating and coordinating sorts at GM/Sequencer and communicating results to Supplier, coordinate PTRs and ECN breakpoints between Supplier/Sequencer/GM.
-
-
-
-
Community and Corporate Affairs Department - Local Business Inclusion Team Leader
-
Dec 2001 - Sep 2007
Ensured that LB Participation was sought at all levels and tiers including: prime contractors, subcontractors, joint ventures, suppliers and brokers.Represented Managment Team in meetings with Implementation team, Construction Managers, Architects, etc. Assisted in LB coordination and negotiations as required.Prepared and maintained LB Inclusion Monthly Reports as required by the owner. Ensured that LB Participation was sought at all levels and tiers including: prime contractors, subcontractors, joint ventures, suppliers and brokers.Represented Managment Team in meetings with Implementation team, Construction Managers, Architects, etc. Assisted in LB coordination and negotiations as required.Prepared and maintained LB Inclusion Monthly Reports as required by the owner.
-
-
-
-
Quality Manager
-
Apr 2000 - Oct 2001
Reviewed technical problems and procedures of departments and recommended solutions to problems or changes in procedures. Visited with representatives of material and component vendors to obtain information related to supply quality, capacity of vendor to meet orders, and vendor quality standards. Conferred with engineers about quality assurance of new products designed and manufactured products on market to rectify problems. Communicated with customers on continuous improvement and quality concerns. Worked with sales representatives.
-
-
-
-
Quality Laboratory Technician
-
Jul 1998 - Apr 2000
Performed physical test on leather in accordance with customer specifications: reported test results on worksheets, logs, and computer systems, evaluated tests against visual, numeric and other standards, assigned dispositions to the tests and production lot’s within a series of guidelines; maintained and filed test samples, worksheets, and production routines; prepared sample presentation packages; visual color evaluations.Returned to work at EOALC in October 2007 through January 2008 contracted through Adecco Engineering & Technical Consultants. Assisted in the company’s transition to Mexico and South American EOALC facilities. Responsibilities included physical and chemical testing, authorizing and shipping material to these facilities as well as to EOALC customers. Other responsibilities included: general administrative duties (data entry, production reporting and updates).
-
-
-
-
Chemical Laboratory Technician / Coatings and Colorants Division
-
Mar 1994 - Jan 1997
Support for color matching and physical testing team for General Motors Product Engineering Department. Research and Development in Heavy Transportation and Industrial Division, performed a wide range of technical and administrative duties including raw material screening, formulations, physical testing, applications, appearance evaluations, cost analysis, risk assessment, new product submission and launch. Support for color matching and physical testing team for General Motors Product Engineering Department. Research and Development in Heavy Transportation and Industrial Division, performed a wide range of technical and administrative duties including raw material screening, formulations, physical testing, applications, appearance evaluations, cost analysis, risk assessment, new product submission and launch.
-
-
-
-
Exterior Coatings
-
1992 - 1994
Support for new product submission and launch of exterior coatings. Support for new product submission and launch of exterior coatings.
-
-
Education
-
Tuskegee University
B.S., Biology -
Central Michigan University
Graduate Program - Pending MSA, Business Administration and Management, General
Community
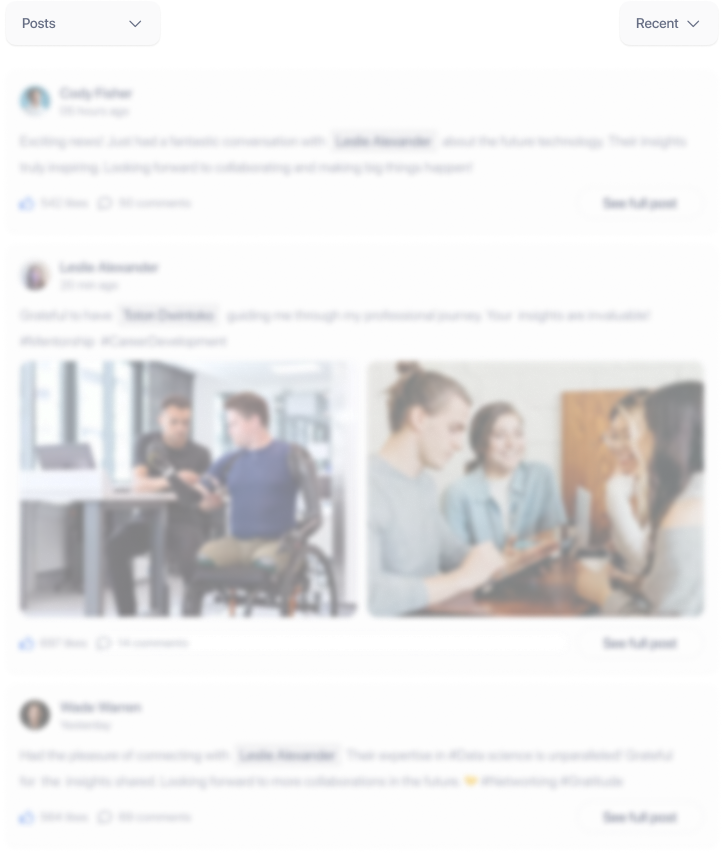