Caleb Moreland, CPIM
Planning and Fulfillment Specialist at Dodge Industrial, Inc.- Claim this Profile
Click to upgrade to our gold package
for the full feature experience.
Topline Score
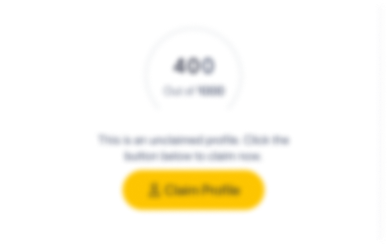
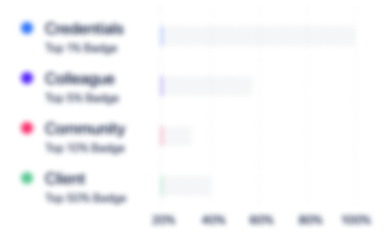
Bio


Credentials
-
L6S Yellow Belt
Lean Methods GroupJun, 2018- Nov, 2024 -
Certified in Production and Inventory Management (CPIM)
APICSApr, 2019- Nov, 2024
Experience
-
Dodge Industrial, Inc.
-
United States
-
Industrial Machinery Manufacturing
-
300 - 400 Employee
-
Planning and Fulfillment Specialist
-
Nov 2021 - Present
-
-
-
ABB Motors and Drives North America
-
United States
-
Industrial Automation
-
400 - 500 Employee
-
Planning & Fulfillment Business Analyst
-
Nov 2019 - Nov 2021
-
-
-
ABB
-
Switzerland
-
Automation Machinery Manufacturing
-
700 & Above Employee
-
Sourcing Specialist
-
May 2019 - Nov 2019
Worked to drive plant cost savings projects with support from global, regional, and local resources. Steps included planning, negotiations, cross-functional collaboration, recording results, and targeting potential new cost savings opportunities. Assisted in daily operations from resolving material shortages to data cleanup for sourcing functions. Organized plant reporting for conflict minerals and supplier performance evaluations. Worked to drive plant cost savings projects with support from global, regional, and local resources. Steps included planning, negotiations, cross-functional collaboration, recording results, and targeting potential new cost savings opportunities. Assisted in daily operations from resolving material shortages to data cleanup for sourcing functions. Organized plant reporting for conflict minerals and supplier performance evaluations.
-
-
-
ABB Motors and Drives North America
-
United States
-
Industrial Automation
-
400 - 500 Employee
-
Supply Chain Analyst
-
Aug 2018 - May 2019
Worked on the Supply Chain Compliance & Productivity Team. Passed examinations and achieved APICS CPIM certification. Led initiative to on-board all potential suppliers for business unit to electronic supplier communication platforms, including EDI. Communicated with suppliers and plant supply chain contacts to mediate communications and troubleshoot supplier On-Time Delivery issues. Used Five-Why process to determine underlying issues and continued to monitor suppliers' performances to drive continued improvements. Reached out to numerous suppliers for updating systematic lead times for cleanup of material master data in SAP. Compared prior supplier/material delivery times to actual delivery times to calculate added safety time for buffer against supplier variability. Additionally used Excel skills and data analysis to correct and update scaled costing lot sizes. Created over a dozen bid packages and RFQs for category managers' cost savings initiatives.
-
-
-
ABB
-
Switzerland
-
Automation Machinery Manufacturing
-
700 & Above Employee
-
Supply Chain Analyst (Corporate - Indirect)
-
Jan 2018 - Jul 2018
Networked with Americas Region Supply Chain Managers and leaders and gained a comprehensive understanding of the Procurement & Logistics organization. Eventually helped with entire organization's supplier payment term standardization initiatives. Added cost savings from contract management using extensive data analysis in order to negotiate a supplier contract relationship. Expanded SCM and business knowledge on a regular basis by working with internal customers in numerous tools extending across the organization's supply chain. Coordinated hands-on training with multiple employees in these tools and other supply chain roles. Reported to ABB's Supplier Diversity Manager, working with external party to ensure data accuracy for reporting and improvement.
-
-
-
Pratt & Whitney
-
United States
-
Aviation and Aerospace Component Manufacturing
-
700 & Above Employee
-
Supply Chain Co-op
-
Jan 2017 - Aug 2017
Sustained production planning activities for aircraft engine fan-blades from initial reception of raw bodies, to material assignments, and eventually into initial operations. Generated requests for quotations and purchased materials used for aftermarket support of engine parts and services for fan blade processing from numerous vendors. Measured, brainstormed, and calculated dimensions for structural and design improvements to warehouse freezer, focusing on safety and ease of employee navigation. Initiated sustainability-focused projects to improve energy consumption and reduce waste, including the introduction of energy-efficient hand dryers for all local plants.
-
-
-
Michigan State University
-
United States
-
Higher Education
-
700 & Above Employee
-
Student Supervisor and Culinary Production Employee
-
Oct 2014 - Dec 2016
Entrusted with supervision, coordination, and training of culinary student and full-time employees in operational tasks and customer service after promotion in January 2016. Given responsibility for a variety of team-oriented duties in numerous Culinary Service processes including: dish room assistance, production of meals, and distribution to student body. Entrusted with supervision, coordination, and training of culinary student and full-time employees in operational tasks and customer service after promotion in January 2016. Given responsibility for a variety of team-oriented duties in numerous Culinary Service processes including: dish room assistance, production of meals, and distribution to student body.
-
-
-
Oshkosh Corporation
-
United States
-
Motor Vehicle Manufacturing
-
700 & Above Employee
-
Materials Management Intern
-
Jun 2016 - Aug 2016
Gained functional business knowledge at the Global Procurement and Supply Chain Management facility through training modules and hands-on experience in multiple supply chain areas including logistics, materials management, and purchasing related disciplines. Accomplished team-supporting tasks for electronic Kanban setup of the new production facility in León, Mexico to efficiently maintain material flow in conjunction with the launch of a new ERP system. Created a comprehensive training manual for Kanban deployment and systems configuration as part of a greenfield plant launch in Leon, Mexico. Spearheaded the deployment of a new tactical purchasing material planning process to improve on-time delivery and reduce freight costs.
-
-
-
Gull Lake View Golf Resort
-
United States
-
Travel Arrangements
-
1 - 100 Employee
-
Stonehedge Golf Shop Assistant
-
2010 - Jun 2016
Mastered vital operations in the Pro Shop and supported the organization’s sales and marketing objectives through retail sales, telephone service techniques, and customer relations. Received numerous service responsibilities through strong commitment to increasing personal abilities and by exhibiting outstanding effort and work ethic. Mastered vital operations in the Pro Shop and supported the organization’s sales and marketing objectives through retail sales, telephone service techniques, and customer relations. Received numerous service responsibilities through strong commitment to increasing personal abilities and by exhibiting outstanding effort and work ethic.
-
-
Education
-
Michigan State University
Bachelor’s Degree, Supply Chain Mangement -
Northern Michigan University
-
Galesburg-Augusta High School
High School
Community
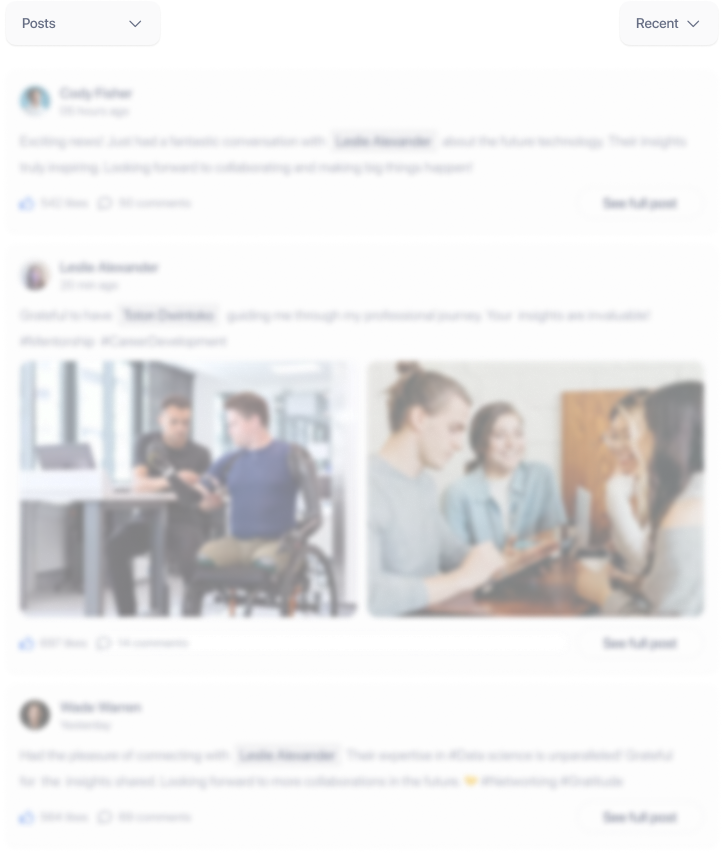