
Ailsa Greene
Operations Manager at Nimbis Designs, LLC- Claim this Profile
Click to upgrade to our gold package
for the full feature experience.
-
Spanish Native or bilingual proficiency
-
French Native or bilingual proficiency
-
English Native or bilingual proficiency
Topline Score
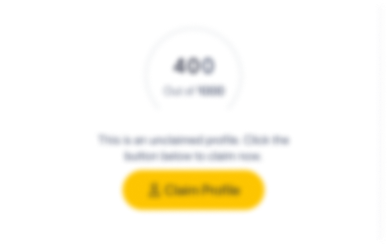
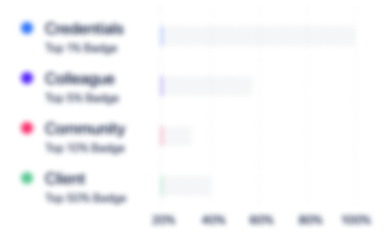
Bio


Experience
-
Nimbis Designs, LLC
-
United States
-
IT Services and IT Consulting
-
1 - 100 Employee
-
Operations Manager
-
May 2020 - Present
-
-
-
Thermo Fisher Scientific
-
United States
-
Biotechnology Research
-
700 & Above Employee
-
Distribution Supervisor
-
Jun 2018 - May 2019
I managed a team of 25 to 30 warehouse employees and am responsible for the successful daily operation and end of shift by striving for 100% Line Item Fill Rate so that our customers get their products on time, the first time, every time.
-
-
Sr. Associate Business Excellence Specialist
-
Jul 2016 - Jun 2018
I spent two years working across the core functions of supply chains: Source, Buy, Make and Deliver. I had to learn and align with each function's objectives fast. At the end, I finished the program with a wholistic understanding of supply chain from end to end. Below is a list of the projects I worked on within each function.Operations Finance (February 2018 - June 2018, Carlsbad, CA)• Supported the Sourcing and Procurement organizations with consolidation of monthly and quarterly financial metrics, • Managed user acceptance testing and improvement projects related to company acquisitions.Master Data Management (August 2017 - February 2018, Carlsbad, CA)• Created audit program for critical ERP data elements that can negatively impact ATP.Distribution (February 2017 - August 2017, Frederick, MD)• Planned and managed a warehouse-wide change project to improve pick rates and saved $48k.• Researched and proposed a business plan for warehouse staffing based on variable daily demand and volume.NGS Manufacturing (July 2016 to February 2017, Carlsbad, CA)• Created sustainable documentation and training methods for the integration of a new automated manufacturing process.• Proposed the usage of “frost-top table” that enabled us to run two manufacturing cells in parallel and reduce waste.• Drove the adoption of the PPI business system within the team by creating a daily management board that displayed and tracked the team’s performance using KPIs.
-
-
-
General Atomics Aeronautical Systems
-
United States
-
Aviation and Aerospace Component Manufacturing
-
700 & Above Employee
-
Senior Design Project
-
Jan 2016 - May 2016
- I worked with two other team members to proposed a plan to reduce non-value added delays in production of aircraft composite subcomponent to increase production rates by 50% using the DMAIC methodology- We applied various Lean/Six Sigma analytical tools to complete this project including ANOVA, paired t-tests, time studies, VOC and value stream mapping. - I worked with two other team members to proposed a plan to reduce non-value added delays in production of aircraft composite subcomponent to increase production rates by 50% using the DMAIC methodology- We applied various Lean/Six Sigma analytical tools to complete this project including ANOVA, paired t-tests, time studies, VOC and value stream mapping.
-
-
-
Thermo Fisher Scientific
-
United States
-
Biotechnology Research
-
700 & Above Employee
-
Sourcing Engineering Intern
-
Sep 2015 - May 2016
I supported the Sourcing Engineering team with asset management of plastic molds and continuous improvement projects.
-
-
Procurement Intern
-
Jun 2015 - Aug 2015
My responsibility was to support the External Manufacturing procurement team as a Global MRP for two international suppliers. I analyzed quarterly forecasts, purchased both MTS and MTO SKUs across two different ERP systems, and improved the MRP settings for a supplier making in order to have healthier inventory and lower risk of BO. I also drove continuous improvement projects for my team's purchasing process, did ERP systems testing for a new MTO product, and wrote an SOP for a buyer that was to take over a new supplier.
-
-
Supplier Quality Engineering Intern
-
Jun 2014 - May 2015
As a Global Operations intern at the Life Sciences Group of Thermo Fisher Scientific I was exposed to how a robust supply chain operates and drives growth and savings for the company. My responsibility is to support the Supplier Quality team. Specifically they include, accompanying and assisting the Supplier Quality Engineers at site visits, implementing and training on improvements to some internal processes, and supporting in the validation process machines for quality purposes.
-
-
-
JAE Electronics
-
United States
-
Appliances, Electrical, and Electronics Manufacturing
-
200 - 300 Employee
-
Engineering Intern
-
Jun 2013 - Aug 2013
- Researched and documented the company’s automatic labeling and tracking system for manufactured harnesses. - Developed troubleshooting and change management procedures. - Researched and documented the company’s automatic labeling and tracking system for manufactured harnesses. - Developed troubleshooting and change management procedures.
-
-
Education
-
University of San Diego
Bachelor’s Degree, Industrial and Systems Engineering -
Immaculate Conception Academy
High School
Community
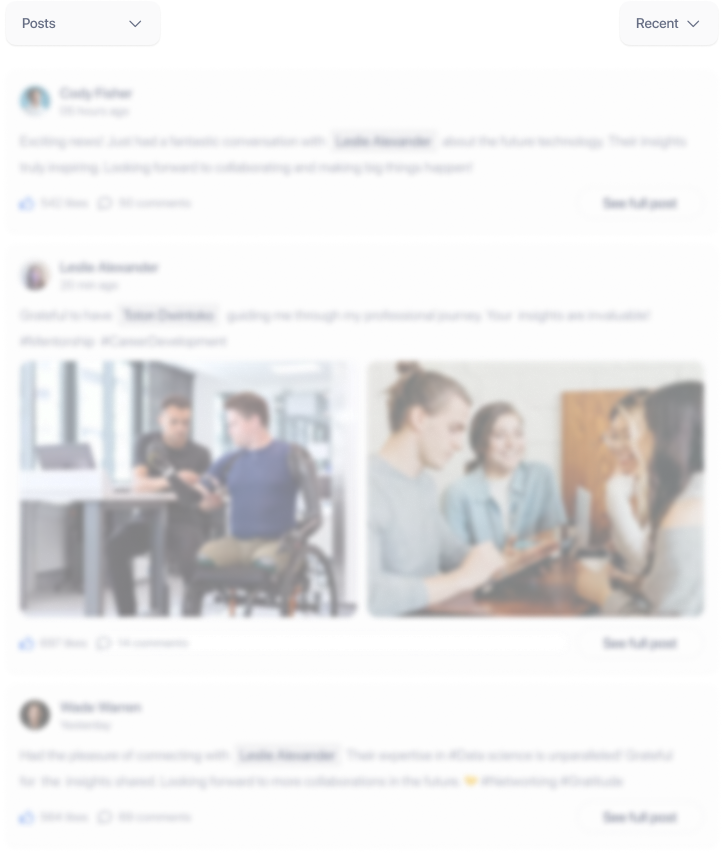