Divy Ashish Shah
Industrial Engineer, Supply Chain Strategy and Planning at Headway Technologies- Claim this Profile
Click to upgrade to our gold package
for the full feature experience.
-
English -
-
Gujarati Native or bilingual proficiency
-
Hindi Native or bilingual proficiency
-
Marathi Native or bilingual proficiency
Topline Score
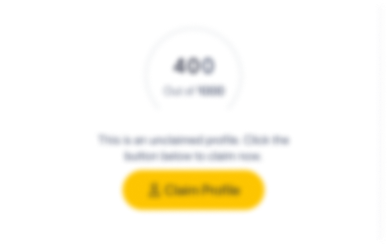
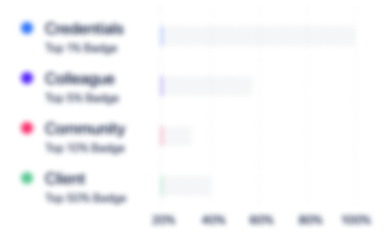
Bio

Rassoul Rassouli
Divy was working in quality department as an Industrial engineer for almost one year between 2018-2019. During that time, he was instrumental on setting the metrics for quality and other departments. He also had an important role in continuous improvement activities which helped Jabil Fremont save hundreds of thousands dollar in scrap reduction. Divy is team player and at the same time persuasive. People across different functions liked him a lot because he was helping them a lot. His persistence on getting the job done is admirable. He is a talented engineer and a fast learner. I highly recommend him for any operational positions.

Jake Summers
Divy produces high quality work and is not afraid to get his hands dirty. He has demonstrated his ability to solve problems by working with multiple groups to understand the root cause and develop sustainable counter measures. He is always looking for ways to improve processes and would be an asset to any team!

Rassoul Rassouli
Divy was working in quality department as an Industrial engineer for almost one year between 2018-2019. During that time, he was instrumental on setting the metrics for quality and other departments. He also had an important role in continuous improvement activities which helped Jabil Fremont save hundreds of thousands dollar in scrap reduction. Divy is team player and at the same time persuasive. People across different functions liked him a lot because he was helping them a lot. His persistence on getting the job done is admirable. He is a talented engineer and a fast learner. I highly recommend him for any operational positions.

Jake Summers
Divy produces high quality work and is not afraid to get his hands dirty. He has demonstrated his ability to solve problems by working with multiple groups to understand the root cause and develop sustainable counter measures. He is always looking for ways to improve processes and would be an asset to any team!

Rassoul Rassouli
Divy was working in quality department as an Industrial engineer for almost one year between 2018-2019. During that time, he was instrumental on setting the metrics for quality and other departments. He also had an important role in continuous improvement activities which helped Jabil Fremont save hundreds of thousands dollar in scrap reduction. Divy is team player and at the same time persuasive. People across different functions liked him a lot because he was helping them a lot. His persistence on getting the job done is admirable. He is a talented engineer and a fast learner. I highly recommend him for any operational positions.

Jake Summers
Divy produces high quality work and is not afraid to get his hands dirty. He has demonstrated his ability to solve problems by working with multiple groups to understand the root cause and develop sustainable counter measures. He is always looking for ways to improve processes and would be an asset to any team!

Rassoul Rassouli
Divy was working in quality department as an Industrial engineer for almost one year between 2018-2019. During that time, he was instrumental on setting the metrics for quality and other departments. He also had an important role in continuous improvement activities which helped Jabil Fremont save hundreds of thousands dollar in scrap reduction. Divy is team player and at the same time persuasive. People across different functions liked him a lot because he was helping them a lot. His persistence on getting the job done is admirable. He is a talented engineer and a fast learner. I highly recommend him for any operational positions.

Jake Summers
Divy produces high quality work and is not afraid to get his hands dirty. He has demonstrated his ability to solve problems by working with multiple groups to understand the root cause and develop sustainable counter measures. He is always looking for ways to improve processes and would be an asset to any team!

Credentials
-
Lean Six Sigma Green Belt
GreyCampusJan, 2017- Nov, 2024
Experience
-
Headway Technologies
-
United States
-
Computer Hardware Manufacturing
-
200 - 300 Employee
-
Industrial Engineer, Supply Chain Strategy and Planning
-
Feb 2019 - Present
-
-
-
Jabil
-
United States
-
Appliances, Electrical, and Electronics Manufacturing
-
700 & Above Employee
-
Industrial Engineer
-
Jun 2018 - Feb 2019
• Designed a comprehensive performance measurement system and developed KPIs like Scrap Ratio, Customer Reject Rate, First Pass Yield Ratio, Defect Rate and designed new processes to collect required data to analyze and worked with teams to improve metrics and reported critical data • Established supplier performance metrics, audited, and assisted the suppliers to improve processes • Optimized material flow process within different facilities, and vendors to reduce motion of the parts, decreased cycle time by 10%, reduced discrepancies by 7%, and decreased the cost of transportation • Verified and validated internal manufacturing processes using Statistical Process Control methods, performed Failure Mode Effect Analysis, collaborated with Operations and Quality Engineering teams to improve manufacturing processes Show less
-
-
-
Tesla
-
United States
-
Motor Vehicle Manufacturing
-
700 & Above Employee
-
Manufacturing Operations Intern, Operations Excellence
-
Jan 2018 - May 2018
• Analyzed quality data and relocated 4 headcounts and 2 handguns in Falcon Door Line in a Kaizen project by using Lean techniques like time studies, Yamazumi charts, line balancing, resulting in a total savings of $285,000 per year and increased utilization of other associates • Created and implemented a standard work process in the Trim 05 Kitting area by implementing color coding, visual Kanban, and designed 5S poke-yoked kitting tote resulting in reduction of downtime from 120 minutes per week to 15 minutes a week due to part shortage issue in the general assembly line, therefore increasing the output by 50 cars • Reduced motion, travel, over processing, defects, overproduction types of wastes by redesigning process in Trim 05 kitting • Planned and implemented Smart Racks (Pick to Light/Box) in the factory and conducted training sessions for the same • Eliminated part shortage issue at South Paints Shop by building a supermarket for the small parts and large parts and planned implementation of Pick to box system to eliminate the communication gap between South Paints and Plastics resulting in 20% reduction of downtime • Reduced 250 sq. ft. lineside footprint by executing a sequencing project and reduced handling and quality defects • Standardized and optimized the manufacturing processes, thus reducing the cycle time, quality defects and variability • Reduced downtime caused by errors in the GA S/X by using root cause analysis, value stream mapping, Kanban and 5S techniques • Optimized General Assembly (GA) line side layout, addressing severe safety, ergonomic issues regarding the parts and standard work, thus reducing line side footprint, safety-related issues, and cycle time • Audited processes at specific stations after combining quality defects data and smart rack compliance data and improved them resulting in an increase in the smart racks compliance report and a drastic reduction in quality defects in general assembly lines Show less
-
-
-
New York University
-
Higher Education
-
700 & Above Employee
-
Graduate Assistant
-
Sep 2017 - Dec 2017
-
-
-
ABCO HVACR Supply + Solutions
-
United States
-
Wholesale
-
100 - 200 Employee
-
Distribution and Supply Chain Intern
-
Jun 2017 - Aug 2017
Process Engineering and Process Improvement 1. Standardized the working processes of receiving, checking-in, staging, ‘putaway’ and picking activities throughout the DC 2. Reduced non-value added time by 20% and motion & over processing of resources by 15% using lean tools like 5S, Kanban and root cause analysis 3. Conducted training sessions for implementation of Warehouse Management System (WMS) and conducted 5S audit throughout the DC 4. Carried out ABC categorization of supplies and optimized warehouse layout 5. Scheduled outbound delivery on the basis of full and effective utilization of the staging area 6. Assessed and optimized the processes and equipment used in the facility 7. Created SOPs for efficient and standardized workflow 8. Conducted data analysis to reduce over processing of products by pitching time and money management to vendors, therefore saving time spent by 38% and saving costs by $148 per truck, roughly saving $15,000 per vendor per year Show less
-
-
-
Reliance Industries Limited
-
India
-
Oil and Gas
-
700 & Above Employee
-
Project Intern
-
Dec 2014 - Jan 2015
Maintenance Department of Shell & Heat Exchanger plant in the Reliance Industries Limited Oil and Petrochemical Oil Refinery. 1. Conducted a detailed study on shell and tube heat exchangers. 2. Responsible for the maintenance of the exchangers under mentors’ supervision. 3. Prepared and presented a report to the Project Manager on the shell and tube heat exchangers studied various parts, nomenclatures, various types of exchangers, inspection methods, problems faced and rectification methods. Show less
-
-
Education
-
New York University
Master of Science (M.S.), Industrial Engineering -
KJ Somaiya College of Engineering, Vidyavihar
Bachelor of Engineering (B.E.), Mechanical Engineering
Community
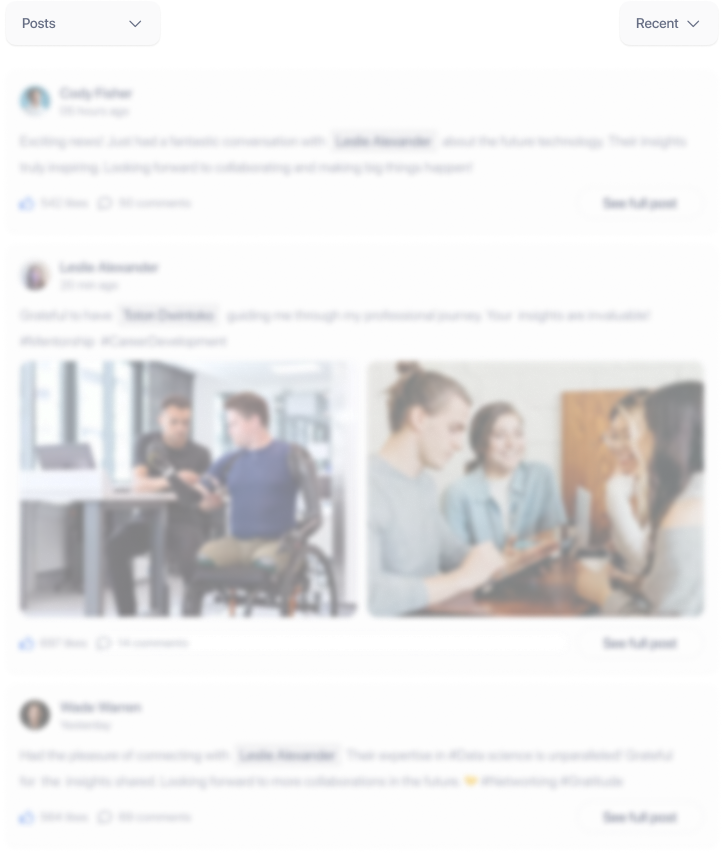