
Robert Trenkenschu
Regional General Manager at Shenandoah Growers, Inc. at Shenandoah Growers, Inc.- Claim this Profile
Click to upgrade to our gold package
for the full feature experience.
-
English Native or bilingual proficiency
-
German Professional working proficiency
Topline Score
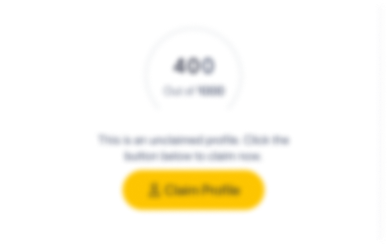
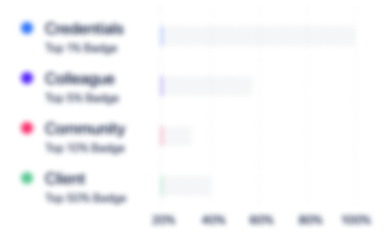
Bio


Experience
-
Shenandoah Growers, Inc.
-
United States
-
Farming
-
1 - 100 Employee
-
Regional General Manager at Shenandoah Growers, Inc.
-
2021 - Present
REGIONAL GENERAL MANAGER/FACILITIES MANAGEMENTRecruited to oversee eastern region build and operations of state-of-the-art indoor vertical farms and greenhouses.► Financial management including financial planning & analysis, CapEx projects, capital growth, financial reporting, inventory controls, policies/procedures, and accounting. Established/maintained budgets.► Provided leadership and developed strategies to achieve favorable variances. Tracked and optimized efficiencies in pursuit of cost-effective production objectives related to customer sales, labor, harvest yields, quality, shelf life, inventory, utilities, transportation, and repair & maintenance.► Maintained, evaluated and recommended improvements for regulatory compliance, food safety, and internal control audits in a fast-paced, high volume CPG manufacturing environment.► Increased daily output and improved plant health through implementation of improved nutrition, irrigation, climate (humidity, temperature, & airflow), LED lighting, and daily recording and reporting of pH, EC, NH4-N, NO2-N, and NO3-N. Instituted weekly tissue, fertigation, water, and soil sample laboratory analytical reporting. Reduced pest pressure by over ninety percent.► Reduced capital equipment and facility unscheduled downtime/breakdowns through the evaluation and implementation of improved maintenance procedures. Oversaw/performed equipment and facility modifications, repair and maintenance.► Led continuous improvement initiatives including Lean Six Sigma 5S methodology, TPS, Lean manufacturing, visual management, performance measurement, Poka-Yoke, QCO, TPM, QCPC, Kaizen & Kanban.► Improved training programs. Documented and maintained elevated standards of training and safety awareness.
-
-
-
Graphic Wood Technologies, LLC (a subsidiary of EcoFuel Group)
-
United States
-
Paper and Forest Product Manufacturing
-
1 - 100 Employee
-
Vice-President Plant Operations & Engineering
-
2018 - 2020
Recruited to oversee production and supervise/perform equipment and facility repair/maintenance.► Increased daily production upwards of 200% and improved on-time deliveries from 53% to 96% within six months (while eliminating overtime).► Reduced manufacturing equipment and facility downtime/breakdowns by 93% through the implementation of improved maintenance procedures.► Restored company profit (first in over ten years) facilitating its acquisition. Recruited to oversee production and supervise/perform equipment and facility repair/maintenance.► Increased daily production upwards of 200% and improved on-time deliveries from 53% to 96% within six months (while eliminating overtime).► Reduced manufacturing equipment and facility downtime/breakdowns by 93% through the implementation of improved maintenance procedures.► Restored company profit (first in over ten years) facilitating its acquisition.
-
-
-
-
Business Consultant - Business Development
-
2015 - 2018
Engaged to assess possible national expansion and introduce product to a national client base, increasing visibility and boosting brand recognition. Engaged to assess possible national expansion and introduce product to a national client base, increasing visibility and boosting brand recognition.
-
-
-
-
President
-
1994 - 2017
Spearheaded all corporate aspects of a multimillion-dollar contract manufacturing company, with a peak performance of $43M in annual revenue and more than 100 employees. Supervise a wide host of operations, manufacturing, engineering, quality, maintenance, supply chain, IT, HR, and customer service managers. Oversaw daily operations, HR/staff management, recruitment, program development, supplier/client contract negotiations, capital growth, technology enhancements, financial reporting, inventory controls, policies/procedures, accounting, customer service, and safety committees. Established/maintained budgets. Consulted with OEM Customers and strategic partners to resolve and/or improve machining and raw material issues/concerns in order to improve quality.►Exceeded EBITDA growth goals and increased sales from $1.9M to $43M annually through expanded customer base, development of strategic partnerships, state of the art equipment acquisitions, lean manufacturing principles, continuous improvement processes, and mergers & acquisitions (M&A).►Planned, deployed, and led all lean activities producing significant cost savings through productivity, business processes, quality, and waste reduction initiatives. Drove improvements via lean Six Sigma 5S methodology, TPS, lean manufacturing, visual management, performance measurement, Poka-Yoke, QCO, TPM, QCPC, Kaizen & Kanban.►Developed and implemented employee training/education procedures that led to the company’s contract machining facility being the only one of its kind to attain the following registrations in a unique integrated management system (IMS): AS 9100, ISO 13485, ISO/TS 16949, ISO 9001, ISO 14001, BS OHSAS 18001 and ITAR.►Created a dedicated, action-oriented employee base and executive team by instilling a culture of open dialogue and collaborative problem resolution that fostered confidence and trust with both internal and external stakeholders, and insured business continuity and broad corporate success.
-
-
-
-
Vice President
-
1988 - 1993
Promoted to manage all equipment, lead facility repair/maintenance, and oversee the supply chain, with leadership responsibility of 35+ people including Production, Quality, Maintenance, and Office Managers. Responsible for employee recruitment and retention to include all aspects of human resources, sourcing, security, recruiting and staffing. Managed bookkeeping functions (A/P, A/R, payroll, cash flow projections, budgeting, proposal work, etc.)►Successfully identified, completed and integrated multiple acquisitions with a total value of approximately $500K.►Negotiated contracts with suppliers (including pricing and payment terms) resulting in cost reductions averaging 18% for raw materials, tooling, equipment, equipment parts and service, utilities, insurance & freight.►Lowered health care costs 28% without decreasing benefits. ►Reduced labor costs 12% by decreasing equipment setup time, job changeover time and improved work holding design.►Reduced tooling costs roughly 30% by extending tool life through the application of new technologies including coatings, lubrication and machining practices. ►Improved Logistics by contracting with local carriers, cutting costs by 22%.►Reduced the frequency of outside equipment and facility repair and maintenance services, saving approximately $36K per year.
-
-
-
-
Maintenance Manager
-
1985 - 1987
Managed all equipment and facility repair and maintenance, bookkeeping functions (A/P, A/R, payroll), logistics, and material handling. Managed all equipment and facility repair and maintenance, bookkeeping functions (A/P, A/R, payroll), logistics, and material handling.
-
-
Education
-
DeVry Institute of Technology
Electronics -
University of Illinois at Chicago
Engineering
Community
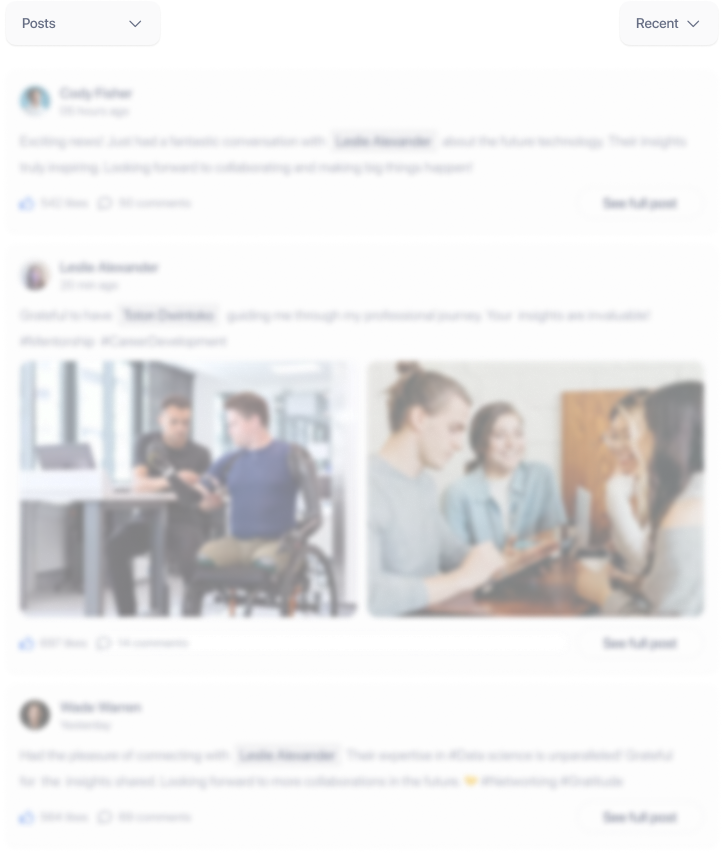