Neal Hunter
Supplier Quality Program Manager at E Ink Corporation- Claim this Profile
Click to upgrade to our gold package
for the full feature experience.
Topline Score
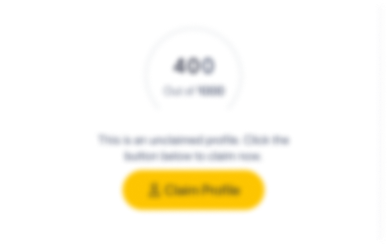
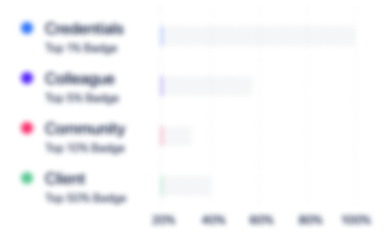
Bio


Experience
-
E Ink Corporation
-
United States
-
Appliances, Electrical, and Electronics Manufacturing
-
400 - 500 Employee
-
Supplier Quality Program Manager
-
Mar 2020 - Present
-
-
-
Symbotic
-
United States
-
Automation Machinery Manufacturing
-
700 & Above Employee
-
Quality Manager
-
Mar 2018 - Jan 2020
Lead the customer product quality efforts to measure and improve product quality and reliability. Lead efforts to define customer product quality metrics and drive improvement in the measures related to customer delight throughout the Symbotic organization. Topics include; OEE, reliability, failure analysis, design validation
-
-
Supplier Quality Manager
-
Jan 2017 - Mar 2018
Implemented and drove improvement of supplier performance metric. Established a APQP process and implemented PPAP requirements for several key new designs and suppliers. Introduced procedures to support product installation including; packaging, part identification, and nonconformance reporting. Lead failure analysis, design improvement, and supplier process control improvement for industrial lift system. Lead quality efforts to establish outsourced industrial control panel production, including UL508a compliance.
-
-
Sr. Quality Engineer
-
May 2016 - Jan 2017
Drive product quality improvement in multi-discipline project teams strategically applying quality tools and methodologies. Champion reliability improvement and develop thresholds for field performance monitoring, trending and identification of improvement opportunities. Support supplier quality trending, root cause analysis, and improvement actions to achieve organization goals. Support design and process validation, and product qualification.
-
-
-
Brooks Automation
-
United States
-
Semiconductor Manufacturing
-
700 & Above Employee
-
Senior Quality Engineer
-
May 2012 - May 2016
Leadership role improving product quality, increasing customer satisfaction and driving continuous improvement on assigned product lines. Achieved 30% improvement on atmospheric robotics product line field performance in failure rates and warranty costs. Lead failure analysis process improvements reducing backlog and cycle time. •Managed team of quality and test engineering personnel. Leadership role improving product quality, increasing customer satisfaction and driving continuous improvement on assigned product lines. Achieved 30% improvement on atmospheric robotics product line field performance in failure rates and warranty costs. Lead failure analysis process improvements reducing backlog and cycle time. •Managed team of quality and test engineering personnel.
-
-
-
Amazon Fulfillment Technologies & Robotics
-
United States
-
Software Development
-
700 & Above Employee
-
Manufacturing Quality Manager
-
Jan 2011 - May 2012
Responsible for product and process quality implementing quality systems, and process improvements. Equipped and organized new manufacturing facility, including developing ISO9001 complaint processes. Implemented key quality processes and metrics; supplier quality, and field failure tracking metrics. Improved product reliability through supplier process controls and implemented ESD standards and procedures. Responsible for product and process quality implementing quality systems, and process improvements. Equipped and organized new manufacturing facility, including developing ISO9001 complaint processes. Implemented key quality processes and metrics; supplier quality, and field failure tracking metrics. Improved product reliability through supplier process controls and implemented ESD standards and procedures.
-
-
-
Biotage - Environmental, Food and Agriculture
-
Sweden
-
Environmental Services
-
1 - 100 Employee
-
Customer Success/Quality Assurance Manager
-
Jul 2008 - Jan 2011
Implemented ISO 9001:2008 compliant quality management system; Product regulatory compliance, field product quality improvement, and supplier quality. Service Dept. manager for aftermarket instrument repairs and maintenance services, EH&S officer implementing employee safety and environmental compliance procedures. Implemented ISO 9001:2008 compliant quality management system; Product regulatory compliance, field product quality improvement, and supplier quality. Service Dept. manager for aftermarket instrument repairs and maintenance services, EH&S officer implementing employee safety and environmental compliance procedures.
-
-
-
-
Quality Assurance Manager
-
Jan 2008 - Jun 2008
Manager the strategic and tactical performance of the business quality management systems, Quality Assurance department, product release, document control and customer relations. Manager the strategic and tactical performance of the business quality management systems, Quality Assurance department, product release, document control and customer relations.
-
-
-
Edwards Vacuum
-
United Kingdom
-
Semiconductor Manufacturing
-
700 & Above Employee
-
Division Quality Manager
-
1993 - 2007
Developed and managed the quality management systems for manufacturing and service facilities, customer service, and distribution. Achieved ISO 9001:2000 certification for USA Sales and Service facilities. Liason to customer for quality performance and improvement. Directed Kaizen process improvement program and product improvement efforts. Managed the Quality and Safety organizations of 3 to 6 employees. Developed and managed the quality management systems for manufacturing and service facilities, customer service, and distribution. Achieved ISO 9001:2000 certification for USA Sales and Service facilities. Liason to customer for quality performance and improvement. Directed Kaizen process improvement program and product improvement efforts. Managed the Quality and Safety organizations of 3 to 6 employees.
-
-
Education
-
University of New Haven
MBA, General Management/Operations -
University of Massachusetts Amherst
BS, Mechanical Engineering
Community
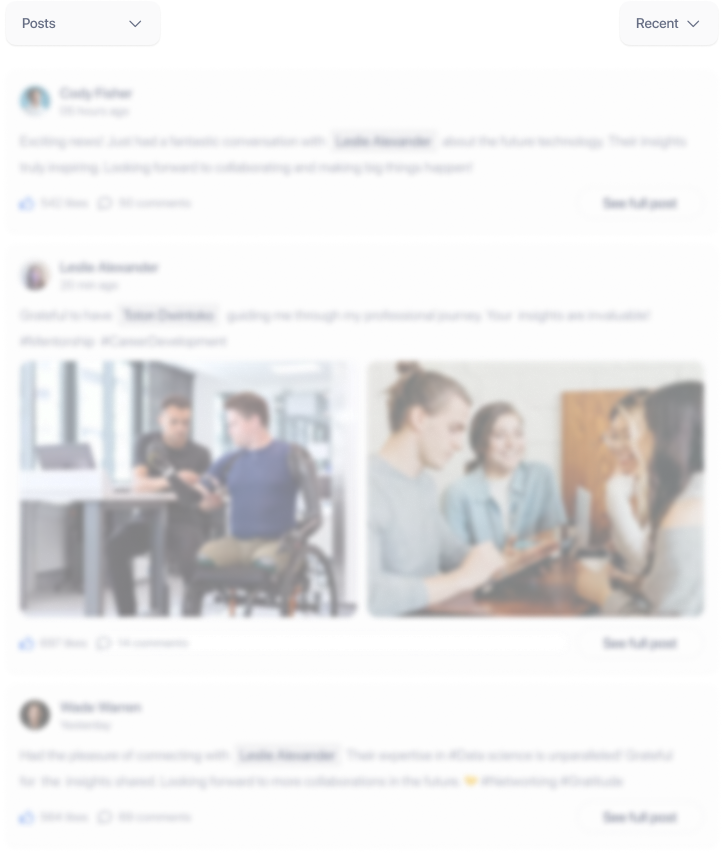