Thomas J. Landusky II
Principal Consultant at Infoverity- Claim this Profile
Click to upgrade to our gold package
for the full feature experience.
Topline Score
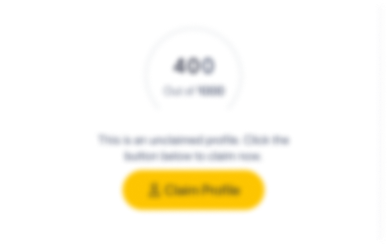
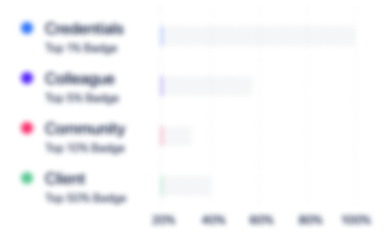
Bio

Pamela Farr
It is my pleasure to recommend Thomas Landusky. I worked with Thomas at AkzoNobel, Strongsville Ohio Site, for approximately one year. Thomas was AkzoNobel Packaging Coatings North America Technology Solutions Manager. His main job role was facilitating product development (Stage Gate Process) though the use of formulation and ERP software. He also initiated the framework to implement an integrated procedure system at the site. I found Thomas to be a talented, self-starter who can drive change and continuous improvements. Thomas would be an asset to any company.

Pamela Farr
It is my pleasure to recommend Thomas Landusky. I worked with Thomas at AkzoNobel, Strongsville Ohio Site, for approximately one year. Thomas was AkzoNobel Packaging Coatings North America Technology Solutions Manager. His main job role was facilitating product development (Stage Gate Process) though the use of formulation and ERP software. He also initiated the framework to implement an integrated procedure system at the site. I found Thomas to be a talented, self-starter who can drive change and continuous improvements. Thomas would be an asset to any company.

Pamela Farr
It is my pleasure to recommend Thomas Landusky. I worked with Thomas at AkzoNobel, Strongsville Ohio Site, for approximately one year. Thomas was AkzoNobel Packaging Coatings North America Technology Solutions Manager. His main job role was facilitating product development (Stage Gate Process) though the use of formulation and ERP software. He also initiated the framework to implement an integrated procedure system at the site. I found Thomas to be a talented, self-starter who can drive change and continuous improvements. Thomas would be an asset to any company.

Pamela Farr
It is my pleasure to recommend Thomas Landusky. I worked with Thomas at AkzoNobel, Strongsville Ohio Site, for approximately one year. Thomas was AkzoNobel Packaging Coatings North America Technology Solutions Manager. His main job role was facilitating product development (Stage Gate Process) though the use of formulation and ERP software. He also initiated the framework to implement an integrated procedure system at the site. I found Thomas to be a talented, self-starter who can drive change and continuous improvements. Thomas would be an asset to any company.

Credentials
-
Lean Six Sigma Black Belt (ICBB)
International Association for Six Sigma CertificationNov, 2020- Nov, 2024
Experience
-
Infoverity
-
United States
-
Information Services
-
100 - 200 Employee
-
Principal Consultant
-
Jun 2022 - Present
-
-
Senior Consultant
-
Mar 2020 - Jun 2022
Delivered data governance and master data management strategy and implementation to clients. Developed and implemented internal standards and systems. • Delivered over $500,000 in revenue. • Key project roles included: o Senior Data Governance Analyst o Senior MDM Analyst o STEP Solution Delivery Manager • Co-founded Infoverity’s Culture Committee and led design of new knowledge management software.
-
-
-
Performance Health
-
United States
-
Wellness and Fitness Services
-
200 - 300 Employee
-
Manager, Data Governance
-
Oct 2017 - Mar 2020
Reported directly to Chief Information Officer (formerly Chief Operations Officer). Built department from the ground up. Established global standards for master data and ERP management with international team members. • Defined and implemented all aspects of department construction including vision and strategy, roles and responsibilities, metrics, budgets, employee evaluation and development planning, and managing overall day-to-day staff activity and project… Show more Reported directly to Chief Information Officer (formerly Chief Operations Officer). Built department from the ground up. Established global standards for master data and ERP management with international team members. • Defined and implemented all aspects of department construction including vision and strategy, roles and responsibilities, metrics, budgets, employee evaluation and development planning, and managing overall day-to-day staff activity and project priorities. • Developed a team responsible for item and vendor setup, data maintenance, and business process management. • Streamlined item setup process from 12 weeks to under 4 weeks with added functional improvements and without additional cost. • Expanded management of GS1 accounts and Global Trade Item Number (GTIN) allocation at the enterprise level. Expanded support of global regulatory, sourcing, and packaging teams with barcode and labeling expertise. Show less Reported directly to Chief Information Officer (formerly Chief Operations Officer). Built department from the ground up. Established global standards for master data and ERP management with international team members. • Defined and implemented all aspects of department construction including vision and strategy, roles and responsibilities, metrics, budgets, employee evaluation and development planning, and managing overall day-to-day staff activity and project… Show more Reported directly to Chief Information Officer (formerly Chief Operations Officer). Built department from the ground up. Established global standards for master data and ERP management with international team members. • Defined and implemented all aspects of department construction including vision and strategy, roles and responsibilities, metrics, budgets, employee evaluation and development planning, and managing overall day-to-day staff activity and project priorities. • Developed a team responsible for item and vendor setup, data maintenance, and business process management. • Streamlined item setup process from 12 weeks to under 4 weeks with added functional improvements and without additional cost. • Expanded management of GS1 accounts and Global Trade Item Number (GTIN) allocation at the enterprise level. Expanded support of global regulatory, sourcing, and packaging teams with barcode and labeling expertise. Show less
-
-
-
The Hygenic Corporation
-
United States
-
Chemical Manufacturing
-
1 - 100 Employee
-
Sourcing Engineer
-
Sep 2014 - Sep 2017
The Hygenic Corporation merged with Performance Health in 2016. Executed global package design and specifications through procurement, qualification, process improvement, and technical writing. • Sourced, qualified, and tested primary, secondary, and tertiary packaging components for: o Development of new products o Enhancements and cost-savings for existing products o Retail Point of Purchase (POP) displays o E-commerce packaging • Authored and improved over… Show more The Hygenic Corporation merged with Performance Health in 2016. Executed global package design and specifications through procurement, qualification, process improvement, and technical writing. • Sourced, qualified, and tested primary, secondary, and tertiary packaging components for: o Development of new products o Enhancements and cost-savings for existing products o Retail Point of Purchase (POP) displays o E-commerce packaging • Authored and improved over 1,000 process and product documents including standard operating procedures, manufacturing instructions, and component and finished goods specifications. • Managed corporate GS1 accounts and supported business with Global Trade Item Number (GTIN) assignment and barcode expertise for Unique Device Identification (UDI) and scannable National Drug Code (NDC) requirements and implementation. Show less The Hygenic Corporation merged with Performance Health in 2016. Executed global package design and specifications through procurement, qualification, process improvement, and technical writing. • Sourced, qualified, and tested primary, secondary, and tertiary packaging components for: o Development of new products o Enhancements and cost-savings for existing products o Retail Point of Purchase (POP) displays o E-commerce packaging • Authored and improved over… Show more The Hygenic Corporation merged with Performance Health in 2016. Executed global package design and specifications through procurement, qualification, process improvement, and technical writing. • Sourced, qualified, and tested primary, secondary, and tertiary packaging components for: o Development of new products o Enhancements and cost-savings for existing products o Retail Point of Purchase (POP) displays o E-commerce packaging • Authored and improved over 1,000 process and product documents including standard operating procedures, manufacturing instructions, and component and finished goods specifications. • Managed corporate GS1 accounts and supported business with Global Trade Item Number (GTIN) assignment and barcode expertise for Unique Device Identification (UDI) and scannable National Drug Code (NDC) requirements and implementation. Show less
-
-
-
Sherwood Valve
-
United States
-
Chemical Manufacturing
-
1 - 100 Employee
-
Quality Engineer
-
Dec 2013 - Jul 2014
Provided support to Quality Department on internal and external quality issues and continuous improvement initiatives through root cause analysis, corrective action reports, material variance reports, verifications, validations, audits, and quality system documentation maintenance. • Supported capital equipment implementation through verifications and validations, including data collection, analysis, and reporting, improving production efficiency and efficacy. • Investigated… Show more Provided support to Quality Department on internal and external quality issues and continuous improvement initiatives through root cause analysis, corrective action reports, material variance reports, verifications, validations, audits, and quality system documentation maintenance. • Supported capital equipment implementation through verifications and validations, including data collection, analysis, and reporting, improving production efficiency and efficacy. • Investigated customer product returns and internal material variances by participating in root cause analysis and corrective action teams, improving customer relations and quality control. • Maintained ISO 9001 standards and ensured in-house and vendor quality by conducting internal and supplier audits through evaluating products, processes, and quality systems. Show less Provided support to Quality Department on internal and external quality issues and continuous improvement initiatives through root cause analysis, corrective action reports, material variance reports, verifications, validations, audits, and quality system documentation maintenance. • Supported capital equipment implementation through verifications and validations, including data collection, analysis, and reporting, improving production efficiency and efficacy. • Investigated… Show more Provided support to Quality Department on internal and external quality issues and continuous improvement initiatives through root cause analysis, corrective action reports, material variance reports, verifications, validations, audits, and quality system documentation maintenance. • Supported capital equipment implementation through verifications and validations, including data collection, analysis, and reporting, improving production efficiency and efficacy. • Investigated customer product returns and internal material variances by participating in root cause analysis and corrective action teams, improving customer relations and quality control. • Maintained ISO 9001 standards and ensured in-house and vendor quality by conducting internal and supplier audits through evaluating products, processes, and quality systems. Show less
-
-
-
AkzoNobel
-
Netherlands
-
Chemical Manufacturing
-
700 & Above Employee
-
Technology Solutions Engineer
-
Apr 2013 - Dec 2013
Facilitated product development through use of SAP and formulation software Product Vision. • Improved workplace productivity and efficiency by implementing and managing chemical inventory system, ChemSW. • Provided necessary clarity and consistency for future quality policy development through technical writing, including manufacturing engineering procedures and business protocols. • Implemented 5S practices site-wide, creating a safer and more efficient work environment. Facilitated product development through use of SAP and formulation software Product Vision. • Improved workplace productivity and efficiency by implementing and managing chemical inventory system, ChemSW. • Provided necessary clarity and consistency for future quality policy development through technical writing, including manufacturing engineering procedures and business protocols. • Implemented 5S practices site-wide, creating a safer and more efficient work environment.
-
-
-
-
Engineering Intern
-
2011 - 2013
Advised CEO and Research and Development team on new product design, as well as enhanced documentation and process controls. Translated customer needs into engineering requirements and technical specifications. Advised CEO and Research and Development team on new product design, as well as enhanced documentation and process controls. Translated customer needs into engineering requirements and technical specifications.
-
-
Education
-
Case Western Reserve University
Bachelor's degree, Biomedical Engineering
Community
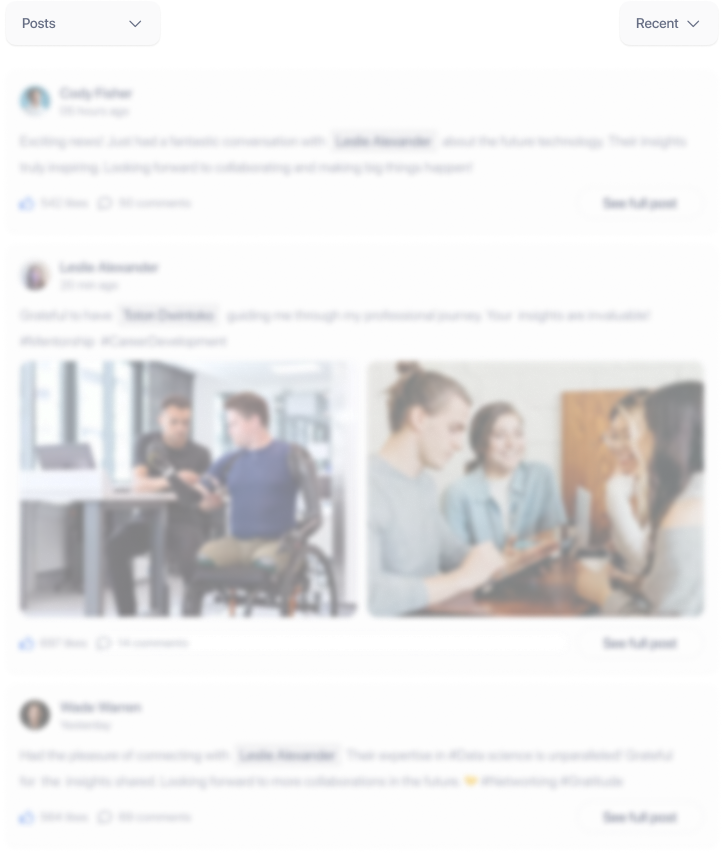