Angelique Reed, MBA
Supply Chain Optimization Sr. Director at GOJO Industries- Claim this Profile
Click to upgrade to our gold package
for the full feature experience.
Topline Score
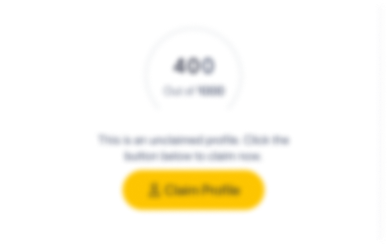
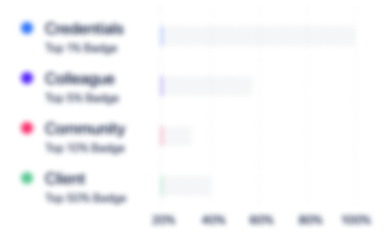
Bio

LinkedIn User
It was my honor to work for Angie for my co-op at Bendix. Angie was not only my direct manager, but she was also more like a career mentor to me. I learned a tremendous amount from her and it is safe to say that she is my professional role model. She is a natural leader and fast learner who knows a lot and is very good at what she's doing.

Alejandra Conner
Angelique is an individual any organization wants on their team. She is detail oriented and understands the big picture. In her role as the business lead for warehouse management, Angelique used her knowledge, experience and skills in SAP to improve and support multiple plant locations. She quickly became and remains a great asset on the team. I hope I get the chance to work with her again.

LinkedIn User
It was my honor to work for Angie for my co-op at Bendix. Angie was not only my direct manager, but she was also more like a career mentor to me. I learned a tremendous amount from her and it is safe to say that she is my professional role model. She is a natural leader and fast learner who knows a lot and is very good at what she's doing.

Alejandra Conner
Angelique is an individual any organization wants on their team. She is detail oriented and understands the big picture. In her role as the business lead for warehouse management, Angelique used her knowledge, experience and skills in SAP to improve and support multiple plant locations. She quickly became and remains a great asset on the team. I hope I get the chance to work with her again.

LinkedIn User
It was my honor to work for Angie for my co-op at Bendix. Angie was not only my direct manager, but she was also more like a career mentor to me. I learned a tremendous amount from her and it is safe to say that she is my professional role model. She is a natural leader and fast learner who knows a lot and is very good at what she's doing.

Alejandra Conner
Angelique is an individual any organization wants on their team. She is detail oriented and understands the big picture. In her role as the business lead for warehouse management, Angelique used her knowledge, experience and skills in SAP to improve and support multiple plant locations. She quickly became and remains a great asset on the team. I hope I get the chance to work with her again.

LinkedIn User
It was my honor to work for Angie for my co-op at Bendix. Angie was not only my direct manager, but she was also more like a career mentor to me. I learned a tremendous amount from her and it is safe to say that she is my professional role model. She is a natural leader and fast learner who knows a lot and is very good at what she's doing.

Alejandra Conner
Angelique is an individual any organization wants on their team. She is detail oriented and understands the big picture. In her role as the business lead for warehouse management, Angelique used her knowledge, experience and skills in SAP to improve and support multiple plant locations. She quickly became and remains a great asset on the team. I hope I get the chance to work with her again.

Experience
-
GOJO, Makers of PURELL
-
United States
-
Manufacturing
-
700 & Above Employee
-
Supply Chain Optimization Sr. Director
-
Jun 2020 - Present
-
-
Director of Strategic Planning
-
Dec 2018 - Jun 2020
-
-
Director Of Warehouse Operations
-
Dec 2017 - Dec 2018
-
-
Supply Chain Strategic Network Director
-
Jul 2017 - Dec 2017
-
-
Supply Chain Strategic Network Manager
-
Apr 2017 - Jul 2017
-
-
Operational Excellence Analysis Manager
-
Jul 2015 - Apr 2017
-
-
-
Bendix Commercial Vehicle Systems LLC
-
United States
-
Truck Transportation
-
700 & Above Employee
-
Corporate Materials and Logistics Manager
-
Apr 2014 - Aug 2015
- Continue to manage all responsibilities listed below under Corporate Logistics Manager.- Harmonize, optimize and ensure all supplier and production planning processes are being adhered to across North America.- Ensure supplier communication tool (e-Ventus) is working properly and all end users are trained on how to use the tool.- Manage end of life and obsolescence (E&O) process to ensure materials on hand are those that are required for business.- Responsible for delivery metrics of all supplier deliveries and intercompany transfers.
-
-
Logistics Manager
-
Jun 2012 - Oct 2014
- Responsible for managing company wide transportation, distribution, and warehouse logistics processes and strategies across the business. Includes activities relatedto all inbound and outbound traffic modes, utilizing a third party transportation provider. - Ensures compliance to all trade regulations including import/export customs compliance. - Manages and optimizes distribution processes and strategies across the business. - Provides general logistics support to the business, including direct responsibility for the packaging function.- Material Logistics Pillar Owner for KPS Activities- Manages relationships with third party logisticscompanies which provide services in the areas of transportation, freight bill audit and payment, and customs compliance and related services. - Supports regional distribution centers to optimize operational performance, especially in the areas of delivery and inventory.
-
-
Logistics and Warehouse Module Lead
-
Jun 2008 - Aug 2012
- System responsibilities include: SAP Warehouse Management (IM and WM), Bar Coding/ RF Utilization, Receiving, Physical Inventory, Cycle Counting, Consignment, Stock transfers and placements.- Design SAP system to meet internal and external customer needs for business processes.- Manage module specific continuous improvement processes for all facilities.- Coach and train key users in key functionality of the Warehouse Management Module for all facilities.- Assisted in Release Upgrade from SAP R/3 4.7 to SAP ECC 6.0- Lead Third Party Warehousing Transition and redesign resulting in a 35% picking efficiency gain.- Managed material reorganization project to accommodate business growth o Worked with contractors to increase racking capacity and provide a safer more consistent workplace. o Resulted in a 40% increase in material capacity and smoother material flow. o Visual management and barcodes implemented to provide quicker and more efficient picking.- Completed two Go Live Roll Outs including a physical relocation from California to Mexico. o Involving new facility layout, condensing of manufacturing lines and decrease of inventory. o Integration of a Bonded Warehouse and cross dock on the United States side.- Designed several RF screens to better accommodate business needs and be more user friendly. o Material & Bin Inquiry Screens o Confirmation and Goods Receipt Screens o Receiving Screens for both IM and WM managed facilities
-
-
-
Carquest Auto Parts
-
United States
-
Motor Vehicle Manufacturing
-
700 & Above Employee
-
Warehouse Manager
-
Jul 2007 - Jun 2008
- Increased picking production by 13%- Oversee all actions within the returns, stocking, picking and shipping departments.- Manage a fleet of 13 CDL drivers and maintained all necessary files for OSHA and DOT.- Supervise personnel including hiring, determining workload, delegating assignments, training, monitoring, evaluating performance and initiating corrective counseling and disciplinary actions.- Motivate, organize and encourage all teammates within the workforce to ensure productivity is met.- Test new hardware and software releases for any problems that may exist and report back accordingly.- Train associates at the Distribution Centers across the US as the WMS System was implemented.
-
-
Stocking Supervisor
-
Sep 2006 - Jul 2007
- Managed and provides direction of processes in regards to all replenishment of product in the Facility.- Maintained the active picking locations Inventory accurately at all times.- Hired and trained staff on Stocking/Replenishment and Cycle Count Process within their area of responsibility.- Assisted in training of warehouse associates going live on our new Warehouse Management System (WMS-HighJump) as well as assisting in training warehouse associates gained thru acquisitions and mergers.
-
-
Office/Customer Service Manager
-
Aug 2003 - Sep 2006
- Reduced office personnel by three individuals while still maintaining customer service levels.- Hire, orient, train, supervise, evaluate, motivate, communicate with, lead and discipline all direct reports.- Responsible for associate payroll, proper billings of customers, bank deposits, oversee all Accounts. Receivable, Accounts Payables and Pack Entry (receiving of inventory) activities.Administers distribution of all catalogs, communications and sales related materials.- Maximizing customer service needs in a timely and efficient manner while minimizing cost to the Facility.- Assisedt in training for office associates gained thru acquisitions and mergers.- Aided in the implementation and development of Carquest Vision- a direct ordering software program.
-
-
-
DRB
-
Software Development
-
200 - 300 Employee
-
Installer
-
2002 - 2003
-
-
Education
-
The University of Akron
MBA, Supply Chain Management -
The University of Akron
Bachelor of Science (BS), Supply Chain Management -
The University of Akron
Bachelor of Science (BS), Operations Mangement -
The University of Akron
Minor, Management Information Systems, General
Community
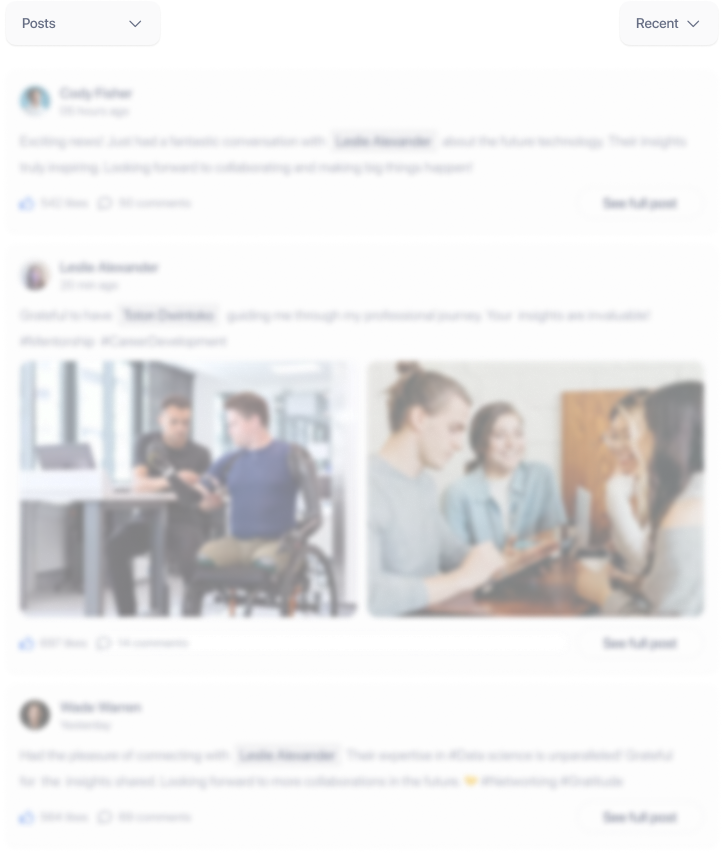