Fábio Cardoso Alves
Principal at STAUFEN.Táktica- Claim this Profile
Click to upgrade to our gold package
for the full feature experience.
-
English -
-
Spanish -
Topline Score
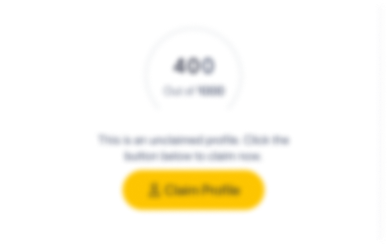
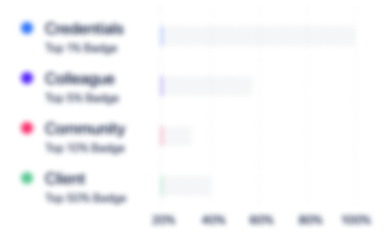
Bio

Marcio Melo, LSSBB, PMP
Fábio é detalhista e equilibrado. Conduz reuniões de planejamento de maneira eficiente, resultando em uma reunião objetiva e eficaz para o negócio. É um líder e um excelente intermediador na resolução de conflitos. Preparado para mudanças quando essas se apresentam no meio do projeto, adaptando-se de modo coerente.

Igor Lopes
Fábio is a results-oriented professional, with great knowledge of Lean Manufacturing and how to apply the tools in several types of manufacturing. He is also an expert in teams and projects coordination, focusing to achieve the targets established.

Marcio Melo, LSSBB, PMP
Fábio é detalhista e equilibrado. Conduz reuniões de planejamento de maneira eficiente, resultando em uma reunião objetiva e eficaz para o negócio. É um líder e um excelente intermediador na resolução de conflitos. Preparado para mudanças quando essas se apresentam no meio do projeto, adaptando-se de modo coerente.

Igor Lopes
Fábio is a results-oriented professional, with great knowledge of Lean Manufacturing and how to apply the tools in several types of manufacturing. He is also an expert in teams and projects coordination, focusing to achieve the targets established.

Marcio Melo, LSSBB, PMP
Fábio é detalhista e equilibrado. Conduz reuniões de planejamento de maneira eficiente, resultando em uma reunião objetiva e eficaz para o negócio. É um líder e um excelente intermediador na resolução de conflitos. Preparado para mudanças quando essas se apresentam no meio do projeto, adaptando-se de modo coerente.

Igor Lopes
Fábio is a results-oriented professional, with great knowledge of Lean Manufacturing and how to apply the tools in several types of manufacturing. He is also an expert in teams and projects coordination, focusing to achieve the targets established.

Marcio Melo, LSSBB, PMP
Fábio é detalhista e equilibrado. Conduz reuniões de planejamento de maneira eficiente, resultando em uma reunião objetiva e eficaz para o negócio. É um líder e um excelente intermediador na resolução de conflitos. Preparado para mudanças quando essas se apresentam no meio do projeto, adaptando-se de modo coerente.

Igor Lopes
Fábio is a results-oriented professional, with great knowledge of Lean Manufacturing and how to apply the tools in several types of manufacturing. He is also an expert in teams and projects coordination, focusing to achieve the targets established.

Credentials
-
Certified in Production and Inventory Management - CPIM | APICS
APICSJul, 2011- Nov, 2024
Experience
-
STAUFEN.Táktica
-
Brazil
-
Business Consulting and Services
-
1 - 100 Employee
-
Principal
-
Jan 2023 - Present
-
-
-
Kimia Consultoria
-
Campinas Area, Brazil
-
Founder and Director
-
Feb 2013 - Dec 2022
Kimia Consulting connects the customer strategy into its operations through an innovative proposal to solve administrative and manufacturing problems. Kimia leads the customer towards operational excellence journey by sistematically eliminating wastes in its value chain. Main features of our value proposition: - Structured work plan to get stakeholders expectations aligned - High participation from people since diagnosis stage - Show weekly gains along project - Simultaneous implementation at office and manufacturing environment Kimia provides high impact soluctions by connecting the customer business to: - Lean solutions to eliminate wastes - Six sigma tools to develop robust and reliable processes - Improvement aligned with ERP - Sustainable processes supported by quality management system Show less
-
-
-
Lord Embalagens Plásticas
-
Sorocaba Area, Brazil
-
Gerente de Projeto da Kimia na Lord Embalagens
-
Feb 2013 - Aug 2015
PROJETO REALIZADO PELA KIMIA CONSULTORIA - Realização de diagnóstico amplo da operação e realização e condução de evento para que os colaboradores identifiquem oportunidades e entrem em consenso sobre a necessidade de iniciar um programa de melhoria (ver fotos dos participantes do evento e das oportunidades identificadas). - Planejamento, coaching e execução de melhorias (49 projetos em formato A3 iniciados até o momento) em áreas produtivas (Fábrica) e administrativas (projetos transacionais envolvendo os departamentos de Vendas, Análise de Crédito, Engenharia, PCP, Expedição, Recebimento, RH, TI, Controladoria, Manutenção e Qualidade). - Principais resultados entregues: redução do atraso de entrega, aumento de produtividade e redução de erros nos processos administrativos e produtivos, redução de aparas, aumento da acuracidade de inventário, redução de tempo de setup, redefinição de lotes de fabricação. Show less
-
-
-
NeoPlastic Embalagens Plásticas
-
Brazil
-
Plastics Manufacturing
-
1 - 100 Employee
-
Gerente de Projeto da Kimia na NeoPlastic
-
Feb 2013 - Jul 2015
PLANEJAMENTO E EXECUÇÃO DO PROJETO: - Em 2013 foram mapeados os processos produtivos (extrusão, impressão e acabamento, expedição) e administrativos (compras, comercial, financeiro), onde foram levantadas mais de 1000 oportunidades de melhoria - Foram realizados cerca de 80 projetos de melhorias gerenciados por meio de A3s - O projeto foi estruturada em ciclos de planejamento e execução (3 a 4 meses) - Em cada ciclo eram realizados entre 8 a 12 projetos simultâneos, com times formados com pessoas de diferentes áreas - Semanalmente os times se reunião para monitorar o progresso das ações junto aos Diretores - Ao final de cada ciclo as equipes apresentavam os resultados alcançados e estabeleciam o projeto do próximo ciclo de melhoria - Ao final do ano um evento de contabilização das melhorias foi realizado, com cerca de 70% das oportunidades levantadas no início do ano concluídas. GANHO DO PROJETO: - O projeto teve uma ganho calculado e projetado de 3 a 5 vezes o investimento. Show less
-
-
-
Dow
-
United States
-
Chemical Manufacturing
-
700 & Above Employee
-
Dow Project Leader
-
Jun 2011 - Jan 2013
-
-
-
-
Lean Consultant
-
Mar 2004 - Jul 2011
-
-
-
Dow
-
United States
-
Chemical Manufacturing
-
700 & Above Employee
-
Taktica Lean Consultant at Dow Automotive
-
Feb 2011 - Apr 2011
Acting as a consultant I directly participate in a production line new proposal concerning layout, machine, labor and material presentation. The Dow Automotive Bumper line was located in a condominium arrange close to Ford Assembly Line. Acting as a consultant I directly participate in a production line new proposal concerning layout, machine, labor and material presentation. The Dow Automotive Bumper line was located in a condominium arrange close to Ford Assembly Line.
-
-
-
Alstom Power
-
Electric Power Generation
-
700 & Above Employee
-
Taktica Lean Consultant at Alstom Brasil
-
Nov 2010 - Jan 2011
I participated in a Lean Construction Project in Dam located in Rio Grande do Sul State. The project was a in-depth analysis about different kinds of wastes during the construction phase of a Dam. The analysis ended with a set of A3s to be implemented by the Constrution Project Manager and recommendations to be considered in the start up phase by the consortium leader. I participated in a Lean Construction Project in Dam located in Rio Grande do Sul State. The project was a in-depth analysis about different kinds of wastes during the construction phase of a Dam. The analysis ended with a set of A3s to be implemented by the Constrution Project Manager and recommendations to be considered in the start up phase by the consortium leader.
-
-
-
Volvo Trucks
-
Sweden
-
Motor Vehicle Manufacturing
-
700 & Above Employee
-
Taktica Lean Consultant at Volvo Trucks
-
Dec 2007 - Oct 2010
-
-
-
Alstom Power
-
Electric Power Generation
-
700 & Above Employee
-
Taktica Lean Consultant at Alstom Switzerland
-
Jun 2008 - Oct 2009
-
-
Taktica Lean Consultant at Alstom Bilbao
-
May 2008 - Sep 2009
-
-
-
Bosch México
-
Mexico
-
Industrial Machinery Manufacturing
-
700 & Above Employee
-
Taktica Lean Consultant at Bosch SLP
-
Aug 2007 - Nov 2007
I implemented Lean between Bosch San Luis Potosi and its two cable speed sensor suppliers, and developed a new process to plan the unit production line based on the US finished goods warehouse consumption integrated with a visual board beside the line. A kanban board was implemented in the supplier line running according to the Bosch raw material consumption. I implemented Lean between Bosch San Luis Potosi and its two cable speed sensor suppliers, and developed a new process to plan the unit production line based on the US finished goods warehouse consumption integrated with a visual board beside the line. A kanban board was implemented in the supplier line running according to the Bosch raw material consumption.
-
-
-
3M
-
United States
-
Industrial Machinery Manufacturing
-
700 & Above Employee
-
Taktica Lean Consultant at 3M
-
Nov 2006 - Jul 2007
Coach Green Belt Leaders in their lean iniciatives at four 3M Sites (Sumaré, Ribeirão Preto, Itapetininga) and Cuno (Mairinque). Coach Green Belt Leaders in their lean iniciatives at four 3M Sites (Sumaré, Ribeirão Preto, Itapetininga) and Cuno (Mairinque).
-
-
-
Grammer AG
-
Germany
-
Automotive
-
700 & Above Employee
-
Taktica Lean Consultant at Grammer
-
Feb 2006 - Nov 2006
I coached 8 Grammer suppliers at the same time running a six months cycle of improvement, twice with different companies (Total 16). The main tools explored was Value Stream Mapping to understand the flow between the suppliers and Grammer Atibaia Unit, and pull system with kanban cards and eletronic signal to trigger the production order in the supplier side based on the customer consumption. I coached 8 Grammer suppliers at the same time running a six months cycle of improvement, twice with different companies (Total 16). The main tools explored was Value Stream Mapping to understand the flow between the suppliers and Grammer Atibaia Unit, and pull system with kanban cards and eletronic signal to trigger the production order in the supplier side based on the customer consumption.
-
-
-
Sulzer
-
Switzerland
-
Machinery Manufacturing
-
700 & Above Employee
-
Taktica Lean Consultant at Sulzer
-
Jul 2005 - Jan 2006
Lean Project in a job shop environment to: - Reduce queue time in the machining operation - Improve on time delivery - Grow shop floor efficiency Lean Project in a job shop environment to: - Reduce queue time in the machining operation - Improve on time delivery - Grow shop floor efficiency
-
-
-
Schaeffler
-
Germany
-
Manufacturing
-
700 & Above Employee
-
Taktica Lean Consultant at INA
-
Mar 2004 - Jun 2005
Lead Lean implementation at Production Unit 2 (Rolling bearings to external market) and Production Unit 15 (rolling bearing to internal Market). Follow bellow main activities done: 1) Levelling and pull systems applying eletronic kanban for internal and external customers; and 2) More than 10 Kaizen events (reduce setup time at stamping and assembly lines, continuous flow at oven process, improve quality in work cells, product availabilty at suppliers etc). Lead Lean implementation at Production Unit 2 (Rolling bearings to external market) and Production Unit 15 (rolling bearing to internal Market). Follow bellow main activities done: 1) Levelling and pull systems applying eletronic kanban for internal and external customers; and 2) More than 10 Kaizen events (reduce setup time at stamping and assembly lines, continuous flow at oven process, improve quality in work cells, product availabilty at suppliers etc).
-
-
Education
-
ISCTE Executive Education
Pós-graduação Lato Sensu - Especialização, Administração e Negócios -
Fundação Getulio Vargas
Master of Business Administration (MBA), Global Executive Program -
APICS
Certified in Production and Inventory Management (CPIM), Supply Chain and Operations Management -
Universidade Federal de São Carlos
Graduate, Industrial Engineering
Community
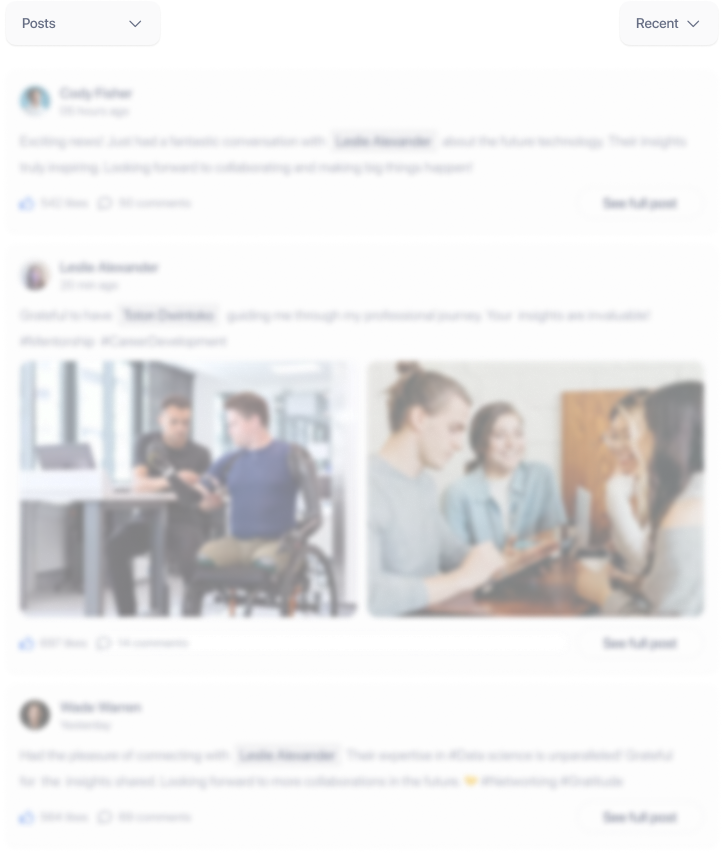