Theo Zacharatos
QRM Consultant at ValSource Inc.- Claim this Profile
Click to upgrade to our gold package
for the full feature experience.
Topline Score
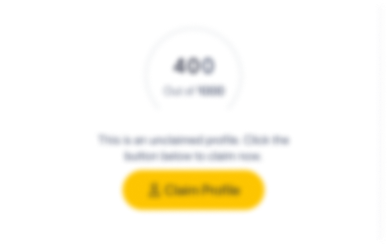
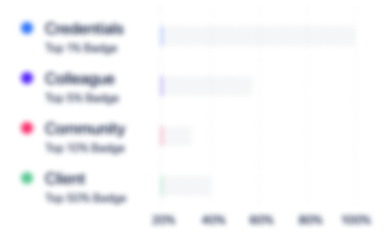
Bio

Kelly Waldron, PhD, MBA
Theo and I worked together in the Quality Risk Management space at Genzyme, where Theo was responsible for managing and developing the risk program at a key Genzyme site. His technical knowledge, leadership presence, and keen eye for improvement opportunities resulted in advances in both the site program and proactive risk culture. Theo is a pleasure to work with!

COL (Ret) Domenick A Garzone PE
Theo is an extremely intuitive and analytical scientist / engineer. He always produced high quality results under extremely difficult time frames. He is management material and has leadership qualities. He has an excellent sense of humor that takes the stress level down even under the most difficult conditions. I had the great pleasure of leading Theo for almost two years and he made my job as Investigations Manager easier because he was part of my staff. He would succeed in any pharma job at any level. He is an extremely talented individual Hire him you will not be unhappy!!

Kelly Waldron, PhD, MBA
Theo and I worked together in the Quality Risk Management space at Genzyme, where Theo was responsible for managing and developing the risk program at a key Genzyme site. His technical knowledge, leadership presence, and keen eye for improvement opportunities resulted in advances in both the site program and proactive risk culture. Theo is a pleasure to work with!

COL (Ret) Domenick A Garzone PE
Theo is an extremely intuitive and analytical scientist / engineer. He always produced high quality results under extremely difficult time frames. He is management material and has leadership qualities. He has an excellent sense of humor that takes the stress level down even under the most difficult conditions. I had the great pleasure of leading Theo for almost two years and he made my job as Investigations Manager easier because he was part of my staff. He would succeed in any pharma job at any level. He is an extremely talented individual Hire him you will not be unhappy!!

Kelly Waldron, PhD, MBA
Theo and I worked together in the Quality Risk Management space at Genzyme, where Theo was responsible for managing and developing the risk program at a key Genzyme site. His technical knowledge, leadership presence, and keen eye for improvement opportunities resulted in advances in both the site program and proactive risk culture. Theo is a pleasure to work with!

COL (Ret) Domenick A Garzone PE
Theo is an extremely intuitive and analytical scientist / engineer. He always produced high quality results under extremely difficult time frames. He is management material and has leadership qualities. He has an excellent sense of humor that takes the stress level down even under the most difficult conditions. I had the great pleasure of leading Theo for almost two years and he made my job as Investigations Manager easier because he was part of my staff. He would succeed in any pharma job at any level. He is an extremely talented individual Hire him you will not be unhappy!!

Kelly Waldron, PhD, MBA
Theo and I worked together in the Quality Risk Management space at Genzyme, where Theo was responsible for managing and developing the risk program at a key Genzyme site. His technical knowledge, leadership presence, and keen eye for improvement opportunities resulted in advances in both the site program and proactive risk culture. Theo is a pleasure to work with!

COL (Ret) Domenick A Garzone PE
Theo is an extremely intuitive and analytical scientist / engineer. He always produced high quality results under extremely difficult time frames. He is management material and has leadership qualities. He has an excellent sense of humor that takes the stress level down even under the most difficult conditions. I had the great pleasure of leading Theo for almost two years and he made my job as Investigations Manager easier because he was part of my staff. He would succeed in any pharma job at any level. He is an extremely talented individual Hire him you will not be unhappy!!

Experience
-
ValSource Inc.
-
United States
-
Pharmaceutical Manufacturing
-
100 - 200 Employee
-
QRM Consultant
-
Apr 2022 - Present
Provide consulting services for clients on their Quality Risk Management program. Ensuring the compliance of regulatory requirements and industry best practices. Provide consulting services for clients on their Quality Risk Management program. Ensuring the compliance of regulatory requirements and industry best practices.
-
-
-
Sanofi
-
France
-
Pharmaceutical Manufacturing
-
700 & Above Employee
-
Associate Director of Quality
-
May 2020 - Apr 2022
Aseptic Processing and FIll Finish quality oversite.Manage site Deviation and CAPA program. Reduced deviation cycle time. Developed training program to perform / lead investigations and root cause analysis. Human Error Prevention. Created and maintained programs to reduce deviations and human errors.Product Release. Reduce product release cycle time. Critical roles for multiple new product launches.Participation in regulatory, third part and corporate audits.Lead for creating and facilitating Quality Technical Agreement. Show less
-
-
Quality Assurance Manager
-
May 2015 - May 2020
Manage the site Deviation and CAPA programRoot Cause AnalysisHuman Error Prevention
-
-
Senior Quality Engineer
-
Jul 2012 - May 2015
Risk Management:Managed the site risk program. Performed and facilitated risk assessments. (FMEA, HACCP, Risk Based Impact Assessments, Comparison Matrix, Risk Estimation Matrix)Process Trending & Statistical Analysis (capability analysis, control limits, sample size determination, correlation analysis, hypothesis testing)Annual Product Review:Organized product review meeting. Compiled product data. Authored final report.
-
-
-
Boehringer Ingelheim
-
Germany
-
Pharmaceutical Manufacturing
-
700 & Above Employee
-
Investigation Services
-
Apr 2012 - Jul 2012
Project managed and completed investigations within aseptic filling operations. Project managed and completed investigations within aseptic filling operations.
-
-
-
Pfizer
-
United States
-
Pharmaceutical Manufacturing
-
700 & Above Employee
-
Investigations Manager
-
Jun 2009 - Aug 2011
Mentored, managed and motivated 5 direct reports to achieve above average investigation closure rates. Project managed a cross discipline team of over 13 personnel to analyze manufacturing deviations, and recommend corrective and preventive actions. Led multiple business teams to prepare, and participate, in third party and regulatory (FDA, EMEA) audits and responses.On time investigation closure rates. Quality of investigations were consistently measured above 90%. This allowed for a reduction of product cycle time by 15%.Continuously collected, analyzed and utilized data to achieve a 60% reduction in the average weekly investigation initiation rate.Implemented proper corrective actions (CAPA) that achieved a 27% reduction in deviation-per-batch. Trained and mentored 7 new investigators to ensure a culture and commitment to quality, data driven solutions, independent risk assessments and collaborative solutions.100% of audit related commitments and investigations were completed on time. Show less
-
-
Lead Investigator
-
Jun 2006 - Jun 2009
Completed manufacturing investigations within Fermentation, Clarification and Purification processing areas. Managed collaborative troubleshooting efforts with quality personnel, production personnel and process engineers to establish a root cause, corrective action, product and process impact. Harmonization between network facilities. Participated in cross-network start-up manufacturing activities for 13v Pneumococcal Polysaccharide Production (Prevnar 13v). Completed investigations and corrected multiple engineering and process discrepancies in the sister site located in Andover, Massachusetts.Member (and department representative) of site-wide cross-departmental Corrective Action Preventative Action (CAPA) Team, where best practices and audit review topics were discussed. Trained all department personnel of discussion topics.Created, implemented and facilitated standardized troubleshooting techniques for automated Filter Integrity Testing to prevent investigations from inconsistent operator practices. Investigations related to Filter Integrity Testing were reduced by over 50%.Collaborated with the creation of Electronic Master Batch Record (eMBR). Ensured the record was 21 CFR compliant. Recommended changes to the eMBR to address known routine manufacturing compliance issues. Ranging from missing or incorrect documentation, hold time issues, incorrect weight measurements and general process events. Show less
-
-
Compliance Specialist III
-
Oct 2004 - Jun 2006
Tasked to establish a change-in-culture within the Technology (Validation) department. Conducted routine audits, authored standard operating procedures, write investigations and enforced compliant practices.Performed routine audits.Authored multiple Standard Operating Procedures.Created an efficient instrument and equipment inventory management and distribution system to manage and track over 300 devices. The traceability of the devices allowed for Out-of-Tolerance (OOT) investigations to be completed within a 10 day period instead of a 30 day period. The inventory management system virtually eliminated investigations related to lost devices.Performed cost analysis to extract numerous cost savings opportunities through equipment purchases. Show less
-
-
Lead Investigator
-
Nov 2003 - Oct 2004
Completed investigations related to equipment and instrumentation calibration, autoclaves and water systems (WFI, RO, purified water). Managed collaborative troubleshooting efforts with quality personnel, production personnel and process engineers to establish a root cause, corrective action, product and process impact.Investigated, written and facilitated closure of investigations, and implemented associated corrective actions, related to FDA 483 and Consent Decree.
-
-
Chemist
-
Oct 2002 - Nov 2003
Analytical examination of raw materials, intermediates, and final products.Created an automated inventory spreadsheet to highlight when a chemical agent expired. Prior to this, inventory was taken once a month and expired material was removed. After the system, inventory was taken once a quarter to ensure the practice of removing expired reagents was completed.Department safety representative. Trained department personnel on site wide safety initiatives.
-
-
Education
-
New York University
Bachelor of Science, Chemistry -
Stevens Institute of Technology
Bachelor of Engineering, Chemical Engineering -
New Jersey Institute of Technology
Pharmaceutical Engineering Certification Program -
SAS Global Certification Program
Base SAS programming
Community
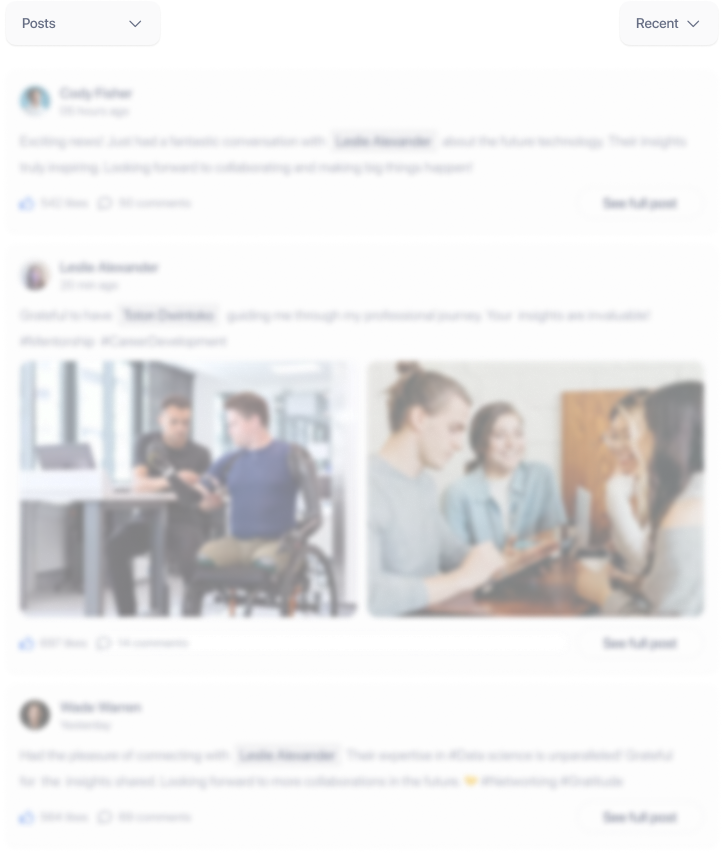