Jeff Ellis
Aftermarket Warranty Coordinator at Proterra Inc- Claim this Profile
Click to upgrade to our gold package
for the full feature experience.
Topline Score
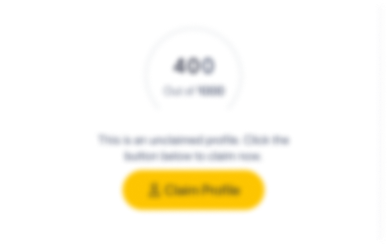
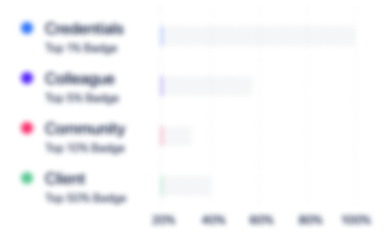
Bio


Experience
-
Proterra Inc
-
United States
-
Motor Vehicle Manufacturing
-
500 - 600 Employee
-
Aftermarket Warranty Coordinator
-
Jun 2022 - Present
Greenville-Spartanburg-Anderson, South Carolina Area Supporting warranty process of electric mass transit solutions for cities and campuses in US and Canada for the premiere manufacturer of electric buses and vehicle batteries in the United States. Leveraging Box and SmartSheet applications to create dash boards visualizing data trends helpful in making leadership level warranty and quality control decisions.
-
-
-
Rockwell Automation
-
United States
-
Automation Machinery Manufacturing
-
700 & Above Employee
-
Asset Management Leader
-
Oct 2021 - Jun 2022
Greenville, South Carolina, United States Responsible for management of Maintenance Parts Inventory for Michelin's high performance tire manufacturing center in Greenville, SC. Responsibilities include maintaining integrity of systematic to physical inventory of critical part inventories used by manufacturing machines inside the plant and coordinating timely repair work on repairable assets.
-
-
-
Formel D Group
-
Germany
-
Motor Vehicle Manufacturing
-
700 & Above Employee
-
QCC Supervisor
-
Jul 2020 - Oct 2021
Greenville-Spartanburg-Anderson, South Carolina Area Responsible for supervising quality control activity in QCC areas controlled by FormelD inside the BMW Manufacturing plant. Supervisor responsibilities include: Training quality control cage leadership team members, guiding prioritization of part processing to ensure part availability for production lines, providing coaching and disciplinary action, and administrative responsibilities. Responsible for auditing data captured by associates for accuracy, and for providing feedback to the… Show more Responsible for supervising quality control activity in QCC areas controlled by FormelD inside the BMW Manufacturing plant. Supervisor responsibilities include: Training quality control cage leadership team members, guiding prioritization of part processing to ensure part availability for production lines, providing coaching and disciplinary action, and administrative responsibilities. Responsible for auditing data captured by associates for accuracy, and for providing feedback to the management team to assist in process improvement. Tools used in daily processes include SAP, Microsoft Excel and Power Apps. Show less
-
-
-
TRIGO
-
France
-
Business Consulting and Services
-
700 & Above Employee
-
Senior Lead
-
Jan 2019 - Jul 2020
Greenville, South Carolina Area Trigo provides quality control services globally within the automotive and aerospace manufacturing industries. +Responsible for managing all aspects of operations for quality control cage on night shift including material call down, associate training, and inventory control. + Training received on drafting contractual agreements between Trigo and the engineering team on location and managing Quality Alerts in SAP
-
-
-
Trigo Enterprises LLC
-
United States
-
Automotive
-
Inventory Analyst
-
May 2018 - Dec 2018
Greenville, South Carolina (Lumbee Enterprises provides on location production line side and logistic center quality control for parts received into the BMW manufacturing facility. They are responsible for ensuring parts arriving at the production lines meet BMW’s quality standards thereby protecting the integrity of their vehicles and the productivity of their lines.) + Training received on SAP as it relates to material tracking, QN (quality notification) generation, Del Note generation, material call downs, as… Show more (Lumbee Enterprises provides on location production line side and logistic center quality control for parts received into the BMW manufacturing facility. They are responsible for ensuring parts arriving at the production lines meet BMW’s quality standards thereby protecting the integrity of their vehicles and the productivity of their lines.) + Training received on SAP as it relates to material tracking, QN (quality notification) generation, Del Note generation, material call downs, as well as other reports and research tools in support of daily operations + Leading operations in the LC06 auxiliary quality control cage through team leadership, training, and execution of SAP and Lumbee apps driven processes as related to inventory tracking, material call down, and associate hours maintenance. + Broad support of Lumbee operations have provided experience with line side operations, SKD operations, PEVL and PEVN bad parts processing, as well as Material Coordinator processes (evaluating upcoming demand and requesting parts via SAP) + Supported continued development and execution of a report used to communicate external influences on Lumbee operations to BMW counterparts + Supported efforts to reconcile physical verses system (SAP) inventory for multiple quality control locations Show less
-
-
-
-
Logistics Center Manager, Lumbee Enterprises
-
Jan 2018 - Apr 2018
Greenville, South Carolina Area + Supported improvement of Logistics Area processes which facilitate the auditing and reworking of parts supplied to the BMW production lines + Supported management of teams of 4 to 25 associates with the goals of process compliance and increasing productivity + Assisted in the development and implementation of a process used to capture and communicate external influences on logistic area operations
-
-
-
Elanders Americas
-
United States
-
Printing Services
-
1 - 100 Employee
-
Lead Project and Process Manager, Contract Accounts
-
Jan 2014 - Dec 2017
Greater Atlanta Area Responsible for leading and developing a team of two project managers in support of key contract accounts. Six years of experience successfully driving production, quality control, and order fulfillment processes in support of the BMW Greer Manufacturing Center as well as additional automotive and commercial truck clients. Trained three members of the project management team to support top earning strategic accounts. Daily participation in process improvement initiatives. Supported the… Show more Responsible for leading and developing a team of two project managers in support of key contract accounts. Six years of experience successfully driving production, quality control, and order fulfillment processes in support of the BMW Greer Manufacturing Center as well as additional automotive and commercial truck clients. Trained three members of the project management team to support top earning strategic accounts. Daily participation in process improvement initiatives. Supported the on-boarding of a new commercial truck manufacturer client requiring chassis specific content production. Responsible for 8D quality reporting in response to incidents. Show less
-
-
-
Elanders
-
Sweden
-
Transportation, Logistics, Supply Chain and Storage
-
100 - 200 Employee
-
Project and Process Manager, BMW account
-
Jan 2011 - Dec 2013
Coordinated cross functional efforts between Elanders and BMW international teams to assist in launching the BMW / Elanders Americas partnership in 2011. Planned production for over 1 million on demand manuals, over 1000 different parts. Helped develop production management processes which reduced order entry time by 60%. Recognized by client and management for exceptional customer care, and strong professional communication skills both spoken and written.
-
-
-
Lionheart Assurance Solutions, LP
-
United States
-
Insurance
-
1 - 100 Employee
-
Sales Agent (Group and CDLP Certified)
-
Apr 2010 - Dec 2010
Evaluated a career as a sales professional for legal services to the trucking Industry; investigating a potential need for a legal representation service in an industry where traffic violations could impact livelihoods. Cultivated sales and networking skills, and broadened my understanding of the commercial trucking industry.
-
-
-
Heidelberger Druckmaschinen AG
-
Germany
-
Machinery Manufacturing
-
700 & Above Employee
-
Demo Production Scheduler/ Print Media Academy (PMA) Registrar
-
Jan 2007 - Feb 2010
Heidelberg USA’s Print Media Demonstration Center (PMDC) in Kennesaw, GA was one of the largest printing technology demonstration facilities in the world. It was a critical tool for closing sales, and was used for training, service support, large customer events, and research & development. < Instrumental in the closing of approximately 125 million USD in sales annually by coordinating demonstration details for 500+ products ranging in value from $10,000 to $1,400,000+ <… Show more Heidelberg USA’s Print Media Demonstration Center (PMDC) in Kennesaw, GA was one of the largest printing technology demonstration facilities in the world. It was a critical tool for closing sales, and was used for training, service support, large customer events, and research & development. < Instrumental in the closing of approximately 125 million USD in sales annually by coordinating demonstration details for 500+ products ranging in value from $10,000 to $1,400,000+ < Partnered with sales representatives, specialists, and management to insure customer expectations were met during demonstrations < Prioritized and scheduled inbound demonstration requests to optimize the volume of activity through the demonstration facility < Reinforced company’s reputation as an industry leader by planning and populating classes for Heidelberg USA’s “Print Media Academy” < Cultivated loyal relationships with Heidelberg USA’s 20% most valued customers by being their personal concierge for DRUPA 2008 in Dusseldorf, Germany. This included pre-event communication with over 100 clients regarding travel logistics and VIP amenities. During the trade show I used German language skills to assist these clients
-
-
Assistant Demonstrator
-
Jan 2005 - Dec 2006
< Supported prepress, press, and post-press demo teams in the fulfillment of demonstrations, R&D, and PR projects < Observed print production “best practices” and was exposed to the benefits of color management and computer integrated manufacturing < Experienced production challenges that required creative thought and dedication in order to maintain deadlines.
-
-
International Trainee Member / Customer Consultant
-
Jan 2003 - Dec 2004
Held at Heidelberger Druckmaschinen AG headquarters in Germany, this exclusive program provided product and international business training in exchange for sales support on important projects. < Helped refine a script critical in communicating a major differentiating factor at the international tradeshow, DRUPA 2004, by applying my product training and ability to translate features into value < Differentiated my company at DRUPA 2004 by professionally delivering our message… Show more Held at Heidelberger Druckmaschinen AG headquarters in Germany, this exclusive program provided product and international business training in exchange for sales support on important projects. < Helped refine a script critical in communicating a major differentiating factor at the international tradeshow, DRUPA 2004, by applying my product training and ability to translate features into value < Differentiated my company at DRUPA 2004 by professionally delivering our message as a speaker. < Cultivated Heidelberg’s image in the eyes of current and prospective customers by providing tours of German headquarters and their nearby manufacturing facility < Cultivated Heidelberg’s image in the eyes of future customers by developing and delivering training on the benefits of computer integrated manufacturing to a group of international students
-
-
Digital/Full Line Direct Marketing
-
Feb 2000 - Dec 2002
Digital Direct Marketing Representative May 2001 – Dec.2002 < Formally recognized by management for telemarketing activity that drove sales and improved brand name recognition in a new market through developing my own call campaigns from available customer data, and professionally representing the company over the phone Full Line Direct Marketing Representative Feb 2000 – April 2001 < Drove sales among the existing client base by communicating a… Show more Digital Direct Marketing Representative May 2001 – Dec.2002 < Formally recognized by management for telemarketing activity that drove sales and improved brand name recognition in a new market through developing my own call campaigns from available customer data, and professionally representing the company over the phone Full Line Direct Marketing Representative Feb 2000 – April 2001 < Drove sales among the existing client base by communicating a broader product portfolio than was popularly perceived. This was accomplished through identifying pain points, discussing relevant available solutions, and qualifying candidates as potential sales leads < Cultivated an understanding of business to business sales, challenges faced by sales professionals, and the different types of print service providers found in that industry
-
-
Education
-
Clemson University
BS, Graphic Communications -
Hart County Highschool
Community
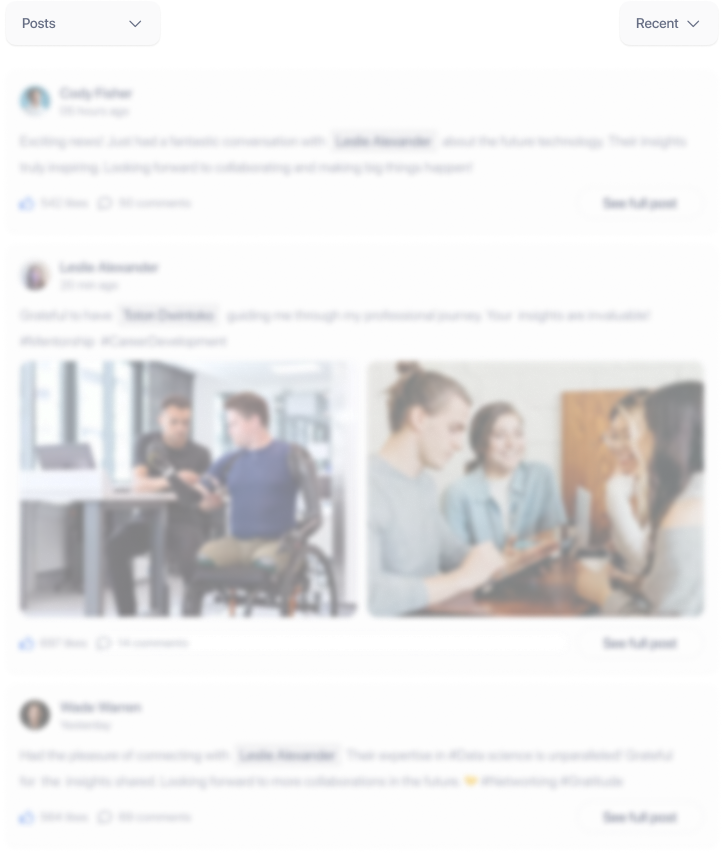