Dennis Kanupp
Vice President Operations at Atlas Precision, Inc- Claim this Profile
Click to upgrade to our gold package
for the full feature experience.
Topline Score
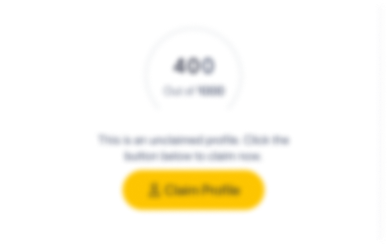
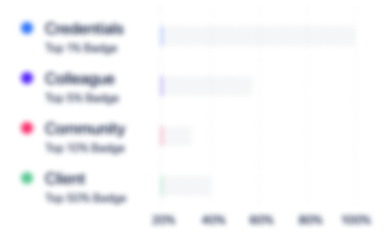
Bio

Doug Kiss
Dennis is an accomplished Operations Manager with a real knack for balancing hands-on management towards objectives and developing those who report to him. I have worked together with Dennis on lean implementation and have seen his passion first-hand. I would strongly recommend Dennis for an operational leadership role.

Doug Kiss
Dennis is an accomplished Operations Manager with a real knack for balancing hands-on management towards objectives and developing those who report to him. I have worked together with Dennis on lean implementation and have seen his passion first-hand. I would strongly recommend Dennis for an operational leadership role.

Doug Kiss
Dennis is an accomplished Operations Manager with a real knack for balancing hands-on management towards objectives and developing those who report to him. I have worked together with Dennis on lean implementation and have seen his passion first-hand. I would strongly recommend Dennis for an operational leadership role.

Doug Kiss
Dennis is an accomplished Operations Manager with a real knack for balancing hands-on management towards objectives and developing those who report to him. I have worked together with Dennis on lean implementation and have seen his passion first-hand. I would strongly recommend Dennis for an operational leadership role.

Experience
-
Atlas Precision, Inc
-
United States
-
Plastics Manufacturing
-
1 - 100 Employee
-
Vice President Operations
-
Feb 2014 - Present
-
-
-
Allegra Marketing
-
Asheville, North Carolina Area
-
VP
-
May 2019 - Jan 2020
-
-
-
Rightline Gear
-
Asheville NC
-
Chief Operations Officer at Rightline Gear , Asheville, NC
-
Feb 2019 - May 2019
Rightline Gear is committed to making products that help our customers have experiences they remember for a lifetime. Rightline Gear is located in Asheville, North Carolina where we have plenty of outdoor opportunities. It may not be official, but Asheville is definitely the car top carrier capital of the world-we like to take our gear with us. Asheville is the perfect setting for Rightline Gear’s design innovations to be developed and tested. We will continue to create new products that will provide our customers with memories for years to come. Show less
-
-
-
STERIS
-
United States
-
Medical Equipment Manufacturing
-
700 & Above Employee
-
Director of Operations at STERIS Corporation
-
Sep 2004 - Jan 2014
Directed operations in four facilities: S.C., Ohio, Puerto Rico, and Canada with focus on utilizing leadership and continuous improvement. Improved the total business from all perspectives including increasing P&L for each of the facilities during my tenure. Responsibilities included: operations, quality, financial, environmental, safety, customer service, and continuous Improvement. • Implemented Total Productive Maintenance in 15 plants across the U.S. This Project introduced and supported the TPM Culture in each of the plants. Achieved strong results with an average improvement of 5% in uptime for all critical and supporting equipment, netting $5M annually. • Led a SMED (Single Minute Exchange of Dies) event reducing change-over-time by 60 hours per month, resulting in a $1M+ gain in revenue per year. • Achieved non-conformity reduction by using problem solving and eliminating waste throughout the process. Resulted in 4% reduction annually for 4 consecutive years. • Developed visual control indicators to allow each employee to clearly understand their performance and their plant’s performance by using SQDC boards throughout the facilities. • Created a functional dashboard for all 18 plants in the network, enabling upper management to clearly see operational performance. Accomplishments:• 2007 Plant of the Year• 2007 & 11 Zone of the Year• 2008, 11, 13 Safety Champion Show less
-
-
Plant Manager
-
May 2003 - Sep 2004
As Plant Manager, promoted to Director of Operations in less than 1½ years as a result of the following accomplishments. • Lean Events: Hosted 3-day event utilizing VSM (Value Stream Mapping). This event included product movement and file flow. Achieved the following results: product movement - 23% reduction, product hand offs - 60% reduction, file movement - 76% reduction, product non-value add - 45% reduction. Resulted in a 24% reduction in total cycle time overall. Other lean tools used included Work Flow Balancing, development of Standard Work, and extensive 5S. • Developed the following teams:• New Customer Start up (Six Sigma) team: Standardized new customer integration time, resulting in 3-day reduction in cycle time from handshake agreement to revenue generation.• Kaizen Blitz team: Streamlined paperwork flow, reducing sterile load release time by 40%. Show less
-
-
-
Medical Action Industries
-
United States
-
Hospitals and Health Care
-
200 - 300 Employee
-
Director of QA and Regulatory
-
1988 - 2003
As Director of QA/RA, served as key leader, fostering $80M+ in company growth through acquisitions and continual market dominance. During my first year in this position, customer complaints were reduced by 50%. The compliance to all relevant standards had been challenged by FDA and ISO-9002/EN-46002, all yielding successful outcomes. As Director of QA/RA, served as key leader, fostering $80M+ in company growth through acquisitions and continual market dominance. During my first year in this position, customer complaints were reduced by 50%. The compliance to all relevant standards had been challenged by FDA and ISO-9002/EN-46002, all yielding successful outcomes.
-
-
Education
-
University of North Carolina Asheville
BS, Marketing
Community
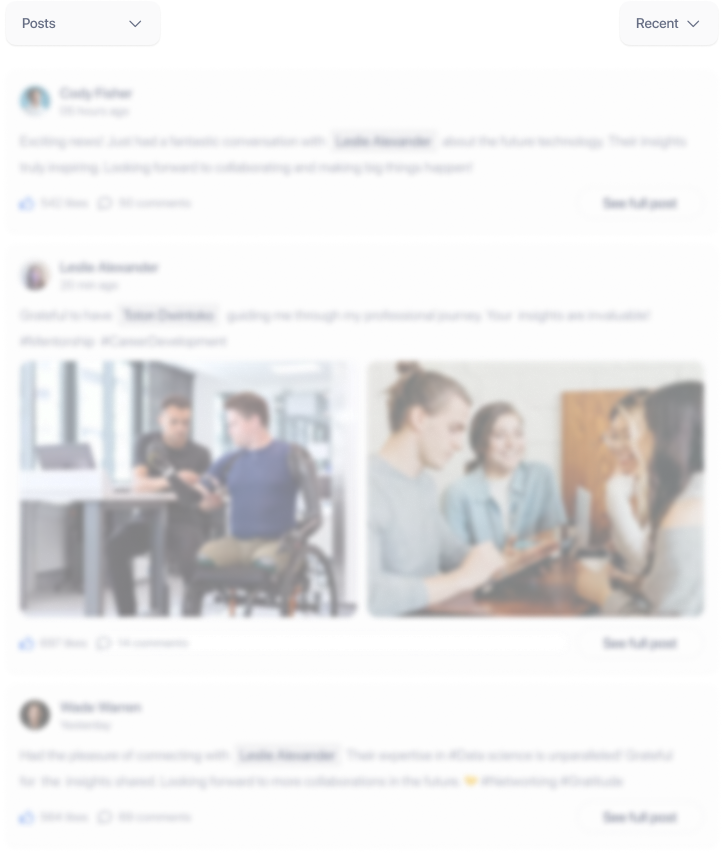