Kyle Furtado
Production Manager at Poyant- Claim this Profile
Click to upgrade to our gold package
for the full feature experience.
-
Portuguese Native or bilingual proficiency
-
English Native or bilingual proficiency
Topline Score
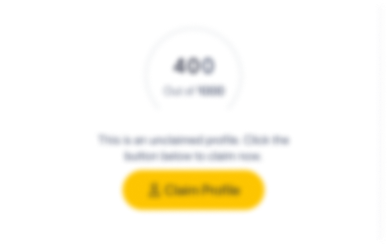
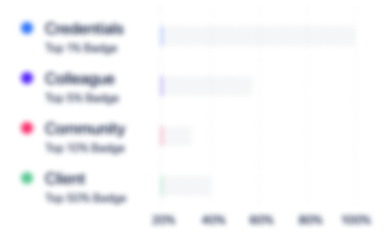
Bio


Experience
-
Poyant
-
United States
-
Advertising Services
-
1 - 100 Employee
-
Production Manager
-
Apr 2022 - Present
• Provide strong leadership, team building, organizational development, coaching and communication skills with a demonstrated ability to motivate, assess and develop employee skills.• Assemble top-performing teams by delegating and encouraging cross-departmental training with the goal of assisting employees in company growth and avoiding downtime within the production process.• Attract, hire, retain and develop employees through performance planning, goal setting, performance evaluations and continuous improvement. Developing business management goals and objectives that lead to growth and prosperity.• Foster innovation and promote continuous learning by providing formal and informal feedback on employee performance.• Set departmental objectives and Key Performance Indicators assessing ongoing performance of direct reports. Operational KPI’s include Indirect labor, Rework, Act vs. Est, and over budget reports.• Contribute to manufacturing operational strategies by providing information, analysis, and recommendations to peer group & executive management.• Maintain a custom manufacturing production schedule, made up of seven cross-functional departments. Proper utilization of the schedule allows for me to efficiently place cross-trained individuals into departments with capacity restraints or bottlenecks.• Instill and drive a lean culture by demonstrating passion for continuous improvement, minimization of waste and cost reductions.• Ensure Lean practices are utilized and sustained, such as company wide Kanban, Visual Tools, SWIS, ARCI, TPM, KPI Kaizen Events, Value Stream Mapping and Department/Work Cell Auditing Process.• Lead Management and Kaizen Teams by setting priorities and driving completion of Lean Initiatives.• Develop and implement predictive and preventative maintenance plans to reduce downtime.• Proactively promote a safe work environment through diligence in accident prevention, investigation, equipment maintenance, and policy enforcement.
-
-
Production Supervisor
-
Apr 2017 - Apr 2022
• Efficiently run day-to-day operations within the Production department. (15-25 employees)• Manage a custom manufacturing master schedule, made up of seven cross functional departments.• Communicate openly, and effectively with employees, recognizing and rewarding employees for results and goal-oriented accomplishments.• Responsible for ensuring proper levels of staffing is maintained within each department, while adhering to labor costs, overtime control, and short term and/or long-term capacity restraints.• Monitor staffing agencies to ensure that they efficiently and effectively provide needed services while staying within budgetary limitations.• Ensure all policies, procedures, practices, and operational standards are effectively communicated to the entire Operations team.• Implement employee relations programs with the objective of improving employee engagement and morale.• Ensure all inventory is maintained with agreed upon guidelines and is real time verifiable.• Facilitate and lead the Quality Standards Process to drive operational excellence. • Review all work orders released. Confirming BOMs, job costs & drawings are all correct in hopes to avoid rework.• Represent manufacturing at daily project management meetings, providing status of all jobs in WIP. (25-150+)• Avoid production delays in coordination with Specialty & Production purchaser based on inventory levels and due dates.• Contribute to the creation & implementation of best practice, Lean vision, strategy, policies, processes, and procedures to aid and improve operational performance.• Maintain weekly/monthly KPI reports including Indirect labor, Rework, Act vs. Est, and over budget reports.
-
-
Production Scheduler
-
Apr 2017 - Aug 2017
- Assist Production Supervisor on day to day tasks- Maintained and updated production schedule to maximize efficiency and customer satisfaction- Distributed work orders, change orders and rework orders among each department- Avoided production delays in coordination with Specialty & Production purchaser- Formulate departmental workflow analysis on a daily basis- Monitored indirect vs direct labor reports to flag any potential labor overages- Effectively communicate with PM's and production staff to ensure flow of information was properly distributed- Confirmed material tracking sheets to prepare for invoicing- Attended daily installation meetings, project kick-off meetings and scope review meetings.
-
-
-
Stop & Shop
-
Retail
-
700 & Above Employee
-
Head Produce Clerk
-
Sep 2006 - Apr 2017
- Train & motivate produce clerks - Quality and Inventory Control - Continuously provided exceptional customer service. - Organize and prioritize work - Product merchandising to maximize sales. - Lead in floor plan adjustments to accommodate weekly price changes. - Responsible for ordering daily merchandise. - Effectively communicate with all levels of management. - Assist numerous stores in the New England district to prepare for grand openings. - Train & motivate produce clerks - Quality and Inventory Control - Continuously provided exceptional customer service. - Organize and prioritize work - Product merchandising to maximize sales. - Lead in floor plan adjustments to accommodate weekly price changes. - Responsible for ordering daily merchandise. - Effectively communicate with all levels of management. - Assist numerous stores in the New England district to prepare for grand openings.
-
-
Education
-
University of Massachusetts Dartmouth
Bachelor's Degree, Business Administration, Management and Operations -
Bristol Community College
Associate's degree, Business Administration, Management and Operations
Community
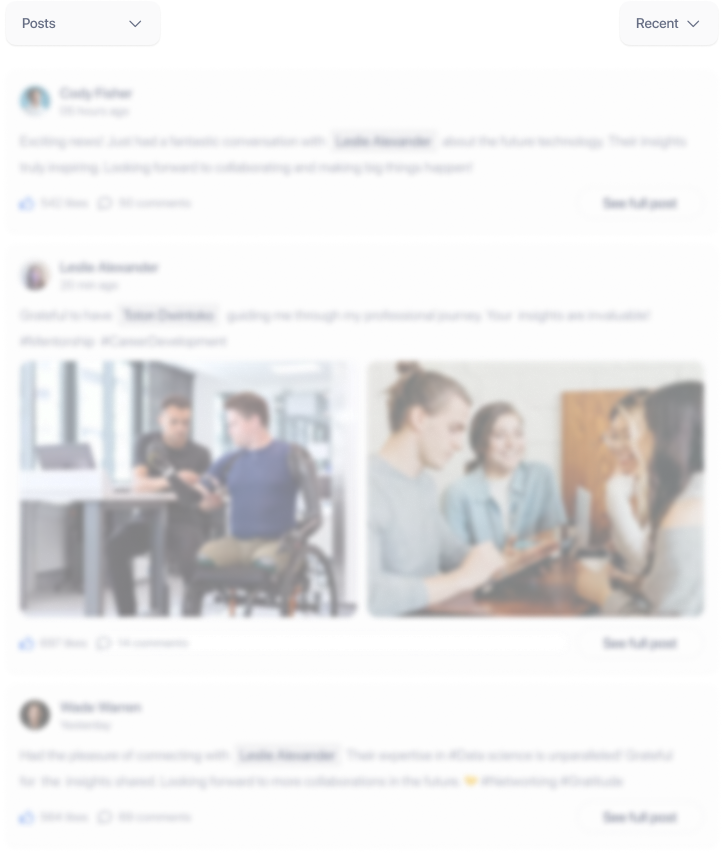