Muhammad Ghazanfar
Manager Program Management at Precision Castparts Corp., Canada- Claim this Profile
Click to upgrade to our gold package
for the full feature experience.
Topline Score
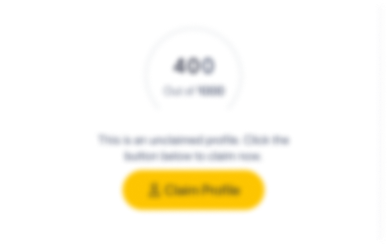
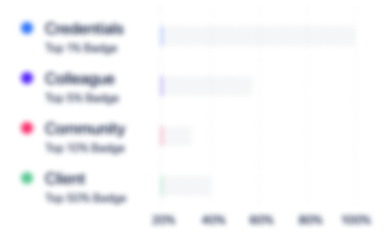
Bio


Credentials
-
The Secret: What Great Leaders Know and Do (getAbstract Summary)
LinkedInOct, 2021- Nov, 2024
Experience
-
Precision Castparts Corp., Canada
-
Canada
-
Aviation and Aerospace Component Manufacturing
-
1 - 100 Employee
-
Manager Program Management
-
Jul 2022 - Present
• Reporting to Vice President and responsible for creating professional relationships with all stakeholders; defined growth plan and successfully communicated to C-level executives. • Accountable for the full lifecycle of products and services from inception through completion, inclusive of pursuit and order capture, design and development, produce to deliver, service/support, and long-term strategic business plans. • Created a performance reporting template, achieving an 80% improvement in on time delivery through proactive identification of bottlenecks and assigning resources early to resolve. • Designed training and peer-mentoring programs for the new hires; reducing onboarding time for the new hires by 60%. • Chaired Integrated Projects Team (IPT) and had direct accountability for the Profit & Loss (P&L) for a specified group of value streams Show less
-
-
-
Collins Aerospace
-
United States
-
Aviation and Aerospace Component Manufacturing
-
700 & Above Employee
-
Operations Program Manager
-
Dec 2019 - Jul 2022
Chaired New Program Introduction (NPI) team as a business consultant and successfully secured Military program contract worth US $200M Revenue at 300% profit margin for period 2023-2027 with sufficient time to support optimal performance (quantitative).• Headed successful closure on 2 projects (Military & Commercial) in 2022 for the site with Nil excess & overages.• Communicated program health KPIs comprising of On Time Delivery (OTD), inventory control status, finance and cost, quality assurance, supply chain, cycle times, Labor productivity, risk management, and Enterprise Business Performance.• Headed Integrated Projects Team (IPT) to collaborate and optimize organizational design and to increase customer satisfaction while improving the effectiveness to available resources.• Spearheaded shop floor execution to plan by removing obstacles to success.• Fostered collaborative environment by initiating daily Gemba walks by acting as interface with cross functional IPT team. Mentored 5 employees directly resulting in improved OTD to 97%.• Standardized 'day in the life of' and 'get to know me' approach within department and coached 3 other departments and achieved desired result of improved employee satisfaction feedback by 17 points.• Established CORE (Customer Oriented Results and Excellence) within department to enable involvement with continuous improvement / lean activities through Kaizen events and resolve problems and issues through best practices, research, and analysis. Show less
-
-
Production Control Planner
-
May 2018 - Nov 2019
• Accomplished optimal shop floor execution and developed project plans through improved dispatch format and achieved desired result through recommendations and solutions of employee engagement and recovery to customer requirement date (CRD).• Supported implementation of Master Production Schedule (MPS) through consulting and providing visibility of forward-looking metrics e.g., DTM (Days to Manufacture), WIP v SWIP, and OTS (On Time Starts). • Demonstrated optimal liaison between operations, quality, engineering, procurement, supply chain, and Master Production to achieve on time delivery of 100%.• Boosted leadership trust and amplified their support in pursuit of recovery for a sensitive customer program.• Overhauled production schedules in accordance with MPS (Master Production Schedule) to expedite product through shop floor execution by developing war room and avoided customer production line stop.• Hired and led a team of 5 individuals to implement 'Value Stream Planner' approach to flow accountability from single point of contact from 'cradle to grave' to support communication among stakeholders. Show less
-
-
-
Emirates
-
United Arab Emirates
-
Airlines and Aviation
-
700 & Above Employee
-
Engineering Repairs Manager
-
Jan 2016 - Dec 2017
• Led a team of 60 R&O (repair and overhaul) professionals with a department budget of US$ 360M in a fast-paced and aggressive deadline environment.• Orchestrated department communication cadence to improve employee engagement and satisfaction.• Delegated mentorship related to package development for new hires thus saving on boarding time and money.• Set goals, annual operating policy, and goals & objectives for each individual and delegated periodic evaluation.• Established effective organizational structure according to local issues; defined business and financial plan and accountable for budget spend. Show less
-
-
Engineering Repairs Supervisor
-
Jan 2014 - Dec 2015
• Reviewed all new repair orders received, on a day-to-day basis, for their work content versus technical documentation, warranty applicability, and modification and filed, in order to facilitate monitoring and follow up.• Checked, on an ongoing basis, Nil stock / AOG requests and followed up with vendors on suitable repair arrangements to assure remedy and control.• Strengthened self-motivation through relationship-building activities and enabled compliance to department goals and objectives through weekly reporting.• Assisted repair & overhaul manager in his review of the documents and physical inspection of unserviceable components and parts. Show less
-
-
-
dnata
-
United Arab Emirates
-
Airlines and Aviation
-
700 & Above Employee
-
Line Maintenance Mechanic
-
Sep 2011 - Dec 2013
1. Performed all work activities in accordance with established laws, regulations, standards, safety protocols, and procedures to ensure safety of self and others. 2. Conducted inspections to locate damage, defects, or wear that may affect safety, reliability, or customer experience, reporting issues as appropriate. 3. Recommended replacement, repair, or modification of aircraft equipment based on inspection. 4. Reported issues, malfunctions, unusual wear, or damage to appropriate personnel, as required. 5. Tested machinery, mechanical equipment, components, and parts for defects to ensure proper functioning. 6. Installed, removed, and modified aircraft structures, systems, or components, following drawings, schematics, charts, engineering orders, and technical publications. 7. Repaired worn, defective, or damaged parts or components (e.g., seat gears, tray tables, wiring/electrical), using hand tools, gauges, and testing equipment. 8. Troubleshooted equipment and systems operation problems. 9. Interpreted discrepancies or logs (written or verbal) to understand history and nature of issue, to troubleshoot issue, and to identify required next steps (e.g., fix, defer, replace). 10. Read and interpreted technical manuals and guidelines to perform inspections, installations, repairs, or other work activities. 11. Maintained repair logs, documenting all preventative and corrective aircraft maintenance activities. 12. Interpreted and used specifications, drawings, blueprints diagrams, schematics, or flow charts to determine operational methods or sequences and to complete work activities. 13. Researched manuals, flight logs, or other technical resources to gather information needed to complete work activities. 14. Practiced safety-conscious behaviors in all operational processes and procedure. Show less
-
-
Education
-
Coventry University
Master of Business Administration - MBA, Aviation/Airway Management and Operations -
Coventry University
Bachelor of Engineering - BE, Aerospace, Aeronautical and Astronautical Engineering -
Emirates Aviation University
Higer National Diploma, Aerospace, Aeronautical and Astronautical Engineering
Community
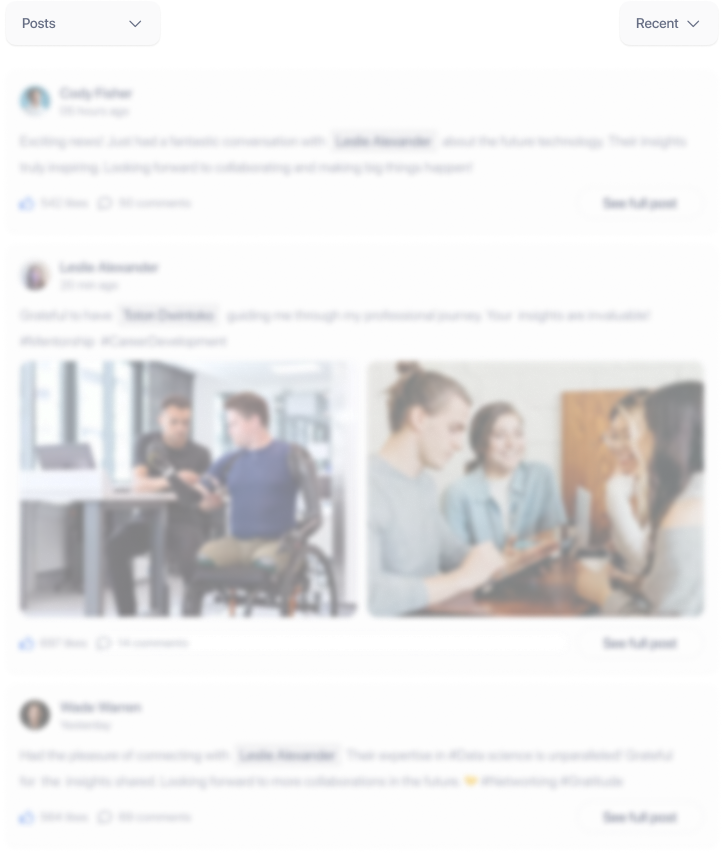