Andrea Delgado Aranza
Stock Administrator at Louis Fitzgerald Group- Claim this Profile
Click to upgrade to our gold package
for the full feature experience.
-
Spanish Native or bilingual proficiency
-
English Professional working proficiency
Topline Score
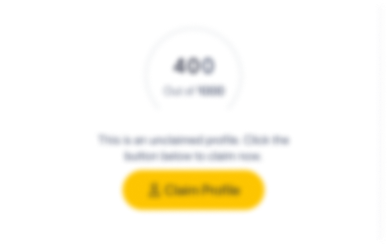
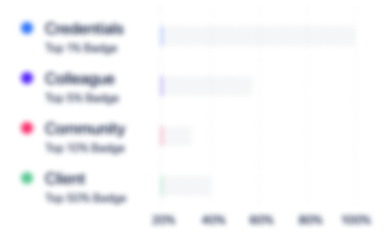
Bio


Experience
-
Louis Fitzgerald Group
-
Ireland
-
Hospitality
-
1 - 100 Employee
-
Stock Administrator
-
Mar 2023 - Present
-
-
General Employee
-
Jun 2022 - Mar 2023
Worked as waitress, hostess, runner of drinks and food. Development projects base on the data of the show to make business predictions. EPOs system management.
-
-
Chef
-
Aug 2021 - Jun 2022
Worked in 8 different restaurant of the company. Conducted training program on the required job functions and orientation with new hires in different restaurants. Worked with menu changes. Checked and ordered stock. Cooking and preparing elements of high quality dishes. Complete requisitions to replenish shortages and additional items needed. Check for status of all orders within designated timelines.
-
-
-
Press Up Hospitality Group
-
Ireland
-
Hospitality
-
300 - 400 Employee
-
Chef De Partie
-
Jul 2020 - Dec 2020
Cooking and preparing elements of high quality dishes. Implementation of strategy to deliver, take away and collection by demand of COVID. Control and improvement of delivery times to the customer and also in the kitchen. Stock control. Standardization of workstations (implementing visual aids and work instruction sheets). Quality control of the final product (Temperature, presentation and portions) Cooking and preparing elements of high quality dishes. Implementation of strategy to deliver, take away and collection by demand of COVID. Control and improvement of delivery times to the customer and also in the kitchen. Stock control. Standardization of workstations (implementing visual aids and work instruction sheets). Quality control of the final product (Temperature, presentation and portions)
-
-
-
Centra
-
Ireland
-
Retail
-
400 - 500 Employee
-
Assistant
-
Feb 2020 - Jun 2020
Check and control the stock in times of COVID. Make the daily purchase requisition. Identify the factors that affect the profits of the in-house restaurant. Standardization of supermarket-restaurant processes to streamline customer service times. Check branch standards and pre-audit to maintain annual service license Check and control the stock in times of COVID. Make the daily purchase requisition. Identify the factors that affect the profits of the in-house restaurant. Standardization of supermarket-restaurant processes to streamline customer service times. Check branch standards and pre-audit to maintain annual service license
-
-
-
Transportes Castores de Baja California
-
León, Guanajuato, Mexico
-
Engineering Project Specialist
-
Jan 2019 - Dec 2019
OEA CERTIFICATION: There was a need to obtain OEA Certification to guarantee the security and protection of information in all supply chains. I formed a multidisciplinary team to mapping of the processes in the corporate and they were validated. Then, we did audits in 4 distribution centre to verify that it complied with the certification protocols. We applied the kaizen methodology to implement the new process and protocols in the company and thus at the time of the final audit obtain the certification. REDUCE WORKLOADS: The Company was exceeding staff costs. Each of the department had to be restructured. I did a mapping of its processes, list of activities and time taking of each department by position. I analysed the obtained information to make a study of method and workloads considering the worker’s play. Changes were made to the job descriptions, department’s structure; the company operational flow was streamlined and expenses were reduced. SIRh: Many of the company processes were overloading the HR department; it had to be systematized. I did a mapping of each of the processes carried out by them, then value stream mapping were created with the entire flow of the company to identify and understand the processes that could or couldn’t be systematized. RFP was created and delivered to the IT department so it could be automated. Show less
-
-
-
Continental
-
Germany
-
Motor Vehicle Manufacturing
-
700 & Above Employee
-
Industrial Engineering Inter
-
Mar 2018 - Dec 2018
This company had several bottlenecks due to the operators’ rotation on different production lines, it needed to be standardized to reduced bottlenecks. I carried out a mapping of processes to redesign the different workstations and standardize it with new production formats. Then a study of times and movements was carried out to establish tack times. A constant cycle time was achieved in the production lines and the bottlenecks were reduced. This company had several bottlenecks due to the operators’ rotation on different production lines, it needed to be standardized to reduced bottlenecks. I carried out a mapping of processes to redesign the different workstations and standardize it with new production formats. Then a study of times and movements was carried out to establish tack times. A constant cycle time was achieved in the production lines and the bottlenecks were reduced.
-
-
-
AIESEC en México
-
Mexico
-
Non-profit Organization Management
-
300 - 400 Employee
-
Vice President Public Relations
-
Feb 2018 - Sep 2018
A contract was signed with the state government to encourage the participation of young people to take an exchange; as well as the brand was positioned in 6 of the 9 largest universities in the city, working directly with the student departments. A totally free workshop was created where the public, private and student sectors participated, achieving an attendance of 200 people. A national award was obtained for organizational development and positioning in the city.
-
-
Operations Team Lead
-
Aug 2016 - Jan 2018
A defined process, tools and response times were missing for the operation area. A study of its interaction was necessary to increase its productivity, which generated a value stream mapping of the entire operation flow. To increase the employees’ productivity, a shared tools were created among collaborator. This work was prized with a national award for highest operational growth in just one semester.
-
-
Education
-
CCT College Dublin
Higher National Diploma, Data Analytics for Business -
City Language School
Certificate, English Language and Literature/Letters -
University of Adelaide
Certificate, Project Management -
IPN UPIIG
Engineer's degree, industrial enginering -
Universidad Iberoamericana León
Certificate, Multisensory negotiation
Community
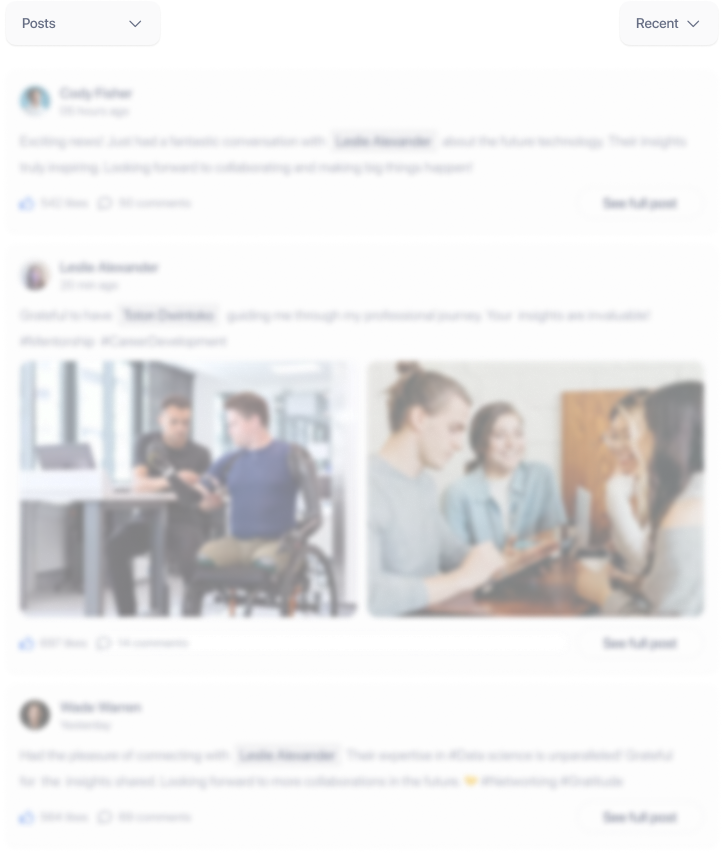