Harsh Patel
Manufacturing Engineer at Ceco Door Products- Claim this Profile
Click to upgrade to our gold package
for the full feature experience.
-
English Full professional proficiency
-
Hindi Native or bilingual proficiency
-
Gujarati Native or bilingual proficiency
-
Spanish Elementary proficiency
Topline Score
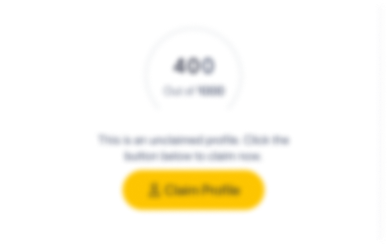
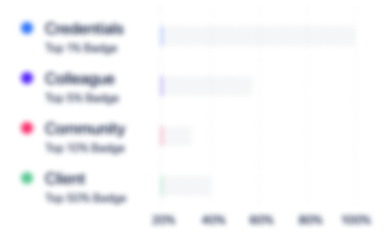
Bio

Mark Bryant
It was an absolute pleasure working with Harsh for over five years. Not only is Harsh a brilliant engineer but a leader along with one of the most pleasant demeanors I have ever encountered. Harsh is one of those unique young professionals that is destined to be a future top level leader at whatever company he is associated. Harsh is the best of the best.

LinkedIn User
If you're looking for a planner and executer, Harsh is your guy. I enjoyed working with him , and sharing the same passions for improvement, innovation, and creative solutions made it easy to work alongside him. We implemented alot of process improvements, however, more importantly we learned from our actions together. Harsh has the natural ability to encourage others and is always full of energy. Great guy to have in your corner at work and outside of work!

Mark Bryant
It was an absolute pleasure working with Harsh for over five years. Not only is Harsh a brilliant engineer but a leader along with one of the most pleasant demeanors I have ever encountered. Harsh is one of those unique young professionals that is destined to be a future top level leader at whatever company he is associated. Harsh is the best of the best.

LinkedIn User
If you're looking for a planner and executer, Harsh is your guy. I enjoyed working with him , and sharing the same passions for improvement, innovation, and creative solutions made it easy to work alongside him. We implemented alot of process improvements, however, more importantly we learned from our actions together. Harsh has the natural ability to encourage others and is always full of energy. Great guy to have in your corner at work and outside of work!

Mark Bryant
It was an absolute pleasure working with Harsh for over five years. Not only is Harsh a brilliant engineer but a leader along with one of the most pleasant demeanors I have ever encountered. Harsh is one of those unique young professionals that is destined to be a future top level leader at whatever company he is associated. Harsh is the best of the best.

LinkedIn User
If you're looking for a planner and executer, Harsh is your guy. I enjoyed working with him , and sharing the same passions for improvement, innovation, and creative solutions made it easy to work alongside him. We implemented alot of process improvements, however, more importantly we learned from our actions together. Harsh has the natural ability to encourage others and is always full of energy. Great guy to have in your corner at work and outside of work!

Mark Bryant
It was an absolute pleasure working with Harsh for over five years. Not only is Harsh a brilliant engineer but a leader along with one of the most pleasant demeanors I have ever encountered. Harsh is one of those unique young professionals that is destined to be a future top level leader at whatever company he is associated. Harsh is the best of the best.

LinkedIn User
If you're looking for a planner and executer, Harsh is your guy. I enjoyed working with him , and sharing the same passions for improvement, innovation, and creative solutions made it easy to work alongside him. We implemented alot of process improvements, however, more importantly we learned from our actions together. Harsh has the natural ability to encourage others and is always full of energy. Great guy to have in your corner at work and outside of work!

Credentials
-
Arc Tool Operations and Programming
FANUC America CorporationMay, 2019- Nov, 2024 -
Handling Tool Operations and Programming
FANUC America CorporationMay, 2019- Nov, 2024 -
PTC Creo Design Engineer
PTCNov, 2015- Nov, 2024
Experience
-
Ceco Door Products
-
United States
-
Building Materials
-
100 - 200 Employee
-
Manufacturing Engineer
-
Jan 2022 - Present
-
-
-
MacLean Power Systems
-
United States
-
Utilities
-
400 - 500 Employee
-
Manufacturing Engineer
-
Apr 2018 - Jan 2022
• Identifying and implementing new technologies to keep all processes technologically competitive. • Facilitating kaizens in the value stream to support operational transformation initiatives. • Plan, manage and execute capital projects ranging from $50K to $1.5M targeted to retain long term strategic advantage. • Implementing, programming and troubleshooting of new robotic cells - experienced with Fanuc and Universal Robotics (UR). • Designing new tooling and fixtures for forge, weld, CNC and forming applications. • Developing new manufacturing processes, preparing standards and training documents. • Root cause problem solving using A3 thinking, "Kata" approach and rapid experimentation. • Ensure safe and ergonomic operations for upsetters, forge presses, forging robots, welding robots, forming presses, shears, CNC saws, automatic band saws, CNC mills and lathes, welding machines, CNC plasma equipment, etc. • Developing self managed teams and next generation of problem solvers on the floor to promote continuously improving processes. Show less
-
-
-
Mega Circuit, Inc.
-
United States
-
Appliances, Electrical, and Electronics Manufacturing
-
1 - 100 Employee
-
Manufacturing Engineer
-
Jan 2018 - Apr 2018
• Performing scrap analysis and communicate top 3 areas of improvement for all department supervisors and prioritize areas of urgent improvement. • Using hypothesis testing (z-test, f-test, t-test, ANOVA etc) to ensure process stability and consistency of product quality from different production lines, operators, machines etc. • Performing First Article Inspection (FAI) as needed by customers. • Coaching departmental teams in root cause analysis and the 7 quality tools for NC reduction projects and developing CAPA strategy. • Update standard work procedures and maintain SCAR reports upon successful completion of projects. • Assist management team to plan for plant layout modifications considering lean principles of flow and design individual work stations with ergonomic and human factor considerations. • Identifying suppliers for special project needs and negotiating quotations. Show less
-
-
-
Mega Circuit, Inc.
-
United States
-
Appliances, Electrical, and Electronics Manufacturing
-
1 - 100 Employee
-
Manufacturing Engineering Intern
-
Jan 2017 - Aug 2017
Main Achievements: 50% reduction in production lead time 11% less non-conformance (NC) incidents 16% less scrap Manufacturing Contributions: • Performed Value Stream Mapping (VSM) and estimated Overall Equipment Effectiveness (OEE) on the shop floor • Involved in preparing Process FMEA (PFMEA) to identify high risk failure modes and brainstorm ways to reduce the Risk Priority Number (RPN) and improving manufacturing processes reliability • Coordinate with maintenance and design department to error proof (poke yokes) manufacturing processes using Ishikawa diagram and FMEA results • Contributed on cross functional six sigma team to identify, prioritize, improve and prevent manufacturing non-conformance (NC) incidents • Worked with operators and managers to track and remove bottlenecks using Theory of Constraints (ToC) • Used SMED to reduce setup and changeover time at CNC machining stations leading to reduced work-in-process (WIP) inventory levels • Implemented lean manufacturing tools such as JIT, 5S, Kanban cards, Andon boards and visual control in cellular layout • Introduced concept of Water Spider to ensure continuous WIP flow to all workstations • Independently automated daily production planning and line balancing using Excel Quality Contributions: • Assisted with identifying Critical to Quality (CTQ) parameters and regular tracking of KPIs to improve quality and ensure compliance requirements • Used Root Cause Analysis (5 Whys, 8D) to investigate machine breakdown and quality non-conformance (NC) incidents • Assisted with procurement of new testing equipment, documenting standard work instructions and operator training • Experienced with PPAP (level 2) documentation for automotive clients and ISO 9001 compliance audit • Hands-on experience with Measurement System Analysis (MSA) and APQP • Use Statistical Process Control (SPC) and statistical methods to monitor processes and determine control limits for continuous improvement projects using Minitab and SAS Show less
-
-
-
KEC International Ltd.
-
India
-
Construction
-
700 & Above Employee
-
Manufacturing Engineer
-
Jul 2014 - Dec 2015
• Supported operations of multiple plastic extrusion machines, wire drawing machines and other auxiliary heavy machines in an HV cable manufacturing plant. • Team leader to setup new central tool room under a capital budget of $50K, resulted in improved process control • Increased overall manufacturing efficiency by 5.1% by improving the fabrication of special purpose tooling and components using DFM • Performed reverse engineering and design improvements for frequent failing parts to lower failure expectancy (MTBF) by 7.3% • Collaborate with cross-functional teams on 8 problem solving projects to improve key performance metrics (KPIs) • Coordinated with Quality and Design Engineering Department to resolve quality problems and process validation using ERP (we used JD Edwards) • Accountable for developing and ensured corrective action and preventive action (CAPA) deployment success over time • Used MS Project for project management of continuous improvement and preventive maintenance projects • Optimized workforce performance based on documented standard work sheets, cycle times and time study analysis and provided training to improve the working procedures and reduce fatigue considering ergonomics of work • Coaching operators and documenting new operating procedures / updating old SOP after improvement training Show less
-
-
-
Pakona Engineers (I) Pvt. Ltd.
-
India
-
Machinery Manufacturing
-
100 - 200 Employee
-
Research and Development Project Team
-
May 2013 - Jun 2014
Project: Alleviating filling related problems in automated packaging machinery • Performed root cause investigation to find and developed an array of ideas to solve problems in machine performance. • Designed timing screw and drip tray with optimized actuation and automatic speed control to match production rate • Improved the manufacturability of systems using design reviews given by design team • Net Benefit = 21% faster attainment of Break-Even cost due to Higher Productivity and Lesser Maintenance Show less
-
-
-
Reliance Industries Limited
-
India
-
Oil and Gas
-
700 & Above Employee
-
Summer Intern
-
May 2013 - Jul 2013
• Intern at the Petrochemical Plant (Oil and Gas Industry) • Involved with preventive maintenance planning and scheduling • Regular checking of pumps and turbines for any signs of failure or abnormal behavior for predictive maintenance. • Working with operations department to delegate tasks to the maintenance crew and procuring tasks • Helping in shutdown activities with problem-solving and getting hands dirty • Intern at the Petrochemical Plant (Oil and Gas Industry) • Involved with preventive maintenance planning and scheduling • Regular checking of pumps and turbines for any signs of failure or abnormal behavior for predictive maintenance. • Working with operations department to delegate tasks to the maintenance crew and procuring tasks • Helping in shutdown activities with problem-solving and getting hands dirty
-
-
Education
-
Gies College of Business - University of Illinois Urbana-Champaign
Master of Business Administration - MBA, Strategic Innovation | Managerial Economics and Business Analytics -
Michigan Technological University
Master of Science (MS), Mechanical Engineering -
Gujarat Technological University
Bachelor of Engineering (B.E.), Mechanical Engineering
Community
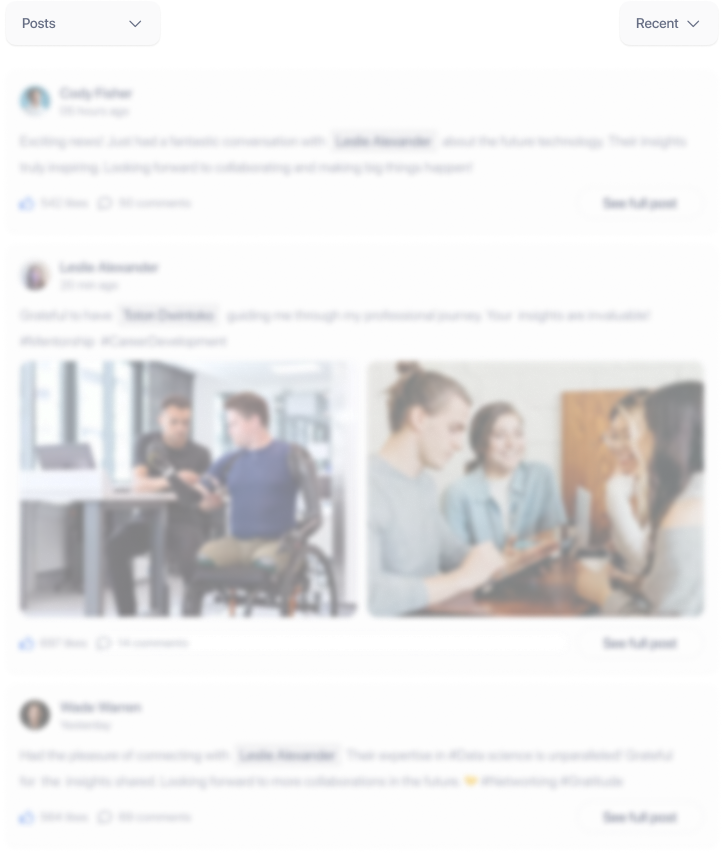