Valter Fernandes Moreira
Industrial Manager at JAL INDUSTRIAL- Claim this Profile
Click to upgrade to our gold package
for the full feature experience.
-
ingles Professional working proficiency
Topline Score
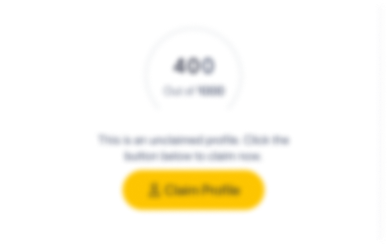
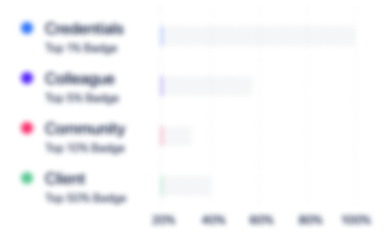
Bio

SILVIO SACRAMENTO
Valter é um excelente profissional, líder enérgico que consegue manter a motivação de seu time sempre em alta. Sempre preocupado com o bem estar de seu time, sabe extrair o melhor de cada colaborador, sempre com respeito e parceria.

Felipe Louzada
Valter é um líder transformador e motivado por desafios e realizações. Trabalhei com ele por três anos e participamos de um grande turnaround de resultados da unidade de SJC, principalmente, nas áreas que ele era gestor.

SILVIO SACRAMENTO
Valter é um excelente profissional, líder enérgico que consegue manter a motivação de seu time sempre em alta. Sempre preocupado com o bem estar de seu time, sabe extrair o melhor de cada colaborador, sempre com respeito e parceria.

Felipe Louzada
Valter é um líder transformador e motivado por desafios e realizações. Trabalhei com ele por três anos e participamos de um grande turnaround de resultados da unidade de SJC, principalmente, nas áreas que ele era gestor.

SILVIO SACRAMENTO
Valter é um excelente profissional, líder enérgico que consegue manter a motivação de seu time sempre em alta. Sempre preocupado com o bem estar de seu time, sabe extrair o melhor de cada colaborador, sempre com respeito e parceria.

Felipe Louzada
Valter é um líder transformador e motivado por desafios e realizações. Trabalhei com ele por três anos e participamos de um grande turnaround de resultados da unidade de SJC, principalmente, nas áreas que ele era gestor.

SILVIO SACRAMENTO
Valter é um excelente profissional, líder enérgico que consegue manter a motivação de seu time sempre em alta. Sempre preocupado com o bem estar de seu time, sabe extrair o melhor de cada colaborador, sempre com respeito e parceria.

Felipe Louzada
Valter é um líder transformador e motivado por desafios e realizações. Trabalhei com ele por três anos e participamos de um grande turnaround de resultados da unidade de SJC, principalmente, nas áreas que ele era gestor.

Experience
-
JAL INDUSTRIAL
-
Brazil
-
Construction
-
1 - 100 Employee
-
Industrial Manager
-
Nov 2022 - Present
Working in the industrial area with a focus on people safety and continuous improvement of processes, ensuring the quality of products. Evolve in the main performance indicators, OEE, Metal Loss, Productivity and Cost, through the application of Lean tools. Working in the industrial area with a focus on people safety and continuous improvement of processes, ensuring the quality of products. Evolve in the main performance indicators, OEE, Metal Loss, Productivity and Cost, through the application of Lean tools.
-
-
-
Gerdau Special Steel
-
Mining
-
400 - 500 Employee
-
Production Coordinator
-
Dec 2020 - Sep 2022
Responsible for the application of routine management tools, resulting in a jump in the evaluation of Operational Excellence from 47% in Jan/21 to 82.7% in Aug/22. Leadership Proactivity Index (IPL) 83%; Evolution of the area towards a more inclusive environment, going from a rate of 2% to 15% of women in the operation; Development of a multipurpose team, with training of professionals in strategic positions for the business, resulting in overcoming 3 years without complaints from customers in the inspection line and 2 years in the heat treatment furnace. Support and development of ergonomic tools in the project zero hand on the bar (hands off), resulting in 3 years without accidents in the oven and 1 year at the rework station; Achievement of 15 years without accidents in inspection lines and 17 years in the heat treatment furnace. Show less
-
-
-
Grupo IBRAME
-
Brazil
-
Mining
-
100 - 200 Employee
-
PRODUCTION COORDINATOR
-
Jan 2019 - Dec 2020
Responsible for the Wire Drawing and ETP Copper Production area, surpassing a daily production in the Shaft furnace of 325t/day and a record production in the FRHC refining furnace of 314t per run (100,000 t/year); Development, together with the support areas, of the career plan for the Unit, having as main challenge the formation of a new leadership team and the inclusion of women in the productive environment; Acting in the development of a culture focused on operational safety with the use of the Regulatory Norms - NR's, and the achievement of 1 year without a lost-time accident (CPT); Promotion of changes through people for an organized environment, with defined methodologies for the continuous improvement of production processes. Show less
-
-
-
Gerdau
-
Brazil
-
Mining
-
700 & Above Employee
-
PRODUCTION MANAGER (TREFILA DE BARRAS, TREFILA DE SOLDAS E TREFILA DE ARAMES INDUSTRIAS)
-
Nov 2016 - Apr 2018
Responsible for reducing operating costs by 5% by training new leaders and consolidating results from three different areas and processes, under a challenging market scenario;Acting in the strategy of new investments (drawing for thick gauge wires), in the growth of productivity and in the reduction of labor liabilities;Identification of gains in small details, encouraging the team to make the best decisions with autonomy and responsibility, in an environment under constant change.
-
-
PRODUCTION MANAGER (TREFILA DE BARRAS E AMPLIADOS)
-
Nov 2014 - Nov 2016
In a new management structure, operating in two areas with different processes, the challenges were to operate in a steel market in crisis, identifying new opportunities and strategies;The use of Lean tools (Gemba Walk, Kamishibai and Kaizen) in the search for world-class results was essential for learning a new culture with the overcoming of the record in the production of Trusses and an OEE (global efficiency) of 90% ;Support for the HR and legal areas in labor proceedings, which directly impacted the cost results of the production areas, was a differential during this period. The preparation of the defense, construction of the questions, participation as a technical assistant in expertise and the presence in hearings as a witness and agent contributed to the reduction of labor costs. Show less
-
-
PRODUCTION MANAGER (TREFILA DE ARAMES INDUSTRIAIS)
-
Sep 2011 - Oct 2014
Evolution of 10%/year in productivity, becoming a reference in internal indicators and operating within a unionized environment were the main challenges;Acting strategically on NR12, it was possible to build a safe environment, reaching the 4-year mark without lost-time accidents. The focus on eliminating risks, working together with the operation, was decisive for the result;The achievement of higher levels in process indicators (metallic loss and utilization) and the 5% growth in production capacity were decisive in attracting new investments to the area. Show less
-
-
PRODUCTION MANAGER (TREFILA DE BARRAS)
-
Nov 2007 - Sep 2011
Reporting to the unit's executive manager, having as main challenge the formation of a new leadership team, breaking the production record of Drawn Bars;With the application of routine management tools, proximity to the operation and working to create a sense of team, it was possible to improve the results of the main indicators. The results were an increase in utilization by 50% and a reduction in metallic loss by 30%;Definition of the action strategy with the tool of times and methods and autonomous maintenance, contributing to a 32% reduction of electrical and mechanical corrective, fundamental to see opportunities and create the future plan with improvement in processes and layout;With strong leadership, autonomy and support for new leaders, it was possible to transform a degraded environment, with unsatisfactory results, into an area of reference in organization, cleanliness and team engagement. Best unit climate survey (93%);Overcoming 500,000 hours without a lost-time accident;Overcoming three years without a lost-time accident. Show less
-
-
COORDINATOR OF TRAINING IMPROVEMENTS
-
Jul 2001 - Oct 2007
Interaction with all productive sectors of the industrial unit, leading the implementation of the management process, aiming to stabilize processes and achieve maximum operational performance;Support to production areas, using methodologies such as MASP, Six Sigma, 5S, to ensure proper routine execution and identify opportunities for continuous improvement of systems and processes;Improvements in the process and safety, exceeding 200,000 hours without a lost-time accident;Increase in productivity and cost reduction;Promoted to area manager with the challenge of maintaining the results achieved and continuous evolution. Show less
-
-
-
Orbital Caldeiraria
-
Mogi das Cruzes
-
MECHANICAL ENGINEER
-
Apr 2000 - Jul 2001
Report to the owner of the company. Supervisor, working in the area of service rendering in several companies (NGK do Brasil, Johnson Controls, Hoganas), led a team with approximately 30 people, focused on the needs of customers (altering lay-outs, installation of machines, industrial boilermaking and renovations in general). Report to the owner of the company. Supervisor, working in the area of service rendering in several companies (NGK do Brasil, Johnson Controls, Hoganas), led a team with approximately 30 people, focused on the needs of customers (altering lay-outs, installation of machines, industrial boilermaking and renovations in general).
-
-
-
MANNESMAN VDO AG
-
Belgium
-
1 - 100 Employee
-
UNIVERSITY TRAINEE
-
Nov 1997 - Jul 1999
University trainee working in the routine maintenance of molds, stamping and plastic injection molding. Acquired the knowledge of process management in the auto parts industry. University trainee working in the routine maintenance of molds, stamping and plastic injection molding. Acquired the knowledge of process management in the auto parts industry.
-
-
-
Villares S.A.
-
Mogi das Cruzes
-
MAINTENANCE MECHANIC
-
Jun 1993 - Jun 1997
Mechanical maintenance in rolling mills, presses, saws and hydraulic systems. Application of the concepts of total productive maintenance (TPM). Mechanical maintenance in rolling mills, presses, saws and hydraulic systems. Application of the concepts of total productive maintenance (TPM).
-
-
-
Villares S.A.
-
Mogi das Cruzes
-
OFFICE BOY
-
Jun 1989 - Apr 1990
Administrative routines Administrative routines
-
-
Education
-
ETEP Faculdades
Post-Graduation in Work Safety Engineering, Industrial Security -
Universidade Estadual Paulista Júlio de Mesquita Filho
Post Graduate in Production Management, 8,75 -
Brazcubas Educação
University graduate, Mechanical Industrial Engineering -
EF English Live
Fluency in English, Learning English as a Second Language -
Superando Consultoria
Judicial Expert and Technical Assistance in Unhealthy and Hazardous -
Lean Way
Management for Genba, Lean Manufacturing -
Lean Way
Fundamentals of Lean Systems, Lean Manufacturing -
Amana Key
APG Middle Advanced Management Program, Leadership development -
INDG Instituto de Desenvolvimento Gerencial
Six Sigma Green Belt -
Liceu Braz Cubas
Mechanical technician -
KIT ENGLISH COURSE
Fluency in the language (private lessons), Seconde language - English -
Universidade Braz Cubas
Engenharia Industrial Mecânica, Engenharia Mecânica
Community
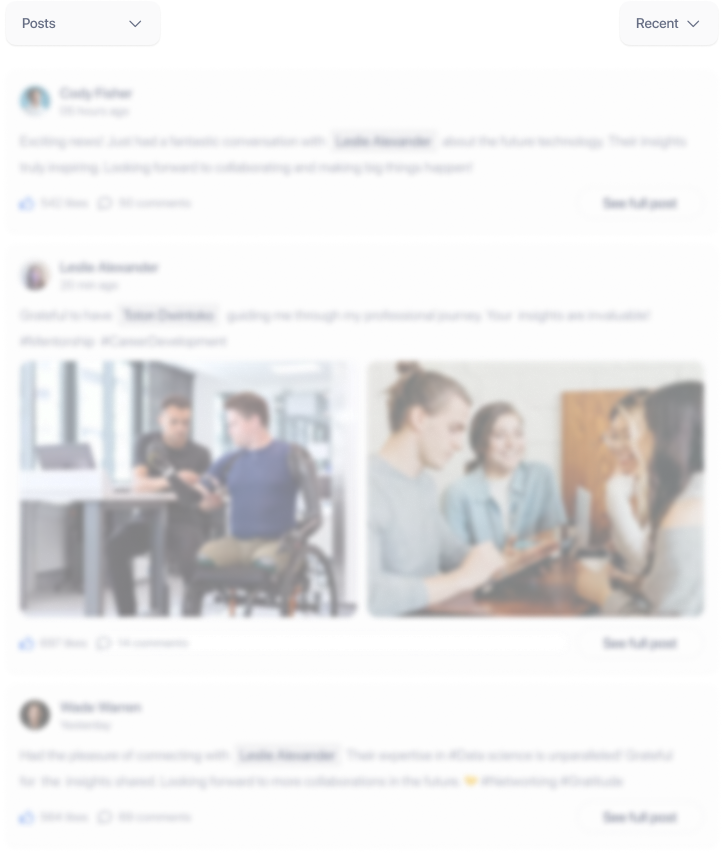