Kathleen Munster, MBA
Chief Quality Officer & SVP, Technical Operations at Intercept Pharmaceuticals- Claim this Profile
Click to upgrade to our gold package
for the full feature experience.
Topline Score
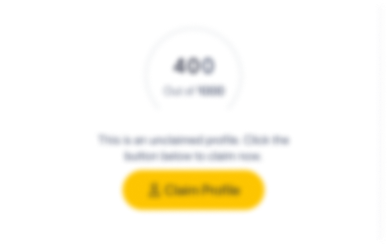
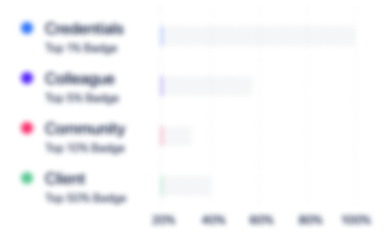
Bio


Experience
-
Intercept Pharmaceuticals
-
United States
-
Pharmaceutical Manufacturing
-
300 - 400 Employee
-
Chief Quality Officer & SVP, Technical Operations
-
Nov 2022 - Present
-
-
-
2seventy bio
-
United States
-
Biotechnology
-
200 - 300 Employee
-
SVP, Enabling Functions (Quality, Facilities, & IT)
-
Nov 2021 - Nov 2022
-
-
-
bluebird bio
-
United States
-
Biotechnology Research
-
300 - 400 Employee
-
Senior Vice President, Quality
-
Oct 2020 - Nov 2021
-
-
-
Catalent Pharma Solutions
-
United States
-
Pharmaceutical Manufacturing
-
700 & Above Employee
-
Vice President, Quality - Cell & Gene Therapy
-
May 2020 - Oct 2020
-
-
Vice President - Quality, Biologics & Gene Therapy
-
Oct 2019 - May 2020
-
-
Vice President, Quality - Biologics & Specialty Drug Delivery
-
Feb 2018 - May 2020
Reporting to the Senior Vice President of Quality for Catalent, responsible for ensuring the successful delivery of quality/regulatory strategy, operational performance, and driving “One Catalent” quality standards across the Biologics & Specialty Drug Delivery business unit. This includes six manufacturing sites responsible for ~600MM in revenue covering analytical services, ophthalmic & respiratory products, sterile blow-fill-seal, and biologics drug substance/drug product manufacturing for distribution covering FDA, EMA and global regulatory markets. Show less
-
-
-
Bristol Myers Squibb
-
United States
-
Pharmaceutical Manufacturing
-
700 & Above Employee
-
Director, Site Quality Lead
-
2015 - 2018
Reporting to the Executive Director, Global Biologics Internal Sites, serve as the head of the Devens Site Quality Unit. Responsible for all aspects of the Quality Unit, including QC Operations, QA Operations, QC Technical Support, and Compliance & Quality Systems. Accountable for the testing, release, and quality systems used in the manufacture and disposition of Biologic Drug Substance and related materials. Scope includes commercial and clinical manufacturing oversight. Operations overseen include multi-shift, multi-level QC laboratories covering release, stability, in-process, and environmental monitoring activities. Total organization comprised of ~125 employees with an operating budget of ~$20MM. Show less
-
-
Director, Quality Product Lead, Global Biologics Quality
-
2014 - 2015
Serve as the primary Quality point of contact for designated product(s) within the global BMS network. Drive the planning and execution of the Quality component of the Product Strategic Plan including, but not limited to: global pre-filing readiness plans, global change control strategy, end-to-end Annual Product Quality Reviews, product lifecycle initiatives, and product risk assessments. Accountable for filing and inspection readiness for new Biologic products.
-
-
Director, Global Quality Systems
-
2011 - 2014
Responsible for the Global Quality & EHS (GQEHS) Quality System Framework (GMP policies and directives), applicable to all Global Manufacturing & Supply sites and functional areas. Serve as the global business owner for the BMS product specification and analytical method database (Global Testing Standards) and the GMS change control program and system; responsibilities include identification and implementation of global standards, processes, and strategic roadmaps for these tools. Oversee Knowledge Management (KM) and training for GQEHS, including the deployment of a KM strategy and baseline CGMP and role-based curricula for Quality. Support site inspections and facilitate the global communication of inspection observations and response to emerging regulations. Manage a team of direct reports, including full-time and contractor resources. Show less
-
-
Associate Director, Global Supply Chain
-
2010 - 2011
Identified and built global business processes and solutions within the BMS enterprise inventory management System (SAP) for Quality and Make (manufacturing) process streams. Built alignment across other work streams (Procure, Plan, and Deliver) and integrated with cross-initiative partners (finance, operations, and enterprise data) to ensure full value of programs was realized. Leveraged technology to lead de-centralized team structure and identified development opportunities to staff project. Implemented project, including a comprehensive change management plan, globally, on-time, and within budget. Work was initiated while a member of Global Supply Chain and was completed after transitioning to current role within GQEHS. Show less
-
-
Associate Director, Technical Operations Information Management
-
2008 - 2010
Responsible for the management and implementation of strategic Technical Operations manufacturing and laboratory solutions including global electronic change control (eCC), Global Testing Standards replacement, and WWQC deviation management system (TrackWise QMS). Developed system requirements based on business processes and created roadmaps for application implementation and cross-divisional system integration. Managed portfolio entries and project budgets. Supported WWQ&C in the roll out of IM initiatives and tools. Ensured inspection readiness of the TOIM organization and systems. Show less
-
-
Manager, Worldwide Quality & Compliance
-
2005 - 2008
Responsible for the development and implementation of a global electronic change control system (eCC). Partnered with TOIM to design TrackWise®-based workflows, identify user requirements, and manage project schedule to ensure timelines are met. Responsible for oversight of the manufacturing change control process. Work completed after transferring to the TOIM organization. Responsible for conducting systems-based audits of BMS Global Technical Operations sites and Third-Party manufacturing (API, sterile, non-sterile, and biologic), finishing and packaging operations, quality systems, distribution centers, and suppliers to ensure compliance with cGMPs, Health Authority regulations, and BMS requirements. Performed PAI readiness audits to support new product approvals and product transfers. Conducted ‘For Cause’ investigations of compliance issues and assist in identifying/tracking corrective and preventive actions in conjunction with the Office of Corporate Compliance. Led Controlled Substance/DEA compliance audits to ensure Technical Operations sites adhere to applicable state and federal regulations and BMS Policies and Directives. Show less
-
-
-
-
Quality Assurance Analyst / Senior Site Compliance Inspector
-
2001 - 2005
Responsible for conducting audits of external vendors, including raw material suppliers, component suppliers, and contract manufacturers and printers. Supported on-site capital projects, including qualification document review and PAI readiness activities. Ensured efficient coordination of regulatory inspection activities, including preparative efforts and collection/review of commitment evidence. Responsible for ensuring departments within Vaccine & Sterile Operations operate in a state of compliance by performing internal audits, weekly Shop Floor Presence inspections, document review, and investigating customer complaint and adverse experience reports. Show less
-
-
Education
-
Rutgers Business School
Master of Business Administration (M.B.A.), Concentration: Marketing -
Temple University School of Pharmacy
Certificate in Drug Development, Quality Assurance / Regulatory Affairs Program -
Lafayette College
Bachelor's degree, Dual degrees in Chemistry & German, minor in Health Care
Community
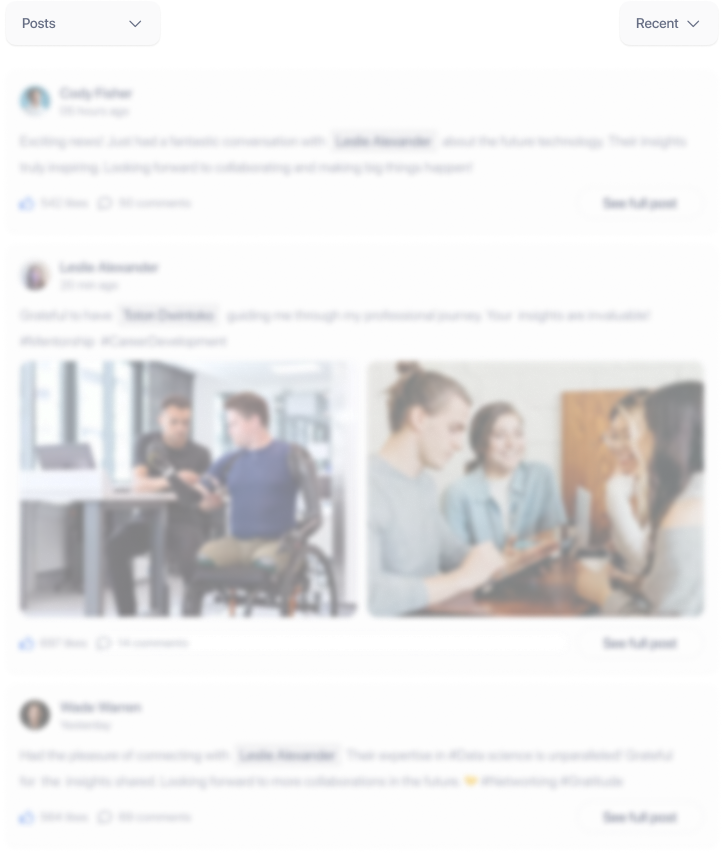