Chris Endress
Industrial/Mfg/Lean Engineer at Thetford- Claim this Profile
Click to upgrade to our gold package
for the full feature experience.
-
Spanish -
-
German -
Topline Score
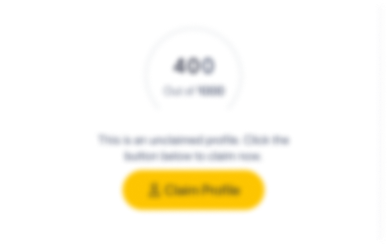
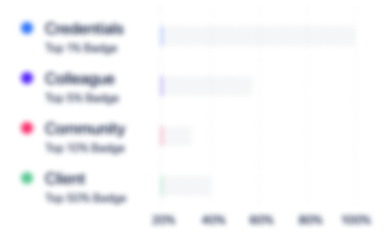
Bio


Experience
-
Thetford Europe
-
Netherlands
-
Consumer Goods
-
100 - 200 Employee
-
Industrial/Mfg/Lean Engineer
-
Jun 2012 - Present
Supporting two Plants in project management, labor analysis, layout, productivity reporting, standard work, Lean application, ergonomics, capital procurement, estimating, project management and problem solving in Consumer Products manufacturing, bottling, and dry chemical processing. Supporting two Plants in project management, labor analysis, layout, productivity reporting, standard work, Lean application, ergonomics, capital procurement, estimating, project management and problem solving in Consumer Products manufacturing, bottling, and dry chemical processing.
-
-
-
Pinnacle Strategies
-
United States
-
Business Consulting and Services
-
1 - 100 Employee
-
Senior Consultant
-
Jun 2010 - Feb 2011
Develop system of work order prioritization designed to enable complex aircraft manufacturer to reduce shortages, minimize work-in-process inventory and achieve FIFO production. Analyze production requirements, integrate work prioritization tool and associated metrics. Create and deliver training for Management and Production personnel. Create supporting policies and procedures. Develop system of work order prioritization designed to enable complex aircraft manufacturer to reduce shortages, minimize work-in-process inventory and achieve FIFO production. Analyze production requirements, integrate work prioritization tool and associated metrics. Create and deliver training for Management and Production personnel. Create supporting policies and procedures.
-
-
-
-
Global Plant Improvement
-
2006 - 2009
Practical application of Lean Principles to Production Environment. Be consistent role model and resource for multiple Lean Mfg., Industrial Engineering and Training activities to Mgt., Engineering and Mfg. personnel. Analyze and graphically depict workload and staffing for Operations. Create Workplace Org. and Visual Mgt. guide. Development of detailed Excel spreadsheet/reports to automatically visually convey status of in-process buffer quantities. Develop and deliver problem solving training to Production Team Leaders and Team Members. Document, organize and visually convey problem/resolution status. Organize and deliver training to Production Launch Managers. Estimate launch team staffing, pre-production and start-up costs for new programs. Develop Standard Work for cyclic and non-cyclic operations. Train TL's and GL's in Standard Work development. Create Value Stream Maps and train Engineers, GL's, TL's and TM's to do same. Show less
-
-
-
-
Manager, Industrial Engineering
-
Jan 1995 - Jan 2006
Lead Plant, Divisional and Corporate Industrial Engineering groups in new program implementation, productivity reporting, layout development, common standards, and best practices. Directed fledgling IE group through significant rearrangement, preparation, and startup of 2 new Transmission Assembly lines while maintaining production on 3 others in same facility. Eliminated 98% of hard copy reporting and distribution by being first in GM to implement web-based reporting systems. Led Divisional People Cost Account Champion process for 6 years resulting in 6-10% annual improvement. Organized Value Stream Mapping training for multiple sessions leading to 120+ knowledgeable Mfg. Engineering and Lean Manufacturing resources. Christopher E. Endress Page 2 GM Powertrain, Show less
-
-
-
-
Industrial Engineering Supervisor, Senior Manufacturing Engineer, Project Engineer
-
Jan 1985 - Jan 1995
Developed manufacturing consolidation strategy and implementation plan for non-strategic Powertrain components. Researched and applied Bill of Process methodology and documentation to Powertrain operations. Specified, recommended, and qualified $3.5 million of equipment for Powertrain component manufacturing. Developed manufacturing consolidation strategy and implementation plan for non-strategic Powertrain components. Researched and applied Bill of Process methodology and documentation to Powertrain operations. Specified, recommended, and qualified $3.5 million of equipment for Powertrain component manufacturing.
-
-
-
-
Manufacturing Engineer
-
1981 - 1985
estimating, processing, continuously improving machined parts. Achieved 24 hr. process development/tool design/production for emergency customer support. Created Tool Life and Costing methodology used to accurately estimate new production. Established changeover Bills of Materials to standardize and reduce setup time. estimating, processing, continuously improving machined parts. Achieved 24 hr. process development/tool design/production for emergency customer support. Created Tool Life and Costing methodology used to accurately estimate new production. Established changeover Bills of Materials to standardize and reduce setup time.
-
-
-
-
Industrial Engineer
-
1978 - 1980
estimating new product, improving layout and material flow, study/reduce labor cost, packaging engineering. estimating new product, improving layout and material flow, study/reduce labor cost, packaging engineering.
-
-
Education
-
GMI (now Kettering)
BS, Industrial Engineering -
GMI-EMI (now Kettering)
MS, Manufacturing Management
Community
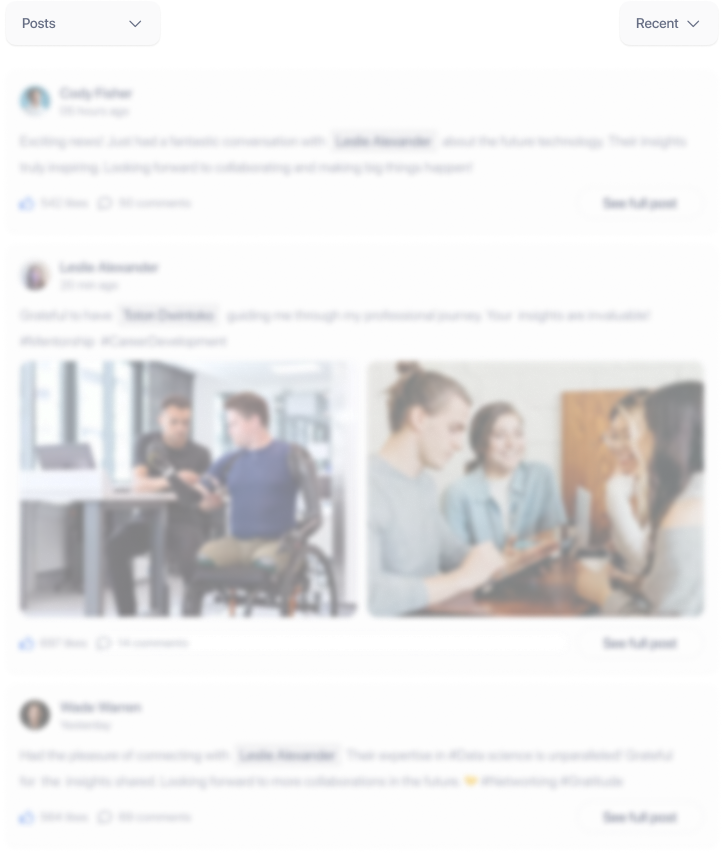