
Mark Volkenant
Director Of Manufacturing Operations at MAUD BORUP- Claim this Profile
Click to upgrade to our gold package
for the full feature experience.
Topline Score
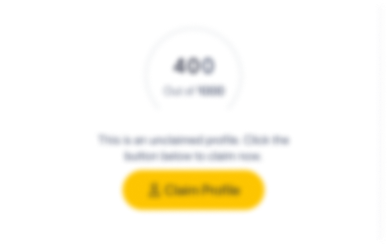
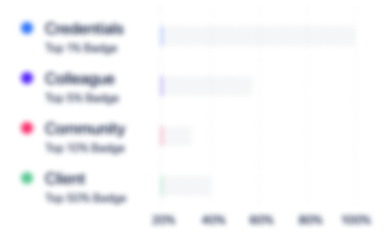
Bio

Alison Egeberg
Like most businesses, our company is organized into functions. Mark has interacted with virtually all of them. There are normal tensions between the functions which if not managed correctly can prove disastrous. Mark has always understood the old adage that we rise or fall together and exceeds expectations in

Alison Egeberg
Like most businesses, our company is organized into functions. Mark has interacted with virtually all of them. There are normal tensions between the functions which if not managed correctly can prove disastrous. Mark has always understood the old adage that we rise or fall together and exceeds expectations in

Alison Egeberg
Like most businesses, our company is organized into functions. Mark has interacted with virtually all of them. There are normal tensions between the functions which if not managed correctly can prove disastrous. Mark has always understood the old adage that we rise or fall together and exceeds expectations in

Alison Egeberg
Like most businesses, our company is organized into functions. Mark has interacted with virtually all of them. There are normal tensions between the functions which if not managed correctly can prove disastrous. Mark has always understood the old adage that we rise or fall together and exceeds expectations in

Experience
-
Maud Borup
-
United States
-
Food and Beverage Manufacturing
-
1 - 100 Employee
-
Director Of Manufacturing Operations
-
Mar 2020 - Present
-
-
-
-
Chief Operating Officer
-
Sep 2017 - Present
Business consulting• Offering professional expertise and monitoring performance to ensure that Company, Department and Individual objectives are achieved. Develop and establish metrics, policies and standard work to build and maintaining a safe, legally compliant workplace. • Impactful leader effecting the organization’s bottom line utilizing my background in quality, management and continuous improvement to improve all business operations including production, operations, and logistics.
-
-
-
Black Forest Ltd.
-
United States
-
Retail Luxury Goods and Jewelry
-
1 - 100 Employee
-
Senior Vice President of Operations
-
Jul 2018 - Mar 2020
Oversee day-to-day operations to support the growth and add to the bottom line of the organization. Focus is on strategic planning, goal-setting and direct the operations of the company in support of its goals. Responsible for helping the company to achieve financial goals and objectives and increase operating performance.Primary responsibilities:- Oversee and manage regional and cross-functional divisions of an organization.- Oversee accounting and financial analysis, and monitor for profitability and losses.- Partner with other senior management to discuss strategies, objectives, and obstacles.- Monitor and strategize to reach annual targets and new markets.- Ensure company policies and procedures are followed by each department.- Attract, retain and motivate staffEnsure highly productive relationships and partnerships for the benefit of the organizationSet goals, monitor work, and evaluate results to ensure that departmental and organizational objectives and operating requirements are met and are in line with the needs and mission of the organization.
-
-
-
Sojos Pet Food
-
United States
-
Food Production
-
1 - 100 Employee
-
Director of Operations
-
Sep 2013 - 2017
SOJOS RAW DOG FOOD MIXES are made from scratch with whole food. It's homemade, raw dog food, made easy. We offer a variety of grain-free options in our full line of all-natural pet food. Unlike kibble, Sojos raw pet food contains no fillers, no preservatives, and no artificial colors or flavors. Just simple, real ingredients like you’d find in your own kitchen. (check us out at WWW.Sojos.com)At Sojos we make the best pet food in the market. Here I direct and coordinate operations, formulate policies, managing daily operational activities, and plan use of materials and human resources toward maximum productivity.Daily job duties include reviewing financial statements, sales and activities reports, oversee production or service delivery, manage the activities of sales and distribution departments, and establishing long-term goals and objectives for the organization. I also analyze areas requiring improvement, reduce costs, maximize efficiency and improve profitability. Direct and coordinate financial budget's and processes. Supervise human resource activities, determining staffing requirements, interviewing, hiring and training new employees. Additionally, I participate in sales activities, including developing a product or service mix, setting pricing and determining customer demand through data analysis.
-
-
-
-
Plant Manager
-
May 2012 - Sep 2013
Creates an injury free and safe work culture. Ensures all employees at all levels are treated with dignity and respect.Drives excellence in both dual bottom lines (business and financial results & personal development and growth) through leadership.Presents a positive ethical example and contribute to a positive tone-at-the-top in the internal control environment.Controls quality and cost of production through employees and coordination with engineering and other departments.Develops monthly and annual budgets consistent with budgetary guidelines established by finance. Responsible for operating the plant within these guidelines.Maintains close collaborative relationships with engineering, customer service, finance, human resources and other departments so that problems relating to operations can be quickly identified, analyzed and corrective action taken.Directs all activities relating to operations including organization and staffing, compensation of employees, control of expenses and coordination of activities with other departments. Maintains policies and administers them fairly and equitably. Makes every effort to effectively handle employee relations with the assistance of Human Resources support when appropriate. Analyzes, recommends and implements practices/procedure improvements in manufacturing in order to increase quality and quantity of manufacturing efficiencies.Determines the need for, justifies, and recommends the purchase of manufacturing equipment to increase efficiencies and economies of operation. This includes preparing and submitting capital appropriation requests.Responsible for hiring and maintaining highly talented individuals and operations to meet or exceed company growth goals. Provides leadership and development to employees through feedback, accountability, coaching and mentoring and growth opportunities.
-
-
-
Kraft Heinz
-
United States
-
Food and Beverage Services
-
700 & Above Employee
-
Production Manager
-
May 2011 - May 2012
Overseeing the production process, drawing up a production schedule; ensuring that the production is cost effective; making sure that products are produced on time and are of good quality; working out the human and material resources needed; drafting a timescale for the job; estimating costs and setting the quality standards; monitoring the production processes and adjusting schedules as needed; being responsible for the selection and maintenance of equipment; monitoring product standards and implementing quality-control programmes; liaising among different departments, e.g. suppliers, managers; working with managers to implement the company's policies and goals; ensuring that health and safety guidelines are followed; supervising and motivating a team of 275 workers; reviewing the performance of subordinates; identifying training needs
-
-
-
Kraft Heinz
-
United States
-
Food and Beverage Services
-
700 & Above Employee
-
Continuous Improvement Coordinator
-
May 2010 - Nov 2010
Worked on continuous improvement activities across mutiple value streams; improving efficiences, removing waste and creating a lean culture. Worked on continuous improvement activities across mutiple value streams; improving efficiences, removing waste and creating a lean culture.
-
-
-
Coloplast
-
Denmark
-
Medical Equipment Manufacturing
-
700 & Above Employee
-
Senior Lean Manager
-
Dec 2000 - Apr 2010
•Driving culture change, accountability and continuous improvement mindset throughout the organization through Lean practices within Coloplast facilities (Mankato, Marietta, Minneapolis) and abroad (Denmark, Hungry, Germany, France, Italy). Efficiency gains in OEE at 20% – 40% within many different Value Streams – embedded into the factory culture and actions. •Developing, managing and coaching all facility Group Leads, Team Leads and Team Member’s to be highly effective and accelerate improvements within value stream(s).•Manage capacity/schedules to achieve On Time Delivery, growth and productivity goals, as well as integrate key elements of Supply Chain to improve cycle times by 35% within Value Steams - implementing Kanban, JIT methodologies and Vendor Managed Inventories (VMI).•Facilitating and executing Kaizen (Rapid Improvement) and Value Stream Analysis events to reduce direct and indirect costs, eliminate waste and increase efficiencies, ensuring process and yield improvements.•Championed employee training and communication programs throughout the organization on Root Cause Analysis, Lean Principles, employee suggestion, and Six Sigma Tools to support operational and strategic goals.•Improved and develop organizational capabilities through effective performance management and planning/utilization of human and capital resources - building self empowered teams and quality circles.•Facilitate Policy Deployment workshops with Executive Management to create objectives and Key Performance Indicators utilizing lean principles. Build concensus and establishing a strategic vision for double digit growth in becoming the market leader in the health care industry. • Proficient in: Value Stream Analysis (VSA), SMED, PDCA, Root Cause Analysis, Kanban, Process Preparation (2P), Pull, Visual Management, Load-Load, Cell Building, Standard Work, 6S, Voice of the Customer (VOC) tools, and Six Sigma tools.
-
-
-
-
Operations Manager
-
1999 - 2000
Supervise the manufacture of AC generators, motor-generator sets and controls for prime, standby, and peak shaving power generation units. Managed Production and Process Technicians (72) in a high volume manufacturing environment utilizing welding, stamping and machining cells. Managing departmental budgets, instructing operations and employees in the manufacturing processes to meet customer needs Supervise the manufacture of AC generators, motor-generator sets and controls for prime, standby, and peak shaving power generation units. Managed Production and Process Technicians (72) in a high volume manufacturing environment utilizing welding, stamping and machining cells. Managing departmental budgets, instructing operations and employees in the manufacturing processes to meet customer needs
-
-
-
Caterpillar Inc.
-
United States
-
Machinery Manufacturing
-
700 & Above Employee
-
Engineering Manger
-
1996 - 1999
Responsibilities were managing capital projects and departmental budgets. Facilities planning, design engineering, implementing procedures, methods, and processes designed to maximize utilization of labor, material, equipment, and improve production efficiency. Maintain Engineering staff job results by coaching, counseling and appraising job performance. Responsibilities were managing capital projects and departmental budgets. Facilities planning, design engineering, implementing procedures, methods, and processes designed to maximize utilization of labor, material, equipment, and improve production efficiency. Maintain Engineering staff job results by coaching, counseling and appraising job performance.
-
-
-
-
Design Engineer
-
Jul 1993 - Jul 1996
-
-
-
United States Air Force
-
United States
-
Defense and Space Manufacturing
-
700 & Above Employee
-
Sgt.
-
Mar 1987 - Mar 1991
Electronic Security / Communications Electronic Security / Communications
-
-
Education
-
Minnesota State University, Mankato
Master of Science, Engineering & Business -
Minnesota State University, Mankato
Bachelor of Science, Manufacturing Engineering -
University of Utah
Lean Manufacturing -
ASQ
Six Sigma Green Belt -
Expert Rating
Six Sigma -
Expert Rating
Project Management -
Food Safety Preventive Controls Alliance
Preventive Controls Qualified Individual
Community
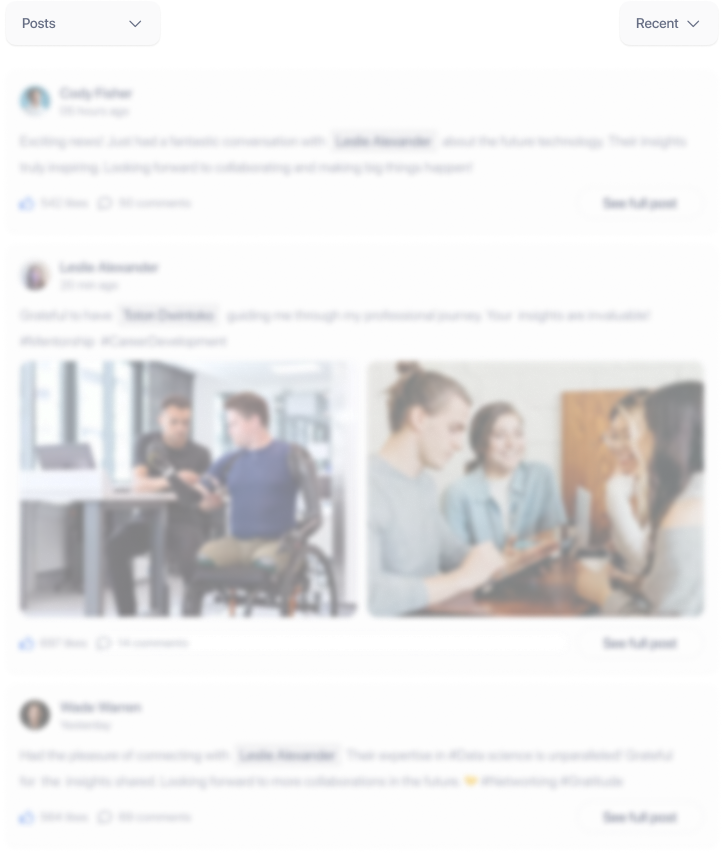