Cynthia Mack
Inventory Control Specialist at Avio-Diepen- Claim this Profile
Click to upgrade to our gold package
for the full feature experience.
Topline Score
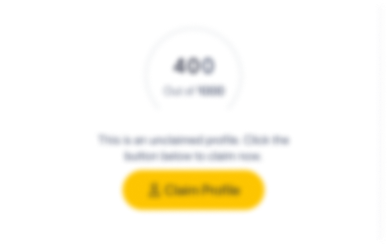
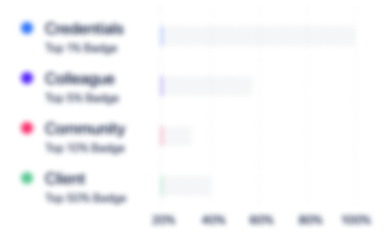
Bio


Experience
-
Avio-Diepen
-
Netherlands
-
Aviation & Aerospace
-
1 - 100 Employee
-
Inventory Control Specialist
-
Oct 2009 - Present
Avio-Diepen is an ISO9001:2015, AS9120B, and FAA AC-0056B distributor of spare parts for the aviation and aerospace industry. Proponent acquired Avio in 2016. This 35K SF site closed and the functions were moved to other locations. – Maintained a high level of inventory accuracy. Team managed approximately 50K receiving and shipping lines processed annually from a combination of U.S. and European-based manufacturers. – Received, stored, picked, packed, labeled, and shipped aircraft parts intended for resale and intercompany. – Placed parts in proper location, scanned documents into system, and filed hard copies. – Coordinated all kitting activities for three team members; personally kitted boxes with up to 90 items. – Coordinated special projects such as a packing, labeling, or boxing for a key customer. – Determined daily operational demands and prioritized workload. – Handled aircraft materials in accordance with applicable company and FAA procedures and instructions. – Managed and operated all shipping systems (UPS, FedEx) and managed numerous customer pick-up requests. – Inspected items to ensure part numbers and serial numbers were correct; ensured no parts were damaged. – Verified that proper paperwork had been sent, including certificates required by FAA. – Inspected parts as they passed through outbound shipping process to ensure correct part number and quantity. Checked for required paperwork, and stamped all copies once item was reviewed. – Led the logistics team in performing daily activities. – Became a front-line logistical expert in both inbound and outbound transactions. Utilized proficiency in multiple carrier systems to execute customer pick-up requests. – Hired as a temp through FutureStaff; converted to full-time April 2010. Show less
-
-
-
Panasonic Automotive North America
-
United States
-
Appliances, Electrical, and Electronics Manufacturing
-
700 & Above Employee
-
Inventory Control Coordinator
-
1998 - 2009
Panasonic Automotive Systems of America (PASA) is a supplier of infotainment systems to the automotive industry. It is a division of Panasonic Corporation of North America, and a subsidiary of Panasonic Corporation in Japan. Customers include Honda, General Motors, and Toyota.– Managed $870K worth of machinery spare parts and supplies. Handled ordering, tracking, receiving, issuing, and returns. Steadily researched and identified spare part alternative vendors in order to obtain better pricing and lead times. Used Datastream MP2 maintenance inventory management system to ensure order integrity. – Consistently reduced spare parts through accurate and timely communication with management and technicians. – Improved inventory process by implementing a bar coding system. Reduced miscounts and improper part sign-out. Decreased monthly inventory time from three-and-a-half days to one, for an annual savings of $8K. – Saved $173K annually by monitoring and reducing on-hand inventory and establishing re-order points. – Saved $300K annually by negotiating long-term agreements and pricing programs with key vendors. – Achieved SOX compliance regularly through monthly physical inventory audits and blind counts. Show less
-
-
Inspector
-
1994 - 1998
– Sorted and placed materials / items on racks, shelves, or in bins according to predetermined sequence including size, type, style, color, or product code. Read production schedules, inventory reports, and work orders. – Processed orders for merchandise received by mail, telephone, or email from customers or company employees. – Assisted in counting physical inventory and fixing inventory discrepancies. Entered information into database. – Examined material received to verify part numbers and check for discrepancies. – Edited orders received for price and nomenclature. – Informed customer of unit prices, shipping date, anticipated delays, and any additional information needed. – Advised customer if an order was close to a discount amount and suggested they add to their order to take advantage of the reduced rate.– Coordinated parts shipments with field service for 100% customer satisfaction. – Made suggestions that were implemented in the department by management. – Conducted inventory cycle counts with a consistent accuracy rate of 97% by monitoring the computer order system frequently throughout the day. Show less
-
-
Quality Assurance Specialist
-
1992 - 1994
– Accurately performed quality checks resulting in zero customer returns due to quality issues. – Proactively identified areas of improvement and provided proposals to management. Implemented appropriate improvements to enhance product quality and practices. – Inspected incoming parts to determine if they met quality standards. Executed corrective action when necessary.– Hired as a temp through Talent Tree; converted to full-time.
-
-
Education
-
LaGrange College
-
Greenville High School
-
Professional Development
Community
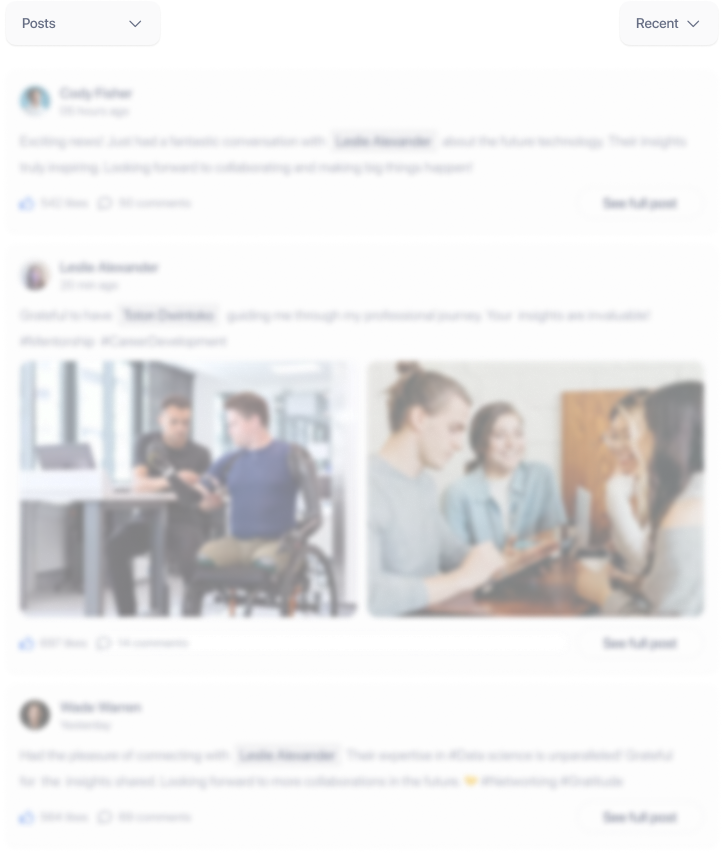