Larry Calabrese
Lead Tier 2 Engineer at CETech- Claim this Profile
Click to upgrade to our gold package
for the full feature experience.
Topline Score
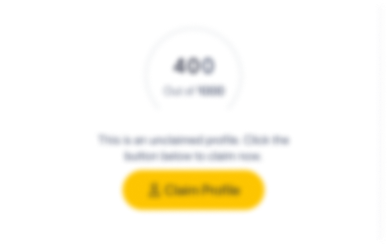
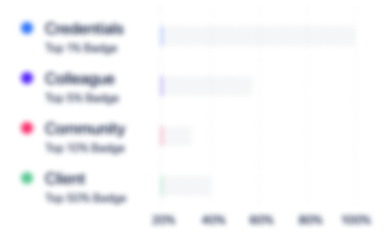
Bio


Experience
-
CETech
-
United States
-
IT Services and IT Consulting
-
1 - 100 Employee
-
Lead Tier 2 Engineer
-
2022 - Present
-
-
Desktop Support Engineer
-
2021 - 2022
-
-
-
Thomson Industries, Inc
-
United States
-
Automation Machinery Manufacturing
-
200 - 300 Employee
-
Test Engineer
-
2018 - 2019
Duties• Develop assembly and test equipment using LabView and PLC’s.• Fully support all assembly, CNC, maintenance, and test equipment for Amherst and St. Kitts facilities.• Develop preventative maintenance schedule along with required spare parts requirements.• Train maintenance associates for proper preventative maintenance and repair of equipment.• Work with Manufacturing to generate continuous process improvement and integrate with test equipment.• Maintain ISO9000 and AS9100 standards.Key Successes• Achieved >98% uptime on all End of line test stands within two months of employment.
-
-
-
Moog Inc.
-
United States
-
Aviation and Aerospace Component Manufacturing
-
700 & Above Employee
-
Test Engineer
-
2018 - 2018
Duties• Assigned to Commercial Aircraft; testing high precision electro-mechanical and electro-hydraulic devices. • Set up, perform, direct, oversee, and troubleshoot electrical, mechanical, and environmental tests.• Measure, record, and analyze test data with minimum error and maximum efficiency.• Writing and modifying test procedures, reports, justification documents, and work instructions.• Interface with customers to determine test requirements and methods.• Responsible for maintaining test schedule.
-
-
-
ITT Enidine
-
United States
-
Aviation & Aerospace
-
1 - 100 Employee
-
Manager, Test Engineering
-
2016 - 2017
Duties• Supervised a team of engineers and technicians engaged in hardware test and qualification activities for aerospace, industrial, military, vibration, shock, and noise dampening systems.• Developed test protocols to measure the functionality and integrity of products, including development of test procedures and test equipment to assess product performance and reliability.• Evaluated the ability of products to meet performance specifications and all other customer requirements. • Responsible for scheduling and assessing staffing needs.• Managed the engagement and coordination of external laboratories.• Participated in the preparation of proposals seeking new business or Research and Development activities.Key Successes• Identified and promoted key employee which led to a 40% increase in throughput on crucial product line.• Proposed and accomplished a capital improvement plan reducing outside vendor costs by $5000 per month.
-
-
Test Engineer
-
2013 - 2017
Duties• Scheduled and executed all R&D testing while supporting Test Technicians.• Designed test equipment, instrumentation, and fixtures required to test and qualify products.• Coordinated all activities concerned with text fixtures, scheduling, cost, and resolving test issues.• Responsible for maintaining all test stands and ensuring peak performance.• Helped establish and write Test Plans, Test Procedures, Test Reports, and Operator Manuals.• Worked with Design and Manufacturing to review and validate product test fixtures, setups, and results.Key Successes• Integral part of obtaining new long-term contracts in the aerospace industry.• Reduced test time on a high-volume product leading to $3000 per month labor savings.• Continually implementing lean manufacturing practices wherever possible.
-
-
-
MGA Research Corporation
-
United States
-
Automotive
-
100 - 200 Employee
-
Test Engineer
-
2011 - 2013
Duties• Performed technical testing services for aerospace, automotive, and battery industries.• Responsible for initial customer contact, proposals, testing, data acquisition, analysis, and writing technical reports for electrical, vibration, shock, pyrotechnic shock, and environmental testing.• Led projects from conception to evaluation, including design, manufacturing, testing, and revisions.• Designed and coordinated new equipment and fixtures. Provided feedback to the fabrication facility to improve future designs and projects.• Proficient with many standards, including ISO, MIL, SAE, UL, and UN.Key Successes• Designed new pyroshock simulation systems, decreasing test time while increasing accuracy and repeatability.• Designed and coordinated construction of a new pyrotechnic shock laboratory, increasing potential revenue by 50% and leading to increased customer confidence and comfort.• Took over all mechanical equipment and fixture design within 2 months, increasing job turn-around time and reducing workload on Fabrication facility by 20%.
-
-
-
-
Customer Service Engineer
-
2010 - 2011
Duties• Ensured 95% uptime by monitoring equipment, troubleshooting, and resolving issues in a timely manner.• Interpreted and utilized technical documentation, schematics, and machine data logs to solve complex mechanical and electrical problems.• Daily reports to senior company management including the President and Vice President of Operations.• Accurately controlled inventory and level settings for proper replenishment of parts, tools, and equipment.Key Successes• Promoted to Lead Engineer in less than 6 months.• Redesigned daily site and maintenance reports, providing a higher level of detail and readability.
-
-
-
University at Buffalo
-
United States
-
Higher Education
-
700 & Above Employee
-
Senior Consultant
-
2007 - 2010
Duties• Provided technical support and troubleshot with customers over the phone, through email, and in person.• Ensured customer service quality regulations were achieved by reviewing and grading previous tracks, as well as following up on unsolved issues and unsatisfied customers. Duties• Provided technical support and troubleshot with customers over the phone, through email, and in person.• Ensured customer service quality regulations were achieved by reviewing and grading previous tracks, as well as following up on unsolved issues and unsatisfied customers.
-
-
-
Applebee's Neighborhood Grill + Bar
-
United States
-
Restaurants
-
700 & Above Employee
-
Line Cook
-
2005 - 2007
-
-
Education
-
University at Buffalo
Bachelor of Science (B.S.), Mechanical Engineering
Community
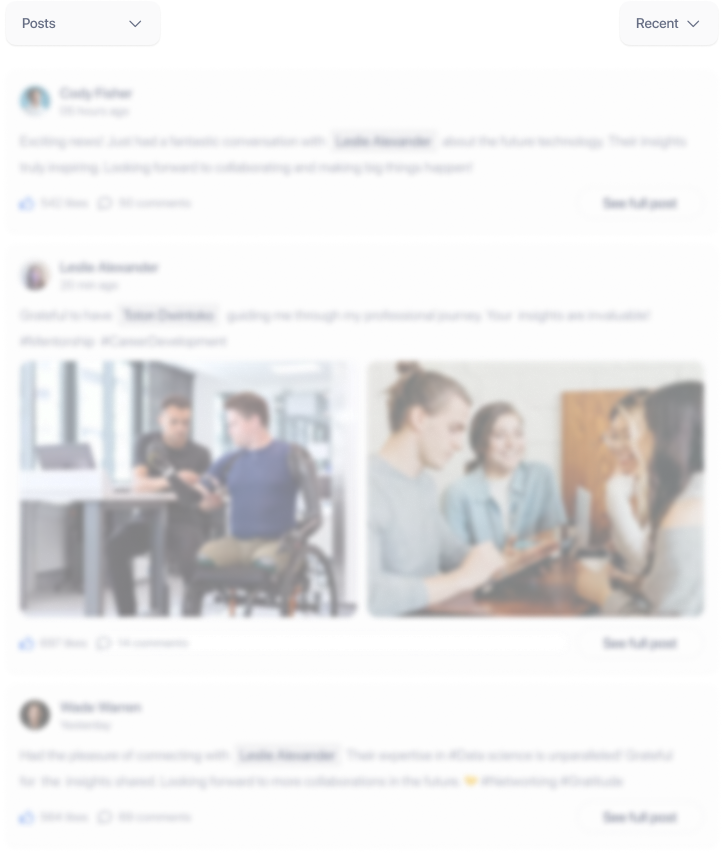