Dean O'Connor
Operations Manager at Wesbeam- Claim this Profile
Click to upgrade to our gold package
for the full feature experience.
Topline Score
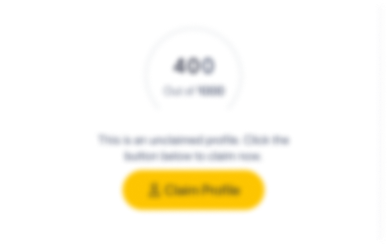
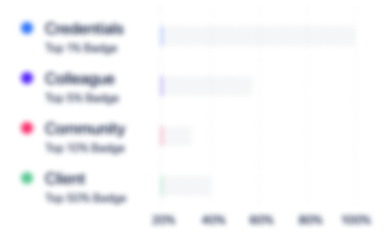
Bio

Gavin Connaughton
Dean conducted his work in a detailed and professional manner ensuring that both safety and product quality was never compromised.

Joanne Egan
Dean has displayed a commitment to improving safety and environmental management in his business.

Gavin Connaughton
Dean conducted his work in a detailed and professional manner ensuring that both safety and product quality was never compromised.

Joanne Egan
Dean has displayed a commitment to improving safety and environmental management in his business.

Gavin Connaughton
Dean conducted his work in a detailed and professional manner ensuring that both safety and product quality was never compromised.

Joanne Egan
Dean has displayed a commitment to improving safety and environmental management in his business.

Gavin Connaughton
Dean conducted his work in a detailed and professional manner ensuring that both safety and product quality was never compromised.

Joanne Egan
Dean has displayed a commitment to improving safety and environmental management in his business.

Experience
-
Wesbeam
-
Australia
-
Wholesale Building Materials
-
1 - 100 Employee
-
Operations Manager
-
Apr 2021 - Present
-
-
-
-
Retail Trader - Equities and Options
-
Mar 2020 - Sep 2021
-
-
-
-
Operations Manager
-
Feb 2019 - Mar 2020
• Improved lead times by up to 58% from 12 days to an average of 5 days within 7 months. • Developed and implemented Q.A processes across all departments with a drop in remakes / recoats by over 9.6% (9.9% to 0.3% within 3 months). • Increased throughput by 73% to date. • Developed departmental accountabilities to ensure key indicators where measurable and addressed accordingly. • Implemented toolbox meetings to drive priorities and allow staff to communicate directly to management in a formal setting. • Reached budget 10 out of the 12 months to date (first time for the company after 2.5 years operation) • Developed then Introduced a preventative maintenance schedule and accountabilities using TPM principles. • Renegotiated supplier contracts for Waste Management (23% saving in costs), Pallet Supply (25.6% saving in costs) Carton supply (17.8% saving in costs). • Plus, many other initiatives that I would love to discuss with you.
-
-
-
-
Operations Manager
-
Apr 2018 - Aug 2018
Operations Manager Operations Manager
-
-
-
Nikpol
-
Building Materials
-
1 - 100 Employee
-
Queensland Operations Manager Nikpol Pty Ltd
-
Aug 2013 - Apr 2018
• Project managed Nikpol from a warehouse facility in Virginia to a new site in Banyo, this included but was not limited to ALL infrastructure, including IT equipment, office setup and layout, racking and new machinery for the new production venture. • Project managed the business from a warehouse operation of 22 staff to a fully operational production / warehouse facility with 52 staff manufacturing benchtops for Trade, KWB, Kitchen Connection and Bunnings Australia for the first time in Queensland for Nikpol. Within my 5 years at Nikpol, Queensland has become the largest producer of manufactured benchtops in Australia, producing on average 250+ metres of high gloss and Egger benchtops per day for the Qld and NSW markets. • Increased delivery efficiencies (from 3 drops/hr to over 6+ drops/hr) by utilising new loading techniques, developing a comprehensive delivery schedule from Translogic and opening efficient communication lines from driver, to base to customer. • Used a program called fleet seek to monitor, report and improve our delivery processes. • Worked closely with our customers to ensure we could deliver their hardware needs if they were out on site. See more on resume
-
-
-
HMI
-
Australia
-
Manufacturing
-
1 - 100 Employee
-
Operations Manager
-
Oct 2012 - Jun 2013
• Managed all activities across the Workshop, CNC Machine Shop and Warehouse. • Introduced ISO 9001 into the business. • Implemented Workplace Health and Safety systems across the business in Brisbane, Sydney and New Zealand. • Managed the installation of new equipment including a 500kg Jib Crane from Dowrie Cranes. • Introduced a new live scheduling system. • Reconfigured the warehouse to make it more efficient and introduced new warehousing management processes. • Negotiated a new packaging contract with pallet express at a savings of 18% PA (aprox $70,000).
-
-
-
Bluescope Lysaght (B) Sdn Bhd
-
Construction
-
1 - 100 Employee
-
Branch Supervisor
-
Mar 2012 - Oct 2012
• Organise the day to day running of the branch to meet DIFOT requirements. • Manage the daily scheduling directly with the CSO’s. • Co-ordinated all the maintenance requirements across all machines (roll-formers, cranes and forklifts). • Manage safety on the site to maintain zero harm. • Ensured we were meeting all customer requirements with regard to quality across all departments. • Organise the day to day running of the branch to meet DIFOT requirements. • Manage the daily scheduling directly with the CSO’s. • Co-ordinated all the maintenance requirements across all machines (roll-formers, cranes and forklifts). • Manage safety on the site to maintain zero harm. • Ensured we were meeting all customer requirements with regard to quality across all departments.
-
-
-
Amcor
-
Switzerland
-
Packaging and Containers Manufacturing
-
700 & Above Employee
-
Operations Manager - Queensland
-
Feb 2011 - Oct 2011
• Re-negotiated the delivery contract with Kings International with a cost savings to the business of aprox. $18,000/mth by negotiating a flat rate of $47:00/hr (inclusive fuel levy and insurance) from $60:00/hr, which also included Kings taking responsibility of any damaged goods during delivery.• Re-negotiated the natural gas contract with Origin Energy, dropping the business cost of liquid gas from $1:20/ltr to $0:72/ltr (40%) and their 18kg cylinder (forklift) costs from $52:00/exchange to $26:00/exchange with a projected savings of aprox $200K pa.• Managed the HR process and ALL manufacturing staff (52 Staff across five departments – Extrusion, Printing, Converting, Warehouse and the Operations Office).•Managed inventory and warehousing and improved DIFOT through introducing sign in/out processes for all incoming/outgoing goods, used lean warehousing technique’s (Kanban) to optimize warehouse space.•Introduced allocated areas for receivable goods and introduced quarantine processes to ensure cost optimization and to ensure transparency across the business. • Introduced an injury management process aligned with WH&S Queensland and mentored the managers on the critical steps and responsibilities required to manage and monitor corrective actions associated with injuries.• Managed new equipment coming into the country and help with the installation and production planning.• Managed and monitored union activity as the AWU started to look into the business.
-
-
Workflow Specialist
-
Sep 2010 - Feb 2011
• Updated Aperio’s safety management system and aligned all relevant documentation to the current standards.• Introduced Finished Product specifications and Conformance certificates as Aperio took on more and more food companies for business opportunities.• Managed all Aperio’s training requirements (Manual handling, fire safety, front line management etc.)• Trained and became Aperio’s F.S.A (Fire Safety Advisor).• Worked closely with operations, sales, logistics and maintenance teams with a key focus on process improvement opportunities, mentoring change and safety responsibilities.• Introduced regular toolbox, quality and maintenance meetings to the business.
-
-
-
-
Operations Manager - Queensland
-
Oct 2009 - May 2010
·Lead a team that successfully instigated a complete Q.A program with a 50% reduction in errors over a 3-month period. ·Cross-trained staff across all departments to help build a multi-skilled team to help with downtime losses. ·Improved the scheduling process to highlight “delivery promise” dates to help prioritize customer orders. ·Improved the Customer Service relationship through regular feedback to operations/customer regarding errors to help build a continuous improvement focus. ·Lead a team that successfully instigated a complete Q.A program with a 50% reduction in errors over a 3-month period. ·Cross-trained staff across all departments to help build a multi-skilled team to help with downtime losses. ·Improved the scheduling process to highlight “delivery promise” dates to help prioritize customer orders. ·Improved the Customer Service relationship through regular feedback to operations/customer regarding errors to help build a continuous improvement focus.
-
-
-
-
Queensland Operations Manager
-
May 2006 - May 2009
Was instrumental in the development and implementation of a Green Field site at Ormeau, Queensland. Developed and implemented a complete visual management system including walkways, work ways, car parks, loading zones, exclusion zones etc. Was an integral part of the development process for BlueScope Waters new venture into a newly designed tank, this included designing the - production flow process, the upgrade of the Ormeau sites main structure to hold the new Urban Liner Tank gantry system, and the training and staffing of the new line. Introduced a new paint process into Queensland to help with WH&S issues, as well as working closely with Phillro Industries to develop and implement a new paint booth and paint kitchen into the new site (the first of its type into the tank business). Introduced acrylic paint to the Queensland paint process to help with quicker dry times, thus expediting the delivery process and reducing quality issues pre and post delivery by over 50%. Introduced a complete quality system into the tank building process to help measure and track manufacturing issues. Developed and implemented the “Service Team” for external customer complaint issues. This helped us pin point quality/delivery issues that could then be presented to the team to help improve our processes. Built up and help implement into Queensland a new Injury Management/Safety system and registered BlueScope Water with Q-Comp and Health for Industries to help manage all workplace injuries with regard to AI, MTIFR, LTIFR reporting. Introduced a Safety Co-ordinator into BlueScope Water Queensland to help manage the safety system with a focus on continuous improvement possibilities. Introduced Safe Operating Procedures into Queensland with a focus on building a level based pay system. Lead other states in worlds best practice techniques and practices.
-
-
-
-
Senior Supervisor - Shed Consolidation/Store
-
May 2004 - May 2006
Introduced a new type of packaging into shed consolidation to help with branding and to ensure restricted access to critical components - component loss went down from 22% to 2% over 3 to 4 months. This worked in conjunction with the help of photos of the shed pack pre-wrapping so we where able to pin point missing items to confirm they where packed. Set up a labeling system for each shed pack to ensure clarity across loading/delivery with a 95% reduction in delivery failures. Streamlined shed consolidation through the introduction of the 5-S program – the 5 steps to lean manufacture/visual management – reducing packing times by one day. Worked closely with other BlueScope Lysaght sites across QLD to look at system improvement possibilities within shed consolidation. Introduced a numbering system within stores to ensure loading/delivery compliance with a reduction in delivery failures by 90%.
-
-
-
-
Production/Planning Manager
-
Jan 2004 - May 2004
Initiated a new “Sales to Dispatch” ordering system to cut down on misplaced orders. Completed an intensive staff restructure to help with O/Time excess to a saving of 150hrs for first month. Initiated an $8700 cost savings on Stretch wrap plus a 20% downgrade in losses due to damaged stock through transport for the month of January. Set up a new hierarchy structure for production to ensure productivity measures managed from a floor level to help with ownership. Planned all aspects of production to ensure orders delivered on time every time. Set up and ran daily and weekly management meetings to ensure core business needs meet. (i.e. Staffing, consumer inquiries, KPI’s etc…). Facilitated transport, for local and interstate deliveries.
-
-
-
Parmalat South Africa & Parmalat in Africa
-
Food & Beverages
-
700 & Above Employee
-
National Specifications Coordinator
-
Jan 2000 - Dec 2003
Helped set up and managed a national specifications database system utilizing MS Access and Adobe.Brought Victoria and NSW into the system to streamline the national process.Managed all mix, process and Finished Product Specifications.
-
-
Senior Production Coordinator – Soft Cheese operations
-
Mar 1999 - Jan 2000
Managed a base of 21 permanent and 8 casual staff over a 7-day rotating roster system.Implemented a multi skilled training regime to improve on lost time at a PA savings of $120K.Improved the shelf life of our cottage cheese giving us a national distributed product, first, by focusing on the cooling regime combined with an improved cleaning and sanitation program.
-
-
Production Coordinator – Yoghurt/UHT operations
-
Apr 1994 - Mar 1999
Coordinated a staff base of 57 permanent staff across all shift operations. Set up and facilitated a team focused on the improvement of our returns due to damaged bottoms on our UHT 1Ltr lines. (losses down from 22% to 6.5% within 6 months at a PA savings of $750K).n Set up and facilitated a continuous improvement team within both departments. The main objective being “unique eye’s, unique perception”, thus leading to a total productive maintenance program by utilising our senior machine operators for the weekly maintenance of our packaging machines and valve batteries. This gave us the opportunity to allow the fitters and electricians more time to focus on machine improvements and innovation, thus improving our machine efficiencies.
-
-
Community
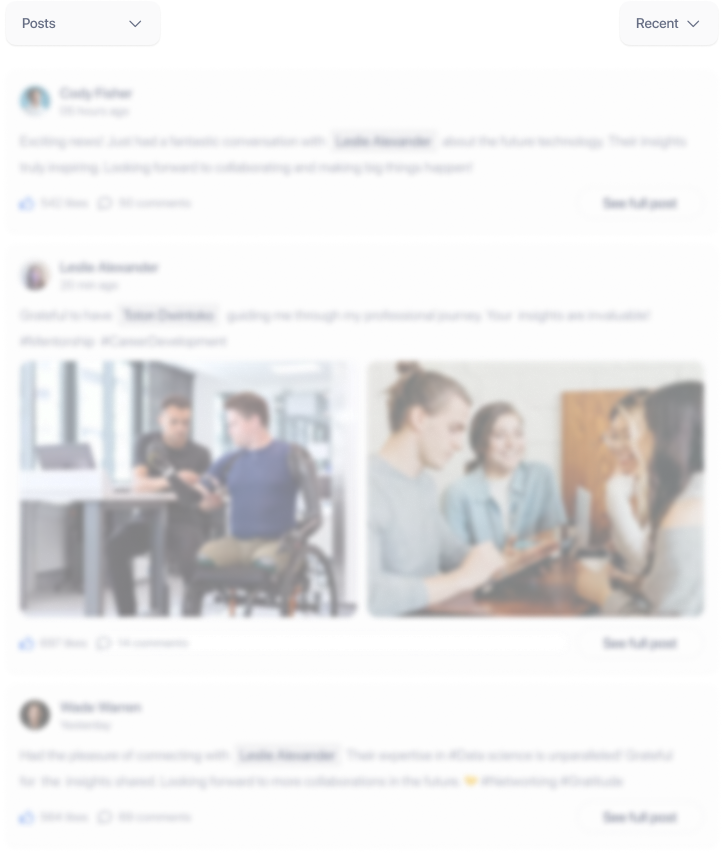