Senthil Raj Ramesh
Product and Plant Startup Manager at Mergon Group- Claim this Profile
Click to upgrade to our gold package
for the full feature experience.
Topline Score
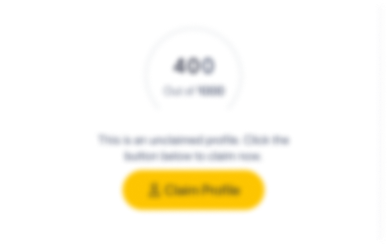
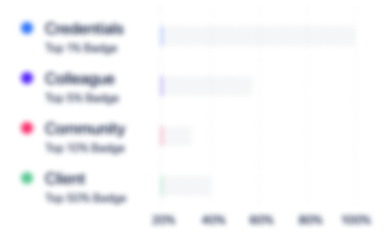
Bio


Experience
-
Mergon Group
-
Ireland
-
Plastics Manufacturing
-
200 - 300 Employee
-
Product and Plant Startup Manager
-
Sep 2022 - Present
Saltillo, Coahuila, Mexico Relocated to Saltillo, Mexico to lead and support the team in the successful startup of Mergon Groups brand new plastic blow molding factory in Mexico.
-
-
Technical Manager
-
Feb 2022 - Sep 2022
Anderson, South Carolina, United States - Currently manage and oversee a team of Engineers and Technicians on all engineering aspects of the plant from Manufacturing Engineers, Maintenance technicians, tooling engineers, automation technicians and Process technicians. - Major focus towards driving the team to achieve everyday production targets alongside overall plant and OEE improvement. - Manage and oversee all engineering aspects of new product implementations in the factory and smooth transition from project management… Show more - Currently manage and oversee a team of Engineers and Technicians on all engineering aspects of the plant from Manufacturing Engineers, Maintenance technicians, tooling engineers, automation technicians and Process technicians. - Major focus towards driving the team to achieve everyday production targets alongside overall plant and OEE improvement. - Manage and oversee all engineering aspects of new product implementations in the factory and smooth transition from project management team to production team.
-
-
Acting Technical Manager
-
Jul 2021 - Feb 2022
Anderson, South Carolina, United States
-
-
Manufacturing Engineer
-
Aug 2019 - Aug 2021
Anderson, South Carolina Own and manage the full-scale operations of 8 blow molding machines in the plant in terms of production, quality, and continuous improvement Lead the manufacturing decisions involving design for manufacturing and equipment selection for various OEMs based on the design, suitability and cost involved Worked on multiple cycle time reduction projects; reduced the cycle time on one of the machines from 70 sec to 36 sec cycle time, which is now the fastest machine in the… Show more Own and manage the full-scale operations of 8 blow molding machines in the plant in terms of production, quality, and continuous improvement Lead the manufacturing decisions involving design for manufacturing and equipment selection for various OEMs based on the design, suitability and cost involved Worked on multiple cycle time reduction projects; reduced the cycle time on one of the machines from 70 sec to 36 sec cycle time, which is now the fastest machine in the plant Involved in robot-cut optimization/design projects for cycle time reduction to improve OEE and labor efficiencies Worked on the installation corrections on BMW X3 by changing the operation sequence, die profile and mold cooling improvement Independently resolved the BMW X3 warpage issue within 2 weeks, which was business critical for BMW reducing a 40% fail rate at the BMW assembly line Working as a single point of contact for supplier and vendor communication Designed and installed full-scale machine automation for HVAC ducts of 2021 Nissan Rogue and BMW X3 Supporting new product implementations by identifying issues in the early stage of the product
-
-
Engineering Intern
-
Feb 2019 - Aug 2019
Greenville, South Carolina Area Involved in the production and quality management of blow molded plastic components Worked on continuous improvement projects on the plant level Implemented part level barcode tracking and label verification systems to reduce logistic errors Performed root cause analysis (RCA) of quality/functional issues in the process – internal to Mergon as well as for customers Visit customer site to investigate failures and corelate them to the RCA understanding Performed work… Show more Involved in the production and quality management of blow molded plastic components Worked on continuous improvement projects on the plant level Implemented part level barcode tracking and label verification systems to reduce logistic errors Performed root cause analysis (RCA) of quality/functional issues in the process – internal to Mergon as well as for customers Visit customer site to investigate failures and corelate them to the RCA understanding Performed work study and time study for design of fixtures and assembly support devices which reduced operator fatigue and made the process easy and repeatable
-
-
-
Clemson University
-
United States
-
Higher Education
-
700 & Above Employee
-
Graduate Research Assistant
-
May 2018 - Aug 2019
Greenville, South Carolina Area United States Department of energy project May 2018-Nov 2018 Graduate Research Assistant Problem statement mentioned lightweighting the door module of a 2014 mid-size luxury SUV for the North American market by 42.5% My area of work involved focused on secondary structural components in the door, majorly the Outside mounted rear view mirror assembly (ORVM) assembly. Worked on benchmarking of the current design, understanding its functional requirements. … Show more United States Department of energy project May 2018-Nov 2018 Graduate Research Assistant Problem statement mentioned lightweighting the door module of a 2014 mid-size luxury SUV for the North American market by 42.5% My area of work involved focused on secondary structural components in the door, majorly the Outside mounted rear view mirror assembly (ORVM) assembly. Worked on benchmarking of the current design, understanding its functional requirements. Redesigned the entire ORVM assembly with a major focus on lightweighting and secondary focus on design simplification for improved manufacturability and assembly. Achieved a 30% weight reduction and a parts consolidation in the new ORVM design by up to 21%. Vacuum infused driver side door module prototype to check fit and functionality. Documented the research and experimental work performed on the project and it has been accepted to be published by the SAE. Experimental support for ongoing research in the university May 2018-Present Graduate Research Assistant Project involves resistive welding of thermoplastic materials for automotive structural applications. Work is structured around design of experiments to identify the optimum process parameters for welding. Conducted destructive testing of the welded sample coupons to identify and analyze the weld quality. Compared the weld method employed in the project with commercially available structural adhesive systems for multi-material joining. Conducted experiments to identify optimum curing conditions across various curing methods such as UV Curing and Thermal Curing of different matrix materials to form natural fiber composites. Show less
-
-
-
Sri Kannapiran Mills Ltd.
-
India
-
Textile Manufacturing
-
1 - 100 Employee
-
Project Intern
-
Dec 2015 - May 2016
Coimbatore Area, India Internship at Sri Kannapiran Spinning Mills, Coimbatore. Worked with the team on managing the logistics for the industry along with general learning of cotton yarn manufacturing. Implemented a colour based identification system to rectify an issue concerning frequent confusion between different grades of cotton yarn. (Dec’15-May’16)
-
-
-
Make A Difference
-
Civic and Social Organizations
-
300 - 400 Employee
-
Teaching volunteer and propel strategist
-
Apr 2012 - May 2016
Coimbatore, Tamil Nadu, India
-
-
-
L&T Technology Services
-
India
-
IT Services and IT Consulting
-
700 & Above Employee
-
Project Intern
-
May 2015 - Jul 2015
Coimbatore Area, India Internship at LARSEN & TOUBRO Precision Machining Centre, Coimbatore. Worked on process optimisation of high precision missile components to reduce overall lead time, with the strategy to minimise lead time for each part program in a way as to curtail overall lead time. The VERICUT software tool was used for optimised tool path calculation. (May’15-July’15)
-
-
-
-
In-plant Trainee
-
Dec 2014 - May 2015
Coimbatore Area, India
-
-
-
Baja Bhais - PSG Tech
-
India
-
Motor Vehicle Manufacturing
-
1 - 100 Employee
-
Technical team member and Driver
-
Mar 2014 - Feb 2015
Coimbatore Area, India SAE BAJA India 2015 March 2014-Feb 2015 Brake sub-system lead and driver Was part of the team that engineered and manufactured an All-Terrain vehicle (ATV) to compete on a nation-wide platform. Gained hands on experience while working on the design and fabrication of various automobile sub-systems. Designed the brake rotors and brake lines during my role as the brake sub-system lead. Was part of the vehicle testing and… Show more SAE BAJA India 2015 March 2014-Feb 2015 Brake sub-system lead and driver Was part of the team that engineered and manufactured an All-Terrain vehicle (ATV) to compete on a nation-wide platform. Gained hands on experience while working on the design and fabrication of various automobile sub-systems. Designed the brake rotors and brake lines during my role as the brake sub-system lead. Was part of the vehicle testing and validation team with an additional responsibility of being the team driver Achieved first position in maneuverability and suspension traction events at the dynamic testing at Pithampur, India. Show less
-
-
-
PSG College of Technology
-
India
-
Textile Manufacturing
-
700 & Above Employee
-
In-Plant trainee
-
Jul 2012 - Nov 2014
Coimbatore Area, India Production & Assembly of Submersible pumps, Open-well monoblock pumps and Motors. Production of PSG A124, A141 LATHE.
-
-
-
Maruti Suzuki India Limited
-
India
-
Motor Vehicle Manufacturing
-
700 & Above Employee
-
In-plant trainee
-
May 2014 - Jun 2014
Coimbatore Area, India Worked in the Automotive servicing and Body shop division of Maruti Suzuki. Investigated and worked on seven real-time accident reports during the two months’ internship timeline. Worked on benchmarking and validation of automotive sub-systems. Learned different automotive failure modes and how to fix them in real time.
-
-
Education
-
Clemson University
Master's degree, Automotive Engineering Technology/Technician -
PSG College of Technology
Bachelor of Engineering - BE, Production engineering
Community
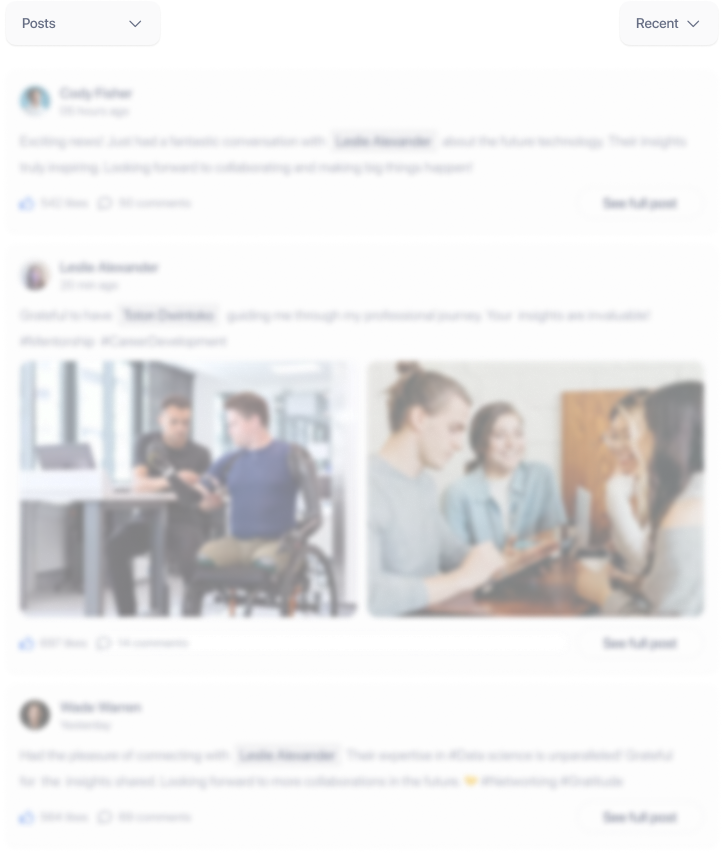