George J.
Product Manager at HYTORC- Claim this Profile
Click to upgrade to our gold package
for the full feature experience.
Topline Score
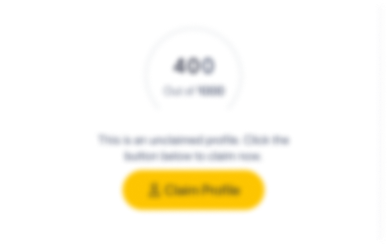
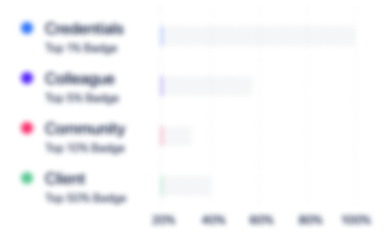
Bio


Experience
-
HYTORC
-
United States
-
Industrial Machinery Manufacturing
-
300 - 400 Employee
-
Product Manager
-
Jan 2023 - Present
-Maintain ownership and focus on assigned Hydraulic Pump and Tool product lines -Primary point of contact on assigned product lines, supporting customers, sales & customer service -Work closely with sales, marketing and management to pursue all sales opportunities. -Primary responsibility for product development prioritization, schedules, tracking and reporting -Develop new product requirement documents for products based on customer feedback, industry requirements and other inputs. -Develop business plans as needed to ensure viability. -Providing PM leadership to cross-functional teams in the development of new and improved products -Develop source material for input to product use and marketing documentation -Work closely with sales and marketing on product field testing -Maintain a current knowledge of relevant industry standards and competition -Develop and maintain technical and market expertise in products and markets Show less
-
-
-
PDI
-
United States
-
Medical Device
-
200 - 300 Employee
-
QC Compliance & Lab Excellence Manager
-
Mar 2022 - Aug 2022
a) QC/QA SME for business system projects i.e., ERP, LABWARE LIMS, Master Control etc.b) Coordinating with third-party testing labs on the project timelines and getting done the tasks on time.c) Creation of SOPS/WIs for new processesd) Supporting all the internal and external auditse) Supporting the analytical chemists on troubleshooting and knowledge transferf) Classroom training on all 3 shifts for major changes g) Process Improvements into more compliance and process optimizationh) Oversee planning of Finished Goods Testing to business priorities. i) Main communicator to business on the timing of completion of testing in the lab. j) Main QC stakeholder at weekly Issues Meeting.k) Managing and scheduling testing to 3rd party labs for both release and stability testing. Communication liaison to QA Data Review team concerning business priorities of review & release of Finished Goods.l) Integration of current processes to the new system(s)m) Historical LIMS Data reviewINTERIM QC LAB MANAGER Show less
-
-
Lead Chemist
-
Aug 2020 - Mar 2022
Distribute work load evenly between analysts and manage the timing of when releases are needed by working with production and planning and assure the accurate analysis of incoming raw materials, bulk liquids and finished products utilizing Standard Operating Procedures (SOPs), Work Instructions (WIs), Nice Pak's Test Methods (NPTM) and Good Laboratory Practices (GLPs) and Good Manufacturing Practices (GMPs). Assures tested raw materials, bulk liquids and finished products have met the required specification criteria prior to release. Investigate out of specification results to determine final disposition. Maintain accurate, complete and traceable documentation related to analysis and disposition of product/material. Maintain accurate, complete and traceable documentation related to analysis and disposition. Ensure the effective and efficient functioning of the Analytical Laboratory.Designate appropriate and trained personnel to perform required tasks. Review documentation to ensure adherence to internal and external requirements.Responsible for ensuring all projects are completed in a timely manner including but not limited to the annual product review (APR) reports and the stability testing of all products in the stability program.Responsible for the maintenance of the Laboratory Information Management System (LIMS). This includes but is not limited to ensuring that all specifications are up to date and in accordance with the document in the depository and additions of new functionality to LIMS. Show less
-
-
Quality Control Analyst III
-
Jan 2020 - Aug 2020
Ensures that the lab activities maintain compliance with current Good Manufacturing Procedures (cGMP) requirements at all times. Performs method transfer, method validation and/or special project assignments as assigned.Continuous Improvement of the lab (5S and Kaizen).Maintain accurate, complete and traceable documentation related to analysis and disposition. Ensure the effective and efficient functioning of the Analytical Laboratory by managing the calibrations/PMs of all equipment and instrumentation in the labOversee the inventory of supplies in the chemistry laboratory Manage the daily schedule of tasks along with the Lead Analytical Chemists to assign to the appropriately trained personnel. Oversee and update the Issues Meeting Report on a daily basis Ensure that all results are accurately recorded in the LIMS system with appropriate laboratory logs/forms reviewed as requiredReview all data generated by the laboratory associated with the manufacturing of Drug and OTC productsDocumentation review: Ensure that all results are accurately recorded in the LIMS system and review appropriate laboratory logs or other designated forms as required. Perform and complete investigations into laboratory Out of Specification Results (OOS) and submit reports for review by QAAssist with Annual Drug Product Review (APR) process.Ensure that all instruments that perform analysis are validated and calibrated.Troubleshoot instruments, lab equipment and ensure proper maintenance and calibration of all equipment and instrumentation. Keep equipment operating by certifying instrument performance; enforcing operating instructions; schedule preventive maintenance; arranging for repairs; planning equipment replacement.Work with the Lead Analysts to communicate and report updates and lot status to other departments in a timely manner. Assure Test Methods, SOPs, Material Specifications, etc. are up-to-date and manuals are current. Show less
-
-
Product Development Project Specialist
-
Apr 2019 - Jan 2020
This position is responsible for oversight of all aspects of the development and lifecycle of wet wipe products for many major brands. Involved at the first step of a project, throughout all the development and continue ongoing maintenance of the product throughout its maturation.Essential Functions And Basic Duties• New product development and product maintenance for assigned customers.• Develop timelines and obtain agreement with customer• Maintain a project tracker with list of deliverables• Responsible for requesting and coordinating key deliverables from other departments and support groups to meet customer requirements• Adherence to timeline agreed upon for project• Communicate deadlines to internal team members• All initial Bill of Materials (BOM’s)/Manufacturing Instructions (MI’s) and updates to BOMs/MIs for product lifecycle maintenance• Obtain item numbers, cost standards, and operational information such as number of operators, line speed, and efficiency• Main point of contact for R&D and Operations• Route deviations, as needed• Attend first production• Customer’s main point of contact—building and maintaining the relationship with assigned customers.• Providing regular updates on project status to the customer via written and verbal communication.• Review customer specifications and translate them into PDI documents and processes.• Troubleshoot any issues that arise with product development or ongoing production.• Line Trials• Draft and route trial protocols• Coordinate with Procurement to order trial materials• Hold pre-trial meetings with internal stakeholders• Host customers on-site for line trials• Post-trial disposition of samples and data. Show less
-
-
Product Development Project Coordinator
-
Apr 2018 - Apr 2019
-Supports development of new business by initiating all necessary activities, such as manufacturing trials and writing Manufacturing Instructions and Bills of Materials for production- On-site customer advocate, managing all workflow with internal support groups to ensure new products are manufactured within the customer’s timeline- Coordinating development of OTCs by successfully facilitating trials and validation batches for commercial production.- Development of brand new medical device wipe by coordinating with R&D on formulation, Operations on machine and packaging compatibility, and Regulatory Affairs to launch product within an aggressive timelineDirect Sales Support Activities-Assist customers in their planning and execution of new projects-Attend Sales Calls and participate in conference calls as needed-Act as home office representatives on the call, communicating feasibility -Facilitate communications and exchanges of information -Be the internal advocate for product development initiatives -Develop relationship with key account personnel in support of the new business Show less
-
-
Quality Control- Analytical Chemist I
-
Dec 2015 - Mar 2018
• Communicate with sourcing/procurment concerning vendor discrepancies. • Testing Raw liquid and Intermediate Bulk Liquid using state of Laboratory equipment such as GC, Specific Gravity, FT-IR, Karl Fisher Titration, UV-Vis, HPLC, etc. • Measurement, functionality, and tensile/seal strength testing for packaging component and applicator materials.• Work closely with Compounding Manager, and Production team to release raw materials and bulk liquids for use in production as close to timeline as possible. • Assist Validation Engineering Team in sampling and testing of residual APIs and cleaners for cleaning validation/verification of filling line and in-process batching equipment.• Work closely with the Contract Manufacturing team to achieve the standards of a drug and OTC production environment. • Changed/organized workflow steps of releasing material that decreased by 90%. • Managing the testing of materials through an internal Laboratory Information Management System (LIMS)• Sampling of raw material ingredients for consumer good, OTC, and NDA products. • Managing Release of raw materials for use on production floor through the internal Business Planning and Control System (BPCS).• Complete certificate of analysis (COA) for raw material testing and in-prcoess bulk batches.• General equipment maintenance trouble shooting and calibration of lab equipment. Show less
-
-
Quality Assurance Inpector
-
Mar 2015 - Dec 2015
• Audits product and production facility for assuring compliance to specifications, cGMPs, and cGDPs based from Bill of Materials (BOM) and Manufacturing Instructions (MI). • Initiate and document inspection results on production lines as per cGDPs.• Verifiy that reworked products conform to required specifications.• Review and finalize completion of liquid master batch records as per cGDPs. • Manage storage of retain samples from various production lines in the main QA Microsoft Excel Spreadsheet.• Assist in execution of validation protocol on line 69. • Assist Quality Supervisor in investigations into non conforming conditions including but not limited to an AQL inspection and root cause analysis.. • Initiate and document inspection results on production lines as per cGDPs. Show less
-
-
-
Starbucks
-
United States
-
Retail
-
700 & Above Employee
-
Shift Supervisor
-
Mar 2012 - Feb 2015
Shift supervisors at Starbucks stores assist the store manager during their scheduled shifts. This includes running the store during those shifts, helping baristas during busy times, training new employees and delegating tasks. According to the company, supervisors are responsible for "modeling and acting in accordance with Starbucks guiding principles." -Managed up to 5 employees at one given time in order for the team to act with integrity, honesty, and knowledge that promote the culture, values and mission of Starbucks. -Prepared store for unexpected EcoSure audits in order to abide to the Starbucks cleanliness and health code standards. -Coordinated with approved vendors for maintenance efforts for the expected standard operation of the store. -Trained new employees on operational standards as well new standards to current employees. Show less
-
-
-
Isolatek International
-
United States
-
Building Materials
-
100 - 200 Employee
-
R&D Technician
-
Mar 2009 - Sep 2010
• Evaluation of Wet Spray Fireproofing through testing physical properties, chemical properties, and high temperature conditions. • Created and updated SOPs for new and current R&D experiment methods. • Coordinated daily workload with R&D technicians in order to achieve project timeliness. • Part of NIST consortium experimentation of new testing method of heating analysis of cement and plaster based wet spray material. • Coordinated with Plant manager and Operations for R&D line trials. • Technical reporting and analysis of R&D formula batching and testing data. • Customer compliance quality testing • Designed and developed a 4 hour resistant plaster-based wet-spray product • Assist in conducting tests at Underwriter’s Laboratory for certification Show less
-
-
-
Polarome International, Inc.
-
United States
-
Chemical Manufacturing
-
1 - 100 Employee
-
Chemist
-
Oct 2007 - Feb 2008
• Performed lab scale distillation experiments • Executed Gas Chromatography tests • Performed lab scale distillation experiments • Executed Gas Chromatography tests
-
-
-
Sanofi
-
France
-
Pharmaceutical Manufacturing
-
700 & Above Employee
-
Principal Validation Specialist
-
May 2007 - Aug 2007
• Performed air quality testing • Oversaw the calibration of Honeywell environmental room monitoring system • Oversaw the repairing and maintenance for pharmaceutical equipment. • Involved a GMP Audit by the European Union Authorities for a Pharmaceutical Development Facility • Executed the USP Water System Performance Protocol • Initiated validation of Butterfly Valves • Performed air quality testing • Oversaw the calibration of Honeywell environmental room monitoring system • Oversaw the repairing and maintenance for pharmaceutical equipment. • Involved a GMP Audit by the European Union Authorities for a Pharmaceutical Development Facility • Executed the USP Water System Performance Protocol • Initiated validation of Butterfly Valves
-
-
-
Saint-Gobain Performance Plastics
-
United States
-
Plastics Manufacturing
-
700 & Above Employee
-
Quality Engineering Intern
-
May 2006 - Aug 2006
• Initiated tighter limits through Statistical Process Control in the production system using SPC 3000 software and Microsoft Excel with SPC Macros. • Tested different mechanical properties of product for assurance of design specifications • Introduced to Six Sigma Concepts • Initiated tighter limits through Statistical Process Control in the production system using SPC 3000 software and Microsoft Excel with SPC Macros. • Tested different mechanical properties of product for assurance of design specifications • Introduced to Six Sigma Concepts
-
-
Community
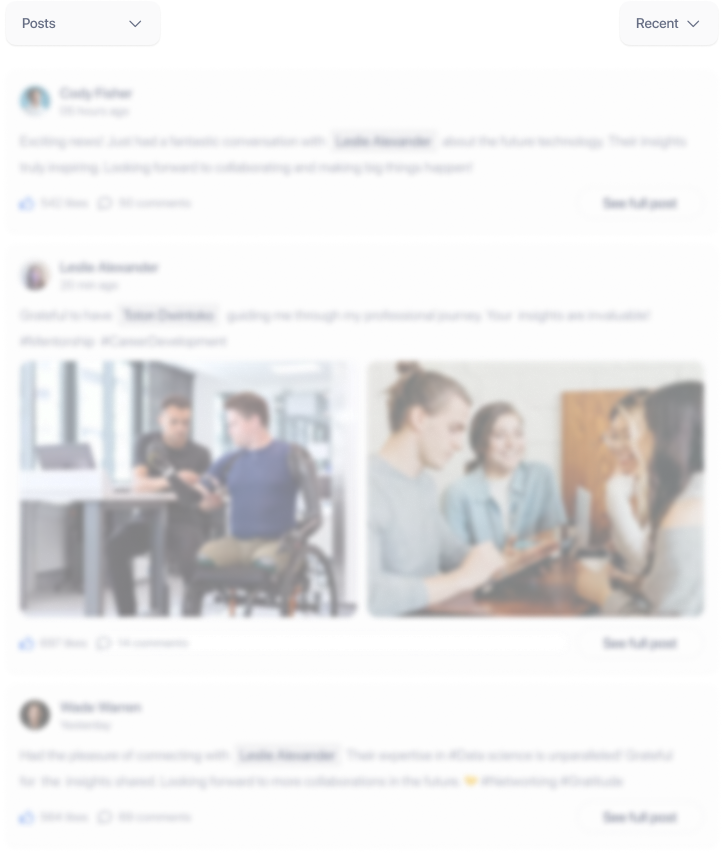