Andrew Spellman
Manufacturing Project Manager at Sigma Design, Product Design and Engineering- Claim this Profile
Click to upgrade to our gold package
for the full feature experience.
Topline Score
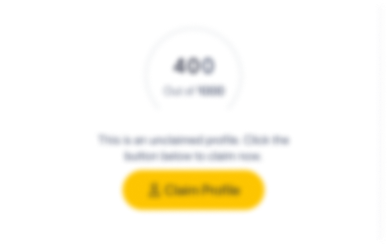
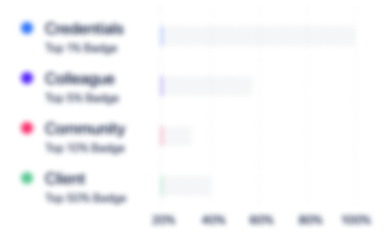
Bio


Credentials
-
Master Digital Transformation
LinkedInSep, 2020- Nov, 2024 -
Advance Your Skills as a Manager
LinkedInAug, 2020- Nov, 2024 -
Build and Manage Effective Teams
LinkedInAug, 2020- Nov, 2024 -
Develop Your Presentation Skills
LinkedInAug, 2020- Nov, 2024 -
Managing Others Effectively
LinkedInAug, 2020- Nov, 2024 -
Master Microsoft PowerPoint
LinkedInAug, 2020- Nov, 2024 -
Develop Your Data Analysis Skills
LinkedInJul, 2020- Nov, 2024 -
Develop Your Strategic Planning Skills
LinkedInJul, 2020- Nov, 2024 -
Improve Processes and Deliver Operational Excellence
LinkedInJul, 2020- Nov, 2024 -
Manage Change and Develop Your Adaptability Skills
LinkedInJul, 2020- Nov, 2024 -
Managing Performance
LinkedInJul, 2020- Nov, 2024 -
Become a Data Scientist
LinkedInJun, 2020- Nov, 2024 -
Certified SolidWorks Professional (CSWP)
Dassault SystèmesFeb, 2018- Nov, 2024
Experience
-
Sigma Design, Product Design and Engineering
-
United States
-
Design Services
-
200 - 300 Employee
-
Manufacturing Project Manager
-
Jan 2021 - Present
• Lead multidisciplinary project teams in new product introduction of complex electromechanical devices. • Manage communications, coordinate activities with all internal and external stakeholders, and maintain scope, schedule, and budget for multiple concurrent projects ranging in magnitude from several weeks at tens of thousands of dollars to multiyear, multimillion dollar engagements. • Proactively identify and mitigate project risks involving design requirements, quality, schedule, and budget. • Drive continuous improvement initiatives for both internal and client processes involving process engineering, quality, supply chain management, inventory control, risk management, data collection and analysis, and KPIs and metrics. • Developed, implemented, and provided training on multiple internal tools for financial and production data collection and analysis. Advised on department KPIs and developed automated processes for tracking and reporting them. • Act as subject matter expert for new project quotes and new client development. Show less
-
-
-
Madstein, LLC
-
United States
-
Leasing Non-residential Real Estate
-
Member
-
Jan 2012 - Present
Assist managing members in operations and expansion of an industrial real estate portfolio. Typical duties include inspecting and evaluating potential new acquisitions, working with tenants to ensure completion of necessary repairs and maintenance, evaluating potential building upgrades, and showing open units to prospective tenants. Also assist in reviewing and updating lease agreements, insurance policies, and acquisition documents as necessary. Assist managing members in operations and expansion of an industrial real estate portfolio. Typical duties include inspecting and evaluating potential new acquisitions, working with tenants to ensure completion of necessary repairs and maintenance, evaluating potential building upgrades, and showing open units to prospective tenants. Also assist in reviewing and updating lease agreements, insurance policies, and acquisition documents as necessary.
-
-
-
ALASIS, LLC
-
Eugene, Oregon Area
-
Principal Consultant
-
Apr 2018 - Dec 2020
Consulting with local heavy manufacturing businesses to provide guidance on data collection and analysis, business strategy, product development, supply chain management, and lean manufacturing. Consulting with local heavy manufacturing businesses to provide guidance on data collection and analysis, business strategy, product development, supply chain management, and lean manufacturing.
-
-
-
Scientific Developments, Inc.
-
United States
-
Wholesale
-
1 - 100 Employee
-
Division General Manager
-
Apr 2012 - Mar 2018
• Advised C-suite and board as industry expert on division market segment. • Led an initiative to transition from an accounting-only software package to a full-featured ERP system while simultaneously changing from a cash flow accounting system to a GAAP-compliant standard cost system. • Directed all operations for two factories with 32 total employees, including full responsibility for P&L budgeting and forecasting, sales and operations planning, new product introduction, and business development. • Updated company policies, improved training techniques, and led company culture improvement efforts, resulting in a 75% decrease in operator turnover and a reduction in average training time from 6 to 2 weeks. • Updated IT infrastructure and implemented an array of office digitization and automation processes, reducing office and personnel expenses per revenue dollar by 50% and eliminating 90% of printed paperwork. • Developed data-driven forecasting procedure and standardized production cells to cut finished good inventory per dollar of revenue by 50% while simultaneously decreasing the average lead time on custom products from 3 weeks to 2 days. • Decreased WIP and raw material inventory by 20% with no impact to customer service levels through MRP analysis improvements, process standardization, SKU rationalization, and WIP optimization. • Designed custom equipment, facility layout, and production scheduling methods to maximize efficiency and flexibility for manufacturing and maintenance. Results of this effort included: o Reduced typical tool changeover time from 3 hours to 15 minutes. o Increased production cell productivity per square foot by 400%. o Reduced total required factory labor by 10% through redesign of factory material handling system. o Decreased required spare parts inventory levels by 80% while maintaining an equipment uptime of over 98%. Show less
-
-
-
Yakima Products
-
United States
-
Sporting Goods Manufacturing
-
1 - 100 Employee
-
Manufacturing Engineer
-
Nov 2010 - Mar 2012
• Engineering and technical resource for moving approximately 50 products and 400 unique SKUs worth $50M in annual sales from factory in Mexico to China. • Teamed with Customer Service and Quality department to identify and address customer quality complaints, including managing all technical aspects for three product recalls. • Developed in-house incoming inspection test procedures and fixtures for all subcontracted components (mainly fasteners) based on international standards and a comprehensive set of design-for-manufacturing criteria for all major manufacturing processes (injection molding, welding, punching, casting, etc). • Reviewed all new product designs at every component level to ensure manufacturability at target price point. • Worked with Testing and Quality to evaluate all alpha, beta and first article samples for design requirement compliance and updated component design and/or manufacturing processes as necessary to comply. Show less
-
-
-
GERBER
-
United States
-
Manufacturing
-
100 - 200 Employee
-
Manufacturing & Sourcing Engineer
-
Jan 2009 - Nov 2010
• Primary engineer and technical resource for approximately $10M existing annual sales plus 20 new products over three product categories (Flashlights, Portable Power, and Camping). • Increased manufacturing capacity both in-house and with outside vendors to meet 5x growth in sales forecast for government and military orders in less than a year. • Acquired $450k in capital equipment to support above growth, including identifying machine manufacturers and models, negotiating prices, ordering, and managing installation. • Developed numerous MS Access database programs for tracking, reporting, and forecasting manufacturing scrap and consumables, resulting in a nearly 30% reduction in budgeting variance on affected items. • Developed comprehensive QA testing documents for first article inspection spanning all categories. • Identified and audited new suppliers (mostly in Asia, but also throughout North America and Europe) to meet internal pricing, quality, and lead-time requirements. • Evaluated new and existing suppliers' quality, manufacturing capabilities, and delivery performance before providing recommendations on awarding new products or transferring existing ones. • Negotiated pricing and terms for new and transferred products with vendors. • Placed and tracked POs for all tooling and samples necessary for new and transferred products through product load-in. Show less
-
-
-
Concept Systems Inc
-
United States
-
Automation Machinery Manufacturing
-
1 - 100 Employee
-
Engineering Intern
-
Mar 2008 - Sep 2008
Designed, built, and tested a dual cylinder hydraulic test stand for RMCTools and hydraulic tuning training of new employees. Responsible for thermal and mechanical design of several small enclosures for a military project. Aided in testing and debugging several customer-specific projects before final approval. Designed, built, and tested a dual cylinder hydraulic test stand for RMCTools and hydraulic tuning training of new employees. Responsible for thermal and mechanical design of several small enclosures for a military project. Aided in testing and debugging several customer-specific projects before final approval.
-
-
-
GERBER
-
United States
-
Manufacturing
-
100 - 200 Employee
-
Engineering Intern
-
Apr 2007 - Sep 2007
Communicated with suppliers to resolve production issues, developed test procedures for both new and existing products, conducted Quality Assurance benchmarking for new products, and executed engineering drawing changes. Communicated with suppliers to resolve production issues, developed test procedures for both new and existing products, conducted Quality Assurance benchmarking for new products, and executed engineering drawing changes.
-
-
Education
-
University of Oregon - Charles H. Lundquist College of Business
Master of Business Administration - MBA, Advanced Strategy and Leadership -
Oregon State University
BSME, Mechanical Engineering -
Oregon Institute of Technology
Mechanical Engineering Technology, Manufacturing Engineering Technology
Community
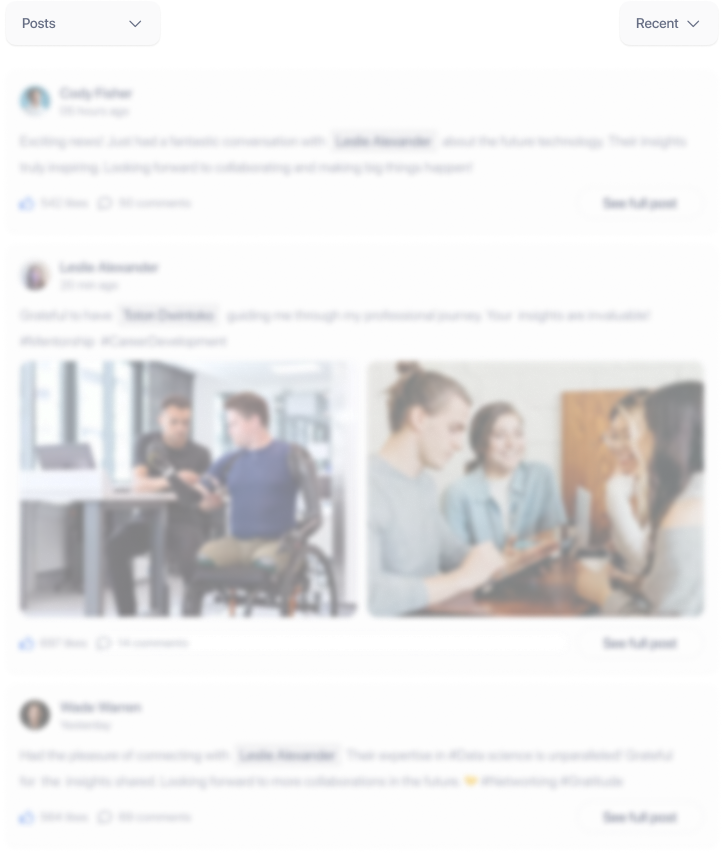