Daniel Warman, MBA
Senior Manager, Supply Chain Operations at Medable, Inc- Claim this Profile
Click to upgrade to our gold package
for the full feature experience.
Topline Score
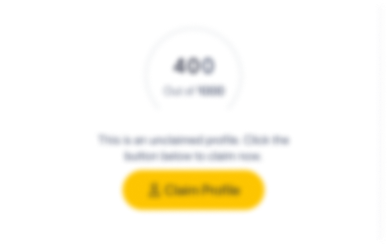
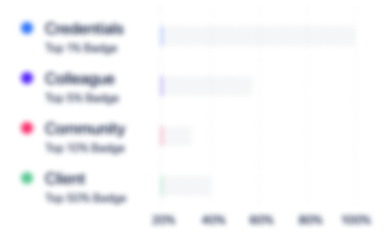
Bio

David McBean LSS BB
Dan was assigned as my Mentor during his time at B&W. In the years since I have always found Dan to be very open, knowledgeable and a true inspiration. His insights in personal and professional development and his willingness to share his experiences in that respect were a huge boost to my career plans and goals. Over the years, Dan has worked with me to development my skills and abilities which aided in my developing a stronger personal brand and professional network. I would highly recommend Dan for any leadership position with any organization as his leadership skills will benefit any team or individual who has the pleasure of working with him.

Bryan Schenkenberger
Dan is a hard worker and really driven by process improvement. He focuses on ways to help the company save money and improve processes to become more efficient and economic. He is always willing to put in the work and ask the difficult questions to drive to the root cause of an issue and help develop the proper solution to improve future operations. Dan comes highly recommended.

David McBean LSS BB
Dan was assigned as my Mentor during his time at B&W. In the years since I have always found Dan to be very open, knowledgeable and a true inspiration. His insights in personal and professional development and his willingness to share his experiences in that respect were a huge boost to my career plans and goals. Over the years, Dan has worked with me to development my skills and abilities which aided in my developing a stronger personal brand and professional network. I would highly recommend Dan for any leadership position with any organization as his leadership skills will benefit any team or individual who has the pleasure of working with him.

Bryan Schenkenberger
Dan is a hard worker and really driven by process improvement. He focuses on ways to help the company save money and improve processes to become more efficient and economic. He is always willing to put in the work and ask the difficult questions to drive to the root cause of an issue and help develop the proper solution to improve future operations. Dan comes highly recommended.

David McBean LSS BB
Dan was assigned as my Mentor during his time at B&W. In the years since I have always found Dan to be very open, knowledgeable and a true inspiration. His insights in personal and professional development and his willingness to share his experiences in that respect were a huge boost to my career plans and goals. Over the years, Dan has worked with me to development my skills and abilities which aided in my developing a stronger personal brand and professional network. I would highly recommend Dan for any leadership position with any organization as his leadership skills will benefit any team or individual who has the pleasure of working with him.

Bryan Schenkenberger
Dan is a hard worker and really driven by process improvement. He focuses on ways to help the company save money and improve processes to become more efficient and economic. He is always willing to put in the work and ask the difficult questions to drive to the root cause of an issue and help develop the proper solution to improve future operations. Dan comes highly recommended.

David McBean LSS BB
Dan was assigned as my Mentor during his time at B&W. In the years since I have always found Dan to be very open, knowledgeable and a true inspiration. His insights in personal and professional development and his willingness to share his experiences in that respect were a huge boost to my career plans and goals. Over the years, Dan has worked with me to development my skills and abilities which aided in my developing a stronger personal brand and professional network. I would highly recommend Dan for any leadership position with any organization as his leadership skills will benefit any team or individual who has the pleasure of working with him.

Bryan Schenkenberger
Dan is a hard worker and really driven by process improvement. He focuses on ways to help the company save money and improve processes to become more efficient and economic. He is always willing to put in the work and ask the difficult questions to drive to the root cause of an issue and help develop the proper solution to improve future operations. Dan comes highly recommended.

Credentials
-
AgilePM® Foundation
Baldwin Wallace UniversityJan, 2021- Nov, 2024 -
Six Sigma Green Belt
Honeywell
Experience
-
Medable, Inc
-
United States
-
Software Development
-
300 - 400 Employee
-
Senior Manager, Supply Chain Operations
-
Oct 2022 - Present
Lead Supply Chain, Procurement, and Forecasting initiatives to build and optimize processes for Client and Participant delivery of handheld devices and Bluetooth Medical Equipment, for Remote & Digital clinical trial data capture.
-
-
Global Supply Chain & Vendor Manager
-
Oct 2020 - Oct 2022
• Manage Medable's client delivery supply chain end-to-end to ensure that items arrive at the client's destination on-time, every time.• Partner with vendors, subcontractors, and partners to deliver a seamless service to Medable's clients.• Identifying and implementing improvements to processes and procedures, while eliminating process bottlenecks and implementing solutions in a timely manner.• Developed Medable’s first “Vendor Management Council” and Vendor assessment process, to ensure business fit and alignment.
-
-
-
Kent State University
-
United States
-
Higher Education
-
700 & Above Employee
-
Adjunct Professor
-
Aug 2014 - Present
I design and deliver innovative and engaging classes for the College of Aeronautics and Engineering (CAE) graduate and undergraduate students, covering a range of subjects including Lean Six Sigma Tools & Applications, Project Management in a Technological Environment, Quality Systems, Ethics, Technology & the Environment, and Facilities Design for Material Handling. I design and deliver innovative and engaging classes for the College of Aeronautics and Engineering (CAE) graduate and undergraduate students, covering a range of subjects including Lean Six Sigma Tools & Applications, Project Management in a Technological Environment, Quality Systems, Ethics, Technology & the Environment, and Facilities Design for Material Handling.
-
-
-
Babcock & Wilcox
-
United States
-
Renewable Energy Power Generation
-
700 & Above Employee
-
Project Procurement Manager / Process Improvement Specialist
-
Jan 2019 - Nov 2020
Here, I play an integral strategic role, steering procurement, coordination, and management for “key” Boiler projects, between the Supply Chain organization, Proposal/Project Management, and Engineering organizations, throughout the project lifecycle. I deliver tactical expertise and strategic leadership to ensure a coherent approach and transition, and adherence to schedules and budgets.➥ Optimized supply chain efficiency for FM Package Boiler product line, liaising with internal partners, and external vendors and suppliers to establish and ensure all supply chain functions, materials, and fabricated components align with quality and project schedules, while securing cost-efficiency.➥ Defined and executed strategies and initiatives to streamline the supply chain and deliver cost savings, protecting and enhancing product revenue and profit margin.➥ Maintained project procurement schedule and plan for 8 FM boiler projects simultaneously, making sure critical path items were resolved quickly and easily, and ensuring the meeting of internal and external customer timing.➥ Successfully implemented a cost reduction initiative for the FM Package Boiler Product Line, by steering development and execution of an inventory plan to enable low cost region sourcing delivering a $20K/unit cost-saving, equating to $200K annually.➥ Resolved a business-critical supplier bottleneck, as well as driving annual cost savings, for the FM Package Boiler product line by Identifying, developing, and implementing 2 pressure vessel suppliers in Mexico, (the company’s first new pressure vessel supplier approved in 20 years).
-
-
Global Strategic Material Leader
-
2018 - 2019
In this role, I advanced to a newly created position at the Copley, OH facility (a warehouse for the global parts and service business), reporting directly to the VP of Supply Chain. I was tasked with creating and steering the implementation of strategies to improve inventory turns, optimize inventory scheduling, and reduce lead time to source after the order is made.➥ Worked collaboratively with Product Line Directors and Business Leaders in Value Stream Mapping for entire Global Parts and Service business and facilitated identifying the top 5 opportunities for the business on sales growth and inventory accuracy. ➥ Formulated a plan on how to impact the bottom line, successfully identifying an opportunity to shift 20% of inventory from obsolete and low turn to current and high demand inventory. ➥ Implemented a process to capture customer feedback on orders lost to identify the top 3-5 customer issues and solve those problems. ➥ Automated replenishment process to address a significant lead time slip between the time a requisition was submitted and material was ordered, saving 2-4 weeks of lead time per order.
-
-
Business Process Improvement Specialist
-
2017 - 2018
Here, I was recruited to provide leadership and strategic insight to guide continuous improvement across the business and enhance profitability. I served as a proactive member and key contributor of a high-performance cross-functional team, steering implementation of process improvement projects. I also identified process improvement opportunities, formulated solutions, and created and presented business cases, securing senior leadership approval. I planned and led system enhancements, including training employees, and ensuring post-launch compliance.➥ Steered multiple Implementation Teams to transform the Project Management Office procedures into Standard Work.➥ Utilized a range of strategies, methodologies, and tools, including Kaizen and rapid improvement events, to lead Human Resources in creating a Global process for Direct Hire and Temp recruiting.➥ Led RACI Analysis and development/delivery of training at multiple locations for new Proposal Process.➥ Designed and developed training plan, processes, and tools for an Engineering Standards Update process, successfully delivering program to 300+ engineers in 2 days.➥ Facilitated development and implementation of a new IP process, working in partnership with legal, the product management team, and IT to define business requirements, identify key stakeholders, define the process and information flow, and collaborated with IT on implementation, to cut the IP process lead time down by 27%.
-
-
-
US Acute Care Solutions
-
United States
-
Hospitals and Health Care
-
700 & Above Employee
-
Continuous Improvement Manager
-
2016 - 2017
In this position, I steered Lean Management System implementation and facilitation across the revenue cycle management value stream that averaged over 5 million visits per year. I planned and managed various continuous improvement initiatives such as Lean training programs, and Kaizen events, together with assessing, coaching, and providing constructive feedback to teams, to drive enhancement and strengthening of lean competencies and organizational development. ➥ Applied lean problem-solving methodology to effectively monitor existing and new business processes to identify improvement opportunities in performance, quality, delivery, and cost. ➥ Oversaw KPIs, Metrics, and Hourly reporting for compliance and utilization of the Lean Management System. ➥ Successfully managed the absorption of 170K additional unplanned visits, while elevating production by 50%, and lowering headcount by 4 for Electronic Records Processing, driving department inventory down by 1.5 days.
-
-
-
BDI
-
United States
-
Wholesale
-
700 & Above Employee
-
Director of U.S. Operations
-
2014 - 2016
Here, I provided strategic leadership steering operational efficiency across 87 US branches and locations offering Industrial Supply and MRO Part Sales & Distribution. Drove Continuous Improvement, Lean, Quality, Project Management, Supplier Data, branch acquisitions and moves, and SAP implementation.➥ Achieved multiple improvements and operational enhancements, including reducing Days Sales Outstanding (DSO) by an additional day, through development and implementation of shipping data reporting process that saved approximately $1.5M.➥ Directed Quality organization in achieving the company’s first ISO re-certification audit with zero corrective or preventive actions.➥ Implemented Standard Work on order follow up processes that increased branch productivity by 6%.➥ Established a new dedicated team for SAP Legacy Data Cleansing, and improved delivery performance by 13%.
-
-
US Operations & Continuous Improvement Manager
-
2013 - 2014
In this role, I developed, and implemented Visual Standard Work across the business, driving reduction of National Accounts Days Sales Outstanding (DSO) metric by 3 days and saving approximately $4.5MM.➥ Developed and established BDI’s first Project Management Organization including all processes and tools and staffed accordingly.➥ Led branch improvement by designing and implementing “2nd generation” Operations Manager training program.➥ Steered legacy system Data Cleansing and Preparation project for SAP, for all US Customers, Materials, and Vendors.➥ Built the BDI Lean Team from the ground up, and developed strategy and execution plan for both internal and external customers.➥ Drove improvement of key customer Quality metrics across all U.S. locations by an average of 7%.
-
-
-
Alcoa
-
United States
-
Mining
-
700 & Above Employee
-
Best Practices Manager
-
2011 - 2013
Here, I conducted detailed analysis of operations to determine, define, and develop Best Practice templates, tools, and processes for Alcoa Wheel & Transportation products. ➥ Overhauled and reengineered Best Practice organization to elevate effectiveness, including developing and establishing a new Best Practice Facilitator role to drive accountability, along with working with individual sites to staff, coach, and mentor associates. ➥ Successfully implemented $4.7 MM in Best Practice cost-saving opportunities in 2012, across 7 global manufacturing locations. ➥ Delivered First Past Yield Quality metrics for 7 global manufacturing locations and drove the business to achieve a scrap rate of 1.35% of revenues and a rework rate of 0.07% of revenues.
-
-
-
Honeywell
-
United States
-
Appliances, Electrical, and Electronics Manufacturing
-
700 & Above Employee
-
Operations (ISC) Project Manager - Business Modeling
-
Oct 2010 - Jul 2011
* Responsible for managing strategic Integrated Supply Chain projects utilizing the standard transition process, to meet project timing, cost, and projected save metrics.* Develop repositioning project feasibility studies and business case creation.* Lead cross-functional teams to implement strategic product, process, equipment, and capability transfers between sites and suppliers.Key Accomplishments:o Led a strategic repositioning project for the Filtration business, resulting in a $1.1MM annual cost reduction.o Developed Business Process Maps to create In-sourcing VS Out-sourcing decision making process, with cross functional “buy-in” and approval.o Developed strategy for transitioning low margin products to suppliers, while maintaining key customer metrics.
-
-
Senior Project Engineer
-
Jun 2007 - Oct 2010
* Responsible for leading major New Product Development programs for the Autolite brand. Currently leading 5-7 new product launches simultaneously.* Develop clear program and product requirements based on customer (VOC) and business expectations, including product performance, cost, quality, capacity, delivery, packaging and support.* Develop program plans, including detailed schedule and timing plans, definition of scope, milestones, deliverables, work breakdown structures, resources, and regularly review with Leadership.* Responsible for program execution, to ensure that customer expectations are met, while maintaining program fiscal and scheduling targets. * Lead cross-functional teams of 8-10 individuals from Engineering, Marketing, Manufacturing, Sales, Procurement, and Supply Chain. * Collaborate with functional experts to create Strategic FMEA analyses, and implement actions to mitigate identified risks. * Responsible for facilitating the monthly Executive Reviews for the Autolite Brand.* Train, mentor, and coach less experienced project leaders in use of program management tools and the New Product Development Process (PDP).* Key Accomplishments:o Leading the creation and implementation of our latest “next generation” technology product line.o Led over $3MM in Cost Reduction initiatives in 2009.o Led the team to achieve our first OE customer and business win in China.o Created the “Innovation Portal” tool and process, to document and evaluate innovation ideas, and “funnel” them into our New Product Development process.
-
-
Engineering Lab Supervisor
-
Jun 2005 - Jun 2007
* Supervised the day to day operation of the Product Engineering Organization (PEO) Test Lab, to meet and balance both internal and external customer commitments for the Autolite brand.* Directly managed and mentored 6 Technicians, 2 Engineers, and 3 Contractors, setting goals and objectives and communicating performance reviews.* Created the PEO Lab annual operating budget, and tracked the related expenditures, ensuring all budgetary metrics were achieved. Managed the request and implementation of all Capital Projects.* Performed project resource planning to identify resources needed for future growth projects, and identified any potential shortcomings.* Set priorities for all work requests presented to the lab, and worked with internal and external customers to maintain all commitments while reducing overtime costs.* Created performance metrics to track critical processes, and developed “lean” strategies to address areas for potential improvement.* Worked with HSE to regularly implement safety procedures and equipment improvements.* Key Accomplishments: o Enabled a $50K positive revenue stream in 2006, by implementing a new methodology to require customer payment for on-site application testing not related to sourced programs. o Worked with HR to recruit, interview, and hire 4 technicians to backfill headcount loss, due to retirement and employee advancement. o Implemented Test Cell scheduling process based on business needs and customer requirements, resulting in a 35% increase in efficiency. o Oversaw 3-D design and spec. creation of new Engineering Test Lab in China, using Auto-CAD.
-
-
-
Diebold Nixdorf
-
United States
-
IT Services and IT Consulting
-
700 & Above Employee
-
CCA Lab Manager
-
Mar 2002 - Jun 2005
* Directed initial setup and installation of Diebold Circuit Card Assembly (CCA) and Manufacturing Lab, and the related automated manufacturing equipment. Managed the day to day operation of the Lab, 5 Technicians, and 1 Engineer. * Developed, documented, and implemented “lean” manufacturing processes for both Prototype and Production assembly, and performed all related training. * Provided detailed DFMA analyses for all Prototype builds, and followed up with Design Engineering to ensure designs were revised for * Performed all Supply Base functions for both prototype and production assembly, including sourcing, procurement, supplier negotiations, and inventory analysis and maintenance. * Facilitated initial implementation of “Diebold Business Improvement System” in my areas of responsibility, and was a back-up Trainer/Facilitator for the North America training program. * Performed annual budget and capital planning for 2004 & 2005. * Monitored, tracked, and evaluated the source of manufacturing defects, and implemented process solutions. * Investigated new technologies, processes, and resources in order to improve and reduce setup and cycle times, increase productivity and utilization, and improve final quality. * Scheduled production / prototype builds and choreographed with the Plant shipment and delivery dates. * Key Accomplishments: o Facilitated the launch of the 1st generation touch-screen voting machines for Diebold Election Systems. o Kaizen blitz on “EAI” circuit card, reducing setup and labor time per board by 32%. o Reduced defect rate of CCA’s from 800 ppm down to 150 ppm.
-
-
-
Solectron Technology
-
Appliances, Electrical, and Electronics Manufacturing
-
1 - 100 Employee
-
Senior Process Engineer
-
Jan 2001 - Mar 2002
* Performed engineering support for Solectron “Hub 1” manufacturing, consisting of Compaq and Nortel products. * Responsible for manufacturing process solutions to improve quality, throughput, and utilization. * Trained and supervised process engineering technicians. * Trained machine operators on proper manufacturing techniques and procedures. * Investigated new technologies, processes, and resources in order to improve factory performance. * Performed programming for placement equipment, screen printers, automated inspection systems, and Reflow Ovens. * Facility was downsized in March 2002 due to the business repercussions of the technology market downturn. * Key Accomplishments: o Created and implemented “Top/Bottom” manufacturing process, increasing placements per hour by 9%, reducing feeder requirements by 16%, and reducing the necessary time to complete a production build by 14%. o Key member of “Global Process Improvement Team”, tasked with developing standard processes, equipment sets, and documentation for all manufacturing facilities worldwide.
-
-
-
Ericsson
-
Sweden
-
Telecommunications
-
700 & Above Employee
-
SMA Manufacturing Process Engineer
-
Dec 1998 - Jan 2001
SMA Manufacturing Process Engineer; Ericsson, Inc. Dec. 1998 – Jan. 2001 * Performed Surface Mount Assembly engineering support for Infrastructure Supply and Distribution and Private Radio Systems; supported all aspects of surface mount manufacturing from process design to reflow. * Facility was sold in January 2001 to facilitate Ericsson Inc. outsourcing all US based manufacturing. * Key Accomplishments: o Re-created and optimized all legacy GE Private Radio systems products to increase throughput and efficiency. o Responsible for full factory equipment software updates for Y2K compliance.
-
-
-
Motorola Mobility (a Lenovo Company)
-
United States
-
Computers and Electronics Manufacturing
-
700 & Above Employee
-
Manufacturing / Process Technician
-
1997 - 1998
* Performed technical and engineering support, both independently and as part of a team, of automated Surface Mount Technology processes and equipment used in the production of analog and digital cellular phones. * Responsible for continuous improvement projects and activities for quality, capacity, and capability, equipment and product support, and issue resolution. * Performed electro-mechanical and computerized troubleshooting and repair of robotic SMT equipment. * Analyzed Defect data to isolate machine, component, solder, and general process issues.
-
-
Education
-
Averett University Graduate & Professional Studies
Master of Business Administration - MBA, Business Administration and Management, General -
Southern Illinois University, Carbondale
B.S., Automotive Technology
Community
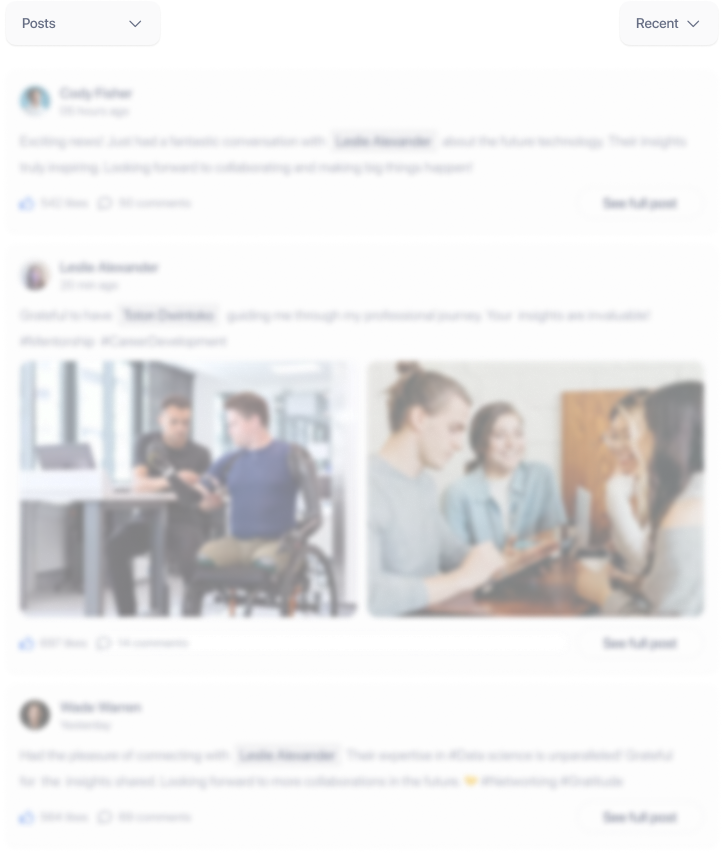