Jerryl Nai
Sr. EHS Manager at nVent Electrical & Fastening Solutions- Claim this Profile
Click to upgrade to our gold package
for the full feature experience.
Topline Score
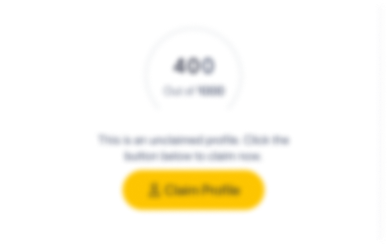
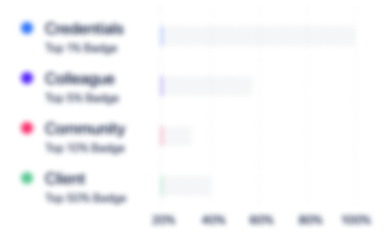
Bio

Robert McCory
I was fortunate enough to have Jerry as part of my team for over 6 years. We worked together at both nVent and Pentair. During our time together Jerryl led and implemented Global Processes and Systems for EHS and Quality including a major installation of Intelex across the global operational footprint. In addition, he supported the global Materials Management processes and systems which was not part of his position remit. Jerryl has a proven track record to lead and implement across multiple sites, functional organizations, and cultures. Jerryl's depth of knowledge, skillset, and experience would be an asset to any organization.

LinkedIn User
I worked closely with Jerryl when he effectively led an Intelex Global Quality project implementation for about 25 sites worldwide. Despite budget and occasional Senior Leadership support challenges, Jerryl very collaboratively worked with the business to deliver a useful, value-added Intelex product that is used widely across the company.

Robert McCory
I was fortunate enough to have Jerry as part of my team for over 6 years. We worked together at both nVent and Pentair. During our time together Jerryl led and implemented Global Processes and Systems for EHS and Quality including a major installation of Intelex across the global operational footprint. In addition, he supported the global Materials Management processes and systems which was not part of his position remit. Jerryl has a proven track record to lead and implement across multiple sites, functional organizations, and cultures. Jerryl's depth of knowledge, skillset, and experience would be an asset to any organization.

LinkedIn User
I worked closely with Jerryl when he effectively led an Intelex Global Quality project implementation for about 25 sites worldwide. Despite budget and occasional Senior Leadership support challenges, Jerryl very collaboratively worked with the business to deliver a useful, value-added Intelex product that is used widely across the company.

Robert McCory
I was fortunate enough to have Jerry as part of my team for over 6 years. We worked together at both nVent and Pentair. During our time together Jerryl led and implemented Global Processes and Systems for EHS and Quality including a major installation of Intelex across the global operational footprint. In addition, he supported the global Materials Management processes and systems which was not part of his position remit. Jerryl has a proven track record to lead and implement across multiple sites, functional organizations, and cultures. Jerryl's depth of knowledge, skillset, and experience would be an asset to any organization.

LinkedIn User
I worked closely with Jerryl when he effectively led an Intelex Global Quality project implementation for about 25 sites worldwide. Despite budget and occasional Senior Leadership support challenges, Jerryl very collaboratively worked with the business to deliver a useful, value-added Intelex product that is used widely across the company.

Robert McCory
I was fortunate enough to have Jerry as part of my team for over 6 years. We worked together at both nVent and Pentair. During our time together Jerryl led and implemented Global Processes and Systems for EHS and Quality including a major installation of Intelex across the global operational footprint. In addition, he supported the global Materials Management processes and systems which was not part of his position remit. Jerryl has a proven track record to lead and implement across multiple sites, functional organizations, and cultures. Jerryl's depth of knowledge, skillset, and experience would be an asset to any organization.

LinkedIn User
I worked closely with Jerryl when he effectively led an Intelex Global Quality project implementation for about 25 sites worldwide. Despite budget and occasional Senior Leadership support challenges, Jerryl very collaboratively worked with the business to deliver a useful, value-added Intelex product that is used widely across the company.

Credentials
-
DOT
Tyco -
Intelex Administrator
Intelex Solutions -
OSHA 30-hour
Lion Technology Inc. -
OSHA VPP Auditor
U.S. Department of Labor -
RCRA
Lion Technology Inc. -
Root Cause Analysis
TapRooT® | System Improvements, Inc. -
Situational Leadership
The Ken Blanchard Companies
Experience
-
nVent Electrical & Fastening Solutions
-
United States
-
Appliances, Electrical, and Electronics Manufacturing
-
300 - 400 Employee
-
Sr. EHS Manager
-
Jan 2022 - Present
Multi-site EHS Manager responsible for driving improvement and changing culture. Multi-site EHS Manager responsible for driving improvement and changing culture.
-
-
-
HSEvolve
-
United States
-
Consulting Director
-
Oct 2020 - Present
Lead discussions and negotiations of customer deliverables, supply gap assessments and data analysis to support implementation of EHS framework and drive actions to meet deliverables by inspiring thoughts and actions. Lead discussions and negotiations of customer deliverables, supply gap assessments and data analysis to support implementation of EHS framework and drive actions to meet deliverables by inspiring thoughts and actions.
-
-
-
nVent
-
United States
-
Appliances, Electrical, and Electronics Manufacturing
-
700 & Above Employee
-
Corporate EHSQ systems
-
May 2018 - Oct 2019
Lead alignment and transformation of global EHS, Quality and Customer Complaint Reporting, manage Policies, Procedures, EHSQ and Customer Complaint Reporting system, Enterprise EHS data analysis, Reporting (CSR, Regional, Global), manage KPI targets, site EHS LEAN assessments. •Led Business Unit Quality Leadership to standardized reporting and tracking processes •Managed Customer Complaint Reporting (CCR) process to standardization •Managed global reduction of OSHA Incident Frequency Rate (IFR) to 30% of industry average through focus shift on leading metrics Show less
-
-
-
Pentair
-
United Kingdom
-
Industrial Machinery Manufacturing
-
700 & Above Employee
-
Corporate EHS Leader - Global
-
Jan 2013 - Jan 2018
Manage EHS Policies, Procedures and GRE performance systems, Enterprise data analysis and Reporting (CSR, Regional, Global), manage KPI targets, site LEAN EHS assessments. •Reduced OSHA IFR - 45% through focus shift on a JUST CULTURE •Improved 4-year sustainability metrics for water, energy and waste •Led global Real Estate Business Case (REBC) process •Supported implementation of global PFEP processes Manage EHS Policies, Procedures and GRE performance systems, Enterprise data analysis and Reporting (CSR, Regional, Global), manage KPI targets, site LEAN EHS assessments. •Reduced OSHA IFR - 45% through focus shift on a JUST CULTURE •Improved 4-year sustainability metrics for water, energy and waste •Led global Real Estate Business Case (REBC) process •Supported implementation of global PFEP processes
-
-
-
Tyco
-
Ireland
-
Security and Investigations
-
700 & Above Employee
-
Corporate EHS Manager - Regional
-
Oct 2011 - Nov 2013
Lead standardization of global EHS KPI reporting processes and support daily operations including performance management assessments at locations.•Mentored 3 sites to OSHA Voluntary Protection Program (VPP) Star Certification•Reduced Americas’ OSHA IFR to 40% of industry average•Led finalization of global Environmental Health and Safety (EHS) Management Systems Evaluation (MSE) process tool
-
-
Operations EHS Manager
-
May 2004 - Jan 2012
Lead location to Environmental Health and Safety (EHS) Excellence through Policies, Procedures, EHS Systems, Data analysis and reporting, and drive EHS excellence through transformation.•Managed site to consecutive 2.4M and 2.8M man-hours (3.5 years) without lost time accident•Implemented autonomous hourly employee Safety Committee using VPP and JUST CULTURE principles•Led site to OSHA VPP Region VI Star, ISO14001, OSHAS18001, Texas Commission on Environmental Quality (TCEQ) Clean Texas Silver, President’s awards, and TYCO EHS Best Practice awards •Acknowledged as leading plant to 3-time recipient of President’s EHS award, and 4-time recipient of OSHA VPP Excellence award, through KPI (Key Performance Indicator) improvements and EHS culture transformation. Show less
-
-
Intl. Sourcing Technology Transfer / Vendor Development
-
2002 - 2005
Manage large multi discipline operations projects in daily operations, global sourcing, vendor development, quality, etc.•Championed divisional MRO initiative which resulted in sourcing selection and $5M annual savings.•Managed technology transfer and vendor development of castings and machined parts to international suppliers resulting in $2.8M annual savings.
-
-
Machine/Weld Shop Manager
-
2000 - 2002
Manage all aspects of machine shop for 4 shifts to increase material velocity and on-time delivery. Key responsibilities; Safety, Quality, Delivery, Cost, Cash (SQDCC)
-
-
Sr. MFG Engineer
-
2000 - 2000
Responsible for constraint assessments, workload alignment with planners and management Team, lead time and quality improvements. Key responsibilities; Safety, Quality, Delivery, Cost, Cash (SQDCC)
-
-
Community
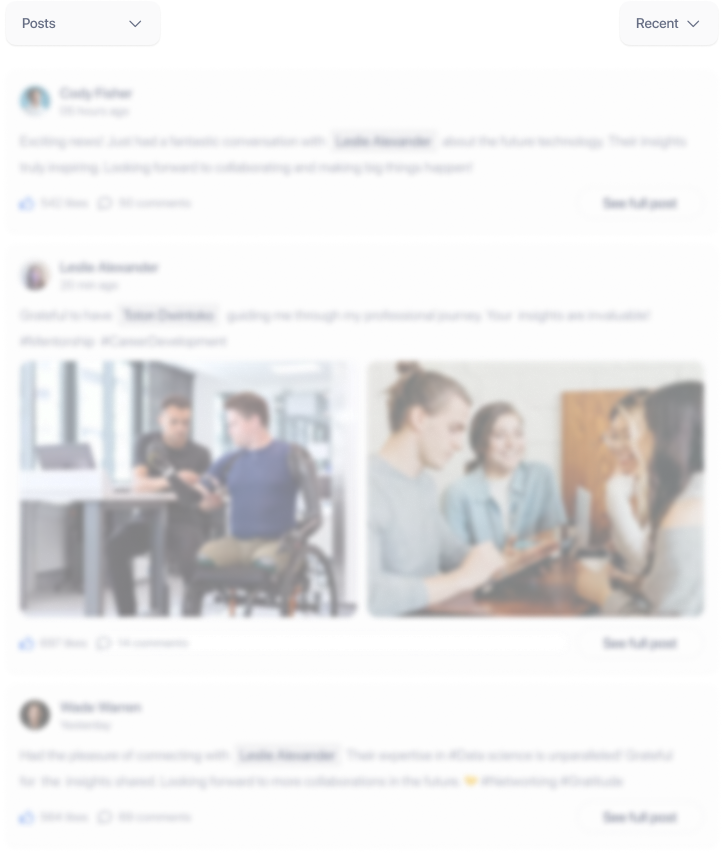