Noriko Mizuno
Operations at Cookpad- Claim this Profile
Click to upgrade to our gold package
for the full feature experience.
-
Japanese Native or bilingual proficiency
-
English Native or bilingual proficiency
Topline Score
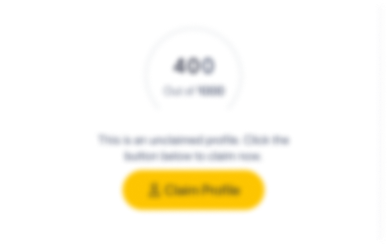
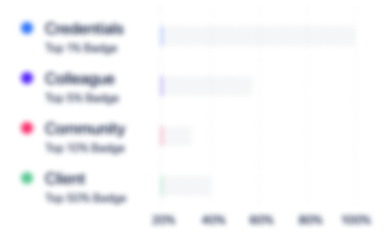
Bio


Experience
-
Cookpad
-
United Kingdom
-
IT Services and IT Consulting
-
100 - 200 Employee
-
Operations
-
Aug 2020 - Nov 2021
クックパッドの食品配送事業のオペレーション立ち上げに従事 ・配送モデルの変更による効率化及びサービス強化を実施 ・配送スポットの配置デザイン及び各スポットのレイアウト最適化を推進 クックパッドの食品配送事業のオペレーション立ち上げに従事 ・配送モデルの変更による効率化及びサービス強化を実施 ・配送スポットの配置デザイン及び各スポットのレイアウト最適化を推進
-
-
-
Procter & Gamble
-
United States
-
Manufacturing
-
700 & Above Employee
-
Market QA Manager
-
May 2016 - Nov 2019
• Eliminated quality incidence in Fabric and Home care category, which had chronic quality issues, through investigation over multifunction and rigid implementation of corrective action • Accomplished the best score ever in quality assurance capability audit for 3PL’s logistic center by finding issues through internal audit and developing solution with 3PL team • Diminished the risk of quality incidents by standardizing and documenting operational procedure after analyzing current… Show more • Eliminated quality incidence in Fabric and Home care category, which had chronic quality issues, through investigation over multifunction and rigid implementation of corrective action • Accomplished the best score ever in quality assurance capability audit for 3PL’s logistic center by finding issues through internal audit and developing solution with 3PL team • Diminished the risk of quality incidents by standardizing and documenting operational procedure after analyzing current processes and assessing the risk • Mitigated the risk of the product shipment after expiration date by engaging stake holders, developing common reference, and establishing the process • Improved service level while minimizing the quality issue risk through rearrangement of “product hold and rework” process with whole QA team
-
-
Market Initiative Planner for Fabric Care
-
Nov 2015 - Apr 2016
• Enabled implementation of multiple promotion campaign in the category by leading feasibility study with multi function team and proposing reasonable plan in cost and time perspective • Minimized service impact to the customers during severe out of stock situation caused by the new product launch through creating emergency handling plan with multifunction team and implementing early production increase • Contributed to planning process centralization (integration to Singapore) by… Show more • Enabled implementation of multiple promotion campaign in the category by leading feasibility study with multi function team and proposing reasonable plan in cost and time perspective • Minimized service impact to the customers during severe out of stock situation caused by the new product launch through creating emergency handling plan with multifunction team and implementing early production increase • Contributed to planning process centralization (integration to Singapore) by standardizing and documenting the Japan demand management process
-
-
Physical Distribution Manager
-
Apr 2013 - Oct 2015
• Avoided service level drop induced by shortage of track in high season through analyzing past track arrangement and developing track arrangement model • Achieved 0 delivery miss operational failure at distribution centers in peak seasons by developing multiple what if senario with distribution center team and optimizing distribution of products all over Japan • Reduced transportation cost of pet care products by realizing distribution center transition to optimize the supply chain •… Show more • Avoided service level drop induced by shortage of track in high season through analyzing past track arrangement and developing track arrangement model • Achieved 0 delivery miss operational failure at distribution centers in peak seasons by developing multiple what if senario with distribution center team and optimizing distribution of products all over Japan • Reduced transportation cost of pet care products by realizing distribution center transition to optimize the supply chain • Completed the transfer of Pet Care operation to MARS without issue by packaging the current operation, reviewing the package with receiving side, and adjusting the detail to fit with new company system • Improved service level during peak season and cut up-charge cost by developing the pallet planning system to avoid the pallet shortage • Realized transportation cost saving by developing new product palletizing pattern with engaging 3PLs • Mitigated truck shortage risk “Cross Dock Operation” after regulation change regarding driving distance by enabling • Accomplished VAT change (5% to 8%) operation without issue by building transition master plan to normalize the huge customer order increment due to VAT change
-
-
Education
-
大阪大学
理学修士, 宇宙地球科学専攻 -
大阪大学
理学学士, 物理学科
Community
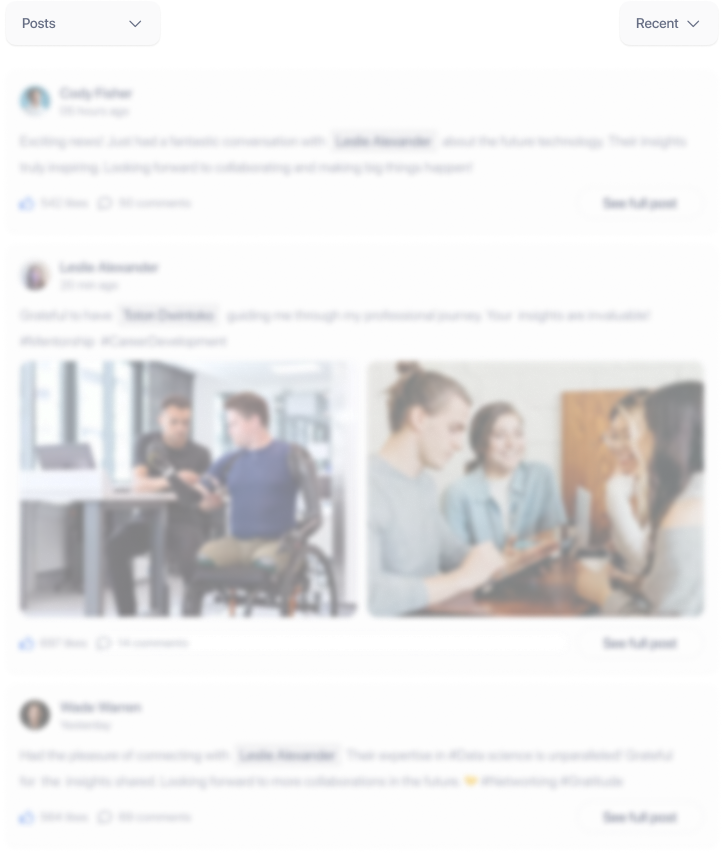